
Electrifying (the) Future
Fossil fuels and alarming emission levels? We can do better than that!
One out of many essential steps towards an energy-efficient world lies in the soaring popularity - and consequently the use - of electrified two-, three- and four-wheel vehicles. Nowadays, new materials and technologies enable greater power efficiency, smaller size, lighter weight, and lower cost solutions. Consumers look for affordable, clean transportation alternatives to address congestion, poor air quality, and lack of mobility.
Want to play a key role in accelerating the transition to e-mobility with your products? Then turn to a true expert, a leader in power, sensing and security solutions: Infineon.
LEVs: an increasingly important EV sub-category
Types of plug-in electric vehicles
Besides conventional gasoline-powered vehicles, the industry currently distinguishes based on the all-electric range (AER) and the level of hybridization between the following types of electric vehicles:
- All-electric vehicles (long-range and limited range versions)
- Gasoline-electric hybrids (range-extended and minimal range versions)
What they all have in common is the fact that for charging their high-energy battery an off-board charging infrastructure is needed which happens to be fundamentally different from the well-developed infrastructure for fueling gasoline-powered vehicles. Charging options vary: AC level 1 chargers use the electric service present in almost every building. DC fast chargers require higher levels of voltage not to be found everywhere, i.e. provided only by specifically installed commercial fast-charging stations with higher charging rates.
Three-hurdles slowing mass deployment of plug-in electric EVs
When focusing on the mass deployment of all-electric vehicles and gasoline-electric hybrids, the challenges currently recognized can be summarized in three main hurdles:
- the high initial investment
- the limited charging infrastructure available
- and consumer misperceptions about their operation
In other words, battery system cost, battery density, range limitations and charging constraints continue to be impediments to adoption.
The rise of LEVs
The named obstacles have become a trigger for the evolvement of another segment in the EV market: light electric vehicles (LEVs). Compared with other EVs as well as with conventional gasoline-powered vehicles, they are extremely low priced what makes them affordable even to the financially underprivileged and hence attractive for emerging markets where a transition to electrified mobility is in progress (e.g. rickshaws into e-rickshaws, scooters into e-scooters)! They can be charged from the grid (e.g. power plugs in private homes) and hence, do not necessarily require installation of a specific charging infrastructure. And due to an extremely simple configuration both - their functioning and handling - are easy to understand. Targets are clearly those driving short distances at lower speed not holding a driving license as for LEVs no certification – neither for the vehicle, nor for the driver - is legally stipulated until today. Depending on the purpose of use there are variants with and without space for carry-on items. And most importantly, they fulfill the zero emissions mandate.
Currently, the LEV market in units is six to ten times larger than the one for plug-in EVs. Already in the near future, LEVs are expected to be highly integrated with automated vehicle technology, i.e. sensors. The industry has seen an incredibly fast rate of conversion from internal combustion engines to full electrical drives (e.g. approximately 62 percent of the number of forklift units sold in 2018 have already been electrical).
LEV industry characteristics and customer challenges
Infineon is aware of its customers’ major challenges and the impactful characteristics of the LEV industry:
- strong price erosion what makes it a cost driven segment
- time-to-market pressure (especially in emerging markets where a lot of newcomers to the industry seek market penetration)
- small form factors
- relaxed lifetime expectations
- growing demand for easy-to-use system level solutions (plug and play, turnkey) comprising the technology, soft- and hardware as well as services (e.g. software design) due to increasing system complexity
Complete system solutions for LEVs
Infineon is specialized in offering complete system solutions encompassing all fundamentals, namely power electronics, controllers, security, and authentication. And of course our advanced sensor technologies add value, too. With our pioneering spirit sustained by technical know-how, highest quality standards and preeminent manufacturing expertise throughout the entire supply chain, we strive to be benchmark in addressing a broad range of light electrical vehicles. With our portfolio we already cater for e-skateboards, e-scooters, pedal electric cycles (i.e. pedelecs), low speed electric cars, e-forklifts, e-rickshaws, three-wheelers in general and many others. Multiple functional blocks are thereby considered (e.g. motor control, battery chargers, air conditioning systems, hydraulic control). Power management and consumption as well as voltage regulation are covered by an exceptional selection of power components (high voltage CoolMOS™, low voltage OptiMOS™, StrongIRFET™, SiC and GaN based products), XMC™ and AURIX™ microcontrollers, and EiceDRIVER™ gate driver ICs – amongst others. In other words, Infineon offers all components that are needed for the compact, cost-effective designs of today, and for the innovative vehicles of tomorrow.
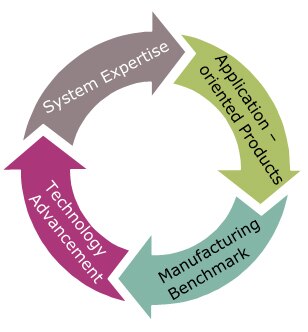
Features and benefits:
- Most robust silicon solutions in the market
- Ideal for both - low and high power density application
- Industry-leading performance with the best figure of merit (FOM) enabling rugged and reliable system designs with reduced BOM count and consequently at an attractive overall system cost level
- Enabling various levels of integration and space saving (depending on the application)
- Application based qualification procedure (beyond JEDEC) according to stringent industrial and automotive (if applicable) standards
- Perfect choice for multiple functional blocks in LEVs (e.g. battery charging, motor control, battery management system, etc.)
