Capacitive Touch Sensing Moves from Exotic to Everyday
投稿人:DigiKey 欧洲编辑
2013-07-17
This article describes the development of touch sensing and switching techniques capacitive sensing technology. Products cited include both stand-alone capacitive sensing controller ICs and microcontrollers (MCUs) that include touch sensing as a peripheral function.
Capacitive touch sensing has experienced explosive growth to become the default human interface for several classes of consumer product. Users of tablets, smartphones, portable media players, and GPS systems now expect a sophisticated and responsive touch interface as a matter of course. This, in turn, has modified the expectations that the user base has of the smart device and domestic appliance markets; consumers now come, in effect, pre-programmed with the language of tap, drag, swipe, and pinch. High-end products that do not offer that mode of user interaction risk being “uncool”.
The launch of Windows 8 in 2012 served only to reinforce the proliferation of touch interfaces, prompting tablet and PC makers to experiment with new formats in the portable computing sector. Those who viewed the touch phenomenon as evolving from the smartphone/digital assistant space regarded Microsoft's Surface product as a relatively large screen format; yet other PC makers are testing the market with larger-format tablet-style products. Taking touch from the format in which it is the only interface – the smartphone – into a space where the keyboard has been indispensable, is likely to see further development in the way consumers interact with technology.
In fact, the touch paradigm appeared in the PC market early in its development. Hewlett-Packard offered a product in the 1980s that used a touch interface, although that used infrared sensing to detect the presence and location of a finger. The first mentions of touch interfaces associated with screens date back decades earlier, with historical accounts quoting an early capacitive-touch system conceived as a means of interfacing with a radar system.
Prior to the current upswing in deployment of touch technology, most consumers' experience of the technology was limited to a small number of applications, largely in areas such as vending kiosks/ATMs. Those mostly used resistive touch technology, or occasionally infrared (where an X/Y matrix of IR beams is placed immediately above the screen) and were invariably single-point detection systems.
Capacitive detection systems have dominated the last decade's explosion in the application of touch technology. Interest began with offerings that permitted replacement of mechanical button switches, resistive sliders, and rotary controls with no-moving-parts equivalent functions, operated through a non-conducting (dielectric) front panel. From initial deployment in applications such as high-end domestic appliances, many would say that the real spark to mass-market use came with Apple's launch of the iPhone, with its all-touch interface. As well as leading to deployment in huge numbers in countless consumer products, this has also changed the face of design of products for professional markets. Makers of rugged monitors and panel PCs for industrial control applications now routinely offer multi-touch as a standard feature.
In fact, the very term “capacitive touch” is a misnomer; unlike its resistive predecessor, detection of an event (usually but not necessarily a finger touch) does not require a physical contact – rather, the detection mechanism is one of very-short-range proximity. There are many variations in detail configurations, but the basic measurement mechanism is capturing the disturbance to a capacitance value by the encroachment of a human finger. In every case, some geometric pattern defining the capacitor is laid down, in metallic conductor if the detection is through an opaque panel, or in transparent material (often ITO, indium-tin-oxide) if the detection is over an LCD or other display. In some cases, the finger forms one plate of a 2-plate capacitor, with the user's body providing a leakage path to ground; in others, the finger spans the two plates of a capacitor in the pattern, modifying its value; in another, the deposited pattern generates a projected set of electric field lines outside the panel. The user's finger intersects these field lines, modifying charge transfer at the closest sensing point or points.
Vendors of touch sensing solutions, which can now be accessed either as stand-alone, dedicated ICs or as a peripheral within a microcontroller, have conceived a wide variety of circuit configurations to detect the capacitance changes that comprise a “touch”. Techniques used have included employing the variation in capacitance to modify the frequency of an oscillator, as the measured parameter; monitoring the change in level of a signal conducted across the variable capacitor; and a variety of others. The various permutations of sensing principle and detection circuit technique are the space in which the various vendors in the field can each lay claim to a unique and patented capacitive touch solution.
