New Material Technologies Deliver Improved LED Replacements for the Popular MR16 Light Bulb
投稿人:DigiKey 欧洲编辑
2013-10-08
It might be one of the most popular lamps in use today - a recent US Department of Energy report estimates that there are 46 million in the US alone - but the MR16 halogen bulb is also among the least efficient. That has also made it an attractive target for manufacturers of high-efficiency LED-based replacements, and already 10% of the MR16 installed base in the US has switched to solid-state versions.
However, there is a downside to many of the LED replacements that are on the market. The DOE says that there are still performance and equivalency issues, mostly to do with the challenge of combining a high lumen output with the small MR16 form factor. Halogen lamps can still deliver more than double the lumens of even the best LED versions, many of which still struggle to meet the performance of a 35 Watt halogen. Other issues include matching the "warm" halogen color and high prices, especially for dimmable LED versions.
While virtually all the major lamp manufacturers are selling LED MR16s, there is still plenty of room for improvement. In this article, we look at how new semiconductor material and phosphor combinations promise to deliver true solid-state replacements for those power-hungry but popular halogens.
Introduction and market data
Many estimates1 suggest that lighting as a whole accounts for about one-fifth of global electricity consumption, and LED-based lighting has long promised to have a major impact on that figure. At the same time, the growing popularity of MR16 halogen lamps makes them increasingly responsible for the world’s growing electricity bill.
Halogen lamps present extra motivation for consumers looking to switch to LED replacements. In rooms where previously a 100 Watt incandescent bulb would have been a typical choice, many may now feature six or more halogen spotlights. If each of those is rated at 50 Watts, the impact on customer bills is obvious.
No wonder LED-based versions of MR16s have already made significant inroads into the market for halogens. The latest figures from the US Department of Energy (DOE), in its April 2013 report on LED lighting adoption,2 estimate that of 46 million MR16 halogens installed in the country, 4.8 million now feature LED chips.
That partly reflects the lack of cheaper compact fluorescent (CFL) alternatives, since the small size and preference for dimmable operation make the CFL a non-starter for halogen replacement. In fact, the DOE found that of all the LED-based lamps analyzed in its report, it was MR16 replacements that have had the greatest success in terms of penetrating the installed base. Whereas LED replacements now account for more than 10% of installed MR16s in the US, the figure for regular A-type lamps is just 1%.2, 3
However, those who have replaced their MR16s with LED alternatives will have noticed something. In many cases, the light that they produce looks quite different. In fairness, the output of halogens is tough to match. Their popularity, especially among lighting designers and in applications where illumination quality is a priority, results from the visually pleasing result of a very close spectral match to the reference “black body” emitter.
Something about the brightness and light quality of LED replacements, on the other hand, often seems inferior. The DOE report confirms this, stating that the lumen output of most LED-based MR16s is in fact less than that from a 35 Watt halogen. “As of April 2013, the maximum lumen output of an LED MR16 lamp listed in DOE’s LED Lighting Facts product list was 590 lumens, while halogen MR16 lamps can offer light output more than twice that amount,” reported the department.
Another reason why LEDs have not penetrated this sector to a much greater degree is of course their price, especially for the bright, high-quality, dimmable versions that many would want. “In 2012, halogen MR16 prices average at roughly $4.60 per lamp, while the average LED MR16 price is $23 per lamp,” pointed out the DOE report.
In other words, although there is an economic case for consumers to buy LED replacements, they soon pay for themselves in efficiency gains; the prospect of paying out more than $100 for six new “bulbs” in a single room is clearly not an attractive one.
LED choices for MR16 replacements
The LEDs used in MR16 lamps currently include offerings from virtually all of the established chip manufacturers, for example Philips Lumileds’ Luxeon H range, optimized for small lamps, and Cree’s MT-G XLamps, optimized for large-formats.
Among those trying to mount a challenge are relative newcomers Soraa, the Californian start-up that spun out of LED pioneer Shuji Nakamura’s Santa Barbara research lab, and Verbatim, which is collaborating closely with Korea-based Seoul Semiconductor. However, while many of their established rivals are aiming to cut LED lighting costs using large silicon substrates, these two are employing emitter structures based on gallium nitride (GaN) instead. They believe that the move will yield a crucial advantage over the more established technologies, both in terms of electrical efficiency and the all-important light quality.
Mike Krames, the Soraa CTO, summed up how he feels about some LED replacement lamps in a colorful recent blog post, writing: “I’m standing in the taxi queue at Chicago’s O’Hare airport, having to squint ahead to gauge my wait. The cause of my discomfort, a horrible, blue-LED array-based outdoor luminaire ahead of me and above, spilling light in all directions and casting a putrid smear of yellow-green color against a nearby wall of the terminal, and directly into my eyes.”