Why Infineon is the right partner for your LEV projects:
- Most reliable, industry-leading solutions, delivering either best-in-class performance or price competitive (cost-optimized) solutions for the widest range of LEV applications
- Mastering all leading power technologies (Si, SiC, GaN)
- Most comprehensive packaging portfolio in Si MOSFET technologies (THT, SMD)
- Number one in in the low voltage MOSFET market
- Extensive application system understanding and manufacturing expertise throughout the entire supply chain
- High quality volume supply that results in faster time to market
- Global application design support via a worldwide network of field application engineers and trusted distributors
- Broad portfolio – all out of one expert’s hand
- Line-up for ease-of-use - combination of complementary switches, gate driver ICs, and controllers
Our service is your success in the highly competitive LEV industry
Critical success factors | Infineon’s offering |
---|---|
|
|
|
|
|
|
|
|
|
|
|
|
|
|
- High Power Light Electric Vehicles
- Low Power Light Electric Vehicles
- Battery Chargers for Light Electric Vehicles
- Development and Evaluation
High Power Light Electric Vehicles
High Power Light Electric Vehicles
High power LEVs can be separated from the rest of lower power LEVs by the following characteristics:
- power levels: 10 kW – 30+ kW
- voltage range: 48 V – 144 V
- mostly four-wheelers with space for carry-on items (e.g. used for material handling in industrial surroundings, passenger transportation with any sort of baggage)
- value drivers: system cost, efficiency / operating range
Target applications:
- E-forklifts
- Light utility vehicles (LUVs)
- Low speed electric vehicles (LSEVs / MicroEVs)
- E-motorbikes
- Golf carts
High power LEVs are named differently depending on the country of jurisdiction. In China, they are known as small EV cars, low speed EV cars, or micro EV cars. In the European Union four-wheeled microcars are categorized as quadricycles, and in the US as neighborhood electric vehicles.
The category of high power LEVs also covers some ‘off-highway’ electric vehicles, such as material handling equipment, golf carts, and people movers. For these applications, an increased operating range is needed to prevent interruptions in the flow of materials and people.
Downturns of the global trend:
- Negative environmental effects resulting from the extensive use of lead-acid batteries
- Lack of regulations for LSEV manufacturers leads to substandard safety performance
- Suboptimal acceleration and fairly low top speed levels
- Violations of traffic regulations as controls are difficult given the non-existence of legal obligations for specific documentation, neither for the driver nor the LSEVs (e.g. driving in bike lanes)
As consequence, the Chinese government is the first to take drastic measures limiting the proliferation of low quality LSEVs. Instead of using lead-acid batteries manufacturers are encouraged to focus on lithium-ion battery versions with extended operating range and improved battery power densities, along with mandatory safety tests.
Infineon’s solutions respond exactly to these latest developments in the field. They enable LSEV manufacturers to upgrade their product portfolio with the shortest time to market. More precisely, they extend the battery life time of e-forklifts, LSEVs and e-motorbikes while providing robust performance at competitive costs. Via a modular approach a wide range of application voltages and power levels can be covered. The customer is offered a vast assortment of products for almost the entire LEV-system including motor control units, hydraulic units, and air conditioning units (depending on the specific application).
System diagram: high power low speed electric vehicle (LSEV)
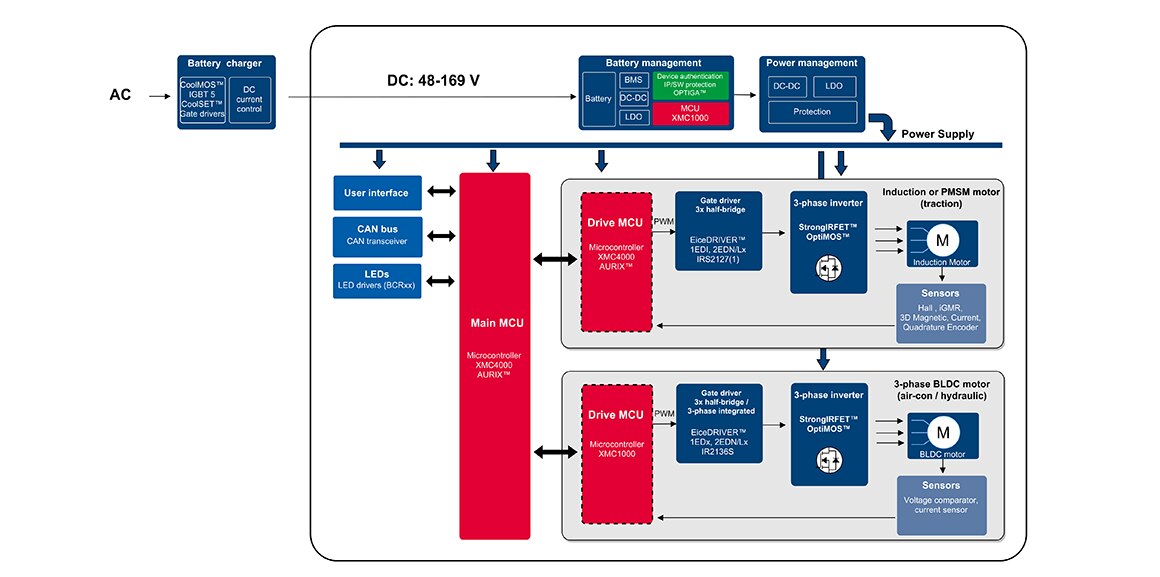
Recommended Products
Motor Control
Part Number | Description | Type | View Details | |
---|---|---|---|---|
![]() |
IPT012N08N5 | TO-leadless, single N-channel OptiMOS™ 5 power MOSFET, 80 V and RDS(on), max = 1.2 mΩ | MOSFET | View Details |
![]() |
IPB019N08N3 G | D2PAK (TO-263) 7-pin, single N-channel OptiMOS™ 3 power MOSFET, 80 V and RDS(on), max = 1.9 mΩ | MOSFET | View Details |
![]() |
IPT015N10N5 | TO-leadless, single N-channel OptiMOS™ 5 power MOSFET, 100 V and RDS(on), max = 1.5 mΩ | MOSFET | View Details |
![]() |
IPB027N10N5 | D2PAK (TO-263), single N-channel OptiMOS™ 5 power MOSFET, 100 V and RDS(on), max = 2.7 mΩ | MOSFET | View Details |
![]() |
1EDI20N12AF | EiceDRIVER™ 1200 V Coreless Transformer IC, single high-side gate driver IC with galvanic isolation, short circuit clamping, and separate sink/source outputs | Gate Driver IC | View Details |
![]() |
2EDL23N06PJ | EiceDRIVER™ Compact - Optimized 600 V half-bridge gate driver IC with LS-SOI technology | Gate Driver IC | View Details |
