How to Protect RS-485 Buses in Industrial Environments
投稿人:DigiKey 北美编辑
2019-09-17
Though electronics and connected systems are an increasingly integral part of the modern industrial complex, that environment remains hostile to electronics. High power motors, large relays, solenoids, actuators, and similar devices generate electromagnetic fields, while high voltage electrostatic discharges (ESDs), fast transients, and inductively coupled surges and even lightning are commonplace. So much so that a serial bus like RS-485, with its long transmission distances, requires a host of special tools to keep it stable and reliable.
RS-485, also referred to as Telecommunications Industry Association and Electronic Industries Alliance (TIA/EIA)-485, is an asynchronous serial data bus that was actually intended for industrial applications where its 4000 foot (ft) reach suits factory floor installations. Despite RS-485’s inherent ruggedness, designers of industrial systems that rely on it need to take pre-emptive measures to ensure bus stability and longevity, particularly as processes become increasingly dependent upon accurate data and constant feedback.
These measures include giving due consideration to shielded cables, transient suppression diodes, ESD and surge tolerant transceivers, and signal pre-emphasis. This article looks at how to employ these protection solutions and techniques to meet existing electromagnetic compatibility (EMC) standards and ensure reliable data communications in a harsh environment.
Threats to electronic devices in industrial environments
There are three major types of electromagnetic interference (EMI) threats to electronic devices used in industrial settings: ESD, electrical fast transients (EFTs), and electrical surge transients. ESD is generally associated with human interaction and the transfer of electrical charge, developed by the triboelectric effect, to a device. ESD events represent the lowest energy transients. EFT is the result of relay contact bounce or the interruption of inductive loads, while transient surge is the result of major interruptions like a lightning strike, motor loading, hot-plug events, or short circuits. Surge generally imparts the highest energy transients.
Designers are helped by a series of related international standards intended to help test industrial devices for robustness and reliability in the presence of these EMC threats. The International Electrotechnical Commission (IEC) created and maintains the IEC 61009-4 series standard for EMC. The standards are:
- IEC 61000-4-2 for ESD immunity
- IEC 61000-4-4 for EFT immunity
- IEC 61000-4-5 for transient surge immunity
Each of these standards specifies tests to assure that devices can withstand the relevant EMC threats. Each test employs specific waveforms, applied in bursts, to simulate the given type of event. The power associated with each individual waveform varies, with ESD being the least powerful. Surge transient waveforms have the greatest power (Figure 1).
Figure 1: The relative power of the ESD, EFT, and surge test waveforms for specific types and classes of IEC 61000-4 testing. The average power levels are proportional to the duration of the transient pulse as well as the peak amplitude. (Image source: Texas Instruments)
The left-hand grid shows the relative power of a 10 kilovolt (kV) ESD, a 4 kV EFT, and a 0.5 kV surge. The right-hand grid shows the relative power levels of a 0.5 kV and 6 kV surge. As can be seen, the average power levels are proportional to the duration of the transient pulse as well as the peak amplitude.
Peak power levels vary with the tests from kilowatts to megawatts as shown in the graphs. These test waveforms provide some insight into the nature of interfering signal waveforms. The question for designers is how RS-485 devices can be protected from these types of electrical transients.
Protection starts with wiring
The physical layer standard for RS-485 is TIA/EIA-485A, which specifies a differential (balanced) transmission over twisted pair wiring. The connection can be half-duplex (alternating between transmit and receive signals over the same line) requiring a single twisted pair, or full-duplex (transmit and receive on separate lines permitting simultaneous operations) requiring two twisted pair lines. Both ends of the twisted pairs are terminated in their characteristic impedance, normally 120 ohms (Ω).
The use of differential signaling over twisted pair provides a good degree of noise immunity because interfering signals, common to both wires in the pair, are subtracted from each other in the differential processing.
