Manufacturers Shift Attention to Light Quality to Further LED Market Share Gains
投稿人:电子产品
2014-12-09
In its early incarnations, solid-state lighting (SSL) struggled to compete with conventional lighting because it was expensive and, frankly, not very bright. However, as manufacturers improved the output and efficiency of their devices and better manufacturing techniques pushed down prices, SSL’s share of the lighting market rapidly expanded.
Today’s quality products from the major suppliers offer unprecedented luminosities and efficacies, and although further incremental improvements are likely, the performance of contemporary products is such that the focus has shifted to enhancing the “quality” of an LED’s light. Chipmakers are now spending their research dollars developing products with improved color rendering index (CRI) and limited correlated color temperature (CCT) variance with temperature and dimming.
This article describes how contemporary LEDs have overtaken conventional lighting in terms of efficacy while the price gap has shrunk dramatically. The article then explains how manufacturers have turned their attention to light quality, and even user-controller “color tuning”, to further increase their market share.
A short history of lighting LEDs
Many engineers are surprised to learn that the history of the LED stretches back over a century to the discovery of electroluminescence in 1907 when Briton H. J. Round of Marconi Labs experimented with a crystal of silicon carbide and a cat’s-whisker detector.
However, the first key discovery that led to today’s high-brightness white LEDs happened in 1962 as a by-product of Nick Holonyak Jr.’s quest to develop a laser diode. Holonyak was employed by Bell Labs and was working with semiconductor diodes comprising gallium arsenide phosphide when he observed that adding more phosphorus to the gallium arsenide material increased its band gap, shortening the wavelength of the emitted light from the infrared to the visible red. Since the light was not coherent, Holonyak’s device was a “light emitting” diode rather than a laser diode.
Further experimentation produced different-colored LEDs. However, from Holonyak’s original discovery in the early 60s, until the early 90s, the lack of a blue device (a critical component for a white light source) consigned LEDs to tasks such as indication, rather than general illumination.
The second key discovery began in 1986 when Isamu Akasaki and Hiroshi Amano of Nagoya University in Japan came up with a way of creating gallium nitride (GaN) crystals on a sapphire substrate. Others had explored GaN’s potential as an emissive semiconductor but no one had managed to either grow crystals of suitable quality or produce the p-type material needed to fabricate an LED junction. By the end of the 1980s Asaki and Amano had cracked both problems.
Meanwhile, Shuji Nakamura, working for Nichia, a Japanese chemical company, was independently working with GaN as the basis of a blue LED. He found a much cheaper way than Asaki and Amano to produce p-type material by heating the crystal instead of bombarding it with an electron beam.
Later, Nichia researcher Yasunobu Noguchi developed an yttrium aluminum garnet (YAG) phosphor that could convert blue photons to yellow, and finally, Kensho Sakano combined Noguchi’s phosphor with a blue LED die to make a white LED. Asaki, Amano, and Nakamura were awarded the 2014 Nobel prize in physics for the invention of the blue LED¹ (Figure 1).
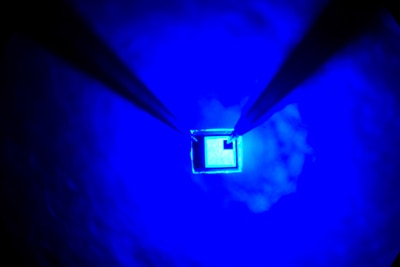
Figure 1: The blue LED enabled today’s generation of solid-state lighting.
Nichia’s first commercial white LED from 1996 could produce 5 lm/W. With intense development, the company had improved that figure to 50 lm/W by 2003. This made solid-state lighting a viable alternative to incandescent bulbs (with an efficacy of 10 to 18 lm/W) and other lighting technologies such as compact fluorescent lights (35 to 60 lm/W) and fluorescent tubes (80 to 100 lm/W) — albeit at high prices for the early adopters among the buying public.
Since then, manufacturers such as Cree, OSRAM, Philips Lumileds, and Seoul Semiconductor have made further rapid improvements in efficacy and luminosity. The result of their endeavors has seen luminosity and efficacy doubling approximately every three years following a trend known as Haitz’s law (analogous to Moore’s law for CMOS-based chips). Meanwhile, prices have plummeted by 20 percent per year in terms of dollars per lumen² (Figure 2).
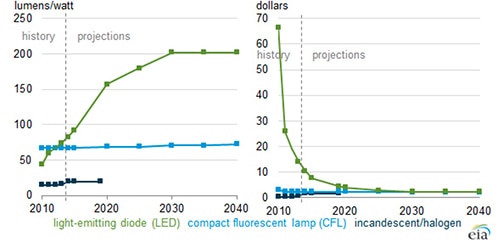
Figure 2: Efficacy and cost of LEDs compared with other lighting technologies. (Courtesy of the U.S. Energy Information Administration)
Now, just under two decades after the launch of Nichia’s first white LED, commercial devices boast efficacies around 30 times that of early LEDs (see the TechZone article “Material and Manufacturing Improvements Enhance LED Efficiency”). For example, a review of the latest launches from various manufacturers shows that Cree’s XLamp XP-L produces 145 lm/W (forward current 1.05 A, forward voltage 2.95 V) with Philips Lumiled’s LUXEON Z (500 mA, 2.8 V) producing 108 lm/W. For its part, Seoul Semiconductor provides the Z5-M1 white LED, which puts out 140 lm/W (350 mA, 2.95 V). (Note that the devices listed here are not necessarily direct equivalents and are examples only. All manufacturers listed make a wide range of LEDs offering varying efficacies and luminosities and engineers should check the datasheets for full specifications.)