As with any engineering solution, touch detection systems involve trade-offs and compromises. A high level of sensitivity is desirable, so that the user experiences a system response with minimum delay; however, the sensing electrode pattern is a potential antenna to pick up any ambient electrical noise, so sensitivity must be tempered with noise immunity. Noise sources that can be troublesome to touch interfaces are numerous, and include the noise radiated by the thin-film-transistor array of a co-located LCD screen and conducted noise on signal and power supply lines. Similarly, a positive user experience is assisted if the rate at which the touch interface reports the position of the touching finger, or fingers, is high. However, a fast report rate means less time per individual measurement or detection, with implications for sensitivity, and also means a higher processing workload to track a moving finger. In the case of a multi-touch controller, the processing load can escalate rapidly with the requirement to extract vectors to represent the movement of two, or several, simultaneous touches.
The designer incorporating a touch interface can draw on the accumulated experience of over (in some cases) more than a decade of refining capacitive touch solutions, and incorporating them into controller ICs. Software plays a significant role: for example, the issue of accuracy, correctly identifying the user's intended touch point and avoiding detection at adjacent points, becomes an issue resolved by a combination of electrode patterning (to shape the individual detection zone), signal level discrimination, and software to recognize the wanted response and reject the unwanted. In an application such as a smartphone, the system must react to one or more discrete touches, identifying them as finger or stylus, but recognize when the screen is held to the side of the user's head and ignore the multiple, apparent, “touches”.
In the industrial market sector, recent months have seen significant adoption of capacitive touch as a mainstream interface for control and automation systems, as major equipment makers such as Siemens and Beckhoff have released ranges of large-format rugged displays incorporating multi-touch detection. The same attractions that pertain in the consumer space apply – elimination of mechanical switches, and the ability to create a single, unbroken front panel – but in the industrial space this translates to rugged construction that can be sealed against contamination. Some of the makers of touch control ICs claim that their systems are particularly adept at handling industrial factors such as correct detection and location of a touching finger contained in a thick protective glove; detection of the required capacitance shift in high-humidity environments, or when the front panel of screen is wet; and tolerance of a very thick dielectric panel in front of the capacitor electrode pattern (glass or polycarbonate, for example, in ruggedized systems). The industrial design context shows the proliferation of the new user interface paradigm; users who have learned the “language” of touch and gesture demand it in all of their interactions with technology, not only in their consumer gadgets, and designers are under pressure to respond.
Among a number of IC ranges, Atmel offers the QTouch series of touch controllers; these employ Atmel's Charge Transfer sensing technology that provides robust detection with good noise immunity and the ability to correctly detect a gloved finger, suiting it to use in industrial as well as consumer products. Within that range, the AT42QT1070 and AT42QT2120 devices implement a sensing architecture that eliminates the need for any external components and uses only one I/O pin for each sensing channel; it supports faster scan time, lower current consumption, and less sensitivity to power supply fluctuations than previous generation devices. The parts communicate with a host microcontroller via a standard I²C bus. Intended for stand-alone front panels on a wide variety of products, the AT42QT1070 supports seven channels and the AT42QT2120 supports twelve channels with support for a slider or wheel interface. Atmel has included a number of features that have evolved as touch interfaces have developed, such as Adjacent Key Suppression (AKS) support, self-calibration, auto-drift compensation, noise filtering, and a selectable sleep interval. The parts operate from 18 to 5.5 V. For sensing larger arrays of keys, Atmel has the QMatrix range of ICs that detect touches on an X-Y grid. Atmel provides its QTouch Library to embed capacitive-touch buttons, sliders, and wheels into designs hosted on a number of its microcontrollers, including the AVR series. The library provides several library files for each device and supports different numbers of touch channels, enabling both flexibility and efficiency in touch applications. By selecting the library file supporting the exact number of channels needed, developers can achieve a more compact and efficient code using less RAM. Parts in the AT42QT1070 and AT42QT2120 series, mentioned above, have the added feature that due to the projected-field nature of the detection mechanism, the detection range can extend to as much as 20 cm, allowing gesture recognition.
