Battery Formation: Your Critical Bottleneck?
Infineon answers with more accuracy, higher power density, and greater efficiency
The world witnesses a rapid rise in the number of battery powered devices – among them more and more electric vehicles (EVs). Consequently, battery manufacturers see themselves confronted with a steady growing demand and hence with the challenge to increase efficiency throughout their factories. Also in battery formation – the known bottleneck given the big investment and the extremely time consuming process. Infineon knows the market and understands the requirements industry players have. Infineon today’s sense for innovation will be your competitive advantage of tomorrow. Continue reading and find out about the full-spectrum system solutions with the respective highlight products.
Battery Formation
The Process
Battery production: 8 main steps
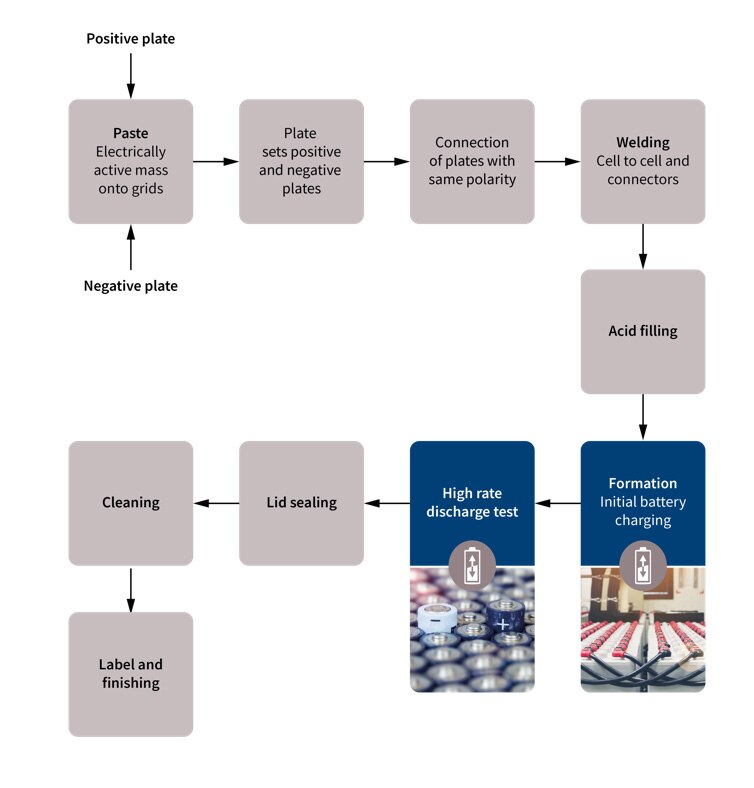
Block Diagram of battery formation system
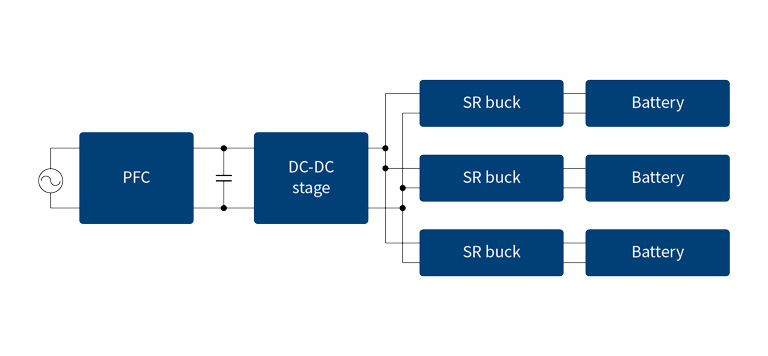
Battery formation is the last step of producing a battery. More precisely, formation is the initial charge and discharge of a newly produced battery. The process, for which high voltage and current accuracy are critical, relies on special battery formation equipment. Formation cycling is expensive because it takes considerable time (up to 20 hours) as each cell must be monitored separately. A true bottleneck! Additionally, with 29 percent the task of “formation cycling and testing” currently accounts for the biggest portion in the breakdown of installed capital equipment costs for the baseline plant.
Prerequisite for market readiness
The process which activates the material in a newly assembled battery cell or pack is essential as it heavily impacts a battery’s quality and cost. Also ensuring that it lasts for the indicated lifetime. Only after testing a battery it can be deemed market-ready.
Power system solutions
Success Factors
Ideally, a suitable battery formation power system solution
- enables high voltage and current accuracy up to 0.01%
- provides thermal management of MOSFETs for higher current rating requirements
- increases the overall power density with higher current rating size
- improves the reliability in 24/7 operation cycles
In general, manufacturers prefer a quality system solution that is not over-engineered. It should have an attractive cost-performance ratio, yet be reliable and stable to facilitate continuous operation under the given conditions. High power density helps them to decrease the solution’s size. And when opting for a standard platform - scalable to fit a wide range of requirements - they are even able to reduce their time to market.
