What Is a Capacitor and What Are the Different Types?
投稿人:DigiKey
2023-06-02
Introduction
At the time of writing, a conservative estimate showed upwards of 37,000 unique manufacturer part numbers for capacitors in stock at DigiKey, 114k if packaging variants are included. Simply maintaining that kind of SKU count involves an awful lot of paperwork, a lot of forklift mileage, and a lot of cash tied up in physical inventory. Being able to re-package those products to order and have them on the loading dock ready for shipment in as little as 15 minutes after receiving an order is a small miracle of modern industry. Why spend so much effort on simple two-terminal components? The combinatorics of voltage and current ratings are certainly a factor, but the more subtle reason is that capacitors aren’t really that simple. The schematic symbols we use to represent them are lies by omission for convenience, and obscure details that are often a) rather important and b) not well treated in academia. Some types tend to burn aggressively or release toxic vapors upon failure or misapplication. Other types weaken with disuse and can fail under stresses well within their rated limits. Some types exhibit wide parametric variations with environmental and application variables, while others are more or less oblivious. Making informed design choices requires awareness and consideration of these varying qualities. The objective of this resource is to offer the reader a guide to capacitor technology in an easy-to-swallow capsule with a (hopefully) non-drowsy formula.
What is a capacitor?
Capacitors are devices which store electrical energy in the form of an electric field. The process is quite similar to the way mechanical springs store energy in the form of elastic material deformation, to the extent that the math describing both is quite similar, save for the variables used. The similarity may in fact be part the reason that students of electrical or mechanical engineering often find the others’ studies arcane and inscrutable; “v” means “voltage” to an electrical engineer (EE), but “velocity” to a mechanical engineer (ME), whose representations of springs may look rather like inductors to an EE, etc. The concept of the parallel plate capacitor is generally used as the starting point for explaining most practical capacitor constructions. It consists of two conductive electrodes positioned parallel to each other and separated by an insulator, usually one of several polymers, ceramic materials, metal oxides, air or occasionally a vacuum. The value of such a capacitor, essentially it’s “spring constant” for the mechanically–minded, is approximated by the formula in Figure 1 when the separation distance between the plates is small relative to their area. It should be noted however, that mechanical spring constants and capacitor values are, by convention, expressed with reciprocal dimensions; a mechanical spring constant is typically expressed in terms of force per unit of displacement (such as newtons per meter or pounds-force per inch), whereas a capacitance value is expressed in terms of displacement per unit force, i.e. coulombs per volt.
Figure 1: The parallel plate capacitance model.
Practically speaking, the plates need not be flat; rolled, folded, crumpled, stacked, sliced, diced, and julienned geometries work also, though the math involved can become rather messy as geometries become more complex. So then, to make a capacitor with a larger value, one can use plates with a larger area, reduce the separation distance (i.e., thickness of the dielectric material) or increase the dielectric constant of the material. Messing with ε0 pretty much requires the creation of an alternate universe, which is a rather difficult thing to do outside the realm of politics. But what the heck is this “dielectric constant” thing? Excellent question; it’s essentially a property of materials describing their ability to become electrically polarized in the presence of an applied electric field, through any of a number of mechanisms. These mechanisms might be at an atomic level, where the cloud of electrons surrounding the nucleus of an atom is displaced, resulting in an atom having a slightly positive charge on one side and corresponding negative charge on the other. It can also occur at a molecular level, due to changes in the orientation of electrically polar molecules in response to an applied field, or through bending & stretching of the bonds between atoms within a molecule, very much like the material in a mechanical spring is bent or stretched. Provided that the electrons in the atomic case don’t “blow away” and reassociate with an adjacent nucleus, and in the molecular cases that the molecules aren’t torn apart by the force of the electric field, the material functions as an insulator; it doesn’t support a sustained flow of charge when an electric field is applied, though it does effectively permit some charge to flow as the field is established due to the shifting of electrons around an atom or reorientation/distortion of molecules. Removing the applied electric field allows the electrons in the dielectric to return to their normal distribution around the nuclei to which they’re attached, or the molecules in the substance to return to their original random orientation or shape. In the process of so doing, most of the charge that flowed through the capacitor when the electric field was applied is returned to the circuit, flowing in the opposite direction. A material’s (relative) dielectric constant describes the extent to which a material facilitates this temporary current flow, relative to the extent that a vacuum does. A material that allows the same amount of charge transfer as a vacuum for a given area, separation distance, and applied field strength has a dielectric constant of 1. A material allowing twice the charge transfer as a vacuum has a dielectric constant of 2, etc. The nuances of different capacitor types are, for the most part, determined by the characteristics of the dielectric used and the method by which a given device is constructed. All dielectric materials have limitations, with regard to the maximum applied field they can withstand for a given material thickness, their dielectric constant, losses that occur in the dielectric material and electrodes, and the amount of current that flows or “leaks” through the dielectric when the applied electric field is constant.
Non-ideal properties of capacitors
For many purposes, real capacitors can be represented using a relatively simple lumped element model, consisting of an ideal capacitor with several additional components.
ESR
Equivalent series resistance (represented by Resr in the model shown in Figure 2) describes losses associated with moving charge through a capacitor. The resistance of the electrode and lead materials is a contributing factor, and losses occurring within the dielectric material itself also occur and are often dominant. The relevance of ESR to capacitor selection is twofold: 1) it influences the AC response of the capacitor, and 2) it imposes limits on the amount of AC current that can be permitted to flow through the capacitor due to thermal limitations. Current flow through a capacitor’s ESR results in I2 R losses just like any other resistor, causing a temperature increase within the capacitor that contributes to diminished device longevity. ESR is influenced by device type and construction, and also by temperature and test frequency to varying degrees. In many cases, the ESR of a capacitor is not directly given in a datasheet, but rather communicated in terms of a summary figure such as Q, dissipation factor (DF), or Tan δ. All are quotients of a capacitor’s ESR and capacitive reactance (XC) expressed differently. Tan δ and dissipation factor are calculated as ESR/XC and are essentially the same figure, though it should be noted that dissipation factor is usually expressed as a percentage, rather than as a simple dimensionless factor. Q is simply the reciprocal of Tan δ, or XC/ESR.
Figure 2: A typical capacitor symbol contrasted with a schematic including non-ideal properties modeled as lumped elements.
ESL
Equivalent series inductance arises from the partial self-inductance of the device leads, coils formed due to the geometry of the device leads within the circuit, etc. In the lumped-model approximation, ESL is represented by an ideal inductor (Lesl) in series with the ideal capacitor (Cnom) representing the device’s nominal capacitance value. The relevance of ESL to capacitor selection is primarily its effect on AC response. As the lumped model suggests, real-world capacitors behave like series-connected LCR circuits. As the frequency of an applied AC voltage increases, the inductive reactance of the ESL increases to a point at which it is equal to the capacitive reactance of the device, and the capacitor behaves as a resistor. At frequencies above this point, the capacitor is effectively an inductor.
Leakage
Leakage is modeled as a relatively large-value resistor in parallel with the ideal capacitor in the lumped model. It arises from the fact that the dielectric materials used within the capacitor are not perfect insulators, and allow some amount of DC current to pass through the capacitor when a constant voltage is applied. Relevance of leakage to capacitor selection is application dependent; it can be a power consumption issue in micro-power applications, an error source in precision analog applications, or a reliability/thermal management issue in power applications.
Polarization
Polarization is a non-ideal property of most electrolytic capacitors, which rely on a dielectric formed through electrochemical action. Applying a voltage to such a capacitor with incorrect polarity causes a reversal of the electrochemical process used to create the capacitor’s dielectric layer. This process of electrochemically destroying the dielectric layer results in higher-than-specified leakage currents, which are exacerbated as the thinning dielectric layer begins to break down under the stress of the application voltage. Since leakage current results in internal heating and increases in temperature cause increases in leakage current, a cascading effect occurs that can result in rather spectacular catastrophic failures when the source impedance of the (mis)applied voltage is low. Non-polarized electrolytic capacitors (which effectively are two polarized capacitors placed back-to-back) are available for use in applications where the polarity of applied voltage is unknown or may be occasionally reversed, though their use requires a measure of caution.
Dielectric absorption
Dielectric absorption, also referred to as “soakage”, refers to energy storage within a capacitor’s dielectric that is absorbed and released on a longer time scale than would be predicted by the device’s nominal capacitance and ESR. In the lumped-element model, it can be represented as a series connection of a resistor and capacitor (or multiple instances thereof) in parallel with a device’s nominal capacitance. Practically, this means that a capacitor held at DC potential for some length of time and then briefly discharged will appear to recharge itself to some degree. In a different example, the discharge through a resistor of a capacitor held at a DC potential for a while will be well-modeled by the usual exponential equation during the rapidly-changing portion of the discharge curve. During the “long tail” portion of the curve however, the capacitor will deliver a current higher than that predicted by the usual R-C discharge equation. The phenomenon can be problematic in precision analog circuits, but poses a potentially lethal safety hazard in the context of high voltage, high capacitance devices such as those used in many power factor correction or DC bus filtering applications. Many types of capacitors used for such applications currently and historically are some of the most prone to energy storage by dielectric absorption, with some being capable of “self-charging” to perhaps a fifth of the voltage previously applied. With larger devices, the energy & voltage present at the terminals due to this process can be sufficient to cause injury directly (burns or cardiac arrest are two possibilities) or indirectly as a result of involuntary reactions to electric shock.