![]() |
IRFB4110 | TO-220, single N-channel HEXFET® power MOSFET, 100 V and RDS(on), max = 4.5 mΩ | MOSFET | View Details |
![]() |
IPB044N15N5 | D2PAK (TO-263) 7-pin, single N-channel OptiMOS™ 5 power MOSFET, 150 V and RDS(on), max = 4.4 mΩ | MOSFET | View Details |
![]() |
IPP051N15N5 | TO-220, Single N-channel OptiMOS™ 5 power MOSFET, 100 V and RDS(on), max = 5.1 mΩ | MOSFET | View Details |
![]() |
IPB107N20N3 G | D2PAK (TO-263), single N-channel OptiMOS™ 3 power MOSFET, 200 V and RDS(on), max = 10.7 mΩ | MOSFET | View Details |
![]() |
IRF200S234 | D2PAK (TO-263), single N-channel StrongIRFET™ power MOSFET, 200 V and RDS(on), max = 16.9 mΩ | MOSFET | View Details |
![]() |
IPB156N22NFD | D2PAK (TO-263), single N-channel OptiMOS™ Fast Diode (FD) power MOSFET, 220 V and RDS(on), max = 15.6 mΩ | MOSFET | View Details |
![]() |
IPW60R018CFD7 | TO-247, 600 V CoolMOS™ CFD7 power MOSFET | MOSFET | View Details |
![]() |
IKW30N60DTP | TO-247, 600 V DuoPack IGBT (TRENCHSTOP™ Performance) with RAPID 1 fast anti-parallel diode | IGBT Discrete | View Details |
![]() |
IKW50N60DTP | 600 V DuoPack IGBT with RAPID 1 fast anti-parallel diode | IGBT Discrete | View Details |
![]() |
XMC4300-F100K256 | ARM® Cortex®-M4 @ 144MHz | Microcontroller | View Details |
![]() |
AURIX SAK-XC2365B-40F80LR AB | Total memory size of up to 832 kB Flash running at up to 80 MHz | Microcontroller | View Details |
![]() |
OPTIREG™ Tracker (TLS115D0EJ) | Monolithic integrated low-dropout voltage tracking regulator with high accuracy in small packages | Voltage Regulator | View Details |
![]() |
Hall switch (TLE4964-1M) | 3.0 V to 32 V operating supply voltage | Sensor | View Details |
Air Condition
Part Number | Description | Type | View Details | |
---|---|---|---|---|
![]() |
IRFP4668PBF | TO-247AC, single N-channel HEXFET® power MOSFET, 200 V and RDS(on), max = 9.7 mΩ | MOSFET | View Details |
![]() |
IRF200P222 | TO-247AC, single N-channel StrongIRFET™ power MOSFET, 200 V and RDS(on), max = 6.6 mΩ | MOSFET | View Details |
![]() |
IR2136STRPBF | 600 V three phase gate driver IC for IGBTs and MOSFETs with typical 0.2 A source and 0.35 A sink current with overcurrent shutdown | Gate Driver IC | View Details |
Protection
Part Number | Description | Type | View Details | |
---|---|---|---|---|
![]() |
IPB048N15N5LF | D2PAK (TO-263), single N-channel OptiMOS™ 5 LinearFET, 150 V and RDS(on), max = 4.8 mΩ | MOSFET | View Details |
![]() |
OPTIGA™ Trust B SLE95250 | Security / authentication IC for battery packs | Security Chip | View Details |
Low Power Light Electric Vehicles
Low Power Light Electric Vehicles
Low power LEVs can be separated from the rest of higher power LEVs by the following characteristics:
- power level: 1 kW – 10 kW
- voltage range: 24 V – 72 V
- two- and three-wheelers
- main purpose: short distance passenger transport
- value drivers: system cost, power density
Target applications:
- E-scooters (standing / self-balancing and folding types)
- E-bikes
- E-rickshaws / E-three-wheelers
In contrast to the relatively small volumes of EVs, millions of electrified two-wheelers have already been sold worldwide. Especially in emerging Asian markets (India, Indonesia, Vietnam, etc.), where two-wheelers are considered by many as the “family car”, a fast transition to electric versions is noticeable. Why? The environmentally friendly vehicles offer a very high degree of mobility combined with convenience and other fun factors. All that at much lower initial and operational costs compared to typical EVs. Emission-free driving versus congested city traffic – governments around the globe are alerted that it is time for greener politics in favor of light e-mobility (e.g. supporting innovative concepts such as dockless e-scooter sharing services or downtown traffic area accessible only via e-two-wheelers).
And not to forget about the electric-vehicle revolution silently happening in India, that is not at all related to cars. E-rickshaws are taking India’s cities, ten of which according to the World Health Organization rank among the world’s most polluted, by storm. They are quieter, faster, cleaner and cheaper to maintain than traditional auto rickshaws. At the moment growth is only slowed by missing government subsidies for charging infrastructure improvements and easy financing options for owners of traditional rickshaws who wish to switch. Once these are solved sales will most likely exceed a double digit million figure per year if India focuses on electrifying two-wheelers and three-wheelers. Already today, the South Asian nation is home to about 1.5 million battery-powered, three-wheeled rickshaws – a fleet bigger than the total number of electric passenger cars sold in China since 2011.