Infineon’s full-spectrum system solutions
Infineon empowers successful designs with more accuracy, higher power density, and greater efficiency. Our full-spectrum system solutions range from the AC grid to battery which requests a highly efficient and power-dense PFC stage and an isolated DC-DC stage. A totem pole PFC converter and a bi-directional DC-DC converter are recommended in our full system silicon solution. An enormous design flexibility will allow designers to meet varying requirements.
Particularly noteworthy: for the non-isolated DC-DC buck-boost stages our products enable the achievement of high power density leading to improved efficiency. Infineon’s comprehensive portfolio of surface mounted devices (SMD) will satisfy those prioritizing lower BOM count and higher power density compared with a package supported by the PCB board.
System diagram: Bi-directional battery formation
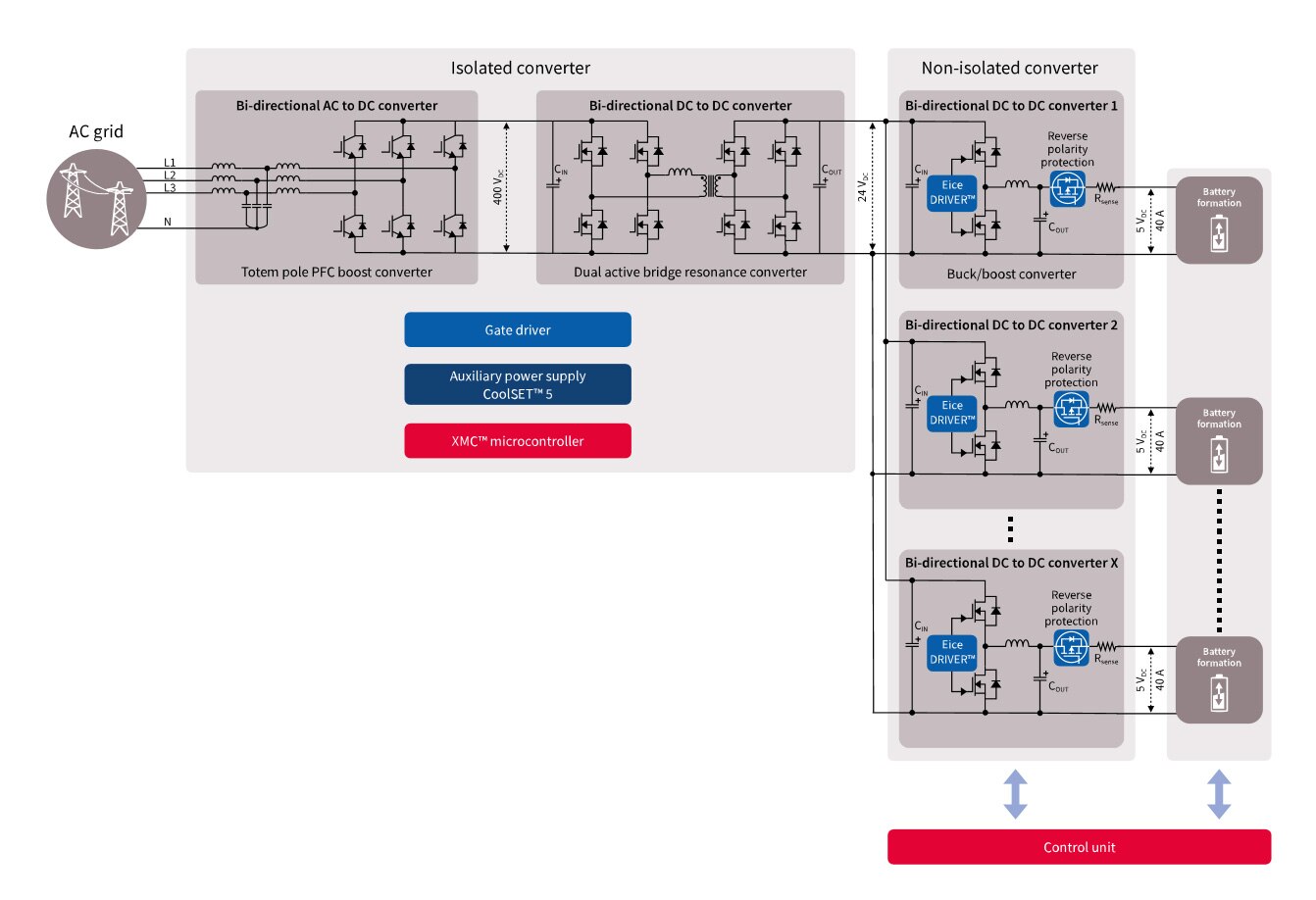
Explore our system solutions and get started with your new battery formation power system designs today.
