增材制造:从原型设计到生产
投稿人:DigiKey 北美编辑
2023-06-28
增材制造 (AM) 是更广泛数字制造趋势的一个缩影,可加快原型设计周期,并使产品更快投入生产。
想想在大规模采用 3D CAD 之后但 3D 打印出现之前的原型制作过程。工程师使用 3D CAD 设计零件,然后将各种细节导出为 2D 图纸。接下来,由机器操作员读取 2D 图纸,对 CNC(计算机数控)机器进行编程以生产零件。如今,数字制造将 3D 零件模型直接发送到机器(无论是数控机床还是 3D 打印机)进行生产。全自动化算法推动了这些零件构建的执行。这种能力使得从零件设计到零件生产的延迟大幅减少。
此外,数字化制造还大幅增加了工程师可用的信息。在某些情况下,通过门户网站提交给原型设计和批量制造服务的设计能够即时返回可制造性反馈和准确的报价。因此,在开始原型设计之前,就能快速计算出多种设计的成本。
图 1:所有类型的增材制造机器(包括图中所示基于 FDM 的机器)均采用步进电机来控制和协调挤出喷嘴(或其他沉积末端执行器)在三维空间的运动。NEMA 17 步进电机经常能够达到 60 oz-in. 的扭矩。(图片来源:Dreamstime)
AM 是这种迭代式预先设计现代版本的核心。另外,AM 可以生产传统加工不可能实现的零件形式,例如具有内部格子的空心骨状结构。能够快速打印热塑性塑料部件(而且成本低),会对早期原型设计产生变革性影响。这些部件可以用作实际的原型零件,也可以用作固定加工零件或模制复合零件的制造工具。最新的发展使高性能金属零件可以直接打印出来,这为原型设计、制造生产工具,甚至直接制造小批量生产的零件提供了更多可能性。
图 2:高级运动控制功能可以最大限度地减少进入 3D 打印机轴电机的电流正弦波的波动,以实现更安静、更平稳的运行。例如,一些驱动两相步进电机的独立 IC 使用优化的斩波器例程来驱动电机步进和方向,以使运动性能、电机扭矩和效率最大化。(图片来源:Trinamic Motion Control GmbH)
专用 AM 工艺有很多名称,但所有工艺都属于 ISO 标准的七个 AM 类别之一。
材料挤出 3D 打印:通过一个喷嘴或孔口选择性地分配材料。最常见的是,热塑性聚合物属于挤出材料,该工艺通常被称为长丝沉积建模 (FDM)。几乎所有低成本的 3D 打印机,甚至许多更高级的机器都使用 FDM。
粉末床熔融 (PBF):聚集来自激光、电子束或等离子弧等的热能,用以熔融粉末床中的粉末材料区域。
事实上,在 20 世纪 80 年代开发的第一种粉末床熔融形式被称为选择性激光烧结 (SLS)。与现行的某些技术相比,SLS 无法完全熔化粉末,因此无法生产完全致密的零件。现在,现代粉末床熔融设备能充分熔化金属粉末,生产出完全致密的零件,其晶粒结构可与锻件相媲美。采用 SLS 技术生产的零件,其机械性能明显优于铸件。
液槽光聚合:液槽中的液态光聚合物通过光激活的聚合作用选择性地固化。该工艺通常被称为立体光刻。
图 3:立体光刻 (SLA) 和数字光处理 (DLP) 是用于创建模型、原型、模式和生产零件的增材制造技术。(图片来源:Dreamstime)
定向能量沉积 (DED):聚集来自激光、电子束或等离子弧的热能,在材料沉积时将其熔融。可以使用填丝或吹粉作为原料。
图 4:圆轨直线导轨和外露同步带驱动在台式 3D 打印机以及更复杂的设备上很常见。(图片来源:Dreamstime)
粘结剂喷射 (BJ) 和材料喷射 (MJ):在 BJ 工艺中,液体粘结剂被选择性地沉积以粘结粉末材料。相反,在 MJ 工艺中,构建材料的液滴采用与喷墨打印非常相似的过程选择性地沉积。
图 5:这种 3D 打印机的末端执行器更重,因此围绕 SCARA 机械臂构建。(图片来源:Dreamstime)
片材层压:薄片材料粘合在一起,形成一个零件。这是最古老的增材制造工艺,早期的机器通过将纸质型材分层并粘合来制造复杂的 3D 零件,类似于制造胶合板的方式。
不同 AM 类型设备的共同点
上述所有 AM 方法都是通过对 2D 型材分层来构建 3D 零件——层层叠加。有些层具有明显悬垂或会脱离的特征,对于此类层的构建,先沉积支撑结构,然后在构建后移除。
虽然基于材料挤出的 FDM 是占主导地位的 AM 方法,用于从业余级 3D 打印机到塑料的工业原型制作,但有两种工艺在生产高强度航空级金属部件中的应用越来越普遍。分别是:
- 粉末床熔融 (PBF),用于小型和完全成品零件
- 定向能量沉积 (DED),用于通常需要精加工的大型零件
图 6:用于生产高级金属工件的 AM 设备是采用高级运动部件的伺服系统,在某些情况下甚至是采用直接驱动电机。这种构建使操作员能够利用激光型构建方法的精度。(图片来源:Dreamstime)
