目录
返回顶部
EV Chargers
Charger Categories
Plug Types
Wide Bandgap Semiconductors for Transportation
Advantages of SiC power devices
Advantages of GaN power devices
How WBGs are impacting transportation systems
Systems within EVs reaping the benefits of WBG Semiconductors
In-vehicle networks (IVNs) and CAN Bus
CAN Bus
Variations on CAN bus that support higher data rate applications
Other protocols used in In-vehicle networks (IVNs)
The hybrid reality of modern In-vehicle networks (IVNs)
Sensors for Transportation
Distance and position sensors
Other sensors
Automotive Subsystems
ADAS
Battery Charging
Braking Systems
Central Body Control
Digital Radio
Electric Power Steering
Infotainment
Instrument Cluster
Main Inverter
Rear Vision System
Seat Control
Start-Stop System
Automotive Qualification and Grade
AEC standards
Reference Designs
Brushed DC (BDC) motors
H-bridge motor driver
Transportation and Automotive
Transportation like planes, trains, and automobiles have traditionally had low voltage systems for accessories. Those continue today and are expanding in the electrification of transportation to high voltage systems that run the primary motors.
EV Chargers
What is the future of electronics in an EV world? View Answer
As more transportation options make the switch to electrification (and remove the need for fossil fuels) there are several changes that need to be made both in terms of vehicle construction and infrastructure development.
Gas tanks are replaced by electrical energy storage and Internal Combustion Engines (ICEs) get replaced by electric motors, vehicles can be become simpler and easier to manufacture as major systems such as fuel distribution, mechanical linkages and exhaust are simply unneeded. With motion able to be generated closer to axel if not directly at the wheel and electrical power transferred by wiring from the battery pack.
Electrical power to recharge and power these vehicles may be from a green or low pollution source, however it may just as well be a coal fired power plant.
The other major concern is that while electrical vehicle recharging points are quicker than ever before they're still taking longer than using liquid fuels like gasoline to refill a tank.
As the era of the Internal Combustion Engine (ICE) comes to end, the era of Electrification in Transportation is starting. The transition is looking towards more efficient, lower pollution transportation solutions. The transition also brings new challenges, like charging infrastructure.
An Electric Vehicle (EV) charging station is a power supply with a connector able to fuel up an EV. These are sometimes referred to as a charging point.
Charger Categories
- Level 1 – the most basic AC charging unit for EVs. While vehicle battery packs can only be charged with Direct Current (DC) electricity most vehicles have on board charging circuity that can convert AC power to DC power. The chargers are typically found at a home where parking overnight would not be unusual. Since level 1 only requires the use of a 110V or 120V input and outputs between 1 and 2 kilowatts of power, a standard electrical outlet can be used nearly anywhere.
- Level 2 – a step up from Level 1 chargers, with the ability to quickly charge vehicle battery packs within a few hours. Level 2 chargers typically requires a 220V or 240V hook up and can output between 3 to 19 kilowatts. Due to the increased power requirement and installation cost, level 2 AC chargers can typically be found in public spaces for EV charging or in private areas given a professional installation from an Electric Vehicle Service Provider (EVSP).
- Level 3 – Direct Current (DC) charging, "fast chargers". Direct Current Fast Charging are the highest power and fastest EV charging stations. While they can nearly charge a battery in less than 1 hour, they require an enormous amount of power to do so. Most Direct Current Fast Charging stations require at least 480 Volts and 100 amps, but some newer stations have the ability of 1000 Volts and 500 amps of electrical power. As such DC fast charging stations are commonly found only in public areas, such as rest areas or near shopping malls.
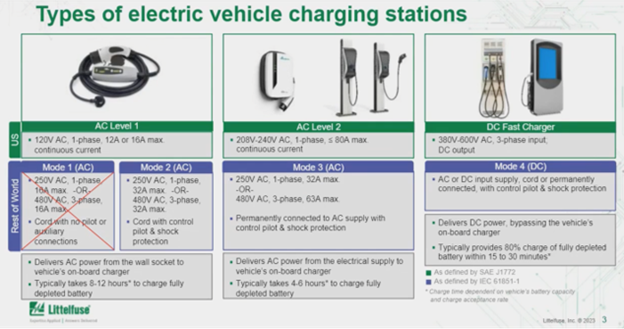
Plug Types
These plug types for EV Chargers are used in different regions and contain conductors for power and communication between the EV and the charger have defined standards for AC charging connectors. An Onboard Charger (OBC) is required within an EV for AC charging to be possible.Society of Automotive Engineers (SAE) and International Electrotechnical Commission (IEC)

Supercharged solutions for EV charging
The future of cars and mobility is electric. As the demand for electric vehicles grows, so does the need for reliable and safe charging systems.