Focus on quality
Since the luminosity and efficacy of white LEDs is now easily good enough to meet consumers’ expectations, manufacturers have switched their attention to improving the “quality” of the devices’ light rather than further increasing the “quantity” of lumens per watt.
There are two key parameters used to quantify the light quality from a white LED: CRI and CCT.
CRI is a quantitative measure of the ability of a light source to reproduce the colors of various objects faithfully in comparison with an ideal or natural light source. CRI is calculated from the differences in the chromaticities (or “color appearance”) of eight CIE standard color samples when illuminated by the light source under test and then by a reference illuminant of the same CCT. The smaller the average difference in chromaticities for the eight samples between the reference illuminant and the light under test, the higher the CRI. (See the TechZone article “What Is the Color Rendering Index and Why Is It Important?”.)
Natural light is classified as having a CRI of 100, the best possible. Incandescent lamps have a CRI above 95, halogen lamps 90 or better, and compact fluorescent lights (CFL) 80. Today’s LEDs perform well, recording values of 80 to 90. OSRAM’s SSL 150 White LEDs, for example, exhibit a CRI of 83.
Not content with matching the CRI of traditional light sources, LED makers have worked hard to improve their products’ CRI when a vibrant red (R9) is included along with the eight standard samples. Previously, LEDs performed poorly in the extended test —recording scores as low as 20 — because their spectral power distribution (SPD) tended to include few red wavelengths; consequently, red or predominantly red objects appeared dull.
White LED manufacturers have addressed this deficiency to some extent by modifying the YAG phosphor to enhance red wavelengths in the SPD and substituting a blue LED for an ultraviolet to gain further improvements.
The new phosphors do have an impact of the device’s efficacy, but because LEDs now have such high intrinsic efficacy, many manufacturers consider a small loss a reasonable commercial compromise to improve CRI when R9 is included in the test. For example, Philips Lumileds LUXEON T range includes a device with a CRI of 95 when R9 is not included in the test and 90 when it is. The chip still has an efficacy of 82 lm/W (2.51 V, 700 mA) [See the TechZone article “Illuminating the Limitations of CRI Testing”].
Limiting color variance
LED makers have also worked hard to develop LEDs that emit light closely matching the color (or “temperature”) of the illumination given out by traditional lighting sources to meet the tough demands of consumers. Manufacturers produce white LEDs with outputs classed as “warm white” (2,600 to 3,700 K CCT), “neutral white” (3,700 to 5,000 K CCT), and “cool white” (5,000 to 8,300 K CCT) grouped into “bins” comprising devices of very similar color output. A lighting designer looking to use an array of LEDs for his or her fixture chooses devices from the same bin to ensure color consistency across the array.
The CCT is defined using the Commission Internationale de l'Eclairage (CIE) chromaticity space (CIE 1931 x, y, z). The LED’s output lies on or close to the Planckian locus that corresponds to the color that an incandescent “black body” would appear to radiate with changes in temperature (Figure 3).
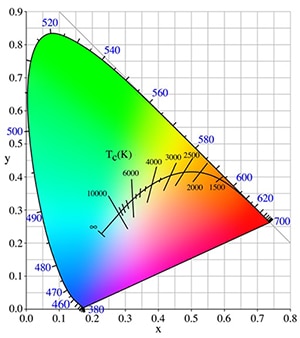
Figure 3: CIE xy 1931 chromaticity diagram with Planckian locus and lines of correlated color temperature.
Unfortunately, as the temperature of the LED rises, the atoms comprising the crystal lattice making up the chip vibrate more, which slightly increases the lattice constant (the dimensions of the crystal’s “unit cell”). This in turn decreases the band gap, which increases the wavelength of the emitted photons.
The net effect is that the output from a blue LED “photon pump” shifts slightly to the red end of the spectrum, and the yellow photons emitted from the phosphor are in turn slightly affected. The output of the SSL — being a combination of the spectra from these two sources — is also altered.
While manufacturers have attempted to minimize the CCT variance due to temperature of their products, some drift is inevitable. Chipmakers specify the CCT of their devices at 25°C and then provide information in the specification sheet as to how far the CCT of a particular device drifts with temperature rise. The good news is that it does take quite a large temperature increase to make the CCT shift noticeable to the human eye.
