Sensor Solutions for Challenging Industrial Applications
投稿人:电子产品
2014-05-01
Industrial control settings were some of the earliest environments for modern sensors. As demands for systems to monitor safety and efficiency increased, sensors designed to perform reliably in challenging environments were used to keep tabs on such concerns as heat, flow, and vibration. They also enabled operators to stay a safe distance from hazardous situations.
Sensors for industrial applications now include a very broad base of sensor types: temperature, pressure, chemical, proximity, force, and load and level. Enabling and supporting technologies include MEMS, nanotechnology, and wireless communications.
Wireless sensors are being employed in systems such as supervisory control and data acquisition, proving that these devices can effectively address the needs of industrial applications. These wireless sensors mostly are being used for position, proximity, image, and security applications. A key factor for their success will be low power consumption; the wireless sensor networks of the not-so-distant future will harvest energy for untethered industrial products that will be disconnected from electrical outlets (see the TechZone article “Energy Harvesting Wireless Sensors”).
Today, from vision to M2M communications, sensors in industrial settings have come into their own. As the factory floor moves rapidly towards greater automation, sensors are an important enabler; they are at the heart of an expansion in industrial capabilities being called “ Industry 4.0”, a term referring to the fourth industrial revolution, encompassing the introduction of new methods of self-optimization, self-configuration, self-diagnosis, cognition, and intelligent support of workers in their increasingly complex tasks.
The goal is the intelligent factory (Smart Factory), which is characterized by adaptability, resource efficiency, and ergonomic improvements, and is being supported by robotics, automated systems and the so-called “Internet of Things” (IoT).
As we will see, it is sometimes the application and at other times the harsh or at least unfriendly operating environment that dictates the type of sensor used and its properties. The Texas Instruments LDC1000 (Figure 1) is the world’s first inductance-to-digital converter, offering the benefits of inductive sensing in a low-power, small-footprint solution. The product is available in a SON-16 package and offers several modes of operation. An SPI interface simplifies connection to an MCU.
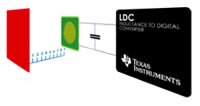
Inductive sensing is a contactless, magnet-free short-range technology that enables high-resolution sensing of conductive targets in the presence of non-conductive interference from dust, dirt, oil, and moisture. The sensor can be a wound wire, a coil on a PCB, a coil printed with conductive ink on a flexible substrate, or even a simple spring. It supports remote sensor placement, making it well-suited for extreme and harsh environments.
Inductive sensors generate and use a high-frequency oscillating magnetic field. The metal target entering the sensing field induces eddy currents in the target, which reduces the signal amplitude of the oscillator. The detector circuit then recognizes the specific change in amplitude and generates a signal which will turn the solid-state sensor output “on” or “off”.
Inductive sensing technology enables precise measurement of linear/angular position, displacement, motion, compression, vibration, metal composition, and many other applications. It enables sub-micron resolution in position-sensing applications with 16-bit resonance impedance and 24-bit inductance values. Inductive sensing can be used to measure the position, motion, or composition of a metal or conductive target, as well as detect the compression, extension, or twist of a spring.
Another example of an industrial sensor is the Silicon Labs’ Si7013 single-chip relative humidity and temperature sensor that is used for industrial HVAC in thermostats, humidistats, and other similar devices. The sensor is a monolithic CMOS IC that integrates humidity and sensing elements, an analog-to-digital converter, signal processing, calibration, and an I²C interface.
The humidity and temperature sensors are factory-calibrated and the calibration data is stored in the on-chip non-volatile memory. Sensors are fully interchangeable, with no recalibration or software changes required.
An auxiliary sensor input with power management can be tied directly to an external thermistor network or other voltage-output sensor. The Si7013 is available in a 3 x 3 mm DFN package and is reflow solderable.
Other features include:
- Precision relative humidity sensor
- Temperature sensor
- Auxiliary second zone sensor input (Si7013)
- 0 to 100% RH operating range
- Up to -40° to 125°C operating range
- Wide-operating voltage range (1.9 to 3.6 V)
- Low power consumption
- I²C host interface
- Integrated on-chip heater
- 3 x 3 mm DFN package
- Excellent long-term stability
- Factory calibrated
- Lifetime protection during reflow and in operation
- AEC-Q100 automotive qualified
The 20.48 ksample/s sampling rate and 5 kHz flat frequency band provide a frequency response suitable for many machine health applications. The aluminum core provides excellent mechanical coupling to the MEMS acceleration sensors.
An internal clock drives the data sampling and signal processing system during all operations, which eliminates the need for an external clock source. The data capture function has three modes that offer several options to meet the needs of many different applications. In addition, its real-time mode provides direct access to streaming data on one axis.
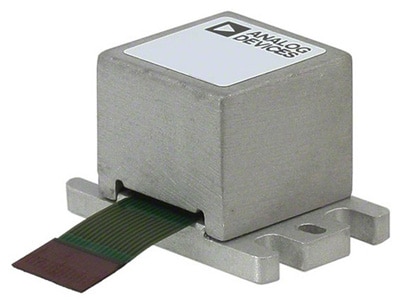
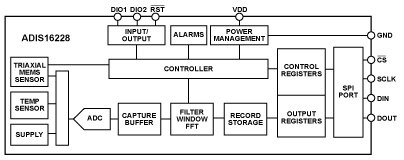
The SPI and data buffer structure provides convenient access to data output. The ADIS16228 also offers a digital temperature sensor and digital power supply measurements. The device is used in such industrial applications as vibration analysis, condition monitoring, machine health, instrumentation, diagnostics, and safety shut-off sensing. It is available in a 15 × 24 × 15 mm module with flanges, M2 machine screw holes, and a flexible connector that enables simple user interface and installation. The ADIS16228 is footprint and pin-for-pin compatible with the supplier’s ADIS16210 digital inclinometer system that provides precise measurements for both pitch and roll angles over a full orientation range of ±180°. The ADIS16228 has an extended operating temperature range of −40° to +125°C.
Analog Devices’ ADIS16000 and ADIS16229 (with an embedded RF receiver) enable the creation of a simple wireless vibration sensing network for a wide variety of industrial equipment applications. The ADIS16000 provides the gateway function, which manages the network, while the ADIS16229 provides the remote sensing function.
The proliferation of advanced electronic control systems has resulted in greater sensor accuracy, reliability, response time, robustness, miniaturization, communications capability, and efficiency. This, in turn, has fueled R&D, furthering opportunities for new sensor applications. Going forward, industrial facilities will all be equipped with more intelligence to better manage complexity, safety, and operations. Sensor systems for these applications are likely to be very small, use little power, and cost a fraction of earlier sensors that did not tightly integrate smart electronics to sensing elements. What’s more, these devices often are housed in a single chip and will operate wirelessly.
In this article we have presented some recent sensors that are well suited to the industrial environment. For more information on the parts discussed here, use the links provided to access product information pages on the DigiKey website.
免责声明:各个作者和/或论坛参与者在本网站发表的观点、看法和意见不代表 DigiKey 的观点、看法和意见,也不代表 DigiKey 官方政策。