Top performance versus cost optimization
When it comes to high volume production, the range and speed of low power LEV applications are distinguishing factors. No matter if customers work on designs with either top performance targets or rather concentrate on cost optimization, Infineon is prepared to deliver the products they require. With best-in-class solutions for motor control, our customers may maximize levels of space and/or volume savings (e.g. essential for two-wheelers). StrongIRFET™ MOSFETs, to the contrary, are to be chosen for the development of cost optimized solutions whenever space and weight do not form limiting parameters (e.g. for three-wheelers).
iMOTION™ - Digital motor control for e-bikes and e-scooters (see also recommended products)
One particular set of products suitable for low power two-wheelers such as e-bikes and folding e-scooters are Infineon’s iMOTION™ motor control ICs. Integrated into these ICs are all the control and analog interface functions required for sensor-less, field-oriented control (FOC) of PM motors using DC link or leg shunt current measurements. In addition, they feature Infineon’s patented and field-proven motor control engine (MCE) that eliminates software coding from the motor control algorithm development process. Implementing a variable speed drive is reduced to configuring the MCE for the respective motor. Assisted by powerful tools like MCEWizard and MCEDesigner it is possible to have the motor up and running in less than an hour. By comprising both, the required hardware and software to perform sensor-less control of a permanent magnet synchronous motor (PMSM), iMOTION™ ICs provide the highest energy efficient motor system with the lowest system cost for the named applications.
Download
- iMOTION™ MCEWizard v2.1.1
- iMOTION™ MCEDesigner v2.1.1
System diagram: low power light electric vehicles (e.g. e-bike, e-scooter, e-rickshaw)
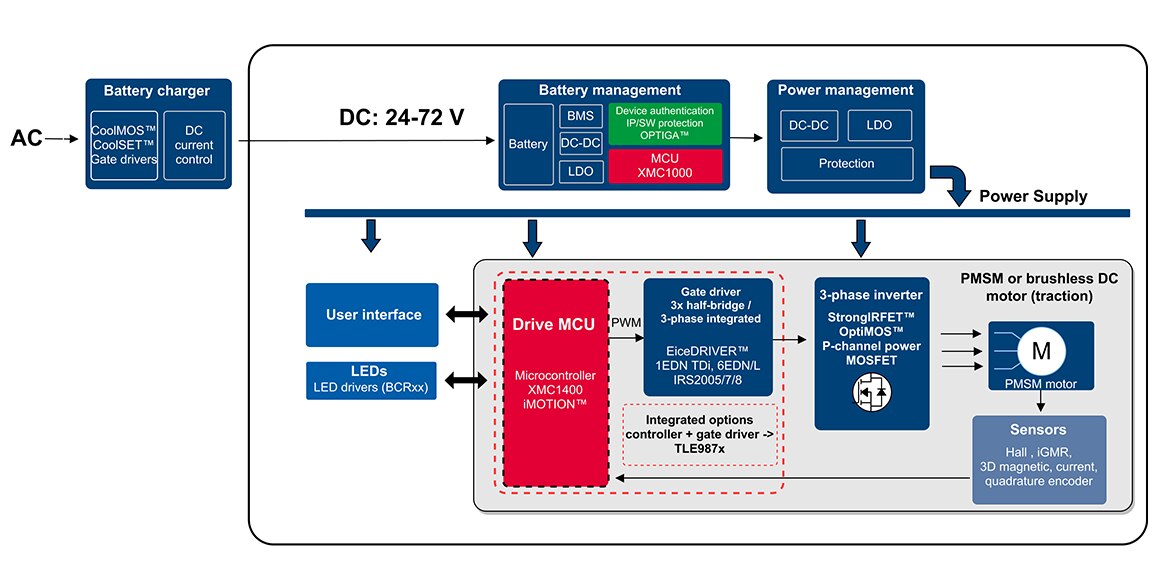
Recommended Products
Motor Control
Part Number | Description | Type | View Details | |
---|---|---|---|---|
![]() |
IRFS3006TRL7PP | D2PAK (TO-263) 7-pin, single N-channel HEXFET® power MOSFET, 60 V and RDS(on), max = 2.1 mΩ | MOSFET | View Details |
![]() |
IPT007N06N | TO-leadless, single N-channel OptiMOS™ power MOSFET, 60 V and RDS(on), max = 0.7 mΩ | MOSFET | View Details |
![]() |
BSC039N06NS | PQFN 5x6mm, single N-channel OptiMOS™ power MOSFET, 60 V and RDS(on), max = 3.9 mΩ | MOSFET | View Details |
![]() |
IRFH7545TRPBF | PQFN 5x6mm, single N-channel HEXFET® power MOSFET, 60 V and RDS(on), max = 5.2 mΩ | MOSFET | View Details |
![]() |
IRFB3607PBF | TO-220AB, single N-channel HEXFET® power MOSFET, 75 V and RDS(on), max = 9.0 mΩ | MOSFET | View Details |
![]() |
IPT029N08N5 | TO-leadless, single N-channel OptiMOS™ 5 power MOSFET, 80 V and RDS(on), max = 2.9 mΩ | MOSFET | View Details |
![]() |
IPP052N08N5 | TO-220, single N-channel OptiMOS™ 5 power MOSFET, 80 V and RDS(on), max = 5.2 mΩ | MOSFET | View Details |
![]() |
IPT015N10N5 | TO-leadless, Single N-channel OptiMOS™ 5 power MOSFET, 100 V and RDS(on), max = 1.5 mΩ | MOSFET | View Details |
![]() |
IPB017N10N5 | D2PAK (TO-263) 7-Pin, single N-channel OptiMOS™ 5 power MOSFET, 100 V and RDS(on), max = 1.7 mΩ | MOSFET | View Details |
![]() |
IPB042N10N3 | D2PAK (TO-263), single N-channel OptiMOS™ 3 power MOSFET, 100 V and RDS(on), max = 4.2 mΩ | MOSFET | View Details |
![]() |
IPB048N15N5 | D2PAK (TO-263), single N-channel OptiMOS™ 5 power MOSFET, 150 V and RDS(on), max = 4.8 mΩ | MOSFET | View Details |
![]() |
IRFP4668PBF | TO-247AC, single N-channel HEXFET® power MOSFET, 200 V and RDS(on), max = 9.7 mΩ | MOSFET | View Details |
![]() |
IR2136STRPBF | 600 V three-phase gate driver IC for IGBTs and MOSFETs with typical 0.2 A source and 0.35 A sink current with overcurrent shutdown | Gate Driver IC | View Details |
![]() |
IRS2008SPBF | 200 V half-bridge gate driver IC with shutdown input, typical 0.29 A source and 0.6 A sink currents | Gate Driver IC | View Details |
![]() |
2EDL05N06PF | EiceDRIVER™ Compact, 600 V half-bridge gate driver IC with typical 0.36 A source and 0.7 A sink output currents | Gate Driver IC | View Details |
![]() |
6EDL04N02PR | EiceDRIVER™ Compact, full bridge three-phase gate driver IC with thin-film-SOI-technology | Gate Driver IC | View Details |
![]() |
1EDN7550 | EiceDRIVER™ fast 1-channel low-side 4/8 A gate driver IC | Gate Driver IC | View Details |
![]() |
TLE9877QXW40 | 3-Phase Bridge Driver IC with Integrated ARM® Cortex® M3 | Microcontroller | View Details |
![]() |
XMC1404-F064X0200 | ARM® Cortex®-M0 (32-bit), 200kB Flash | Microcontroller | View Details |
![]() |
IMC101T-F064 | iMOTION™ digital motor controller, highly integrated solution | Motor Control IC | View Details |
![]() |