Dependence of ____ on _____
In the first blank, insert any device parameter of interest; capacitance, ESR, ESL, leakage, lifetime, etc. In the second insert most any application parameter; temperature, voltage, frequency, time, etc. There’s a relationship between the two, and it’s dependent on device type and construction. Some of the relationships aren’t particularly strong and are usually negligible, while others are stronger and less negligible than an 800-pound gorilla. Consequently, the existence and relevance of such relationships should be considered when making device selections.
Aging
Some capacitor types exhibit significant variations in their characteristics that occur on time scales much longer than most electrical signals of interest, rather like the way a Krispy Kreme® doughnut changes in character with time after leaving the fryer. This can pose problems from design, manufacturing, or calibration perspectives; a device that tests OK when it’s fresh out of the reflow oven might not meet spec after a week, for example.
Microphonics/Piezo effect
Recall that the equation for the capacitance between two parallel plates is a strong function of electrode separation/dielectric thickness; if the distance between the plates is changed (such as by application of a mechanical force) the capacitance changes also. If the capacitance changes but the amount of stored charge remains constant, the voltage across the capacitor’s terminals varies in inverse proportion to the change in capacitance. The result is that capacitors provide a transduction mechanism between the mechanical and electrical realms, commonly called a microphonic effect for its similarity to/application in audio microphones of the sort used in stage performances, portable electronics, etc. The effect is fantastically useful for these applications, but can also be problematic when it results in unintended coupling of mechanical signals into an electrical circuit, becoming a noise source or worse yet, an unintended feedback path. The transduction mechanism is also bi-directional; application of voltage across a capacitor’s terminals results in mechanical forces being applied to the electrodes that can in turn couple mechanically into the surrounding environment, as audible noise for example. Though present in all capacitors due to electrostatic forces (the phenomenon behind “static cling”), it’s most pronounced in devices that incorporate piezoelectric dielectric materials. Such materials develop an electric charge in response to mechanical strain, and going the other direction, deform mechanically when subjected to an electric field. Because the piezo effect tends to generate significantly more mechanical force per volt applied than electrostatic forces do, the coupling between the electrical and mechanical realms is much stronger in capacitors that incorporate piezoelectric materials.
Figure 3: Illustration highlighting the ability of capacitors to function as audio/ mechanical transducers.
Failure mechanisms of capacitors
Capacitors (like all other human contrivances) eventually fail, either parametrically or catastrophically. Parametric failures are those in which a device continues to function, but has slowly degraded to a point where it no longer meets performance specifications. Catastrophic failures on the other hand, are characterized by abrupt, dramatic shifts in device characteristics that result in out-of-spec behavior, which might include self-disassembly, combustion, incandescence, etc.
Dielectric breakdown
Failure by dielectric breakdown is an electrical condition where the insulating properties of a dielectric material are unable to maintain leakage current below a specified level. Frequently resulting from application of voltage in excess of a device’s rated limit or operation outside of specified thermal limits, failures by dielectric breakdown tend to be self-aggravating, low-impedance (short-circuit) failures. Consequently, they’re often spectacular, though some capacitor types have the ability to endure minor dielectric breakdown events gracefully. Since dielectric breakdown and thermal failures can be either’s cause or effect, categorizing a failure event as due to one or the other can occasionally be difficult .
Thermal
Thermal failures are those that occur due to excess device temperature. In circumstances where excess temperature causes a dielectric breakdown event, they’re usually short-circuit failures. Thermal failures may also be considered a long-term phenomenon, whereby prolonged operation at elevated temperature results in device parameter shifts beyond allowable limits.
Mechanical
Mechanical failures are those in which physical damage to a device is the proximate cause of failure, and may manifest as out-of-spec parameters, short, or open circuits. Frequently encountered with ceramic capacitors, mechanical failures are usually caused during manufacturing and assembly processes, but may also occur in the field due to abuse or poor mechanical design.
What are some common general capacitor specifications
Voltage ratings
A capacitor’s voltage rating is an indication of the maximum voltage that should be applied to the device. The context of the rating is significant; in some instances it may indicate a maximum safe working voltage, in others it may be more akin to a semiconductor’s “absolute maximum” rating, to which an appropriate de-rating factor should be applied.
Tolerance
A capacitor’s tolerance describes the limits of deviation from nominal capacitance value that a device should be expected to exhibit under specified test conditions, particularly AC test voltage and frequency. Quoted tolerance figures include the steady-state deviation from nominal value due to variability in manufacturing, and may (on rare occasions) also include temperature-induced variation in capacitance value over the stated operating temperature range. It should be noted that test conditions (temperature, frequency, amplitude, and DC bias value of test voltage among others) frequently have a strong influence on observed device parameters.
Safety ratings
Capacitors designed for use in applications where failure may pose a risk to the safety of persons or property (typically those involving AC line voltages) are designated with an alphanumeric safety rating, such as X1, X2, Y1, Y2, etc., according to regulatory standards. “X” rated devices are certified for applications where failure is not expected to pose a shock hazard, such as “line to line” applications, while “Y” rated devices are certified for applications where failure would pose a shock hazard, such as “line to ground” applications. The number in the designation indicates a level of tolerance to surge voltages, as specified in applicable regulatory standards such as IEC 60384-14. Devices may also carry multiple safety ratings, indicating their certification for use in different circumstances; for example a capacitor with an X1Y2 safety rating may be used in applications requiring an X1 rating as well as those requiring a Y2 rating.
Dielectric/electrode type
Capacitors are distinguished by the materials used in their construction, and to some extent by their operating mechanism. “Ceramic” capacitors for example use ceramic materials as a dielectric; “aluminum electrolytic” capacitors are formed using aluminum electrodes and an electrolyte solution, etc. Further specification of dielectric characteristics (and hence device performance characteristics) within a general capacitor type are often made, particularly among ceramic capacitor types. One common distinction to note is that between electrolytic and non-electrolytic capacitor types. Electrolytic capacitors use a dielectric material which is formed in-place electrochemically, usually by oxidizing the surface of the electrode material, whereas non-electrolytic (often called “electrostatic” capacitors) use dielectric materials that are generally formed through various mechanical processes and are not a chemical derivative of the electrode material itself. This distinction is useful because the two device categories share general traits within themselves, allowing one to roughly predict a given device’s qualities and application suitability simply by identifying whether or not it is an electrolytic type. Generally speaking, electrolytic capacitors offer high capacitance per unit volume, are polarized, low cost, high-loss, and exhibit lousy parameter stability. Non-electrolytic device types in contrast tend to be bulky for their ratings, are non-polar, relatively expensive, low-loss, and with a handful of notable exceptions, exhibit fair to excellent parameter stability.
Operating temperature range
A capacitor’s (operating) temperature range indicates the range of temperatures over which a device has been qualified for use. When specified separately, a storage temperature range is that range of temperature across which storage in a non-active state will not cause damage to the device or result in irreversible parameter shifts upon operation within the normal temperature range. For unassembled devices, further (more stringent) environmental Specifications may be made regarding storage in order to assure that lead finish materials do not degrade to a point that would inhibit proper assembly. Unlike most other qualifying parameters, operation outside of a device’s specified temperature range (particularly at lower temperatures) is often comfortably possible, provided that provisions are made to account for parameter shifts that occur as a result, and that the temperature excursions do not result in mechanical damage to the device. Operation at temperatures above a device’s rated limit is more perilous due to the presence of temperature-related wear and failure mechanisms, but is often possible in circumstances where device longevity is not a significant concern. Such out-of-spec operation is, however, at the designer’s risk and requires due care in device qualification.
Ripple current ratings
A capacitor’s ripple current rating indicates the maximum AC current that should be allowed to pass through the capacitor. Because current flow through a capacitor results in self-heating due to ohmic and dielectric losses, the amount of current flow a given device can tolerate is finite, and is influenced by environmental conditions.
Lifetime
Many capacitors, aluminum types in particular, possess strong wear mechanisms that limit their service longevity. A lifetime specification is an indication of a device’s expected service life under specified operating conditions. Note that definitions of service life may vary; one common definition is the length of service under specified conditions (which usually are near rated maximum values) within which 50% of fielded devices can be expected to fail. Some specifications are more stringent, others may be more lenient.
Military, high reliability, and established reliability
For applications that are ill-tolerant of device failure, capacitors are available which are produced and tested according to defined protocols in order to provide a statistical assurance of device reliability. Particularly sensitive applications commonly require that components be procured through documented channels, which allow a given component’s origins to be traced back through the production processes in order to assure device integrity and facilitate root cause analysis in the case of failure. MIL-HDBK-217F Notice 2 is, at the time of writing, the most widely used guide for predicting reliability of electronic equipment, though the procedures established by Telcordia have also been widely used, particularly in the telecommunications industry.
