如何在恶劣环境中使用雷达进行车辆探测并避免碰撞
投稿人:DigiKey 北美编辑
2024-11-12
在物流、制造、采矿、运输、农业和其他行业中,运动监测和位置传感器可用于避免碰撞、确保安全并提高生产率。这些传感器可安装在车辆上,也可以放置于关键固定位置。
传感器必须能够根据特定的应用需求进行配置,并具有多功能感测能力,包括基于距离、角度位置和速度的物体检测。在繁忙或复杂的环境中,需要有同时探测多个目标的能力。
对于像装卸月台和叉车速度控制这类应用,采用不受污垢、灰尘、风、降水和其他环境条件影响的技术会很有利。定制像检测窗形状和目标设定点这样的参数可进一步提高性能。
本文首先探讨工作频率对几个关键雷达技术指标的重要性,然后比较调频连续波 (FMCW) 和脉冲相干雷达 (PCR) 等现有雷达技术、探测方案、波束图和感应区。接下来,介绍一款软件套件,可用于加速开发使用雷达传感器的系统。
最后,以应用实例说明 Banner Engineering Q90R 系列雷达传感器如何利用所有这些因素提供多功能感测能力,在苛刻的环境中进行可靠的检测,包括检测装卸月台是否有卡车,及控制叉车速度以提高安全性。
无线电探测与测距(雷达)是一种主动传感器技术,会发射高频射频能量。发出的能量会被路径上的物体反射,反射能量的特征可用来探测物体、确定其距离,有时还能测量物体靠近或远离传感器的速度。
工作频率是决定雷达传感器性能的基本特征。工业雷达传感器的工作频率为 24 GHz、60 Ghz 和 122 GHz,属于工业、科学和医疗 (ISM) 频段,无需特殊许可证即可使用。
雷达传感器的工作频率对多项技术指标有重大影响,包括:
- 探测距离 - 24 Ghz 等低频雷达传感器的探测距离最远。
- 精度 - 122 GHz 等高频雷达传感器具有更高的精度,可以探测到更小的物体。
- 盲区 - 雷达传感器的盲区或阻挡距离是由于目标太近造成的。一般而言,通常传感器的频率越高,盲区越小。
- 耐候性 - 感测功能耐受风、雾、蒸汽和温度变化的能力。雷达一般不受雨雪干扰。24 GHz 雷达具有最佳的抗雨雪干扰能力。
- 目标材料 - 虽然 24 GHz 雷达的抗天气干扰能力最好,但其感测各种材料的能力却最为有限。60 GHz 或 122 GHz 雷达传感器可探测高介电和低介电材料(图 1)。
图 1:雷达传感器的工作频率对其基于材料介电特性识别各种目标材料的能力有很大影响。(图片来源:Banner Engineering)
频率之外的技术指标
频率是雷达传感器的一个决定性特征。其他重要技术指标还包括雷达技术(如 FMCW 与 PCR)、探测方案(包括可调场与反射式传感器)以及视场、窗形和目标设定点。
FMCW 发射连续信号,信号经过调制,频率在固定带宽内增减。通过测量反射信号的频率,雷达可以知道信号从目标反射回来所需的时间。因此飞行时间 (ToF) 信息决定了目标距离。
FMCW 的一些优势包括:无需单独的天线或脉冲就能同时测量距离和速度、优异的测距分辨率、区分密集目标的能力,以及在挑战性环境中更高的精度。
PCR 雷达发射一个脉冲,关闭发射器,等待接收目标的回波,然后重新打开发射器,发射新的脉冲,不断继续这一循环。与 FMCW 一样,也采用一种 ToF 分析形式来确定目标的距离和速度。使用脉冲意味着 PCR 雷达的功耗比 FMCW 更低。PCR 通常是电池供电型系统的首选,非常适合低功耗短距离应用。
可调场传感器与反射式传感器的对比
可调场雷达通过感应反射的射频波来探测物体,其非常适合探测雷达截面较大而能反射大量射频能量的物体。金属表面积较大的物体,尤其是垂直于雷达波束的表面,通常具有较大的雷达截面积。
可调场雷达传感器可配置设定点距离。这种传感器使用 ToF 计算来确定目标范围,并只在设定距离内出现目标时发出信号。
反射式雷达传感器依赖于墙壁等反射参考目标,它通过识别来自参考目标的返回信号中的干扰信号来探测物体。这些雷达传感器经过优化,能够检测雷达截面积较小的物体。
60 Ghz FMCW 雷达传感器
Q90R 系列 FMCW 可调场雷达传感器的工作频率为 60 GHz,在精度、距离和材料探测能力方面性能均衡。此外,这些传感器的防护等级为 IP69K,适合在苛刻的环境中使用(图 2)。这些产品提供 120° x 40° 或 40° x 40° 的视场选择。可以根据具体的应用要求修改探测距离、检测最近或信号最强的物体等参数。
图 2:Q90R 系列 FMCW 可调场雷达传感器的工作频率为 60 GHz,采用坚固的 IP69K 级封装。(图片来源:DigiKey)