Hall switch (TLE4964-1M) | Integrated Hall effect switch, 3.0 V to 32 V operating supply voltage | Sensor | View Details |
![]() |
3D Hall sensor (TLE493DW2B6Ax) | 3D magnetic sensor, flux density sensing of ±160mT | Sensor | View Details |
Protection
Part Number | Description | Type | View Details | |
---|---|---|---|---|
![]() |
IPB017N10N5LF | D2PAK (TO-263) 7-Pin, single N-channel OptiMOS™ 5 LinearFET, 100 V and RDS(on), max = 1.7 mΩ | MOSFET | View Details |
![]() |
OPTIGA™ Trust B SLE95250 | Security / authentication IC for battery packs | Security Chip | View Details |
Battery Chargers for Light Electric Vehicles
Battery Chargers for Light Electric Vehicles
Off-board versus on-board battery chargers
Depending on their power requirements, LEV batteries can be charged either directly from the grid (i.e. any standard wall outlet) through a dedicated on-board charger or through the use of a low cost off-board charger.
Off-board chargers are more suitable if:
- the LEV can be easily located / moved close to the charger (even with an empty battery!) (i.e. e-bikes, folding e-scooters)
- the LEV battery does not require a complex battery management system, e.g. low cost sealed lead acid (SLA) batteries (i.e. low cost scooters, electrical wheelchairs)
- whenever charging requires very high power, because of limitations of weight/volume on the vehicle itself – as is the case for electrical forklifts
AC on-board chargers are more suitable if:
- more flexibility in charging is needed (no special infrastructure has to be installed, no need to carry additional charging equipment) (i.e. low speed EVs (quadricycles), golf carts, small electric lift trucks)
- more complex battery management systems are used, e.g. for Lithium ion batteries (i.e. high power e-scooters)
The on-board charger’s performance is evaluated by its power-conversion efficiency and power quality (i.e. total harmonic distortion and power factor). As for all items installed in the vehicle, size (the smaller, the better), weight (the lighter, the better), and lifetime (the longer, the better) are critical parameters. Conventional on-board chargers usually have a two-stage structure consisting of a power factor correction (PFC) stage and a DC–DC power-conversion stage. This specific structure brings along major drawbacks such as low efficiency and circuit complexity, and a bulky intermediate DC link capacitor. Due to high current flowing through the intermediate DC link capacitor significant power loss is caused, what considerably reduces the capacitor lifetime, eventually leading to capacitor failure. As an alternative to the two-stage structure single-stage approaches are being investigated with the aim to eliminate the PFC stage and reduce the DC link capacitance.
Energy efficiency – critical factor in developing countries
At this moment, the battery charger market for LEVs is mostly cost driven, as most LEVs being sold today are low cost two- and three-wheelers. However, as the number of LEVs is expected to grow further, the efficiency becomes particularly important. Taking into account that the vast majority of LEVs sold each year are deployed in developing countries with weak local power grids, every percentage point of efficiency increase translates into significant energy savings. A noteworthy relief of the national power networks!
Infineon’s LEV battery charger solutions
Infineon’s LEV on-board and off-board battery charger solutions comprised of power MOSFETs, gate driver ICs, PWM/flyback based controllers, integrated power stage ICs and microcontrollers are optimized to fit any system. In order to satisfy as many customer requirements as possible different topologies are available and meeting a variety of cost / performance optimization targets is possible.
Customers benefit from small form factors, best-in-class performance ratio (attractive pricing with competitive long term price down roadmap), easy-to-use technologies, powerful and reliable components.
OPTIGA™ Trust – Authentication at its best (see also recommended products)
Another particular aspect of interest for chargers is their close connection with the type of battery stacks that they are supposed to charge. Practically, any LEV manufacturer selects different variants of batteries that best fit its own, very specific applications. The battery chargers must hence be designed with the proper charging algorithms for the corresponding battery stacks chosen by the LEV manufacturer. It is not advisable to connect any charger type to any battery! Otherwise there can be a significant risk of damaging the batteries, and void the manufacturer’s warranty. Infineon’s OPTIGA™ Trust security solution is easy to use and implement, and will ensure that only the right type of charger is used in connection with a certain type of battery, reducing the risk of hazardous damage/fires.