Packaging and mounting types
Like most electronic components, capacitors are available in a variety of package and mounting types. Device characteristics and common application constraints influence the available options, which may include surface-mount devices, axial- and radial-leaded through-hole types, and chassis-mount types.
What are aluminum capacitors?
Aluminum capacitors are a family of devices that fall under the umbrella of “electrolytic” capacitors. As such, they offer high capacitance values in small packages at relatively low cost. In trade for these desirable qualities, their electrical properties and service lives tend to be relatively dismal. Though ill-suited for all but the most barbaric of signal-related applications, aluminum capacitors are a staple for DC power-related functions. Three distinct types are available; the standard aluminum electrolytic capacitor, a bipolar variant on that theme, and a newer type which incorporates a conductive polymer electrode. Referring to the family as “aluminum capacitors” rather than “aluminum electrolytic capacitors” is a hat-tip to this latter device type which doesn’t contain a traditional liquid electrolyte.
Figure 4: Aluminum capacitors in different package styles. L-R, surface mount, through-hole, and chassis mount. (Not to scale)
Device construction
Standard aluminum electrolytic capacitors consist of two sheets of high purity aluminum foil, interleaved and separated by a spacer material such as paper that is saturated with an electrolyte solution. These foil sheets are usually etched on a microscopic level, increasing their effective surface area by as much as a few hundred times what it would be were the foil left smooth. On one of the foil sheets (in standard Aluminum electrolytic capacitors) a layer of aluminum oxide is formed that serves as the capacitor’s dielectric material by applying a voltage to the foil through an oxygen-bearing electrolyte solution. So doing causes oxygen from the electrolyte to bind to the aluminum foil’s surface, forming an oxide layer with a thickness proportional to the voltage applied during the formation process, and determined by the intended working voltage of the capacitors to be produced. Typically, the thickness of this oxide layer is on the order of 1 micrometer, or 0.00004 inches. The underlying, non-oxidized metal forms one of the electrodes of the aluminum electrolytic capacitor. The other electrode is not the second sheet of foil, but rather the electrolyte solution. In standard aluminum electrolytic capacitors, the second foil sheet has no deliberately formed oxide layer and is simply used to make electrical contact with the electrolyte because it’s kind of hard to solder a liquid to a circuit board... In bi-polar capacitors, an oxide layer is formed on both aluminum sheets, resulting in a device that’s effectively two capacitors connected in inverse series. Because the electrolyte is a fluid (except in the case of aluminum polymer capacitors, where it’s a conductive polymer material) it is able to conform to the microstructure of the etched & oxidized foil sheet, resulting in a large area between the two electrodes of the capacitor. Since the dielectric material (aluminum oxide) is quite thin, the end result is a capacitor with a high value; per the basic capacitor equation, capacitance increases in proportion to electrode area and in inverse proportion to electrode separation distance/dielectric thickness. Lead wires are attached to the foil sheets, the assembly is wound, folded, or otherwise formed to fit in a container (usually also made of aluminum), and the assembly is sealed using a rubber sealing plug. Because fault conditions can result in a buildup of internal pressure, most aluminum capacitors also include provisions for venting such pressure in a relatively safe manner. A dedicated mechanism is usually used for this purpose in larger devices, whereas smaller devices achieve the protective venting function through careful design of the rubber sealing plug and/or scoring of the container so that it ruptures in a relatively controlled fashion should excess internal pressure develop. Standard, bi-polar, and polymer types are included.
Range of available capacitances and voltages
Figure 5: An illustration of the range of voltage/capacitance ratings for aluminum capacitors available through DigiKey at the time of writing.
Application strengths and weaknesses
The primary strength of aluminum capacitors is their ability to provide a large capacitance value in a small package, and do so for a relatively low cost. Additionally, they tend to have good self-healing characteristics; when a localized weak spot in the aluminum oxide dielectric layer develops, the increased leakage current flow through the weak point in the dielectric causes a chemical reaction similar to that used during the initial formation of the dielectric layer, resulting in a thickening of the dielectric at the weak point, and a consequent reduction in leakage current. The shortcomings of aluminum capacitors are mostly related to (a) the chemically-reactive nature of the materials used in their construction, (b) the conductive properties of the electrolyte solutions, and (c) the volatility of liquid electrolytes. The chemically reactive nature of the materials used in aluminum capacitors is problematic on two points; the stability of the dielectric layer and the long-term mechanical integrity of the device. Since the aluminum oxide dielectric layer in these devices is formed through an electrochemical process, it can also be eroded by an electrochemical process simply by reversing the applied voltage. This is why most aluminum capacitors are polarized; application of voltage with the wrong polarity causes rapid erosion & thinning of the dielectric, resulting in high leakage current and excessive internal heating. From a mechanical integrity standpoint, mixing a highly reactive metal (aluminum) with a corrosive electrolyte solution is a delicate proposition; errors in electrolyte composition can result in premature failure, as evidenced by the “capacitor plague” of the early 2000’s. Another shortcoming of aluminum electrolytic capacitors is the fact that the electrolytes used aren’t particularly efficient conductors because conduction in electrolyte solutions is achieved through ionic, rather than electronic conduction; instead of loose electrons moving between atoms serving as the charge carriers, ions (atoms or small groups thereof that have a charge due to a surplus or deficit of electrons) are moving about throughout the solution. Since ions are more bulky than electrons, they don’t move as easily and hence ionic conduction generally tends to be a higher resistance proposition than electronic conduction. The extent to which this is the case is influenced significantly by temperature; the lower the temperature, the more difficult it is for ions in an electrolyte solution to move about through the solution, which translates into a higher resistance. Thus, electrolytic capacitors tend to have a relatively high ESR that exhibits a strong inverse correlation with temperature. The third major downside to aluminum capacitors (with the exception of the solid polymer types) is that the liquid electrolyte solutions tend to evaporate over time, eventually being lost to the atmosphere by diffusion through the rubber sealing plug, leaks in safety vent structures, or similar phenomena.
Common uses and applications
Aluminum capacitors are primarily used in DC power applications calling for a relatively large value, low-cost capacitor, when AC performance and parameter stability over time are not particularly critical. Such applications include bulk filtering of rectified AC line voltage in power supply applications and output filtering in low-frequency switching power supplies, etc. Due to the time constant formed by their relatively high ESR in series with their large nominal capacitance, aluminum capacitors as a class tend to lose their appeal quickly as ripple frequencies approach about 100 kHz. Device optimizations vary widely though, and the useful frequency limit for any given device might be as low as a few kHz to 1MHz. Aluminum electrolytic capacitors are generally not suitable for applications where high losses and wide variability of device parameters with environmental and operating conditions is undesirable, which includes most analog signal paths.
Common failure mechanisms/critical design considerations
Electrolyte loss
The liquid electrolyte found in most aluminum capacitors is subject to evaporation over time, leading to an increase in ESR and reduction in capacitance. This is a wear mechanism which is typically the limiting factor for the service life of an aluminum electrolytic capacitor. The clock starts immediately upon manufacture of a device and does not stop, although application and storage conditions influence the rate at which the hands move. Temperature is the principle factor in determining the rate of electrolyte loss, and is well-described by the Arrhenius equation, which predicts roughly a factor-of-two change in process rate for every 10°C change in temperature. Stated differently, reducing the temperature of an electrolytic capacitor by 10°C roughly doubles its expected service life, all other factors being equal. Electrolyte loss is also influenced by atmospheric pressure, with lower pressure resulting in accelerated electrolyte loss. Extreme low-pressure environments may cause devices not designed for such environments to experience case rupture or opening of the safety vent, resulting in failure much sooner than would occur at higher ambient pressures. When estimating capacitor lifetime on the basis of the Arrhenius relationship and the manufacturer’s stated lifetime specification, self-heating due to ripple current must be taken into account; the internal temperature of the capacitor is the quantity of interest, not simply the application’s ambient temperature. For high-altitude or low-pressure operations, consult manufacturers’ specifications, as de-rating of stated lifetime will be required, down to zero at an ambient pressure at which the difference between the electrolyte’s vapor pressure and the outside ambient pressure will cause the capacitor’s safety vent to open. Note that vapor pressure generally increases with temperature, resulting in a tradeoff between operating temperature and maximum permissible operating altitude.
Faulty electrolyte
Improper electrolyte formulation can cause rapid corrosion of internal components and/or buildup of gas pressure in an aluminum capacitor, resulting in premature failure. This mechanism is reportedly responsible for widespread premature failures of aluminum electrolytic capacitors in many consumer electronic devices in the early 2000’s. Aside from independent testing and evaluation, the best way to avoid this problem (which has proven extremely expensive for many companies) is to purchase product only from reputable manufacturers, either direct or through a manufacturer-authorized distributor. Buying cheap electronic components from questionable sources is a lot like buying pharmaceuticals in plastic baggies from a stranger on a street corner in the bad part of town at 2AM… Don’t do it.
Voltage overstress
As the voltage applied across an aluminum electrolytic capacitor exceeds prescribed limits, the leakage current through the aluminum oxide dielectric layer increases rapidly, beginning at localized “thin” spots within the dielectric material. This increase in leakage current results in increased localized heating within the device. If the leakage current is not limited, the increased localized heating can cause further damage to the dielectric layer, resulting in a cascading failure of the dielectric material and destruction of the capacitor.