AC-DC Stage: Bi-directional Converter
Power | Stage | CoolMOS™ and IGBT | Drivers |
---|---|---|---|
2 KW | PFC | IPW60R090CFD7 TRENCHSTOP™ H5 |
2EDFx, 2EDSx, 2EDNx, 1EDIx |
4 KW | PFC | IPW60R040CFD7 TRENCHSTOP™ H5 |
2EDFx, 2EDSx, 2EDNx, 1EDIx |
2 KW | Isolated DC-DC primary side | IPW60R105CFD7 | 2EDFx, 2EDSx, 2EDNx, 1EDIx |
4 KW | Isolated DC-DC primary side | IPW60R090CFD7 | 2EDFx, 2EDSx, 2EDNx, 1EDIx |
Auxiliary Power Supply | CoolSET™ 5 - ICE5QR4780AZ | ||
Microcontroller | XMC™ 4000 family |
Isolated DC-DC Secondary Side*
Vout | MOSFET Breakdown Voltage |
SMD Package OptiMOS™ 6 and OptiMOS™ 5 | |||
---|---|---|---|---|---|
D2PAK | SSO8 | TOLL | D2PAK 7pin | ||
12 V | 40 V | IPB015N04L G (1.5 mΩ) | BSC007N04LS6 (0.7 mΩ) | IRL40T209 (0.7 mΩ)** | IPB011N04L (1.1 mΩ) |
24 V | 60 V | IPB019N06L3 G (1.9 mΩ) | BSC012N06NS (1.2 mΩ) | IPT007N06N (0.75 mΩ) | IPB014N06N (1.4 mΩ) |
48 V | 100 V | IPB020N10N5 (2.0 mΩ) | BSC027N10NS5 (2.7 mΩ) | IPT015N10N5 (1.5 mΩ) | IPB017N10N5 (1.7 mΩ) |
96 V | 150 V | IPB048N15N5 (4.8 mΩ) | BSC093N15NS5 (9.3 mΩ) | IPT059N15N3 (5.9 mΩ) | IPB044N15N5 (4.4 mΩ) |
96 V | 200 V | IPB107N20N3 (10.7 mΩ) | BSC220N20NSFD (22 mΩ) | IPT111N20NFD (11.1 mΩ) | |
Drivers | 1EDN7550B, 2EDF7275X | ||||
Micrcontrollers | XMC™ 4000 family |
Non-isolated bi-directional DC-DC stage*
Vin | MOSFET Breakdown Voltage |
SMD package OptiMOS™ 6 and OptiMOS™ 5 | THD package OptiMOS™ and StrongIRFET™ | ||||
---|---|---|---|---|---|---|---|
D2PAK | SSO8 | TOLL | D2PAK 7pin | TO-220 | TO-247 | ||
12 V | 30 V | IRLS3813PbF (1.95 mΩ) | BSC011N03LS (1.1 mΩ) | IPT004N03L (0.4 mΩ) | IPB009N03L (0.95 mΩ) | IRLB3813 (1.95 mΩ) | IRFP3703 (2.8 mΩ) |
24 V | 40 V | IPB015N04L G (1.5 mΩ) | BSC007N04LS6 (0.7 mΩ) | IRL40T209 (0.7 mΩ)** | IPB011N04L (1.1 mΩ) | IRLB3034 (2.0 mΩ) | IRFP7430PBF (1.3 mΩ) |
48 V | 60 V | IPB019N06L3 G (1.9 mΩ) | BSC012N06NS (1.2 mΩ) | IPT007N06N (0.75 mΩ) | IPB014N06N (1.4 mΩ) | IPP020N06N (2.0 mΩ) | IRFP7530 (2.0 mΩ) |