Video Goes here:
CoolMOS™ - Cutting-edge power MOSFET technology (see also recommended products)
Our CoolMOS™ P7 offers the optimized balance between high efficiency and ease of use. Customers may choose from 71 parts in 9 different packages with an impressive RDS(on) granularity ranging from 24 mΩ to 600 mΩ. Industrial and standard grade packages are available.
Our CoolMOS™ CFD7 fulfills customer needs by providing efficiency improvements of up to 1.45 % compared to previous CoolMOS™ families and most similar competitive offerings. Its attractive price convinces with a competitive long term price down roadmap.
Download Battery Charger Application Note
System diagram: 2 kW battery charger for light electric vehicles
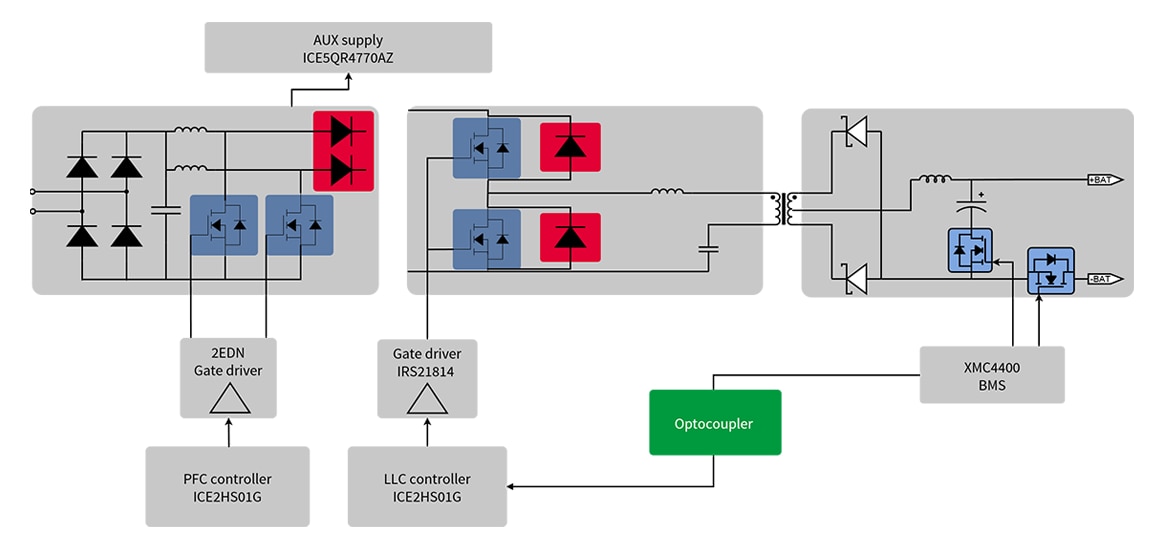
Recommended Products
Charger
Part Number | Description | Type | View Details | |
---|---|---|---|---|
![]() |
IPW60R037P7 | TO-247, 600 V CoolMOS™ P7 power transistor / Superjunction MOSFET, RDS(on), max = 37 mΩ | MOSFET | View Details |
![]() |
IPW60R060P7 | TO-247, 600 V CoolMOS™ P7 power transistor / Superjunction MOSFET, RDS(on), max = 60 mΩ | MOSFET | View Details |
![]() |
IPW60R080P7 | TO-247, 600 V CoolMOS™ P7 power transistor / Superjunction MOSFET, RDS(on), max = 80 mΩ |
MOSFET | View Details |
![]() |
IPW60R070CFD7 | TO-247, 600 V CoolMOS™ CFD7 power transistor / high voltage Superjunction MOSFET with integrated ultrafast body diode, RDS(on), max = 70 mΩ | MOSFET | View Details |
![]() |
IPAW60R280P7S | TO-220 FullPAK wide creepage, 600 V CoolMOS™ P7 power transistor / Superjunction MOSFET, RDS(on), max = 280 mΩ | MOSFET | View Details |
![]() |
IPA70R450P7S | TO-220 FullPAK, 700 V CoolMOS™ P7 power transistor / Superjunction MOSFET, RDS(on), max = 450 mΩ | MOSFET | View Details |
![]() |
IPA80R360P7 | TO-220 FullPAK, 800 V CoolMOS™ P7 power transistor / Superjunction MOSFET, RDS(on), max = 360 mΩ | MOSFET | View Details |
![]() |
IPA95R450P7 | TO-220 FullPAK, 950 V CoolMOS™ P7 power transistor / Superjunction MOSFET, RDS(on), max = 450 mΩ | MOSFET | View Details |
![]() |
IDH16G65C6 | TO-220 real 2pin, CoolSiC™ Schottky diode 650 V G6 for high power PFC topologies | Schottky Diode | View Details |
![]() |
IKB40N65ES5 | D2PAK (TO-263), 650 V / 40 A, high speed switching TRENCHSTOP™ 5, addressing applications switching between 10 kHz and 40 kHz |
IGBT Discrete | View Details |
![]() |
IKB40N65EF5 | D2PAK (TO-263), 650 V / 40 A, high speed switching TRENCHSTOP™ 5 |
IGBT Discrete | View Details |
![]() |
2EDL05N06PF | EiceDRIVER™ Compact, 600 V half-bridge gate driver IC with typical 0.36 A source and 0.7 A sink output currents | Gate Driver IC | View Details |
![]() |
2EDN7524F | Fast dual-channel 5 A EiceDRIVER™ gate driver IC, peak source/sink current |
Gate Driver IC | View Details |
![]() |
1EDN8550 | Fast single-channel, low-side, non-isolated EiceDRIVER™ gate driver IC with 4 A source current/ 8 A sink current |
Gate Driver IC | View Details |
![]() |
ICE2HS01G | High performance resonant mode controller designed especially for high efficiency half-bridge or full-bridge LLC resonant converter with synchronous rectification | AC-DC PWM-PFC Controller | View Details |
![]() |
XMC1301-Q040F0032 AB | 32-bit Microcontrollers with ARM® Cortex®-M0, microcontroller for low cost flyback type chargers | Microcontroller | View Details |
![]() |
XMC4300-F100K256 | EtherCAT® node on an ARM® Cortex®-M4 @ 144MHz with on-chip flash and analog/mixed signal capabilities with outstanding Flash to RAM ratio |
Microcontroller | View Details |
![]() |
ICE5GR4780AG | Fixed frequency CoolSET™ G5, auxiliary power supply with 125 kHz maximum switching frequency and 800 V integrated MOSFET | AC-DC Integrated Power Stage | View Details |
Development and Evaluation
Development and Evaluation
Development Tool:
DAVE™ - professional development platform for XMC™ microcontrollers
DAVE™ and complementary tools supporting the entire development process from evaluation to production (E2P). Experience DAVE™ IDE, XMC™ Lib (Low Level Driver), DAVE™ APPs and examples and reuse in one of the major ARM® compiler/IDEs such as Altium, Atollic, ARM/KEIL, IAR Systems, Rowley.