Current overstress
Aluminum electrolytic capacitors often have a comparably large ESR value, mostly due to the resistivity of the electrolyte solution. AC currents flowing through this resistance result in ohmic heating, which contributes to electrolyte loss and increases the risk of a dielectric breakdown event. It should be noted that the apparent capacitance of an aluminum electrolytic capacitor is frequency dependent. Consequently, the ripple current specification provided by the manufacturer should be interpreted in light of the ripple frequencies present in the application. Maximum ripple current figures for aluminum electrolytic capacitors are commonly quoted at 120 Hz and 100 kHz, so one should take care not only to observe the quoted ripple current value when selecting the device, but also the test frequency for which the figure is quoted.
Voltage overstress due to aging
Due to the electrochemical nature of the dielectric formation process, storage at zero applied voltage for extended periods of time results in degradation of the aluminum oxide dielectric layer. With the dielectric weakened, voltage overstress conditions can occur even though an applied voltage may be within a device’s rated limits. In mild cases, the only symptoms may be an increased leakage current and elevated device temperatures for a time, until the device self-heals. In severe cases where maximum rated voltage is applied though a low source impedance across a badly-degraded dielectric, a device may fail short-circuit and rupture in spectacular fashion. While developments in electrolyte formulations to address the issue have been and continue to be made, storage stability varies significantly among different products, with some experiencing measurable degradation after only 1 to 3 years of storage in a discharged state. In designing applications that may lie dormant for extended periods of time, moderate voltage de-rating of devices is recommended in order to provide an improved margin of safety against this effect. Use of products specifically designed to be robust against degradation in storage is also suggested. In repair/recommissioning situations, the generally prescribed treatment for atrophied aluminum electrolytic capacitors is to apply the system voltage gradually, over a period of 4-8 hours. Before so doing, verify that the equipment will not be damaged by a prolonged period of operation at below-spec supply voltages.
Device features, options, and targeted applications
Audio
Aluminum electrolytic capacitors marketed for audio applications are commonly low-ESR types, and design compromises in their construction may be skewed in favor of electrical performance and parameter stability at the expense of things such as size and cost. It should be noted however, that the audio field is riddled with subjectivism and marketing designed to separate fools from their money, and that this effect permeates even down to the component level. If capacitor A has a prettier label and costs ten times more than capacitor B, then obviously capacitor A is better, right? Not necessarily. Check the specifications, know which ones are important for the application at hand, and pick whatever device best meets the application requirements. Unless you’re building something to sell to the sort of person who is willing to spend hundreds or thousands of dollars on “directional” speaker cables. In that case, pick whatever offers you the most bling for the buck…
Automotive
Devices highlighted for automotive applications are typically designed for long life and operation over an extended temperature range, extending at least to 105°C. Most are qualified to AEC (Automotive Electronics Council) standards.
Bi-polar
Bi-polar electrolytic capacitors are designed to operate without damage when subject to voltages that change polarity, by forming an oxide film on both of the foil sheets used in a standard aluminum electrolytic capacitor, rather than just one. Because of the high ESR of such devices they’re generally considered unsuitable for operations with a continuously applied AC voltage, and for this reason are occasionally referred to as “non-polar DC capacitors” to emphasize the point. Their use is typically limited to DC applications where the polarity to be applied is uncertain, may occasionally reverse on a transient basis, or where the current flow through the device can be limited to values that do not result in excess self-heating.
General purpose
“General purpose” is a catch-all designation for devices that are not expressly designed to address a particular application category, and have no major distinguishing characteristics in their construction.
High temp reflow
Devices designated as “high temperature reflow” types are designed and qualified for use in applications where higher process temperatures are encountered during manufacturing, as is commonly encountered in lead-free/RoHS-compliant re‑flow soldering operations.
Motor run
Aluminum Electrolytic capacitors with this designation are designed for continuous-duty, high-ripple applications such as variable-speed motor drives and inverter applications.
Motor start
Aluminum Electrolytic capacitors with this designation are generally designed for use in AC motor starting applications. Typically they’re bipolar, rated for several hundred volts, and have values between a few tens to a few thousand uF.
Polymer
This designation is associated with aluminum electrolytic capacitors which use a solid conductive polymer as an electrolyte material, rather than a liquid electrolyte. Typically they exhibit better stability, lower ESR, and better lifetimes at elevated temperature than comparable liquid electrolyte devices, though availability is constrained to relatively low capacitance and voltage ratings, and the cost of devices for a given capacitance and voltage rating is significantly higher than a similar liquid electrolyte type.
Stainless-steel case
Devices with this designation are designed with ruggedized, stainless-steel cases that are capable of withstanding higher-than-typical pressure differentials between the inside and outside of the capacitor. This allows operation at lower atmospheric pressures than most other devices, and permits a longer expected operating life due to the ability to mitigate electrolyte loss. Typically, these devices are also quite costly.
What are ceramic capacitors?
Ceramic capacitors are electrostatic devices characterized by their use of various ceramic dielectric materials, which are commonly based on barium titanate (BaTiO3). They are non-polarized with characteristics covering much of the quantity-quality spectrum, with perhaps a slight bias toward quality. Many variations in construction and dielectric properties are available to address diverse application needs, and this broad applicability together with relatively low cost structures renders ceramic capacitors the most popular capacitor type in current use, reckoned by number of devices sold.
Device construction
Figure 6: Left: Multilayer Ceramic Chip Capacitor (MLCC); Right: Through-Hole Disk Capacitor.
Early devices were constructed as a single layer of ceramic dielectric material (usually circular in shape) between two metal electrodes. Leads were affixed to the metal electrodes and the assembly encapsulated in an insulating material, typically a ceramic or epoxy. While this construction type is still found in devices intended for AC line or high voltage applications, few if any devices based on this construction method are suitable for surface mounting, which limits their appeal for many applications. Far more common today are multilayer ceramic chip capacitors (MLCCs) which use alternating, interleaved thin layers of electrode and dielectric materials in order to achieve a large electrode surface area in a small overall package volume. Such devices are constructed by extruding thin sheets of unfired ceramic “clay” upon which an electrode material in finely divided form is deposited through a process similar to screen printing. A number of these “sheets” are stacked and pressed together to create the desired number of electrode layers, cut into individual capacitors, and fired in a high temperature oven to harden the ceramic dielectric material and fuse the particles in the electrode metal. Terminations are then applied, and the devices passing final inspection are packaged for shipment.
Figure 7: Simplified MLCC production process. (Source: WikiMedia Commons)
Range of available capacitances and voltages:
Figure 8: An illustration of the range of ceramic capacitor voltage/capacitance combinations available from DigiKey at the time of writing.
Application strengths and weaknesses
Ceramic capacitors (MLCCs in particular) have earned widespread favor due to their versatility, economy, durability, and generally favorable electrical characteristics. Where their application territories overlap, ceramic capacitors generally have favorable characteristics relative to other types (aluminum, tantalum, etc.) used for bulk power processing, and somewhat inferior characteristics relative to thin film or other types used where the utmost in stability and precision are required. The versatility of ceramic capacitors is reflected by the range of available values, which span some 9 orders of magnitude in capacitance and 4 in voltage as represented in Figure 8; not many technologies scale across such breadth. For the most part, the raw materials used in ceramic capacitor construction aren’t particularly costly and are efficiently utilized, and while a high degree of precision and process control is required, the basic manufacturing processes aren’t grievously complex. Together, these attributes allow MLCCs to be produced by the billions each year, often at sub-penny unit costs. From an application perspective they are well-suited for long-lived applications; being essentially a layer cake of durable materials (metals and ceramics) they possess no strong wear out mechanisms, no acute vulnerabilities to temperature, pressure, or voltage reversal, nor risk of leakage, combustion, or toxicity as variously encountered with electrolytic devices. Since they do not depend on relatively high-resistance electrolyte solutions for their operation as do electrolytic devices, the ESR of ceramic capacitors tends to be quite low, and their internal geometries (and short lead lengths, in the case of MLCCs) render board layout the dominant contributor to ESL in many cases. Application weaknesses of ceramic capacitors include mechanical vulnerability, absence of self-healing capabilities, cost at high capacitance values, and varying degrees of parameter dependence on environmental and electrical operating conditions, depending on the specific formulation of the ceramic dielectric material. Like most ceramic objects, ceramic capacitors are quite brittle and inflexible. Consequently, they are vulnerable to damage as a result of mechanical stress or thermal shock, and careful mitigation of such factors during assembly and service in the end product are needed. The downside to ceramic capacitors’ relatively inert “steel and stone” construction is that no self-healing mechanism is present; stresses resulting in dielectric breakdown tend to result in irrecoverable damage to the device, and substantive safety factors must thus be built in as additional dielectric thickness, since weak spots in the dielectric cannot easily be “burnt out” during production. This contributes to ceramic capacitors’ relatively high cost per Farad (compared with electrolytic types) and together with the increasing risk of mechanical damage as device sizes increase, results in diminishing appeal/availability of ceramic capacitors in values beyond a few 10’s of microfarads. Finally, many ceramic dielectric formulations are not parametrically stable or linear with temperature and dielectric stress, to an extent that’s generally proportional to their dielectric constants. Consequently, high-value ceramic capacitors are frequently unsuitable for precision applications.