Q90R2-12040-6KDQ 具有高度可配置的 120° x 40° 视场,可分割成独立的检测区域,实现精确的位置感测(图 3)。该传感器具有多维感测能力,可支持基于距离、径向位置和速度阈值进行更智能的物体检测。与 Q90R 系列雷达传感器的其他型号一样,其探测距离为 0.15 至 20 米。此外,这款传感器还提供灵活的连接选择,包括 IO-Link 和 Banner 的 Pulse Pro 脉冲频率调制 (PFM) 技术。
图 3:Q90R2 雷达传感器具有 120° x 40° 的可配置宽视场(图片来源:Banner Engineering)
软件解锁性能
Q90R 和 Q90R2 雷达传感器的强大功能可以通过 Banner 的测量传感器软件来实现,该软件是一个图形用户界面 (GUI),能够让设计人员配置和可视化来自传感器的数据。
该软件以图形形式呈现传感器看到的情况,这对雷达传感器等没有可见光束的传感器非常有用。用户可以修改传感器参数,如响应速度、输出配置和过滤选项。
Q90R2 的视场为 120° x 40°,具有很高的可配置性,可实现精确定位和控制。设计人员可以使用 Banner 软件定制高级感测参数,例如每个应用的窗形和目标设定点。(图 4)。
图 4:Banner 的测量传感器软件能够让设计人员优化视场(上图)以及窗形和目标点(下图)。(图片来源:Banner Engineering)
装卸月台车辆检测
自动、准确地检测装卸月台的卡车对于提高生产率和安全性,以及满足环保标准非常重要。传统的门铃或指示灯解决方案往往并不适用。装卸月台可能非常嘈杂,门铃的声音不一定能被听到。此外,叉车上的顶灯、机器照明灯和闪光灯也很容易让人忽略指示灯,即使是闪烁的指示灯。
自动传感器解决方案是理想之选。然而,卡车有多种尺寸,由各种材料制成,颜色和表面处理也多种多样。这些挑战,再加上噪音、灰尘、雨雪等环境条件的不确定性,使得实现可靠的基于光电或超声波传感器的解决方案非常困难。
像 Q90R2 这样的雷达传感器通常是首选。这类传感器不受周围环境条件的影响,外壳具有 IP67/IP69K 防护等级,适用于暴雨和其他挑战性环境条件,并具有 -40°C 至 +65°C 的宽工作温度范围。无论材料的颜色、质地或反射率如何,它们都能可靠地检测到卡车的存在。
Q90R2 具有独立和可配置的传感区域,以及 120° x 40° 的波束图,一个传感器可以完成两个传感器的工作,并能检测到两个相邻月台是否有卡车(图 5)。
图 5:Q90R2 雷达传感器的 120° x 40° 波束图意味着一个传感器可以监测两个卡车月台。(图片来源:Banner Engineering)
叉车速度控制与安全
除了探测车辆,雷达传感器还可以安装在叉车等车辆上,以检测周围环境的变化,从而提高安全性。例如,Q90R2 雷达传感器可安装在叉车的背面或侧面,并在不同距离配置多个区域。
Q90R2 具有 120° x 40° 的宽波束图,特别适合监测周围可能移动的物体。此外,Q90R2 还可提供径向距离、角度位置和目标速度反馈。当危险越来越近时,叉车驾驶员会收到报警,叉车速度会自动受到限制,或者叉车会被停止。
如果叉车在室内和室外使用,则可在车顶安装一个波束图为 40° x 40° 的 Q90R 雷达传感器,以检测是否存在天花板。当叉车在室外且未检测到天花板时,机器就可以最高限速行驶。当叉车在室内移动且存在天花板时,最大速度可自动降低,以提高安全性并防止损坏(图 6)。
图 6:雷达传感器可用于监测叉车周围是否有人员或物体,以及是否有天花板。(图片来源:Banner Engineering)
根据系统需要,Q90R 有多种型号可供选择,输出配置各不相同,包括:
- Q90R-4040-6KDQ,带有两个分立式 NPN/PNP、PFM 输出和一个 IO-Link 输出
- Q90R-4040-6KIQ,带有一个模拟电流(4 至 20 mA)输出、一个 NPN/PNP 分立输出和一个 IO-Link 输出
- Q90R-4040-6KUQ,带有一个模拟电压(0 至 10 V 或 0.5 至 4.5 V)输出、一个 NPN/PNP 分立输出和一个 IO-Link 输出
结语
Q90R 系列雷达传感器用途非常广泛,其工作频率为 60 GHz,能够探测各种材料。这些 FMCW 雷达的探测距离最远为 20 米,波束图可配置,可支持多种应用。输出选择有多种选择,可满足不同的系统需求,并可安装在叉车等车辆上或放置在月台等关键固定位置。最后,设计人员还可以利用 Banner 的测量传感器软件来加快系统设计和部署。
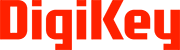
免责声明:各个作者和/或论坛参与者在本网站发表的观点、看法和意见不代表 DigiKey 的观点、看法和意见,也不代表 DigiKey 官方政策。