Achieving Wireless Connectivity for IoT Applications in a Power-Budget-Efficient Way
投稿人:DigiKey 欧洲编辑
2016-04-06
The IoT promises to deliver significant changes in the way we manage and interact with our homes and offices. It is also forecast to change the way that businesses provide services, especially in the commercial and industrial sectors where previously capital intensive equipment can be delivered as a service for rental to a customer. While the concept is easy to understand, the impact on an organization contemplating this will depend, on a large scale, on constant and reliable data gathering of many different data elements. This will be a job for an army of wireless connected microcontroller-based sensors, many battery operated and left in-situ for long periods of time. Provisioning such sensor data will require the design to use ultra-low-power wireless transceiver microcontrollers that not only have extremely-low-power standby currents but also employ power conservation techniques to prolong the operating life from a single coin cell. Such techniques could be implemented in hardware or software or a mixture of both, but clearly there are a number of other broader factors that the designer needs to consider before getting ready to select individual devices.
One of the key factors will be the wireless protocol selected. This will, in the main, be already determined by the amount of data to be transferred at a time. While Wi-Fi is a natural choice for moving large amounts of data, it is power hungry and for typical sensing applications it will be down to methods such as Bluetooth Smart and ZigBee along with other 802.15.4 sub-GHz techniques that will be the preferred choice. When selecting devices, engineers should also be aware of the various aspects that make up the overall power consumption profile of a device. There is a balance between computing performance and the power profile. You might use a more powerful device that offers more compute resources even though it might consume more power simply in order to complete the calculation and transfer tasks much quicker. Also, do not forget some communications stacks require the radio to operate longer for a given data packet so it is not just the standing consumption of the combined wireless MCU.
Figure 1: Ultra-low sensor controller runs independently of the rest of the device.
One such series of devices that offers this wide choice of communications methods is Texas Instruments' SimpleLink CC26xx device family. Combining a 2.4 GHz Bluetooth Low Energy (BLE) v 4.1 compliant wireless transceiver, an ARM Cortex-M3 32-bit processor, and an ultra-low-power 16-bit sensor controller, the TI CC2650 device offers a standby power consumption down to 1 μA with the RTC running and RAM retention and down to as low as 100 nA in shutdown mode from which it can be woken up by triggers from external events. With a CoreMark benchmark score of 141.85 and a CoreMark/MHz of 2.955 (CC2650-7ID device running at 3.0 V and 48 MHz) the MCU consumes 61 μA/MHz during active mode while the active mode transmitter current is 9.1 mA at +5 dBm output. The 16-bit sensor controller is responsible for keeping the radio transceiver in sleep for as long as possible. By combining with the external sensors such as analog comparators or ADCs, the sensor controller, Figure 1, is designed to run completely autonomously, allowing the radio and the 32-bit MCU to be kept in the extremely power efficient standby mode until it is required to send data. Capable of performing up to 10 ADC reads per second with an average consumption less than 3 μA, this approach could be used, for example, in a heart rate sensor application. For this you could perform up to ten measurements per second and then send all ten measurements at the same time. This hardware approach to implementing power conservation means that not having to wake up the radio and MCU for each measurement equates to a 10x power consumption saving (Figure 2).
Figure 2: Reading sensors 10 times before communicating data.
Another approach to conserving power is adding some degree of energy harvesting into the power supply. Silicon Labs has taken this approach with its Si1010 series of ultra-low-power sub-GHz wireless microcontrollers. The Si1012, for example, uses a high-speed 25 MIPS 8051 MCU combined with an EZRadioPro transceiver that can be operated from 0.9 to 3.6 V and consumes down to 0.1 μA in deep sleep mode. With the RTC and radio state retained it requires approximately 1 μA. Wake up from deep sleep is within 2 μs. Equipped with an ADC, three GPIO pins and four GP counter/timers, it makes an ideal device for use in IoT sensor applications. Capable of being powered from an energy-harvested source, the expectation is that an IoT sensor could be designed with a 15-year life expectancy without the need to replace the thin-film battery. To speed the design using this approach, Silicon Labs supplies an energy harvesting reference board that serves to fully prototype and demonstrate an ultra-low-power sensor design in practice (Figure 3). In addition to the Si1012 device, the board is equipped with a printed antenna, a power management IC and a solar panel.
Figure 3: Silicon Labs energy harvesting sensor evaluation board.
When the Si1012 is not transmitting data it can remain in an extremely-low-power state that equates to approximately 50 nA. As little as 50 lux of light is required to compensate for solar panel leakage currents and start charging the thin-film cell. The thin-film cell alone provides enough energy to power the wireless transceiver and sensor for approximately seven days. Indoor light typically provides up to 200 lux while outdoor conditions will provide up to 10,000 lux, more than sufficient to keep the cell charged and providing power. Figure 4 illustrates the likely duty cycle against energy consumption for an example IoT sensor application transmitting data every second.
Figure 4: Energy consumption profile Si1012.
Managing a sensor’s energy-efficient wireless communications can also be a job for finely-tuned software. This approach requires a detailed knowledge of the processes going on within the MCU and wireless transceiver at any moment in time. It should also be noted that in some instances the developer should also check that any compiler optimization options, such as ‘Optimize for time’, should be made full use. The quicker a sequence of code can be executed, the more time the device can be kept in a sleep mode. IDE tool chains are increasingly providing functions to monitor energy consumption during debugging, further helping a design to have as small an energy consumption profile as possible. The Atmel ATmega256RFR2 family of ZigBee/802.15.4 wireless transceivers is an example, where a set of published software techniques are available with the aim of adaptively lowering power consumption below normal specified limits. Combining an Atmel 8-bit AVR MCU core with a low power 2.4 GHz transceiver tailored for ZigBee/802.15.4 use, the device operates from a 1.8 to 3.6 VDC supply and has a deep sleep power current consumption of less than 700 nA. Maximum transmit current for the MCU and the transceiver is 18.6 mA. Figure 5 illustrates the different total power consumption across the available modes.
Figure 5: Atmel ATmega2564RFR2 wireless MCU power/sleep mode profiles.
Atmel’s Smart Reduced Power Consumption Techniques application note documents a set of reduced power consumption (RPC) software techniques that are self-contained, self-calibrating adaptive power-reduction schemes. One of the schemes is that of PLL energy-saving mode. This mode helps reduce the consumption by automatically switching into a power-saving mode immediately after the PLL has been calibrated. This approach, documented in more depth in the application note, can reduce device consumption from 5.2 mA to 450 μA. Another technique is that of smart receiving technology (SRT) where the transceiver can be periodically enabled and disabled while listening for an incoming dataframe. Depending on environmental conditions, data traffic and channel noise, the SRT mode can result in savings of up to 50% of the current consumption, although this will result in a small amount of sensitivity loss.
The benefits of the IoT will rely on myriad battery-powered wireless sensors that are often deployed in remote locations or difficult to access positions within large plants. Changing a cheap button cell battery is made significantly a lot more expensive when you consider the time to visit the location regularly, not to mention the disruption it can cause to IoT analysis and control systems in the intervening period.
Time spent implementing power conservation techniques, whether hardware, software, or a mixture of both, will lengthen operating life between battery replacements and also present that manufacturer’s sensor as being the most cost efficient in the market.
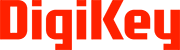
免责声明:各个作者和/或论坛参与者在本网站发表的观点、看法和意见不代表 DigiKey 的观点、看法和意见,也不代表 DigiKey 官方政策。