Evaluation:
Low Voltage Drives Scalable Power Demo Board Platform
Quick Start Guide
Interactive 3D Model

KITLGMBBOM503TOBO1
Target use/applications: Light electric vehicle (LEV) prototyping (Low speed electric vehicles, e-scooters, three-wheelers, golf carts, e-forklifts)
The mother board provides the gate driver IC for 2nd and 3rd phase but it does not include the XMC™-connector.
Features and Benefits:
- Gate resistors on FR4 for ease of rework
- Additional ceramic capacitor connected to the DC bus
- Optional branch out connection for paralleling of MOSFETs
- Scalability and versatility
- Rapid prototyping
- Fast building of customized solutions
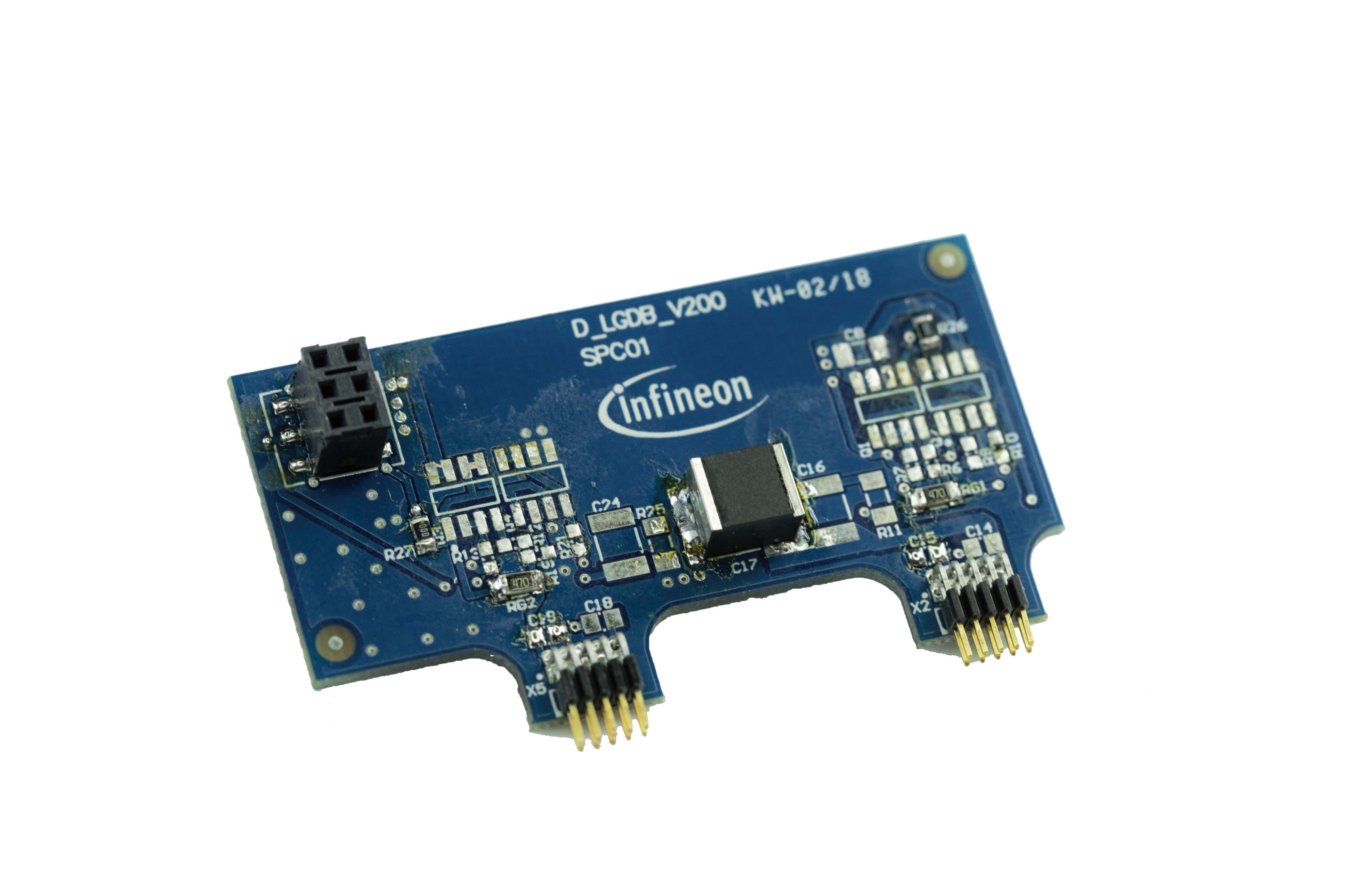
KITLGDBBOM003TOBO1
Target use/applications: Light electric vehicle (LEV) prototyping (Low speed electric vehicles, e-scooters, three-wheelers, golf carts, e-forklifts)
This daughter board is supporting the LVD scalable power demo board platform. Its main function is to provide the system with the interconnection between the gate drivers and the power boards (MOSFET gates). It enables paralleling of the power boards by branching the interconnection of the gate driver signals, and providing each additional MOSFET the respective gate resistor. This board can only be used in conjunction with the LVDSPD mother boards and power boards, serving as the interconnection between the two categories when paralleling the power boards.