Important design considerations
Temperature characteristics and dielectric classifications
Numerous ceramic dielectric materials are in common use, and vary widely in their volumetric efficiency, temperature dependence, loss characteristics, and other non-ideal behaviors. Different devices are categorized according to their temperature characteristics, with different lines of demarcation and systems of identification established over the years by the EIA (Electronics Industry Association) and IEC (International Electrotechnical Commission), as well as the U.S. military and other standards bodies. The common thread among these systems is a distinction between quality and quantity of capacitance; low-loss/high-stability/temperature linear types used for precision analog and resonant circuit applications are addressed differently from types providing a high capacitance per volume at a cost of poorer stability and linearity. The IEC standard designates dielectrics designed for quality and quantity of capacitance as class 1 and class 2, respectively. Like the IEC standard, the EIA standard designates quality-focused dielectrics as class I (Roman numeral, not always used) though it subdivides the IEC class 2 devices into the EIA classes II and III. EIA class II devices are those which retain a measure of dignity with regard to parameter stability over temperature (+/- 15% or better over a stated range, usually -50°C to 85°C or higher), while the EIA class III dielectrics abandon all pretense of temperature stability in pursuit of volumetric efficiency, having wider parameter variations over narrower temperature ranges; +22%/-56% across +10° to +85°C or +22%/-82% across -30°C to +85°C are common class III limits. Figure 9 illustrates the phenomenon graphically, showing one manufacturer’s characterizations of dielectrics with several different temperature characteristics.
Figure 9: Typical capacitance variation as a function of temperature for ceramic capacitors of several different dielectric classifications. (Source Data: AVX Surface Mount Ceramic Capacitor Products Catalog, v13.10)
Various dielectric formulations are available in each general dielectric class, categorized by temperature coefficient of capacitance in the case of class 1 dielectrics, and limitations on change in capacitance across a specified temperature range for the other device classes. “Secret decoder rings” for a few classification schemes are shown in the tables of Figure 9A. MLCCs with IEC Class 1 (EIA Class I) dielectrics are designed with controlled, specified temperature coefficients of capacitance; the capacitance of these devices is a linear function of temperature. The dielectric classification for EIA class I devices indicates both the slope of that line and the tolerance of said slope. In contrast, the dielectric classification for class II and III ceramics indicates outer boundaries on two quantities: 1) changes in capacitance as a function of temperature, as a percentage relative to the value at a standard temperature (usually 25°C) and 2) the temperature range over which the boundaries apply. Nothing is implied about the slope of the temperature characteristic within those limits; most aren’t even monotonic, much less linear.
Figure 9A: Tables showing the behavioral limits signified by different designators under the EIA and U.S. Military classification schemes..
Two important observations should be made regarding classifications of the IEC class 2 (EIA class II/III) dielectrics:
- They indicate capacitance change as a function of temperature only. Other influences are NOT included in the ∆C figures, and these influences may be SIGNIFICANT. (See section on voltage coefficient of capacitance)
- They are NOT absolute prescriptions for a dielectric formulation, only a means of grouping devices on the basis of temperature behavior alone. Different part numbers (particularly those with differing package sizes) can behave differently in a given application, even if they have the same value, tolerance, voltage rating, and dielectric classification.
Tolerance specifications
The distinction between manufacturing tolerance and temperature behavior specifications for ceramic capacitors is easily misapprehended, owing likely to the frequent similarity of the figures’ magnitudes, the common practice of expressing both as a percentage, and imperfect linguistic discipline. Properly speaking, the “tolerance” specification on a ceramic capacitor indicates permissible variations in device value under standard test conditions as a consequence of manufacturing variability. It is typically specified as a percentage of nominal value, and refers to variations between different devices with the same part number under standardized test conditions, relative to nominal value. Put differently, it is a measure of the uniformity of the parts coming off the manufacturing line. In contrast, the “temperature characteristic” of a ceramic capacitor indicates the extent to which the capacitance of any given device can be expected to vary with temperature across that device’s stated operating temperature range. The term “temperature coefficient” is best reserved for devices using class I dielectrics, which have a more or less linear temperature dependence, while the term “temperature characteristic” is more appropriate for capacitors using EIA class II and III dielectrics, which exhibit decidedly nonlinear shifts in capacitance with temperature.
Figure 10: Tolerance vs. temperature of a Vishay BC Components D471K20Y5PH6UJ5R ceramic capacitor.
For example, P/N BC5214CT-ND is a ceramic disc capacitor specified as having a nominal 470 pF capacitance, +/-10% tolerance, and a Y5V temperature characteristic. Measured under the specified test conditions, devices with this P/N should exhibit a capacitance between 423 pF and 517 pF; this is the device tolerance, and is stating that some point on the red line in the graph at left in Figure 10 should describe a device with this part number. However, the Y5V temperature characteristic indicates that device capacitance may vary by an additional +22%/-82% when measured at temperatures between -30°C and +85°C, relative to its value under the standard test conditions. In other words, a device can meet specification as long as the plot of its capacitance vs. temperature (measured with the specified test signal, with specified temperature history, etc.) stays within the blue box vertically and passes through the red line; outside the horizontal (temperature) limits of the box, anything goes. When the temperature characteristic is factored in, we find that this (nominally) 470 pF capacitor could exhibit a capacitance anywhere between 76 and 630 pF (except at 25°C) yet remain completely within specification. With the addition of aging and voltage effects as variables, the actual observed capacitance can vary over an even broader range without violating the device’s specified limits. The distinction between “tolerance” and “temperature characteristic” here is clearly quite important; a designer mistakenly believing that the device will exhibit a value within 10% of nominal is likely to be disappointed if the application ever strays much from room temperature. Compare P/Ns 490-3271-2-ND and 490-5920-2-ND; both 0.1 uF, 25 V capacitors in an EIA 0402 package. The former uses a class III dielectric with a Y5V characteristic, has a tolerance of -20%~+80%, and a per-unit list price of $0.00399 in quantity at the time of writing. The latter uses a class II dielectric with an X5R characteristic, has a +/-10% tolerance, and sells for $0.00483. The tolerance bands and windows that result from factoring in the temperature characteristics are plotted together in the chart at right in Figure 10. As with the previous chart, devices that come off the assembly line are in spec if their actual capacitance as a function of temperature stays within their respective box and passes through the vertical line@ 25°C. The X5R (class II) device stays more than three times closer to nominal value than the Y5V (class III) device and does so over a wider temperature range, while the ratio between maximum and minimum device values due to the combined effects of manufacturing variability and temperature is nearly ten times less for the class II device. Less than 1/10th of a cent can buy a reduction in required design margins, improved production yields, reduced testing requirements, improved product longevity, etc. Such benefits would be worth every penny, but they don’t cost that much.
Voltage coefficient of capacitance
Ceramic capacitors exhibit changes in capacitance with variations in DC bias level. Stated differently, measuring the capacitance of a device with a 1 VP-P size wave averaging 0 V will yield a different (typically greater) value than if the same device is tested with a 1 V sine wave having a DC offset of 10 V. The effect stems from stresses placed on the dielectric’s crystal structure as a result of an applied voltage gradient, and consequently scales with dielectric thickness/device voltage rating; all else being equal (which it rarely is…) a device rated for 100 VDC will require a DC bias four times greater than a device rated for 25 VDC in order to exhibit the same proportional change in capacitance. Unsurprisingly, the effect is also influenced by dielectric formulation. EIA Class I dielectrics exhibit relatively small voltage coefficients, with observed capacitance typically changing by a few percent at most (often less) as DC bias is varied between 0 and 100% of a device’s rated voltage. EIA class II dielectrics are markedly more influenced by DC bias, with capacitance changes on the order of 20-60% being par for the course. Such variations are certainly nothing to sneeze at, but are markedly less severe than those exhibited by EIA Class III dielectrics, which commonly exhibit capacitance variations as large as 80-90% or more over their rated voltage. No, that’s not a typo; the effective capacitance of a ceramic cap using an EIA class III dielectric material can change by an order of magnitude simply as a result of DC bias. The effect may also be unfavorably non-linear; some devices can exhibit reductions in capacitance of 75% when biased to only 20% of their rated DC voltage. Making matters worse, the effect is cumulative (though not linearly additive) with temperature effects. -100 -80 -60 -40 -20 0 20 0 2 4 6 8 10 12 14 16 18 Capacitance change (%) DC Bias (V) DC Bias Characteristics 0402 (CGB2A1X5R1C105K033BC) 0603 (C1608X5R1C105K080AA) 0805 (C2012X5R1C105K085AA).
Figure 11: The influence of package size on DC bias effect. Source: Data from TDK Components Characteristic Viewer online tool.