96 V | 100 V | IPB020N10N5 (2.0 mΩ) | BSC027N10NS5 (2.7 mΩ) BSC093N15NS5 (150 V, 9.3 mΩ) |
IPT015N10N5 (1.5 mΩ) | IPB017N10N5 (1.7 mΩ) | IPP023N10N5 (2.3 mΩ) | IRF100P219 (1.7 mΩ) |
96 V | 200 V | IPB107N20N3 (10.7 mΩ) | BSC220N20NSFD (22 mΩ) | IPT111N20NFD (11.1 mΩ) | IPP110N20N3 (11 mΩ) | IRF200P222 (6.6 mΩ) | |
Drivers | 1EDN7550B, 2EDF7275X |
* Best-in-class products for given package
** StrongIRFET™
Recommended MOSFETs and Driver ICs
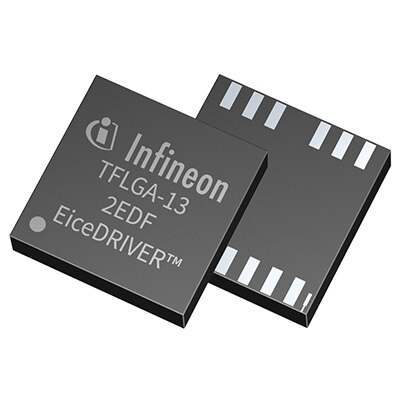
2EDF7275KXUMA1
EiceDRIVER™ 2EDi family, dual-channel, functional isolated, PG-TFLGA-13
View Details »
Recommended Evaluation Board
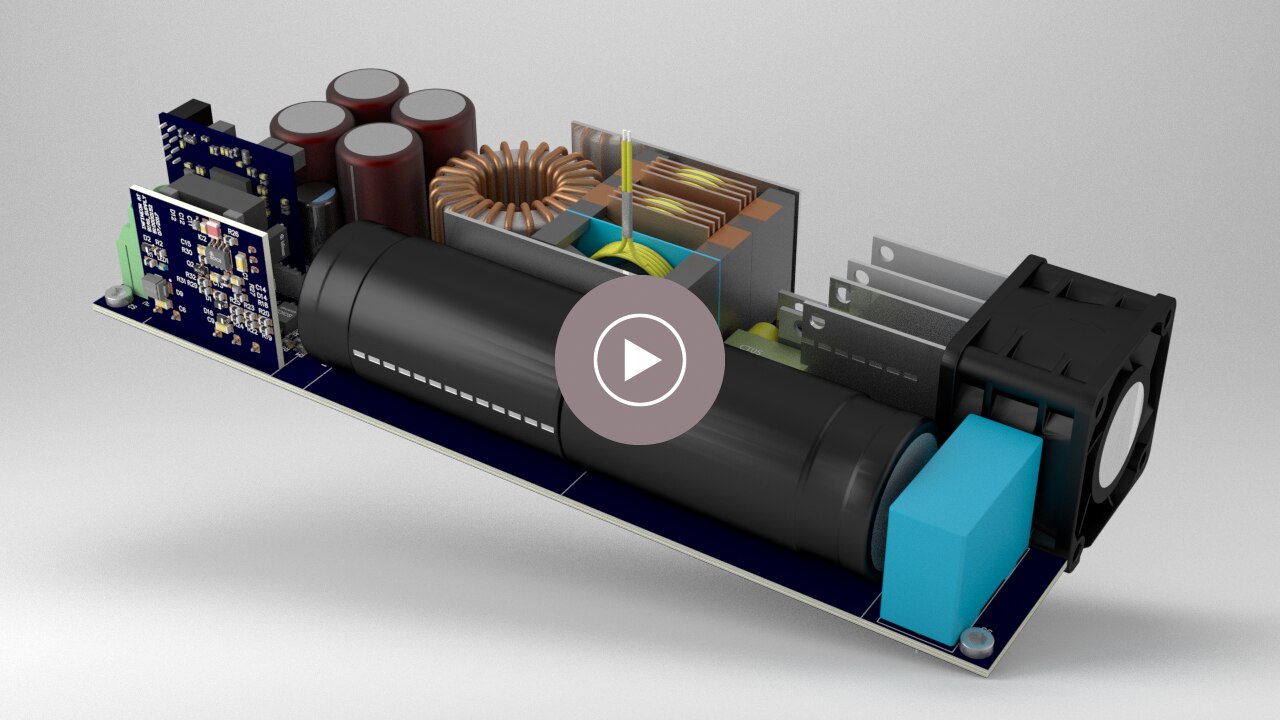
EVAL_3K3W_BIDI_PSFB: 3300 W, 54 V bi-directional SMPS phase-shift full-bridge solution featuring 600 V CoolMOS™ CFD7 and XMC™
This evaluation board represents a complete system solution for a 3300 W telecom/battery charging DC-DC converter block which achieves 98% efficiency peak. The DC-DC converter is composed of a ZVS PSFB with bi-directional capability (patent pending).
Target applications: battery formation power system, EV charging, telecom
Features:
- Innovative cooling concept and stacked magnetic structure for high power density in a full SMD solution
- Full digital control. Peak current mode and novel control algorithms (patent pending) enabling best voltage class devices and improved performance
- Bi-directional capability of PSFB without additional circuitry or impact on forward operation performance (patent pending)
- High efficiency PSFB design at the level of fully resonant topologies (LLC)
- Fast body diode devices for improved reliability in all working conditions
- Graphical user interface (GUI available for customers upon registration)
Benefits:
- Optimal use of CoolMOS™ and OptiMOS™ best-in-class devices
- Full SMD solution. Reduced BOM and assembly effort
- High efficiency converter block realized by a low complexity topology
View Details Datasheet