The bins into which the manufacturers group their products are defined by quadrilaterals on the CIE color space, the borders of which indicate the limit of CCT change with temperature before things become noticeable. The datasheet for a Cree XLamp XP-E, for example, shows that the device will not exhibit a perceptible CCT shift provided its junction temperature does not rise above 90°C (Figure 4).
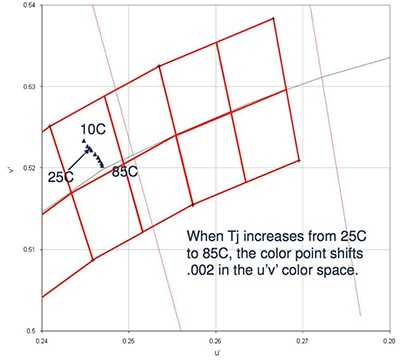
Figure 4: Cree XP-E LED chromaticity shift in the CIE 1976 L, u’, v’ color space. (Courtesy of Cree)
LEDs can run perfectly well at higher junction temperatures than 90°C, of course, but in addition to unacceptable CCT shift, high operating temperatures also shorten the life of the LED so it’s incumbent on the designer to keep his or her device temperature down to reasonable levels by adequate thermal management (see the TechZone article “Thermal Effects on White LED Chromaticity”).
However, it’s not just temperature that changes the color of an LED, analog dimming — an inexpensive technique that is popular for dimming many conventional light sources — can affect it too.
This problem occurs because the wavelength of every emitted photon from a given LED at a given forward voltage is not exactly the same. Wavelengths vary according to a bell-shaped curve centered on a dominant frequency.
The luminosity of the LED is proportional to the forward current, which in turn is proportional to the forward voltage (above a threshold voltage). It turns out that reducing the forward voltage to dim the LED shifts the bell-shaped curve so that the dominant frequency occurs at a slightly shorter wavelength, changing the color.
Manufacturers have addressed this problem by implementing LED drivers incorporating digital dimming. The technique maintains a constant forward voltage (and forward current), but uses pulse width modulation (PWM) to rapidly cycle the LED on and off. By altering the duty cycle of the pulse train, the light can be dimmed without color variation (see the TechZone article “Digital Dimming Solves LED Color Dilemma”).
Lighting for the 21st century
Despite the success of manufacturers to maintain color consistency, some LED makers are looking to use the flexibility of LEDs to differentiate their products from conventional lighting by actively encouraging consumers to change the color — but this time in a controlled manner.
Combining red, green, and blue (RGB) LEDs is an alternative method for producing white light. However, such devices have struggled to gain market share because of the poor efficacy of the green LED which drags down the overall performance.
Now, however, a lime-green LED from Philips Lumileds’ Rebel ES family (Figure 5) is helping to address the problem. The lime-green device is not a pure-color LED, rather a combination of blue emitter and proprietary lime phosphor that overcomes the efficiency problems of green devices. According to the Philips Lumileds’ datasheet, this blue LED/green phosphor combination is capable of an efficacy of up to 190 lm/W (2.75 V, 350 mA).
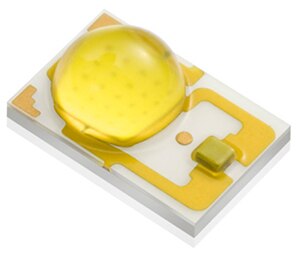
Figure 5: Philips Lumileds is offering its lime-green LED for RGB light engines in color-tunable applications.
The lime-green LED is incorporated into the Hue bulb from Philips, which fits into a standard light socket, and allows consumers to alter the bulb’s output using a wirelessly connected smartphone- or tablet computer-based app. The app matches the LED output colors to a rainbow palette, or even to the user's favorite images.
Other manufacturers are addressing the poor efficacy of pure-color green LEDs directly. There are already some impressive devices on the market; for example, Cree’s 528 nm green chip from its XLamp XP-E1 family produces 84 lm/W (3.4 V, 350 mA.)
LEDs are maturing fast. The technology always offered the potential to be more efficient and last longer than conventional lighting, but now, after years of investment in research and commercialization, that promise has been realized. The devices’ performance is superior to virtually all types of conventional lighting and prices continue to drop. Moreover, manufacturers have made great strides in addressing color quality and consistency such that any change in the tone of a LED lighting fixture due to temperature or dimming is imperceptible. The next step, which will cement LEDs as the lighting technology of the future, is user-controlled dimming and hue, via smartphone control, to suit the consumer’s mood.
For more information on the parts discussed in this article, use the links provided to access product pages on the DigiKey website.
References
- “Blue LEDs — Filling the world with new light,” The Nobel Prize in Physics 2014 Popular Science Background, The Royal Swedish Academy of Sciences, 2014
- “Light Emitting Diodes and the Lighting Revolution: The Emergence of a Solid-State Lighting Industry,” Susan Walsh Sanderson, Rensselaer Polytechnic Institute, October 2013.
免责声明:各个作者和/或论坛参与者在本网站发表的观点、看法和意见不代表 DigiKey 的观点、看法和意见,也不代表 DigiKey 官方政策。