Cypress Semiconductor implements its CapSense® technology in the medium of its PSoC (Programmable System on Chip) configurable, mixed-signal ICs. The CapSense offering, on chips such as the CY8C20434, provides up to thirty-three capacitive buttons and six sliders and features such as LED effects. There is a “superset” configuration, CapSense Plus, which accommodates up to forty-four capacitive buttons and eight sliders as well as LED effects, proximity detection, and rejection of erroneous detection due to the presence of water. A reduced feature set for rapid development of projects with fewer detection needs, CapSense Express supports simple button or button/slider designs with up to sixteen capacitive buttons or up to five capacitive buttons and one slider. The CY8C20434 operates as a complete, low-power detection sub-system, as it contains analog circuitry to implement direct connections to the sensor grid, and a processor-based logic core. The core is Cypress' own M8C, 12 MHz configuration; Cypress also implements CapSense with PSoC devices based around the ARM® Cortex™ M3 core.
A problem that all vendors of touch sensing devices have had to address is that the designer has limited control over the environment in which the end product is used; humidity varies (an issue where detection depends on the behavior of small amounts of electric charge), screen and panels become contaminated, and human fingers vary greatly. Internal calibration routines, in various forms, are a regular part of the capacitive touch landscape; in the case of Cypress' CapSense offering, it is called the SmartSense Auto-Tuning algorithm. CapSense can also function in the presence of water.
STMicroelectronics offers its S-Touch technology, both as an embedded function in a section of its STM8 microcontroller family, and in stand-alone controllers such as the STMPE24M31; ST cites possible applications for this part as the media control bar on a notebook PC, as it caters for up to eight buttons plus a slider or wheel variable control, but many other applications are possible. The chip is a touch measurement subsystem, and it contains a ratio engine to derive the user's intended input on twin slider controls. The sensor geometry for sliders often takes the form of two opposed and tapering sections of conductor; the IC measures the effect of the finger on each electrode and the ratio of the signals from each establishes where, along the taper, the finger has touched. Eight independent PWM controllers allow the IC to control up to sixteen LEDs with brightness control, ramping, and flashing capabilities. The I²C interface supports up to 400 kHz communication with the system host. A wide dynamic range allows most applications to work without hardware tuning.
Among many other chipmakers providing touch solutions, either embedded within microcontrollers or as a stand-alone controller, are Microchip, Analog Devices, Freescale Semiconductor, and Integrated Device Technology. Each offers development support and pre-packaged solutions that reduce the need for low-level coding in most applications, with function libraries that cover the most frequently required modes of sensing. The designer cannot expect to be completely removed from the detail of the sensing mechanism, as it is achieved through a combination of digital techniques with sensitive analog signal and charge handling.
Touch sensing, and especially capacitive touch sensing, has changed product design. Not every product needs an integrated high-pixel-count LCD and multi-touch detection layer, but the widespread use of such high-end products – tablets and the like – has altered the design context for products with less sophisticated human-interface needs. Users expect flawless activation of functions in response to their touch, without electro-mechanical switching. (An unanticipated consequence is that in some situations designers have had to retrofit haptic feedback to some systems, to confirm to the user that an action is ensuing.) Design teams that are working with high-end touch screens now need an unprecedented level of interaction between design groups; graphics must co-operate precisely with touch detection, for example. Still being explored is the way that replacement of mechanical switches gives a new dimension in product design, freeing packaging and electronic design groups to create more innovative products.
References:
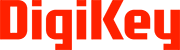
免责声明:各个作者和/或论坛参与者在本网站发表的观点、看法和意见不代表 DigiKey 的观点、看法和意见,也不代表 DigiKey 官方政策。