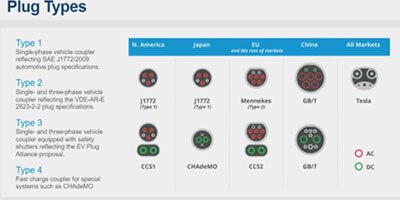
Onboard and offboard chargers in eMobility applications
With an increasing number of electric powered vehicles on market and the roads: passenger cars, light vehicles, buses, trucks and construction and mining vehicles, there is a growing need in the eMobility industry for reliable, compact, efficient, and powerful products that help safeguard against outages disruptions,
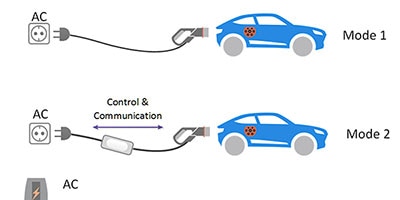
How to Use Residual Current Monitors to Ensure Electrical Safety When Charging Electric Vehicles
Charging of the high-voltage battery of electric vehicles (EVs) translates to high mechanical stress for charging cables and connectors. If the insulation breaks and live metal parts are exposed, or shunts appear in the onboard electronics, life-threatening residual currents can occur in the EV user’s body.
Wide Bandgap Semiconductors for Transportation
The future of electric transportation can be said to rest on the future of Wide Bandgap (WBG) Semiconductors. With their mix of higher working temperature and voltage when compared to traditional silicon semiconductor devices, wideband gap semiconductors can operate at higher power levels with lower losses.
The two most common wideband gap semiconductors on the commercial market are Silicon Carbide (SiC) and Gallium Nitride (GaN).
Advantages of SiC power devices
- SiC MOSFETs are unipolar devices that exhibit very low turn-on and turn-off switching losses. This property enables higher switching frequencies with lower losses, allowing the reduction of passive components and magnetics.
- High operating temperatures: silicon carbide offers superior thermal properties compared to silicon. SiC exhibits low leakage currents over a wide range of temperatures, allowing operation beyond 200°C. Simplified cooling and excellent thermal management are a bonus of this property.
Advantages of GaN power devices
- Low gate charge (QG) and on-resistance RDS(ON), which translate into lower drive losses and faster switching rates.
- Zero reverse recovery, resulting in lower switching losses and less EMI noise.
- High dv/dt: GaN can switch at very high frequencies and has 4x faster turn-on and 2x faster turn-off than SiC MOSFETs with similar RDS(ON)
How WBGs are impacting transportation systems
Higher operating temperature voltage and switching rates can directly improve transportation systems, here are some examples:
- Smaller and lighter weight electronics allow for compact and more efficient electric powertrains.
- Higher operating temperature and lower power losses allows for cooling systems to be smaller and lighter.
- Reduced power losses across components directly improve electrical efficacy.
Faster switching frequency, smaller components, and faster response times allows for more efficient use of battery power.
With smaller, lighter, more efficient electric drivetrains and related systems wideband gap semiconductor based electric vehicles have a very promising future in land, sea, and even air transportation.
Systems within EVs reaping the benefits of WBG Semiconductors
There are some key systems, within EVs, to keep in mind in terms of benefits from WBG semiconductors. You'll find the WBG Semiconductors in the traction inverter, onboard charger (OBC) , and EV Charger.
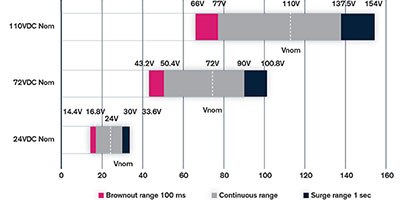
Specialized DC/DC Converters Meet the Unique Challenges of Railway Power Delivery
Designers specifying DC/DC converters for use in railways need to ensure those converters can perform reliably in confined spaces under difficult electrical, mechanical, and thermal stress conditions.
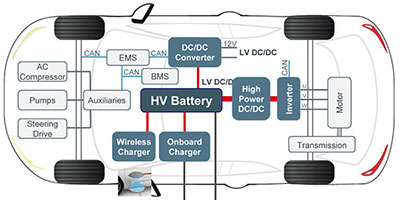
Wide Bandgap Semiconductors Are Reshaping the Transportation World
The entire transportation sector is undergoing a radical transformation, with internal combustion engine (ICE) vehicles gradually giving way to less polluting electric and hybrid cars and cleaner mass transportation solutions
In-vehicle networks (IVNs) and CAN Bus
In-vehicle networks are the common name for the set of connections that allows devices such as an Electronic Control Unit (ECU), cabin control, and Microcontroller Unit (MCU) in the vehicle to communication and exchange information.