That is not quite what you might expect to hear from somebody who has spent much of his working life working on LEDs for lighting applications. As Krames points out, people are likely to attribute the offensive glare aspects of such products to the LEDs themselves. That would be unfair, the lamp design is the main problem, but all the same it reflects badly on the technology.
Soraa believes that for replacement LED lamps of all types to really prosper, the quality of the light that they produce is just as important as their efficiency. The company even told the US Environmental Protection Agency in May 2013 that its Energy Star program must begin to make serious requirements for lighting quality, and not just electrical efficiency, or else LED lighting may suffer from the same problem as the CFL, potentially ruining consumer confidence.
Soraa is proposing that the EPA introduces a new two-tier standard, setting minimum requirements for light quality as defined by color rendering index (CRI), alongside those for minimum lamp efficacy, with efficacy requirements relaxed by 5 lumens per Watt for the higher-quality bracket. It wants to raise the color quality to a minimum CRI of 90 for lamps operating at the minimum lamp efficacy. For lamps with a CRI of between 80 and 90, it proposes an increase to luminous efficacy requirements to compensate.
Overcoming “glare”
Part of the difficulty for lighting designers is the very-high optical source brightness of LEDs, which can be both a blessing and a curse, depending on the design employed. In a poorly designed product, optics can cast images of the high-brightness LEDs outside of the target beam pattern, leading to an excess of high-angle light entering the eye of the casual passer-by; in other words, an example of light pollution in the form of the “glare” that Krames described.
In fact, the high-brightness characteristic of LEDs can instead be used to design lamps that distribute light in a far more elegant and aesthetically pleasing manner, using only a few optical elements.
Where conventional halogens can spill nearly half of their light outside of the intended beam, Soraa’s LED MR16s are said to produce only about 10% so-called “spill light”, meaning less glare. Despite the DOE’s finding, that many LED retrofits are not as bright as conventional lamps, Krames says that Soraa’s designs could deliver more than 200 Watt equivalence before reaching the glare level of a typical halogen.
The latest “GaN-on-GaN” LED MR16 lamp products from Soraa, first unveiled at the Lightfair show in April 2013, are designed to replace 65 Watt and 75 Watt halogens, delivering up to 600 lumens of warm-white light (3000 K) across a range of narrow-spotlight and wider flood-type outputs, are said to operate at up to 120 degrees C. At a luminous efficacy of just over 50 lumens per Watt, they consume only around a fifth of the electrical power of a standard halogen MR16. There is still a hefty cost premium though, with the lamps expected to sell “in the high $20 range”.
GaN material benefits
What is it about using GaN substrate material that is so beneficial? It boils down to crystal lattice structures, with GaN providing a near-perfect base material to match the active semiconductor layers of InGaN and AlGaN that are used in short-wavelength LEDs. The trouble has always been that it is very difficult to manufacture large-area, low-defect crystals of GaN at a sufficiently low cost to make for economic LED production.3
As a result, the vast majority of blue-emitting LEDs, such as those used in the multi-die components featured in today’s solid-state MR16 retrofit lamps, consist of light-emitting semiconductor layers deposited on either sapphire or silicon carbide material. Silicon substrates are also starting to make inroads as manufacturers look to scale production to large volumes in old silicon fabs.
Compared with the wider semiconductor world, that makes LEDs highly unusual. Virtually all other electronic chips, whether based on silicon, indium phosphide, or gallium arsenide, are produced by depositing the active material layers on top of what is usually called a “native” host, that is, exactly the same material found in the device’s active layers. The use of foreign substrates comes with the inevitable penalty of more complex fabrication processes and reduced yields.
The fundamental problem that arises is that although relatively cheap (especially in the case of silicon), foreign substrates completely undermine the potential power of the GaN devices that they are supposed to support, according to Krames. A lack of atomic alignment between the mismatched crystal lattices leads to defects, while their different thermal properties leads to wafer bow in the hot growth chambers used to deposit the critical light-emitting layers.
Higher defect levels that result in the active light-emitting semiconductor layers also restrict the current densities that the material can deal with, as well as limit operating temperatures. In a small lamp like an MR16, often housed in an enclosed fixture and requiring high light output, this is a particular problem. It means that standard LED chips must be cooled, leading to the kind of bulky heatsinks that can make LED replacements more difficult to accommodate in an enclosed space.