随着所有类型 AM 工艺的发展,它们已经开始采用许多相同的自动化解决方案。例如,Festo 的各种先进自动化部件(包括运动型滚珠丝杠或皮带驱动的机电式线性执行器)已经出现在各种 FDM 机器中,从业余级到专业设备以及高度复杂的 SLS 设备。
AM 设计的自由和限制
与机加工等减材工艺相比,AM 零件的一个显著优势是能够更加自由地创建不同形状。机加工特征只能在机床可以放置刀具的地方创建。这往往限制了内部转角的最小半径,使某些悬空的特征很难创建,并意味着内部空隙根本不可能用单一部件来实现。这些限制往往导致需要用螺栓将多个部件组装在一起形成结构,增加了制造成本和重量,同时降低了强度和可靠性。使用增材制造工艺生产的零件摆脱了这些限制,通常可以整合许多部件,在提高性能的同时大幅降低成本。
生成式设计是一种过程,在这个过程中,算法通过做许多小的改变和模拟不同部件的性能来设计部件,这个过程很像进化。由此产生的形状通常远比人类设计师所能创造的复杂,并且与自然进化的结构惊人地相似。
图 7:用生成式设计创建的结构通常与增材制造有关,尽管它们经常通过数字制造和五轴数控加工来生产。“NASA 进化结构”项目创造了图中所示的部件;NASA 团队采用了数控加工,因为对于超高性能的应用来说,机加工零件比 AM 零件性能更优异。部分原因是(尽管 AM 更先进)机加工部件受材料特性变化的影响较小。(图片来源:NASA)
随着部件越来越复杂,出现了有机外部形状及内部格子和槽道,数字模型需要更多的数据。渲染、切片、支持结构生成和机器代码生成等操作都变得更加困难。现有的棋盘格文件格式(以平面三角形的网格表示曲面)正变得越来越繁琐。一种方法是允许带有 3D 曲面三角形的网格文件,这样就可以用较少的三角形来近似表示一个曲面。
表示这种复杂几何形状还有个更有效的方法,即使用隐式几何,但这还不能与大多数 CAD 软件兼容。
AM 允许对内部几何形状进行控制
AM 创造内部几何形状的能力无可匹敌。凭借这种能力,使本来不可能实现的轻质和高强度结构具有类似于骨骼和植物茎的内部格子,还能设计具有内部管道、管子、歧管、冷却通道或热交换器等特征的整合零件。传统上这类部件由管材和板材加工和制造,导致恒定的直径和通道宽度,而使用 AM 可以改变轮廓。可以加入扰流器等功能,以改善传热。
图 8:图中所示为 GE 的 Aero LEAP 燃料喷嘴。(图片来源:GE)
想想 AM 航空部件如何在飞机上使用多年。最熟知的一个例子是通用电气自 2015 年以来一直在生产的 Aero LEAP 燃料喷嘴。这种喷嘴用单个整合部件取代了 18 个部件,而这个部件具有所有需要的复杂内部槽道。
通用电气的 Catalyst 涡轮螺旋桨发动机进一步利用了 AM,它将 800 多个传统方法制造的零件整合为 12 个 AM 零件。该发动机预计将于 2023 年取得认证。
激光束粉末床熔融 (PBF-L) 是最成熟的 AM 金属工艺。该工艺用于生产 GE 的发动机部件,也可以生产高质量的聚合物部件。由于需要在构建区域保持稳定的气流,以及在床中填充粉末的成本,构建体积的大小限制为 400 mm × 400 mm × 800 mm。金属粉末很重,而且要达到稳定熔融所需的质量,成本也非常高昂。单个激光器的沉积速率可达 20 cm3/h,而带有多个激光器的系统对铝制部件的沉积速率可达到 150 cm3/h。可以达到适合成品部件的良好表面光洁度。表面质量取决于粉末原料的颗粒大小,粒径可小至 5 µm。
粉末床熔融法生产的零件,其材料特性很大程度上取决于对熔池的控制,熔池用于将粉末材料熔融成固体零件。控制熔池在本质上与焊接操作相同,基本理解基于多年的焊接研究和开发。激光和电子束焊接的使用已有 50 多年的历史,而电弧焊已有 100 多年的历史。这种知识使生产的零件具有高度精细的晶粒结构,通常可与最高性能的锻件相媲美。但是,工艺的变异性仍然较高。
总结
虽然不太常见,但除激光外,其他能量束也可用于粉床熔融。电子束粉末床熔融的优点是可以用磁铁来控制光束,而不需要机械控制反射镜。这意味着可以实现更高的制造速率,但表面光洁度不如激光工艺好。
从技术的另一方面说,开源 3D 打印机可以内部制造,甚至可以打印自己的部件——本质上是自我复制。只需购买一些自动化部件,如步进电机;所有机械构件都可以制作出来。
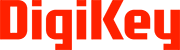
免责声明:各个作者和/或论坛参与者在本网站发表的观点、看法和意见不代表 DigiKey 的观点、看法和意见,也不代表 DigiKey 官方政策。