CAN Bus
The CAN Bus standard started in the early 1980's and is a basic differential voltage signaled message-based protocol designed to allow devices and microcontrollers to communicate without a central host computer, this saves on cost and complexity. Fully described in ISO11898, classic CAN bus is for relatively low speeds of up to 1 megabit per second (Mbps) for a length of 40 meters or less and while developed nearly 40 years ago is not suitable for modern high bandwidth uses.
In modern applications CAN bus can be found in applications such as user interface controls and other medium bandwidth roles.
Variations on CAN bus that support higher data rate applications
- CAN Flexible Data Rate (CAN FD) was the first improvement with data rate up to 5 Mbps
- CAN Extra Long (CAN XL) improved data rates even further with speeds of up to 10 Mbps making it comparable to basic base10 ethernet connectivity and compatible with previous versions of CAN including CAN FD
Other protocols used in In-vehicle networks (IVNs)
- Local Interconnect network (LIN) Developed in the late 1990s as a cheaper and more cost-effective communication protocol to CAN Bus. With data rates of up to 20 kilobits per second (kbps), LIN is designed for Low-bandwidth applications where the complexity and cost of CAN bus is not needed.
- FlexRay is another IVN standard using synchronous communication that can provide higher data rates and bandwidth when compared to basic CAN bus, up to 10 Mpbs. FlexRay was developed by OEM automotive, and circuit manufactures as an answer to limitation in CAN speeds for higher data rate applications such as Advanced control and safety systems that require multiple high-speed sensor inputs.
- Automotive Ethernet was developed in response to increasing need for bandwidth for an Advanced Driver Assistance System (ADAS). Capable of speeds up to 100Mbps and allowing for Service-Oriented Architecture (SOA) software architecture like those used in Data Centers and with the ability to re-use of existing Internet Protocol (IP) software for other industries. The primary difference between automotive ethernet and regular ethernet can be found in the physical layer, with more robust cabling and interfaces to operate in the automotive environment of electrical interference.
The hybrid reality of modern In-vehicle networks (IVNs)
Most modern vehicles have several overlapping networks of CAN, LIN, and Ethernet connections depending on the connected hardware devices and data rate bandwidth required.
- LIN for simple electronic connections such as body electronics like side mirror and power seats positioning
- CAN for powertrain components, transmission positioning, and ABS control
- Ethernet for higher bandwidth like in cabin entertainment displays
Networking gateway devices can link these different networks together, allowing for a unified control system throughout the vehicle.
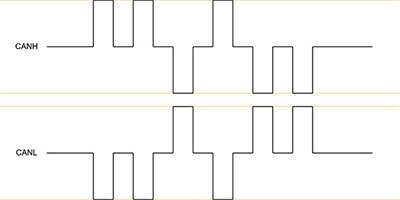
An Introduction to CAN Bus
The Controller Area Network, typically abbreviated to CAN or CAN Bus, is a serial, message-based communication protocol with the ability to connect numerous devices to exchange data on a single network.
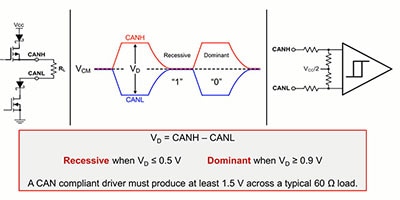
The Basics of the Controller Area Network (CAN bus) and its Use in Automotive Applications
One of the classic IVNs is the Controller Area Network or CAN bus. Let’s take a look at it, and some example CAN bus transceivers.
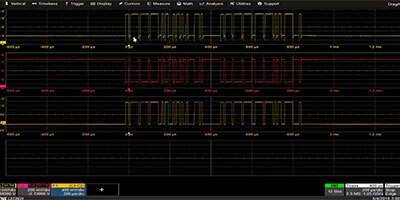
How to Simplify the Test of CAN Bus Networks Using the Right Oscilloscope
One of the classic IVNs is the controller area network or CAN bus. CAN has been around for about thirty years, but it continues to develop.
Sensors for Transportation
With the increase in Advanced Driver Assistance Systems (ADASs) for safety and protection and the beginning roll out of Autonomous Driving vehicles, the need for sensors in transportation is only growing. Predictive safety systems can set off airbags and prepare for impact at the first signs of a collision, or in some case even prevent it all together.