That is not all, sapphire is electrically insulating, while silicon even absorbs some of the light output that the device engineers are trying to maximize. The overall result, Soraa argues, has been complicated and costly LED chip architectures with a performance far below that which GaN is capable.
So why is a non-native GaN host used for GaN-based LEDs? This boils down to the physics of GaN (a very-high vapor pressure and melting point), which make it incredibly difficult to grow a crystal boule of the material from a typical melt. Nitrogen gas is also so inert that it will only react with gallium metal at extremely high temperatures, and so despite plenty of research activity to explore different growth methods, a really simple, cost-effective way to produce large-diameter GaN crystals has remained elusive.
Blue laser diode ramp
GaN substrates were first developed out of necessity thanks largely to Sony, supporting the ramp in production of blue laser diodes needed for the first Blu-ray Disc players and recorders. That was after it became clear that the wafer yields of blue laser diodes produced on foreign substrates were horribly low, meaning that the resulting laser diodes were too expensive to make for such a mass-market product.
The first generation of GaN substrates was made using a deposition technique called hydride vapor phase epitaxy (HVPE), slowing building up a crystal, and HVPE is also what Soraa has been using so far. However, devices made in this way remain relatively expensive to produce, so the company is aiming to improve matters further with an all-new deposition technology that promises a future of large-area, low-defect, low-cost GaN substrates, providing even further improvements in LED performance.
At an ARPA-E summit held in Washington, DC, in late 2012,4 Soraa presented its “Scalable Compact Rapid Ammonothermal (SCoRA)” growth technology, the new method for producing GaN crystal boules. If the production method scales up to volume, the availability of such substrates could have a huge impact on not only lighting, but many other applications, particularly in power electronics, and lead to smaller, more efficient, and more cost-effective power subsystems, such as power adaptors and inverters for solar power plants or electric vehicles.
The new SCoRA method is based on ammonia chemistry and an adapted vessel in which to grow the crystal. Normally, the physics of GaN demands higher temperatures and pressures than a standard autoclave can handle, and so Soraa has made a significant change by lining steel autoclaves with an insulating and protective layer of ceramic material.
Reportedly, the firm has been able to grow high-quality GaN crystals at reasonable speeds using a pilot-scale reactor. The crystals it has grown have provided two-inch diameter material, and Soraa is working towards four-inch sizes that would be suitable for economic LED and laser diode chip production.
Phosphor options
It is not just Soraa taking the GaN substrate approach. Verbatim, the electronic storage company that has diversified into the LED lighting space, has developed its own version of GaN-on-GaN LED technology. It released MR16 replacements in early 2013, featuring LEDs based on GaN substrates made by its parent company Mitsubishi Chemical, as well as defect-reducing “nPola” technology from Korea’s Seoul Semiconductor (SSC).
Add a licensing deal between Sumitomo Electric Industries (SEI) and Soitec on GaN substrate production earlier this year, and it appears that the use of GaN substrates is gaining wider traction. SEI will use Soitec’s “Smart Cut” layer-transfer technology, already widely employed in the silicon semiconductor world, in combination with its existing free-standing engineered GaN substrates, enabling LED chip-making customers to reduce costs by re-using the material several times.
Verbatim has an additional piece of chemistry up its sleeve, too. Its chips now feature a new combination of phosphors designed to work with an LED emitting in the violet, rather than blue, wavelength range.
The “VxRGB” phosphor technology comes from parent company Mitsubishi Chemical, and the light produced by the new MR16s is said to ensure that illuminated objects appear more vivid than under regular LED replacements. At the moment, they are restricted to a relatively dim output of 180 lumens, typically to replace standard 20 Watt halogens, and are aimed at specialist applications in hospitality, high-end retail, and museums.
Summary
The near-perfect, dimmable light quality and compact design of halogen lamps is what has made them so popular. Although existing LED versions already provide much lower energy consumption, the halogen is a tough act to follow. While solid-state replacements have certainly made a market impact, to truly replicate halogen performance, and stimulate mass adoption, new semiconductor and phosphor material combinations could be crucial.
References:
- EURAMET Metrology for Solid-State Lighting (EURAMET project report)
- Adoption of LEDs in Common Lighting Applications (US Department of Energy report)
- LED Replacement Lamp Trends (Vrinda Bhandarkar, Strategies Unlimited, market report)
- Sapphire and GaN Substrate Materials (DOE SSL Manufacturing R&D Workshop presentation)
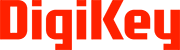
免责声明:各个作者和/或论坛参与者在本网站发表的观点、看法和意见不代表 DigiKey 的观点、看法和意见,也不代表 DigiKey 官方政策。