What is perhaps more surprising (and insidious) is the relation between the magnitude of the DC bias effect and device package size. Cramming ever-larger capacitances into ever-smaller packages entails compromises at some point, as illustrated in Figure 11, showing capacitance change as a function of DC bias for three different 1 uF/16 V/ X5R capacitors from the same manufacturer’s product series; the main difference among them is simply package size. The cost of the smaller packaging is evident; the device in an EIA0805 package (green) exhibits a few percent loss of capacitance with a 5 V bias, while the more aggressive 0402-packaged device (blue) loses nearly 70% under the same conditions, and the device in 0603 packaging (red) falling somewhere in between. Recognizing that many applications involve both a DC bias and an interest in maintaining some minimum capacitance (output filters for low-dropout voltage regulators, for example) the potential for ignorance to carry an unpleasant penalty here is evident. Unfortunately, descriptions of these voltage-dependent effects are not a de-facto part of device datasheets, making it easy to overlook or remain ignorant of their existence, and complicating efforts to compare different products. Be assured that they do exist however, and bear the fact in mind when making device selections.
Cracking
Due to the brittle and relatively inflexible nature of ceramic materials, mechanical damage is the principle cause of failure in ceramic capacitors. Electrical symptoms of failure can manifest as a reduction in capacitance as well as short or open circuits. In some cases, these symptoms may appear to come & go with external influences such as temperature. Sometimes cracks in ceramic capacitors are visible with the unaided eye, other times they’re too small to see, or hiding on the underside of a mounted device or at the edge of a terminal. Mechanical damage is typically inflicted through one of several mechanisms:
- Board flexure during assembly or resulting from connector mating forces, rough handling, etc.
- Thermally-induced stresses from operational temperature cycling or assembly operations.
- Direct damage due to mishandling prior to or during assembly.
By far, multilayer ceramic chip (MLCC) types are the most frequent victims of cracking due to the tight mechanical coupling between the ceramic material, the terminals and the PCB. The relatively long and flexible terminals of through-hole or lead frame-mounted devices reduce the forces applied to the ceramic capacitor body as a result of temperature cycling or board ‑flexure, making cracking much less of a concern with these devices. For applications subject to harsh service conditions, MLCCs designed with improved mechanical flexibility between the terminals and the ceramic device body are available, as well as devices designed to mitigate the risk of short-circuit failure. Many of the sources of capacitor cracking are assembly-related and beyond the designer’s direct control; it’s the assembler’s responsibility to avoid crushing and smashing components during pick & place operations, for example, as well as to provide appropriate pre-heating and cool-down periods for the assembly processes used. Other factors such as the amount of solder paste used/paste stencil thickness are something of a shared responsibility, while factors such as pad sizes, board layout, and package selection rest squarely with the designer. Detailed discussions of MLCC cracking phenomena and their avoidance are available in industry literature, and will not be repeated here for brevity’s sake. Several rules of thumb for the designer distilled from this body of hard-won knowledge however are as follows:
- Choose an experienced, quality-conscious assembly contractor.
- Avoid thermal shocks; wave soldering and traditional soldering irons are particularly risky methods of assembly and rework for MLCCs.
- Reduce component size; larger devices experience greater stresses as a result of board flexure, and are more vulnerable to damage by thermal shock. Devices in 0805 (2012 metric) or smaller packaging are recommended.
- Use extreme care when singulating panelized boards after assembly, in order to avoid board flexure. Manual breaking of arrays along score lines by hand is the least-preferred method, with scissor shears not far behind. If possible, use a saw or other separation method that does not impart bending stresses to the PCB.
- Keep MLCCs away from board edges, connectors, mounting holes, large/heavy components, panelization tabs, or other points where mechanical stresses are likely to be introduced into the PCB. A minimum distance of 0.2” or 5 mm is suggested.
Aging
Ceramic capacitors are subject to an aging phenomenon related to changes in the dielectric crystal structure, which manifest as changes in capacitance and dissipation factor following the initial firing of the dielectric material. In keeping with established patterns, the EIA class I dielectrics are the least affected and are widely considered to be nonaging, while the EIA Class II dielectric materials are moderately affected, and the EIA class III materials tend to be affected quite severely. This aging process can be reset (or a device “de-aged”) by exposure to a temperature above the dielectric’s curie temperature for a period of time long enough to allow the crystal structure to re-form; the higher the temperature, the shorter the amount of time required. Since the curie temperatures of many ceramic dielectrics are below that encountered in many soldering processes, devices are likely to be at least partially de-aged during assembly. This aging behavior of a device is typically communicated as a percentage change in capacitance per decade hour, relative to its capacitance as measured at “last heat;” the last time the device was heated above its curie temperature long enough to fully reform its crystal structure. Stated differently, a capacitor with a (-) 5% aging rate that measures 100 uF in its “oven fresh” state would be expected to measure roughly 95, 90, and 85 uF after being out of the oven for 1, 10, and 100 hours, respectively. Obviously, this gives rise to questions as to what the nominal capacitance of the device should be, if that quantity is continuously changing even as a device sits unused on a shelf in its original packaging. Industry standards EIA-521 and IEC-384-9 speak to this question, essentially stating that a device should meet its specified tolerance values 1000 hours (about 42 days) after last heat. The next decade hour marks (10K and 100K hours) translate into a bit over 1 year and 11 years, respectively. Complicating matters, the aging process proceeds at a temperature-dependent rate; up to the dielectric’s curie temperature, increases in device temperature generally accelerate the aging process. Since aging phenomena can cause devices to appear to be outside of their stated tolerances, it’s important for product design & production test personnel to be mindful of the fact; testing of recently-re-flowed assemblies should expect capacitance values to be a bit high, and the design should have sufficient margin to function properly as devices age. Power conversion circuits are a good example of where this effect can pose acute dangers, since ceramic capacitors often end up having strong influence on the control loop of such circuits, either as compensation network components or as filter elements. A system that appears stable under the influence of a capacitor de-aged during assembly may be found to grow less stable with time as loss of capacitance due to aging affects the dynamics of the control loop. Most importantly, if a stable capacitance value over time is important, capacitors that age significantly should be avoided. Were Sisyphus a 21st century figure, his task might have been to tune an active filter built using surface-mount Y5V ceramic chip capacitors…
Piezo effect/microphonics
The IEC class 2 (EIA Class II and III) ceramic dielectrics are notably piezoelectric in nature, resulting in a not-insignificant transduction mechanism between electrical and mechanical domains. Applying a voltage across a piezoelectric material causes mechanical deformation and conversely, mechanically deforming a piezoelectric material causes a voltage to appear across it. This can be problematic particularly with surface-mounted MLCCs because of the tight mechanical coupling between the capacitor and the PCB. On one hand, ripple voltages imposed across a capacitor can be translated into bothersome audible noise; on the other, external mechanical vibrations can be coupled as signals into an electronic circuit. Ceramic capacitors based on class 1 dielectrics are affected the least, as these dielectrics exhibit little to no piezoelectric effect. The electrical-mechanical transduction mechanism via the electrostatic effect (inherent in all capacitors) still exists however, so while generally negligible for class I devices, microphonic effects are nonetheless still present.
Electrode metallurgy
The electrode materials in MLCCs follow one of two general metallurgical paths, referred to as noble metal electrode (NME) or base metal electrode (BME) systems. Though not a common selection criteria for most applications, the two technologies do result in differing characteristics which bear note. Noble metal electrodes are typically based on a palladium-silver alloy, and may also be referred to as precious metal electrodes (PME), since noble metals (those that are relatively nonreactive, particularly with oxygen) also tend to be expensive. Since these electrode materials are used because of their low reactivity and not because they are expensive, it could be argued that the former term is the proper one, though reason and marketing seem to disagree on the point… Base metal electrodes are commonly nickel-based. The significant issue at hand from a production standpoint is how the electrode metals react chemically at the high temperatures required to fire the ceramic dielectric materials; the noble metal electrode systems can tolerate the presence of more oxygen at elevated temperatures, and thus can be made using air-atmosphere kilns and dielectric formulations requiring oxygen to cure properly. Base metal electrode systems don’t have the same tolerance for oxygen at high temperatures, and thus must be manufactured using different equipment and dielectric formulations. The NME approach was the original route taken, and has some advantages in terms of reliability and accumulated industry experience. Consequently, much of the high-reliability and mil-spec product available at the time of writing is produced using this process. Principle drawbacks are high cost of electrode materials and lower achievable capacitance per volume relative to BME devices, due to the typical use of thicker dielectric layers in NME devices as a consequence of characteristic material and process differences.
Device features, options, and targeted applications
Automotive
Capacitors marketed as “automotive” types are designed for application in mechanically demanding environments, such as automobiles. Typically, they are also produced and tested in accordance with some protocol such as the AEC-Q200 standard established by the Automotive Electronics Council, which prescribes test methods and performance levels for various stress mechanisms such as ESD, mechanical force applied to the terminals, surge voltages, etc.
Controlled ESR
Capacitors designated as “controlled ESR” types are designed with a small amount of deliberately-added ESR in order to reduce the “Q” factor of the L-C circuit created by a capacitance with its parasitic inductances. This is helpful for applications such as supply rail de-coupling, where the presence of modest amounts of ESR can dampen the “ringing” of a capacitor with trace inductance, or help avoid anti-resonance conditions between parallel capacitors.
Epoxy mountable
Devices designated as epoxy mountable are designed to be mounted using conductive adhesives rather than the usual soldering processes. The difference is primarily in the materials used for the finish plating of the terminals, which differ in order to result in good bonding for the mounting method to be used; standard soldering processes don’t work well with epoxy mountable devices, and vice-versa. Epoxy mounting is beneficial in applications subjected to large, frequent temperature swings (such as automotive applications) where an epoxy joint’s increased mechanical ‑ flexibility relative to a solder joint reduces mechanical stresses that occur as a result of differing thermal expansion coefficients between a circuit board, solder joint, and capacitor body. Epoxy mounting is also useful for applications that are heat-sensitive, such as LCD panels.
Floating electrode
Devices designated as “floating electrode” types are effectively composed of multiple capacitors in series with inner electrodes that are not connected to either device terminal, but which are instead left “floating”. The purpose of this construction method is primarily to reduce the risk of short-circuit failure modes which often occur as a secondary effect of capacitor cracking, though it also offers benefits in terms of robustness to ESD and surge voltages.
High temperature
Devices designated as “high temperature” types are (unsurprisingly) intended for applications that experience temperatures above those encountered by most electronic equipment. Commonly this also means “wide temperature range” as devices with this designation tend to also be specified for use down to the lower ends of the commonly encountered operating temperature ranges for electronic devices. What isn’t blindingly obvious about this designation is that most devices bearing it exhibit rather impressive parameter stability for their kind, with respect both to temperature and often DC bias as well.
High voltage/Arc Guard™/Arc Shield™
Capacitors bearing “High voltage” and/or proprietary anti-arc designations are designed for use at application voltages beyond that which is typical for electronic devices. Definitions of what constitutes “high voltage” vary between manufacturers, though the lines of demarcation seem to fall in the 100 V to 1 kV range. At such potentials, MLCC technology begins to suffer complications from surface arcing between terminals, or between a terminal and an electrode connected to the other terminal through the device’s outer covering. This, of course, is not a good thing. While surface arcing becomes a problem for any component at high enough voltages, MLCC technology is particularly vulnerable due the fact that its compact construction necessarily places the two device terminals and their connected electrodes in very close proximity, increasing the risk of dielectric breakdown and arcing. Increasing device size to compensate is an option, but it comes at the expense of greatly increased risk of device cracking. Devices such as the Arc Guard™ and Arc Shield™ series of products are designed to mitigate these effects, and improve the tradeoff equation between the risk of failure via dielectric breakdown and that of mechanical cracking.
High Q/low loss/low dissipation factor
Devices marketed as High Q, low loss, or low dissipation factor types are designed to minimize ESR. Typically these devices are made of class I dielectric materials and used in RF or other high-frequency applications where near-ideal capacitors are desirable for frequency-discrimination purposes.
Integrated bleed resistor
Devices with this designation integrate a parallel-connected resistor for purposes of ensuring that charge does not remain or accrue on the capacitor when equipment is unpowered. At the time of writing, DigiKey lists only 3 part numbers bearing this designation, all of which are non-stock and carry hefty price tags. Why? Well, suggested applications listed on the marketing (first) page of the datasheet for these devices include “detonation devices” and “electronic fuzing” which aren’t exactly the sort of thing you see on most capacitor datasheets. (No, application notes are not available…)
Low ESL
Low ESL ceramic capacitors are designed to allow minimization of series inductance. In the case of surface-mounted MLCCs, most of this inductance is not intrinsic to the part itself, but rather related to the geometry of the package and the leads connecting it to the circuit. Thus, low ESL MLCCs are for the most part geometric and lead configuration variants of standard devices. Multi-terminal low-ESL devices use multiple physical terminals for each logical capacitor terminal and interleave them in such a way that the magnetic fields created by currents entering and leaving the device cancel to a large degree, resulting in lower inductance. Reverse Geometry ceramic capacitors place the device terminals on the long sides of a capacitor rather than at its ends, as is standard practice with other devices. Stacked low-ESL ceramic capacitors join multiple MLCC devices together on a lead frame, which allows them to be handled and assembled as a single unit and provides benefits in terms of reduced risk of cracking and microphonic effects. The description of such devices as "low ESL” is something of a marketing ploy because it’s only accurate in the context of an apples-to-oranges comparison with different capacitor technologies. Relative to the same ceramic capacitors mounted directly to a PCB, devices mounted on a lead frame (which elevates them above the board) will exhibit significantly greater ESL. The X2Y descriptor for low-ESL MLCCs is a trademark, and should NOT be confused with the similar-looking safety designators such as “X1Y2”. While there is some remote similarity between the two device groups in terms of why they’re used, the devices themselves are radically different. Low-ESL X2Y capacitors are rated for as little as 6.3V and are permitted to fail short-circuit every single time, whereas safety-rated devices must tolerate kV-level surges and avoid short-circuit failure modes like the plague. That said, X2Y low-ESR capacitors have significant merit for applications in low-voltage power supply decoupling, common-mode filtering, and similar applications. Their distinguishing feature is their 4-terminal construction; two terminals are electrically connected and act both as a “pass through” connection and as a common terminal for two separate capacitors within the device, each of which uses one of the remaining terminals for its second electrode connection. The geometry of this arrangement allows reduction of layout-related inductance for de-coupling applications, common mode suppression, etc.
Low profile
Low profile capacitors are made thinner than typical devices of comparable length and width in order to facilitate use in applications with strong height constraints. Devices with thickness measurements as small as 0.006” (0.15 mm) are available. It should be noted that the reduced thickness of these devices renders them more vulnerable to cracking from board flexure, making careful design, assembly, and handling procedures doubly important in light of the fact that applications calling for the extra millimeter or two of height reduction offered by these devices are also likely to use thinner (and thus more flexible) circuit substrates.
Military
Product designated as “military” and procured under the U.S. military’s standardized part numbering scheme are produced to specifications established by the military, in the interest of securing product consistency across multiple sources of supply. Traditional “mil-spec” standards spelled out not only the what, but the how of production, in an effort to assure uniformity and interchangeability of product from different suppliers. Newer MIL-PRF standards are performance-based, and specify how a product must perform, while leaving the precise methods of achieving the objective largely up to the manufacturer. The flexibility offered by the latter approach allows greater leeway for adopting new technologies and manufacturing processes at a somewhat increased risk of product behavior variation between manufacturers and over time. In either case, “true” military product procured to military Specifications tends to be rather costly due to the extensive testing and documentation requirements involved. As a middle ground, products produced to military specification but marketed as standard commercial products are available, though without the extensive documentation.
Non-magnetic
Non-magnetic capacitors are made with materials that are neither attracted nor adversely affected by magnets, and do not influence a magnetic field in which they are placed. They are often screened post manufacture to assure that the end product retains these properties. Such products are used in medical imaging and diagnostic equipment, navigation systems, laboratory equipment, and other applications where it would be undesirable for a device to be influenced by magnetic fields or retain fields that would influence operation of the application circuit or other equipment.
Open mode
MLCCs marketed as “open mode” devices are designed to decrease the risk of short-circuit or low-impedance failure modes that can occur as a result of mechanical cracking. A common approach used to achieve this objective is to reduce the area of overlap between the two sets of electrodes such that the typical path of board stress cracks does not travel through the area where the electrodes overlap. So doing reduces the active area available within the capacitor, and as a consequence the maximum capacitance values achievable in a given package size are reduced. This approach can be combined with floating-electrode and soft termination technologies to further reduce the risks associated with crack-induced MLCC failures. While open-mode MLCCs greatly reduce the risk of short-circuit failures, it should be noted that the probability of such failures is still not zero. If the probability of short-circuit failure must be reduced further still, the use of two series-connected devices oriented at 90° relative to each other has been suggested in industry literature.
Soft/flexible termination
MLCCs marketed as having soft or flexible terminations are designed to provide a bond between the metal end terminal and ceramic capacitor body that is more mechanically compliant than that found in standard MLCCs. This reduces the risk of cracking by reducing the amount of stress applied to the ceramic material as a result of board flexure or temperature cycling.
What are electric double layer capacitors?
Electric double layer and supercaps:
Device construction and distinguishing traits:
Electric double layer capacitors (ELDCs) and supercapacitors are a group of electrolytic-like devices characterized by extremely high capacitance per volume and low voltage ratings, typically no more than a few volts. Construction types and operating principles among these devices differ and are topics of ongoing R&D efforts, but common themes found among them are the use of electrode materials that offer extremely high surface area per volume (such as activated carbon, aerogels, etc.) and an absence of a conventional solid dielectric. In place of conventional ceramic, polymer, or metal oxide dielectrics as found in other capacitor types, ELDCs, supercapacitors, and similar devices by other names rely on various electrochemical, electrostatic, and charge transfer effects that provide extremely small charge separation distances; the distance by which the “plates” of the capacitor are separated is commonly measured in fractions of a nanometer. For practical purposes, ELDCs, supercaps, and similar devices of a different name can be regarded as a sort of middle ground between traditional capacitors and secondary (rechargeable) cells. They have energy storage densities that are higher than traditional capacitors but lower than electrochemical cells, ESR values that are high by capacitor standards, but low by electrochemical cell standards, and a nearly indefinite cycle life compared to chemical cells’ cycle lives of only a few hundred to a few thousand cycles. As with electrochemical cells, several ELDCs can be integrated into a single package to yield a composite device with a higher nominal voltage. The combination of high ESR and poor linearity characteristics relative to other capacitor types renders ELDCs and supercaps unsuitable for most signal and high frequency (>kHz) applications, but they are quite useful for energy storage on human-scale time frames. Within this realm, there is a continuum of devices intended for different applications. Smaller devices may have ESR values as high as a few hundred ohms, and are intended for applications such as memory and real-time clock backup supplies with uA-level current requirements. At the other end are devices with fractional-milliohm ESRs, intended for use in applications with currents into the hundreds of amps such as regenerative braking systems for vehicles.