Distance and position sensors
- Radar: radar sensors use radio waves to detect vehicles and other objects in the environment around the car. By measuring the time, it takes for a radar pulse to return to the receiver, the distance can be calculated.
- Lidar: distance is measured by sending a short laser pulse and recording the time taken between outgoing light pulse and the detection of the reflected light pulse.
- Ultrasonic: Measuring the time between sending out a short high frequency pulse of sound until it bounces off an object returns to a receiver Typically found in the front and rear bumpers useful for short range object detection or collision avoidance.
- GPS: By receiving GPS signals from orbiting satellites exact position can be determined within a few centimeters of accuracy with widespread and near global cover this is one of the most common types of system in use today.
Other sensors
Accelerometers, temperature, humidity, and optical sensors also get used within transportation. For more on these sensors see the Applications & Technologies page on Sensors.
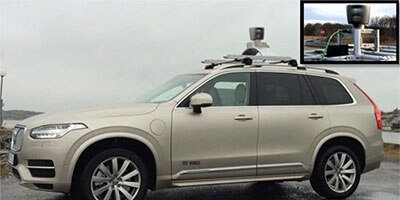
An Understanding of How LiDAR Works Shows the Importance of Careful TIA and Comparator Selection
Light detection and ranging (LiDAR) has come to be most widely associated with the field of automotive design, where dreamers believe it can help realize a hands-free future.
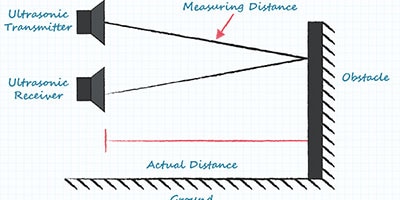
Understanding Ultrasonic Sensors
In this article, we explain the principle of operation of ultrasonic sensors, consider their advantages and disadvantages, and review some of their most common applications.
Automotive Subsystems
ADAS
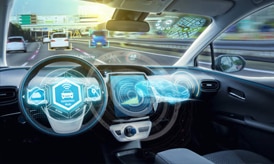
Battery Charging
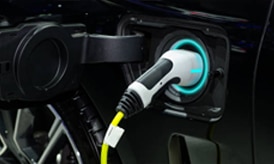
Braking Systems
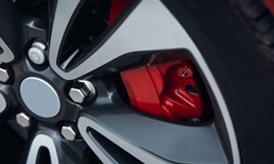
Central Body Control
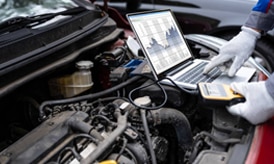
Digital Radio
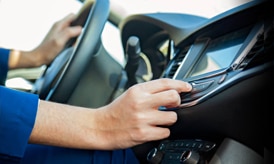
Electric Power Steering
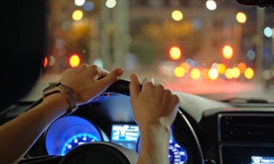
Infotainment
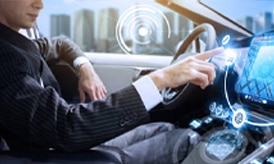
Instrument Cluster
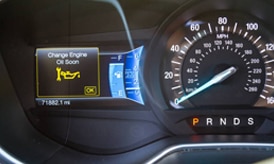
Main Inverter
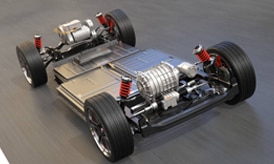
Rear Vision System
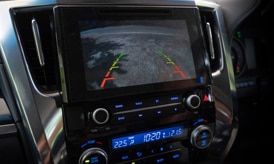
Seat Control
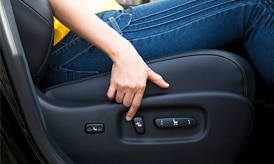
Start-Stop System
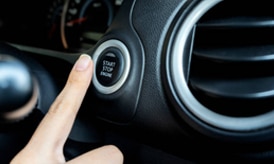
Automotive Qualification and Grade
Who is the AEC? View Answer
As the consumer electronics market expanded in the late 1980 and early 1990's it became necessary to develop electronic specifications and part qualification standards for automotive circuits and systems components to ensure that automotive systems received the necessary parts that can withstand the harsh conditions and operate in automotive environments over a sustained time frame. The difference between driving home and an expensive repair bill could be the operation or failure of a single IC.
The Automotive Electronics Council (AEC) is an automotive industry organization originally established in the early 1990s by major automotive manufacturers Chrysler, Ford, and GM for the purpose of establishing common electronic part qualifications and standards. Today the AEC has expanded to include many different automotive component manufacturing companies and other industrial equipment manufacturers.
