用于食品、饮料和制药加工生产线的 IP69K 级传感器有哪些新选择?
投稿人:DigiKey 北美编辑
2024-10-31
食品、饮料和药品在加工过程中必须满足卫生要求。与所有工业 4.0 运行一样,这些加工生产线也需要大量传感器来支持的高度自动化。
这意味着需要使用 69K 级耐环境侵蚀保护 (IP) 传感器。这些传感器可以承受高压冲洗和日常就地清洁 (CIP) 程序,以保持卫生的工作环境,同时确保高效运行。
除了 IP69K 等外,这些应用中的传感器通常还需要使用符合美国食品药品管理局 (FDA) 要求的材料制造,例如 SAE 360 L 不锈钢合金。这种不锈钢具有很强的耐腐蚀性,可以承受常规的 CIP 程序。在其他应用中,可以使用 FDA 级塑料外壳。
本文首先概述 DIN 40050-9 中规定的 IP69K 要求,介绍包括 SAE 200、300 和 400 系列在内的各种 FDA 不锈钢性能,以及市面上有售的 FDA 级塑料及其应用场合。
然后,介绍 Banner Engineering 推出的几款适用于食品、饮料和制药加工生产线的新型传感器,以及一些应用和安装建议。本文最后介绍一种瓶盖应用。该应用需要 IP69K 传感器性能,但不需要使用 FDA 批准材料制成的外壳。
IP69K 传感器是否也符合 IP68 标准?
可将传感器设计成同时满足这两种标准。这些 IP 等级中的“6”表示这些设备防尘,可阻止灰尘进入。
不过,达到 IP69K 标准并不意味着传感器自动达到 IP68 标准。国际电工委员会 (IEC) 40050-9 以德国标准为基础,扩展了 IEC 60529 IP 级系统,增加了与其他 IP 级有些不同的 IP69K,以用于高压、高温冲洗应用。
IP68 防水等级以 IP67 为基础。按照 IP67 规定,设备可在一米深的水中临时浸泡至少 30 分钟。IP68 还包括水中浸没测试,测试条件由设备制造商和用户商定,且必须比 IP67 更严格。例如,Banner Engineering IP68 级传感器可在两米深的水中连续浸泡至少 24 小时。
IP69K 不要求浸入水中。IP69K 测试包括三项内容:
- 能够以每分钟 14 至 16 升 (L/min) 的流速、10 Mpa(每平方英寸 1500 磅 (psi))的压力向设备喷射 +80°C 的水
- 喷头必须在距离设备 10 cm至 15 cm 处,并以 0°、+30°、+60° 和 +90° 的角度各保持 30 秒,累计共喷射 120 秒。
- 设备在转盘上每 12 秒旋转一圈
Banner Engineering IP69K 级传感器还通过了至少一米的浸水测试,这一要求超过了 IP69K 的测试标准(图 1)。测试后,检查传感器内部是否进水。传感器内不得有水,传感器必须继续正常工作才能通过测试。
图 1:如这种传感器要一样, IP69K 级传感器能够承受高压、高温冲洗。(图片来源:Banner Engineering)
腐蚀也很重要的问题
IP 等级系统表示外壳对固体颗粒和液体侵入的防护能力。该系统不考虑腐蚀性运行环境。FDA 的要求涵盖了这一点。
FDA 监管外壳材料,以确保其可安全地用于食品、药品。例如,食品级不锈钢必须满足以下要求:
- 含铬量必须至少达到 16%。氧化铬薄膜在氧气存在的条件下会自我修复,从而使不锈钢具有耐腐蚀性。
- 必须采用 SAE 200、300 或 400 系列不锈钢,且这三种不锈钢分别包含了铬镍锰合金、铬镍合金和铬合金。
- 不锈钢表面必须光滑、易于清洁。
- 不锈钢必须能够防止点蚀、剥落、开裂、刮擦和划痕,具有足以承受反复的高压、高温冲洗的厚度。
- 不应在食物上产生任何气味儿、味道或颜色。
对于重量较轻的解决方案,FDA 认为阳极氧化铝为“公认的安全”材料。使用铝材料时,必须进行适当的加工处理。
FDA 批准了种类繁多塑料。塑料的共同特点包括耐磨损、抗弯曲和易于改变尺寸。具体如下:
- 聚碳酸酯是一种轻型透明且异常坚固的材料。
- 聚对苯二甲酸丁二醇酯(PBT 聚酯)具有很高的强度、刚性和尺寸稳定性。这种材料具有抗化学性、抗氧化性和耐水性,可耐受高达 150°C 的温度。
- 丙烯酸(亚克力)是一种无毒透明塑料,经批准后用于材料处理。这种塑料还具有耐热性,适合在恶劣环境中使用。
- 尼龙能很好地阻隔氧气和湿气。这类材料用于保护部件不受外部环境的影响。
FDA 级不锈钢光电传感器
Banner Engineering 的 Q4X 系列光电传感器的检测范围从 25 mm 到 610 mm 不等,具体取决于型号。例如,Q4XFKLAF310-Q8 型的检测范围为 35 mm 至 310 mm。
外壳由 316 L FDA 级不锈钢制成,防护等级为 IP68(符合 IEC60529 标准)和 IP69K(符合 DIN 40050-9 标准)。该系列传感器能够兼容设备清洁卫生过程中常用的酸性或腐蚀性清洁和消毒化学品,并获得了 ECOLAB 认证。
当传感器处于运行模式时,4 位 7 段显示屏会显示当前的测量读数或相应的模拟输出值(图 2)。其他特性包括:
- 离散、模拟(0 V 至 10 V 或 4 mA 至 20 mA)、清晰的目标和 IO-Link 型号
- 高分辨率型号提供模拟输出,具有更高的过量增益,适用于更具挑战性的应用
- 根据距离检测各种目标颜色、材料和表面
- 双示教模式(强度 + 距离)可用于防错应用, 且无需逆向反射器即可实现清晰的目标检测
图 2:这款 IP69K 和 IP68 级光电传感器采用 FDA 级不锈钢封装。(图片来源:Banner Engineering)
加快配置和转换
选配型 RSD1QP 远程传感器显示器 (RSD) 可与 Q4X 系列和 Banner 的其他传感器系列一起使用,用于配置和监控(图 3)。该器件可加快工业 4.0 工厂的产品转换速度,并在配置完成后保持连接或被移除。这种显示器还简化了对难以接近位置的传感器的监控。RSD 的其他用途包括:
- 在传感器之间复制具体的设置
- 支持快速更换传感器
- RSD 最多可存储六种配置,用于不同的运行
图 3:RSD1 可用于远程配置和监控 Banner Q4X 系列等传感器。(图片来源:Banner Engineering)
采用塑料外壳的光电传感器
T18-2VPRL-2M (T18-2) 冲洗传感器是一种独立式光电传感器,设计用于食品生产线、家禽加工、箱体检测和检重站运行触发等恶劣环境。
这种外壳由黑色和黄色 PBT 聚酯纤维制成,指示灯和观察窗由白色半透明丙烯酸树脂制成。这种塑料外壳采用超声波焊接,以确保完全密封,电子元件采用 IP69K 级环氧树脂封装,以提供冗余密封(图 4)。这些传感器还达到了 IP68 防护等级。
图 4:这款 IP69K 和 IP68 级光电传感器采用 FDA 批准的塑料封装。(图片来源:Banner Engineering)
IP69K 铝制雷达传感器
Q90R 系列等雷达传感器可用于保护人员免受机器伤害、与协作机器人 (cobots) 协同工作,或用于食品、饮料和制药加工生产线的箱/罐液位测量。IP69K 级铝制外壳坚固而轻巧。这些传感器的工作温度为 -40°C 至 +65°C,因此适合在潮湿和多雾等恶劣环境下使用。
例如,Q90R-4040-6KDQ 型传感器的检测范围为 150 mm 至 20 m,提供两个输出端,一个是具有 IO-Link 通信功能的 PNP/NPN 输出端,另一个是 1 PNP/NPN 输出端。所有 Q90R 传感器都可以自定义传感参数,如观察窗形状和目标设定点。IO-Link 可支持实时数据传输。
物体检测可基于相对传感器的距离、速度和角度位置进行,提供可配置的多维性能。两个独立区域可同时检测和测量多个目标(图 5)。
图 5:这种铝制外壳雷达传感器可用于食品、饮料和制药加工生产线上的箱/罐液位监测。(图片来源:DigiKey)
视觉系统照明
用于品质控制和检测应用的视觉系统需要良好的照明才能达到最佳运行状态。Banner 的 BL60 密封式 LED 条形灯可提供明亮、集中的照明。有可产生四种高强度可见光波长、红外线 (IR) 和两种紫外线 (UV) 波长的型号可供选择。通过选择最合适的照明方案,可进一步提高视觉系统的性能。
耐油、耐化学腐蚀和防水型铝制外壳达到 IP69K 防护等级,长度有 340 mm 和 640 mm 两种。有三种观察窗可供选择:透明或漫射聚碳酸酯和硼硅玻璃。这些照明灯具具有 1 V 至 10 V 调光控制功能、可调脉宽调制 (PWM) 选通功能。340 mm LED 条形灯的光色如下:
- 日光色 (5000 K),BL60W340L14ASQ
- 红色,BL60R340L14ASQ
- 绿色,BL60G340L14ASQ
- 蓝色,BL60B340L14ASQ
- 红外,BL60I340L14ASQ.
- 365 nm 紫外线,BL60UV365-340GL30ASQ
- 395 nm 紫外线,BL60UV395-340L30ASQ
用于瓶盖的 IP69K 级镀镍锌激光传感器
并非食品、饮料和药品加工生产线中的每种传感器应用都需要使用经 FDA 批准的外壳材料。瓶盖就是一个很好的例子。
瓶盖通常散装,在灌装线上使用前需要进行分类。错位的瓶盖(如倒置)会导致瓶子无法盖上瓶盖,或卡住封盖机,从而降低生产率。像 Q3XTBLD-Q8 (Q3X) 这样的激光传感器在瓶盖到达瓶盖输送系统之前,可快速识别瓶盖是否朝向错误的方向。
Q3X 具有 100 mm 的背景抑制能力,非常适合方位检测应用。通过固定的背景抑制功能,Q3X 传感器可设置为识别特定距离,并忽略设定点以外的任何信息。
在瓶盖分类应用中,可将 Q3X 设置为检测瓶盖顶部是否朝向传感器。如果瓶盖朝外,则忽略不计。如果瓶盖朝向传感器,就会发出失败输出并剔除该瓶盖。此时,瓶盖可以回收到分拣机中再次尝试。
Q3X 的快速检测率对高速灌装线非常重要。该传感器可在 250 µs 内检测一个工件,每秒可捕捉多达 2,000 个事件。倾斜式 3 位数显示屏可提供用户反馈,加快设置和调试速度。镀镍锌外壳的防护等级为 IP67 和 IP69K,适用于潮湿环境(图 6)。
图 6:这款 IP69K 级激光传感器采用镀镍锌封装,适用于瓶盖工艺。(图片来源:Banner Engineering)
结束语
食品、饮料和制药加工生产线需要符合 IP69K 标准并能承受高压和高温 CIP 运行的坚固型传感器。其中许多传感器的设计还符合 IP68 浸没要求。在大多数情况下,传感器必须使用 FDA 批准的材料进行封装,但也有例外情况,比如瓶子的封盖操作。
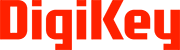
免责声明:各个作者和/或论坛参与者在本网站发表的观点、看法和意见不代表 DigiKey 的观点、看法和意见,也不代表 DigiKey 官方政策。