Additional protection against interfering signals can be obtained by using a shielded twisted pair cable. A typical shielded wire pair intended for RS-485 applications is the Alpha Wire type 6453 BK005 cable. It contains a single American wire gauge (AWG) #22 twisted wire pair surrounded by a wire braid and aluminized mylar tape shield. Of note in this context, there is an AWG #22 drain wire used to facilitate connections to the shield. The signal pair has a nominal impedance of 120 Ω. This particular cable is 100 ft long, though it is also available in lengths of 500 or 1000 ft from the manufacturer.
The cable shield, carefully grounded, provides a return path for EMI signals and prevents coupling of interfering signals with the internal twisted pair (Figure 2).
Figure 2: Using shielded RS-485 cable helps reduce induced noise and interference on the signal wire pair. (Image source: DigiKey)
Ground interconnections on an installation separated by hundreds or thousands of feet require some study as there may be substantial potential differences between one end of the bus and the other. Connecting them directly, via the cable shield, can result in high ground currents. A simple starting configuration is to connect the shield on one side of the data link, usually the primary ground reference point, shown in Figure 2. Alternative connections include alternating current (AC) coupling the ground in the presence of direct current (DC) offsets between local grounds or isolating the signal and power ground and handling them separately. The best method is very dependent upon the specific situation.
Transient suppressor diodes
Transient voltage suppression (TVS) devices belong to a class of protection components that include gas breakdown tubes, metal oxide varistors (MOVs), and thyristors. They are intended to conduct current when the applied voltage exceeds a known breakdown voltage. They are fast acting, offering response times on the order of 50 picoseconds (ps). Breakdown voltages are in a range from 3 to 400 volts and the devices can sink significant currents.
The TVS diode is an avalanche breakdown diode that begins to conduct current when the applied voltage is above the breakdown voltage, VBR (Figure 3).
Figure 3: The circuit model for a TVS diode (left) and its current/voltage characteristic (right). The clamp voltage (VCLAMP) is a function of the breakdown voltage (VBR), the dynamic resistance (RDYN), and the current through the diode (IPP). (Image source: Texas Instruments)
VCLAMP is dependent upon the breakdown voltage, the dynamic resistance of the diode, and the current passing through the device. The device shown is a unidirectional diode that is clamping only positive voltages. There are also bidirectional devices that clamp both positive and negative surge transients.
These devices are connected between the RS-485 signal lines and ground as shown in Figure 4.
Figure 4: Two bidirectional TVS diodes are used to protect the A and B signal lines of a TIA/EIA-485 transceiver. (Image source: DigiKey)
As shown, two bidirectional TVS diodes are used to protect the A and B signal lines of a TIA/EIA-485 transceiver. Voltage transients exceeding the clamp voltage cause the diodes to break down and conduct transient current to ground to protect the transceiver.
The current-dependent clamp voltage of a conventional TVS diode requires higher transceiver transient tolerance limits. The Texas Instruments TVS0500DRVR TVS protection device is one of a family of protection devices that offers a precision clamp voltage. The TVS0500DRVR has a standoff or breakdown voltage of 5 volts and a clamp voltage of 9.2 volts at 43 amperes (A) for an IEC 61000-4-5 8/20 microsecond (µs) surge test. It achieves this narrow breakdown-to-clamp range by using a unique feedback topology to reduce dynamic resistance (Figure 5).
Figure 5: The circuit model for a flat clamp using a voltage sensing circuit to drive a FET. The resulting flat current-voltage (I-V) characteristic has a clamp voltage nearer the nominal standoff voltage rating compared to a conventional TVS diode, resulting in less stress on the protected bus. (Image source: Texas Instruments)
This ‘flat’ clamp combines a precision voltage sensing circuit with a gate drive and a power field-effect transistor (FET). The FET behaves as an active clamp. When the input voltage is below the breakdown or standoff voltage the FET is off. When the voltage increases to the standoff voltage, the voltage sense circuit drives the FET into conduction. As the input voltage continues to increase, the FET is driven harder into conduction, holding the voltage across the device at a nearly fixed level. The lower on-resistance of the FET greatly reduces the clamp voltage compared to a conventional TVS diode.