Features and Benefits:
- Gate resistors on FR4 for ease of rework
- Additional ceramic capacitor connected to the DC bus
- Connection for paralleling of MOSFETs
- Scalability and versatility
- Rapid prototyping
- Fast building of customized solutions

KITLGMBBOM003TOBO1
Target use/applications: Light electric vehicle (LEV) prototyping (Low speed electric vehicles, e-scooters, three-wheelers, golf carts, e-forklifts)
The master mother board (KIT_LGMB_BOM003) including Infineon’s EiceDRIVER™ half-bridge gate driver IC (2EDL23N06PJ) connects to the first power board (KIT_LGPWR_BOM003) and also provides supply for the XMC™ control card (Evaluation board KIT_XMC4400_DC_V1).
Features and Benefits:
- Gate resistors on FR4 for ease of rework
- Additional ceramic capacitor connected to the DC bus
- Optional branch out connection for paralleling of MOSFETs
- Scalability and versatility
- Rapid prototyping
- Fast building of customized solutions
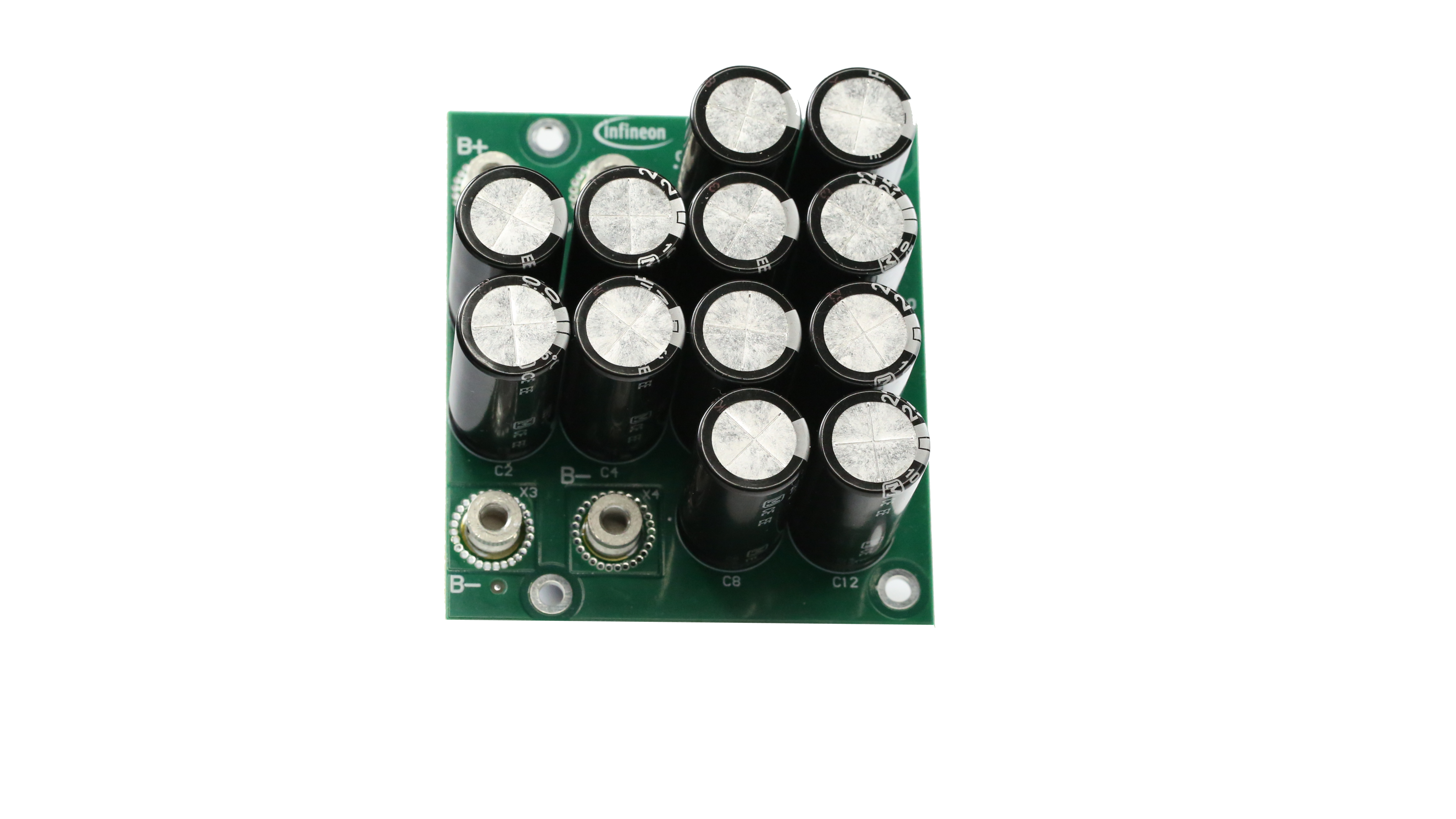
KITLGCAPBOM005TOBO1
Target use/applications: Light electric vehicle (LEV) prototyping (Low speed electric vehicles, e-scooters, three-wheelers, golf carts, e-forklifts)
This capacitor board is a supporting design for the LVD Scalable power demo board platform. It provides the system with an interconnection platform for leaded capacitors for the DC bus supplying the power half-bridges. This board can also be used in other lab setups requiring a DC capacitor bank in the range of up to 250V.
Features and Benefits:
- Connectors for DC bus copper bars
- 7.5 mm radial capacitor footprint
- Scalability and versatility
- Rapid prototyping
- Fast building of customized solutions
Resources
- Application Brochure:
- White Paper:
- Product Selection Guide: