Higher Precision Fuel Gauge ICs Promise Longer Runtimes
投稿人:DigiKey 北美编辑
2016-06-29
Given the pivotal role battery life plays in user satisfaction and the market success of portable products, it’s hardly surprising that a wide variety of vendors offer fuel or gas gauge ICs. By continuously estimating the charge in the battery across all operating conditions, these devices perform a number of important tasks including extending system runtime and battery life, helping manage the health of the battery, and improving safety by reporting on fault conditions. At the same time, by performing tasks that would otherwise require the use of discrete components, fuel gauge ICs help reduce component count, cost, and product footprint while minimizing software overhead on the system processor.
However, accurately estimating the capacity of a lithium-ion (Li-ion) battery is no simple task. State of charge (SOC) in Li-ion batteries is driven by a wide range of factors, including temperature and discharge rate. The algorithms used by fuel gauge ICs to estimate SOC must compensate for issues as diverse as self-discharge, the internal impedance of battery cells, and cell aging. The fuel-gauge IC must combine this data with prior knowledge of the battery to accurately estimate SOC.
The aging issue is an excellent example of the challenge inherent in this task. While cells typically vary in capacity, the capacity of individual cells also changes over time as they age and lose their ability to store charge (Figure 1). One of the more difficult challenges designers face when estimating SOC is how to compensate for older cells that can deliver voltage for a shorter time than newer cells.
Figure 1: Fuel gauge ICs must compensate for the effects of cell age on capacity. The figure above illustrates how as a cell’s age or number of cycles increases, its ability to hold a fixed voltage over time declines. (Source: Texas Instruments)
Rapid evolution
Typically, the fuel gauge IC sits on the battery pack and tracks current into and out of the battery using a low value shunt resistor. Early battery monitoring circuits simply measured the voltage of the cell. However, it was difficult to get highly accurate battery capacity estimates because as load current levels change, the instantaneous voltage of a cell can move up or down for a given SOC.
Most fuel gauge ICs today use a coulomb-counting methodology to calculate battery capacity. These devices track milliamps in and out of the battery over time using a small sense resistor with a measurement circuit and a timer/counter. To generate a model of cell capacity under typical conditions, they count mAH in and out of the battery from a known starting point, such as 100% capacity. The circuit can then track SOC as the battery is charged and discharged.
The coulomb counting approach has some weaknesses of its own, however. Gauges of this type must account for all operating charge and discharge activity to accurately measure SOC. Yet this approach often fails to account for losses during long periods of storage when the cell typically loses charge due to self-discharge. It also fails to compensate for widely variable load currents, particularly on the very low or high end, that the current sensing circuit may not be able to measure.
Some fuel-gauge suppliers integrate a coulomb counter with an on-chip sense resistor that is temperature-compensated to improve accuracy. Others use cell impedance measurements to estimate SOC for Li-ion cells. This approach uses real-time resistance profiles to predict the battery’s discharge curve by adjusting for IR drop under all use conditions. By combining coulomb counting when the system is on with open-circuit voltage measurement when the system is off, these gauges can deliver a high level of accuracy.
Multiple options
Today vendors offer a wide range of solutions from simple gas gauge ICs to fully integrated battery management and protection circuits. For applications like tablet computing, portable and wearable health devices, and portable audio devices, Texas Instruments’ bq28z610 offers a highly integrated gas gauge for 1-series and 2-series cell Li-ion battery packs (Figure 2). The device minimizes software overhead on the system controller by enabling autonomous battery charging control using Master Mode I2C broadcasts of charging current and voltage information. The integrated gauge combines a low-power TI bqBMP processor with a high-accuracy analog front end featuring two independent ADCs, integrated flash memory, and a wide array of peripheral and communication ports. It also adds a high-side protection N-CH FET drive to support serial bus communication during fault conditions, and a SHA-1 authentication responder for battery-pack security.
Figure 2: Texas Instruments’ bq28z610 gas gauge offers a high level of integration. High-performance embedded analog peripherals support sense resistors down to 1 mΩ and simultaneous current/voltage data conversion for power calculations. (Source: Texas Instruments)
To calculate remaining battery capacity accurately without modeling or learning, the bq28z610 uses Texas Instruments’ proprietary Impedance Tracking algorithm. While many gas gauges rely on model cell performance or perform re-calibration sequences to update on-chip model parameters, the Impedance Track method uses cell impedance measurements to estimate SOC for Li-ion cells. Texas Instruments claims this methodology achieves less than 1 percent error over the lifetime of the battery.
Power dissipation and footprint are usually critical considerations in the selection of a fuel gauge IC. Low quiescent current is particularly important because the fuel gauge must be powered up when the load to the battery is turned off to periodically measure open circuit voltage. Maxim’s MAX17048 and MAX17049 fuel gauge ICs operate at 23 µA and run as low as 4 µA in hibernation mode (Figure 3). Indicative of their small footprint, the two devices are available in 0.9 x 1.7 mm, 8 bump wafer level package (WLP) or a 2 x 2 mm, 8-pin TDFN package.
Both devices use Maxim’s ModelGauge Li+ battery modeling algorithm. Unlike traditional coulomb counting gauges which require multiple external components including a sense resistor, ModelGauge reduces footprint by delivering accurate state of charge that compensates for temperature and load while eliminating the resistor and battery learning cycles. Temperature compensation is implemented using the system microcontroller. The MAX17048 operates with a single lithium cell while the MAX 17049 supports two lithium cells in series.
Figure 3: With its ModelGauge battery-modeling algorithm, Maxim Integrated’s MAX17048/MAX17049 fuel gauge ICs reduce footprint by eliminating the current sense resistor and other external components used in traditional fuel gauge designs. (Source: Maxim Integrated)
Current and voltage protection are key considerations in any fuel gauge solution. For single-cell Li-ion battery packs, Texas Instrument’s bq28550-R1 combines a battery gas gauge with a complete set of current and voltage protection functions (Figure 4). The device requires host microcontroller support for implementation. The bq28550-R1 supplies all critical battery information including state-of-charge, run time to empty, charge time to full, battery voltage, and pack temperature to the system processor via a serial interface. At the same time, it provides short-circuit, overcurrent charge and discharge, overvoltage charge, and undervoltage protection.
Figure 4: Designed for battery pack integration, the bq28550-R1 single cell Li-ion battery gas gauge adds short-circuit, overcurrent, overvoltage, and undervoltage protection. (Source: Texas Instruments)
To accurately estimate fuel capacity, the device uses a compensated end of discharge voltage (CEDV) methodology where the algorithm mathematically models cell voltage as a function of battery SOC, temperature and current. It also models battery impedance (Z) as a function of SOC and temperature.
Conclusion
As the use of battery capacity gauges has spread, so, too, has designers’ reliance on the accuracy of the data they provide. Today’s portable systems must be more responsive than ever before to changing environmental conditions. Increasingly they are designed to make operational decisions based on available battery capacity. By precisely measuring critical parameters, accurately estimating SOC and supplying that information to the host processor, fuel gauge ICs can help systems more efficiently extract power from the battery and maximize run-time.
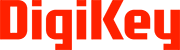
免责声明:各个作者和/或论坛参与者在本网站发表的观点、看法和意见不代表 DigiKey 的观点、看法和意见,也不代表 DigiKey 官方政策。