Comparing the time domain responses to an 8/20 µs surge pulse for both a conventional TVS diode and a flat response device shows a lower peak voltage amplitude (Figure 6). This also reduces the power dissipation of the component. The flat clamp devices also have much lower capacitance—only 155 picofarads (pF) for the TVS0500DRVR—which reduces bus loading and improves the bandwidth of the bus being protected.
Figure 6: Comparing the time response of both a traditional TVS diode and a flat clamp device for an 8/20 µs surge pulse. The flat clamp reduces the peak voltage that the protected bus experiences. (Image source: Texas Instruments)
Bus transceiver with integrated surge protection
Texas Instruments has incorporated TVS protection diodes into the THVD1429DT RS-485, half-duplex transceiver. This transceiver offers bus input/output protection up to: ±16 kV human body model (HBM) ESD; ±8 kV IEC 61000-4-2 contact discharge; ±30 kV IEC 61000-4-2 air-gap discharge; ±4 kV IEC 61000-4-4 electrical fast transient; and ±2.5 kV IEC 61000-4-5 1.2/50 μs surge. It offers bus speeds up to 20 megabits per second (Mbits/s) and fits into an 8-pin SOIC package.
As with all bus transceivers, the maximum usable data rate is a function of the bus length. The 20 Mbits/s rate is only achievable where the bus connection has appropriately low attenuation at the signal frequency (Figure 7). The chart shows the plot of data rate as a function of bus length. The data rate can be extended beyond the conservative characteristics by allowing for a small amount of timing jitter, on the order of 5% to 10%. Signal processing such as pre-emphasis can improve the reliability of communications.
Figure 7: The cable length versus data rate characteristic for the THVD1429DT RS-485 bus transceiver. The data rate can be extended beyond the conservative characteristics by allowing for a small amount of timing jitter, on the order of 5% to 10%. (Image source: Texas Instruments)
Transceiver pre-emphasis improves reliability
Long bus runs are subject to inter-symbol interference (ISI). ISI changes the signal amplitude at the output of the bus depending on the data pattern. A long run of ones followed by a single zero will result in a higher peak voltage compared to a run of zeros followed by a single one. The former data pattern takes longer to fall to the threshold level than the latter pattern. This results in the effective signal duration being pattern dependent, a form of timing jitter. Pre-emphasis reduces the effect of ISI by increasing the signal amplitude at each edge, reducing the time difference between different data patterns.
For example, the Maxim Integrated MAX3292ESD+ is a full-duplex RS-485 transceiver that incorporates pre-emphasis to operate up to 10 Mbits/s. The result of pre-emphasis allows a doubling of the bus length for a fixed data rate, or a doubling of the data rate for a fixed bus length (Figure 8).
Figure 8: Graph showing the improvement in either bus length or data rate through the use of pre-emphasis. Pre-emphasis enables a doubling of the bus length for a fixed data rate, or a doubling of the data rate for a fixed bus length. (Image source: Texas Instruments)
This graph of cable length as a function of data rate shows the relationship for both conventional and pre-emphasized operation. At a data rate of 2 Mbps the maximum data bus length, without pre-emphasis, is about 900 ft. If pre-emphasis is used the line length increases to 1,800 ft.
Conclusion
Although the RS-485 bus is designed for industrial applications, there is much that designers can do to protect it and ensure signal integrity and extend transmission range for a given data rate. Several techniques, including the use of shielded cable, transient surge protection devices, and signal processing in the form of pre-emphasis, can be used to improve signal integrity in the presence of electromagnetic interference.
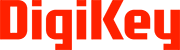
免责声明:各个作者和/或论坛参与者在本网站发表的观点、看法和意见不代表 DigiKey 的观点、看法和意见,也不代表 DigiKey 官方政策。