AEC standards
The AEC-Q series of standards are a set of qualifications and testing standards for all electronic components used in automotive applications. The specifications have been established by the Automotive Electronics Council (AEC) and are accepted by most automotive manufacturers across the globe. There are several testing conditions covered under AEC standards. Electrical performance, operating temperature range and thermal cycling, moisture and chemical resistance, vibration, physical stress testing, and solderability.
The testing areas, each with specific subcategories and testing regimes are as follows.
- AEC - Q100: Integrated Circuits (Chips)
- AEC - Q101: Discrete Semiconductors
- AEC - Q102: Discrete Optoelectronic Semiconductors
- AEC - Q103: Sensors in Automotive Applications
- AEC - Q104: Multi-Chip Modules (MCM)
- AEC - Q200: Passive Components such as Resistors, capacitors, and inductors
While the AEC-Q standard form the basis for testing and qualification some component manufactures go above and beyond those standards testing for more extreme conditions and operating environment and call them automotive rated, but the AEC-Q standards ensure minimum standards accepted by most automotive companies.
For more information, the AEC Public Documents page can be found here: AEC Documents
Do I need to use AEC-Q parts in my application? View Answer
Not necessarily, while AEC-Q rated parts are typically rated at high levels of ruggedness and reliability, especially in terms of thermal operating conditions and mechanical vibration to withstand automotive environment and applications, that also comes with a higher individual component cost and at times limited availability.
For most everyday consumer applications, regular commercial part will be more then suitable. Very rarely do everyday items face the conditions in an engine bay that has been running for hours.
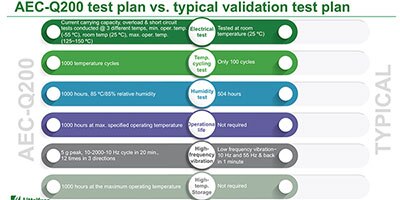
AEC-Q200 Qualified Fuses Play a Critical Role in the Automotive Environment
AEC-Q200 Rev E sets rigorous stress tests for fuses to ensure their reliability in automotive environments.
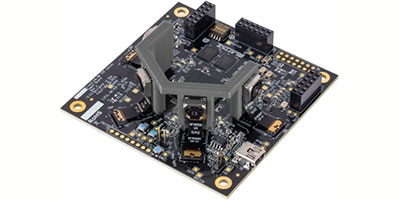
The Selection and Use of FPGAs for Automotive Interfacing, Security, and Compute-Intensive Loads
FPGAs can be used to augment legacy microcontrollers and application processors in automobiles to enhance connectivity, processing performance, and security.
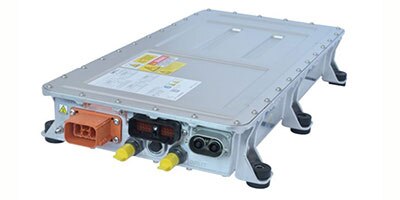
How to Ensure Circuit Protection, High Speed Data, and Power Conversion for eMobility Platforms
Use automotive qualified circuit protection, communications, and power conversion solutions to design sustainable and safe eMobility systems.
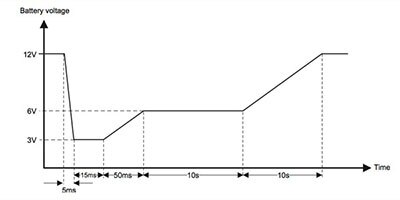
Automotive Applications Test a Power Chip’s Mettle
A look at the demands of cold cranking and solutions available to cope with the strain of starting a cold engine from STMicro, TI, and Linear Technology.
Reference Designs
Here at Digi-Key we have a wide range of reference designs from the top automotive component suppliers, allowing you to design and build the features of tomorrow's transportation solutions.
Brushed DC (BDC) motors
Brushed DC motors still play a vital role in automotive subsystems in everything from power steering, passenger cabin controls, and automotive engine control. Here is a small sample of reference design that use Brushed DC motors in automotive contexts.
Rohm
- BD6222FP-EVAL-N: DC Brush Motor, 6 ~ 15V
- BD6232FP-EVAL-N: DC Brush Motor, 6 ~ 32V
- EVAL-N.BD6232FP: DCBM Driver, 6 ~ 32V, 2A
ST Microelectronics
H-bridge motor driver
The rough world of Transportation and Automotive applications demand rugged, low power solutions with precise control and simple interfaces. That is where H Bridge motor controllers can shine in a variety of pump and engine control gates. Here are a few examples of Automotive qualified H Bridge reference designs.