Range of available capacitances and voltages:
Figure 12 illustrates the voltage and capacitance ratings of ELDCs and supercapacitors in stock at DigiKey at the time of writing. Note that the vertical scale has units of Farads, in contrast to units of microfarads found in similar charts.
Figure 12: Plot of capacitance values vs. voltage ratings for ELDC/supercapacitors and arrays thereof available through DigiKey at the time of writing.
Common failure mechanisms/critical design considerations:
Variations in technology among devices under the ELDC/supercap umbrella preclude detailed discussion of failure mechanisms and critical design considerations for the group as a whole. From an applications perspective however, it is sufficient to note that the concerns applicable to aluminum electrolytic capacitors transfer more or less directly to ELDCs and supercaps:
- They contain a liquid electrolyte solution that is subject to evaporation, and the Arrhenius rule of thumb predicting a halving of device longevity for each 10°C temperature increase holds. It should be noted that temperature ratings for many ELDCs/supercaps are relatively low and that self-heating effects can become significant in applications involving prolonged charge cycling. Also, many board mounted devices will not tolerate reflow soldering processes, and may require special care during assembly as a result.
- They should not be operated above their rated voltage. So doing will cause failure through electrolyte loss and/or dielectric breakdown. This is particularly pertinent in the case of devices incorporating organic electrolytes, since materials released during a failure can prove to be quite toxic.
- They exhibit significant dielectric absorption and changes in device characteristics as a function of temperature. Additionally, leakage current is often quite high in ELDCs/supercaps, particularly in compound devices composed of series-connected capacitors. Frequently, such devices require some form of circuitry to balance the voltage applied to each in order to avoid an overvoltage condition on any given cell caused by capacity or leakage current imbalances.
- Capacitors exhibit a linear relationship between state of charge and output voltage per the Q=C*V equation. This differs from electrochemical cells which generally have a broad, more or less flat plateau in output voltage as a function of their state of charge. In many/most applications, this means that some form of power management circuitry will be needed to make full use of an ELDC/ supercap’s full capacity.
What are film capacitors?
Figure 13: Examples of film capacitors in a variety of package styles and lead configurations. (Not to scale)
Device construction
Devices in the Film Capacitors category are electrostatic in nature, and made using dielectric materials such as paper or various polymers that are formed into thin sheets or “films” and interleaved with electrode materials to form a capacitor. The term “film capacitor” generically refers to any device made using this sort of process, and the term “film” is in reference to the nature of the dielectric material used. When the term “metal” is used as a qualifier for “film” as in “metal film” or “metallized film”, it’s a more specific reference to a film capacitor sub-type in which the electrodes are built up on a supporting substrate in a very thin (10’s of nanometers) layer, usually through a vacuum deposition process. The substrate used frequently also serves as the dielectric material for the capacitor, though this is not always the case. In contrast, a “foil” electrode capacitor uses an electrode material more akin to household aluminum foil, which is thick enough (on the order of micrometers) to be mechanically self-supporting.
Figure 14: Illustration of the distinction between metal film and foil electrode styles in film capacitors.
Film capacitors based on metal film electrodes have the advantage of being able to self-heal; the electrode material near a localized fault in the dielectric is thin enough to be vaporized by the leakage current caused by the fault, thus eliminating (or “clearing”) it at a cost of some lost capacitance. This ability to self-heal permits the use of thinner dielectrics than would otherwise be feasible due to reliability or production yield concerns, and results in a high capacitance per volume. The advantage of foil electrode capacitors is that the thicker electrodes result in lower ESR, allowing better RMS and pulsed current handling abilities at the expense of self-healing capability and a reduction in achievable capacitance per volume. Numerous clever combinations of and tweaks to the basic film and foil electrode types are in common use. For example, foil and film electrodes are often combined in a single device, using a “floating electrode” configuration, which (like similarly-designated ceramic capacitors) is effectively two or more capacitors connected in series. By making the “outer” electrodes a foil type and the “floating” electrodes a film type, one can realize a capacitor with good current handling capabilities, self-healing ability, and improved capacitance per volume. Another technique frequently employed is the use of patterned film electrodes. By partitioning an electrode into a number of interconnected segments, the interconnects can be made to act as fuses that limit the amount of current available to a fault site during a self-healing event, allowing the risk of cascading or short-circuit failures to be reduced.
Common usages and applications:
Film capacitors of some form are the dominant capacitor technology in power applications involving reversal of voltage applied to the device. Metallized film types are well-suited to safety-rated applications due to their self-healing characteristics and ability to fail open under many fault conditions. Metal foil types are often used in applications where higher ripple current amplitudes are expected, such as in starting/ running AC motors or providing capacitive reactance for bulk power distribution. Additionally, film capacitors are often used in low-voltage signal applications where relatively high capacitance values as well as linearity and stability over temperature are required, such as in analog audio processing equipment. In applications such as DC bus filtering where the polarity across the device is not reversed, film capacitors may be an alternative to aluminum electrolytic types (or vice-versa). When comparing film capacitors with aluminum electrolytic types of similar voltage and capacitance ratings, film capacitors tend to be larger and more costly by roughly a factor of 10, but have ESR values that are lower by a factor of roughly 100. Film capacitors’ lack of a liquid electrolyte eliminates the problem of dry-out and increase in ESR at low temperatures encountered with aluminum electrolytic devices, and they do not suffer dielectric degradation during extended periods of disuse in the way that aluminum electrolytic devices do. Additionally, the lower ESR characteristic of film capacitors may permit use of a smaller capacitance value than would be required with an electrolytic device in some applications, offsetting the cost disadvantage of film technology relative to electrolytic types.
Common failure mechanisms/critical design considerations:
Though film capacitors are generally quite durable, they are susceptible to a few long-term wear mechanisms. Over time, the dielectric materials used weaken, become brittle, and experience degradation in their voltage withstanding capability, which eventually leads to a dielectric breakdown failure. The process is accelerated by temperature and voltage stress, and reducing either can extend service life. Depending on the severity of the dielectric breakdown event, the failure modes exhibited can range from relatively benign to quite spectacular. A mild breakdown event that is arrested either by a film capacitor’s self-healing properties will manifest as an incremental reduction in capacitance. As more such events occur over time, the cumulative effect causes a reduction in capacitance and increased ESR, until the point where the device’s performance is no longer within specification and it is considered to have failed parametrically. In a more extreme case, which can follow a parametric failure if parametrically-failed devices are not removed from service, a cascading failure can occur when the thermal energy released during self-healing prompts additional dielectric breakdowns nearby. Because self-healing events remove portions of the capacitor from the circuit, application stresses are re-distributed across an ever-shrinking portion of the device as self-healing progresses, causing an increase in stresses placed on the portions of the device that remain effectively in-circuit. The next weakest portion of the capacitor then fails, dumping its burden on what’s left, prompting more breakdown events, more stress concentration, more breakdown events, etc. in an exponential fashion. If this process occurs rapidly enough, the gaseous byproducts from the self-healing process can build sufficient pressure to violently rupture the device’s case. Larger devices often include a venting mechanism to limit/prevent collateral damage from flying debris when this happens, and may also include a fusing mechanism to remove the device from the circuit in the event of an internal overpressure condition. Note that parametric failures due to repeated self-healing can simply be a waypoint on the route to a more catastrophic, explosive failure if devices that have failed parametrically are left in operation. Another overstress failure mode found in film capacitors occurs when peak current limits are exceeded, due to a fuse-like action at the region where the “plates” of the capacitor join to the external leads. This is particularly common with the metallized film types due to their very small electrode thickness and the resulting delicacy of their connection to the outside world. Many film type capacitors will specify a maximum rate of voltage change (dV/dt) that is to be applied across the capacitor. This is tantamount to specifying a peak current through the device since I(t)=C*dV/dt, though voltages are typically more convenient to measure than currents. Environmental conditions also play a role in the longevity of film capacitors. As with other devices, elevated temperatures reduce device lifetime considerably. More unique to film devices is a vulnerability to moisture; prolonged exposure to high humidity environments or post assembly wash cycles can cause the ingress of moisture into a device through imperfections in the epoxy-to-metal seals around the device leads, or by diffusion through a device’s polymer case. Moisture ingress is bad on several fronts; it both degrades the dielectric material, and promotes corrosion of the electrode materials. Particularly in metal-film type devices where the electrodes are only a few dozen nanometers thick to start with, it takes very little corrosion to cause problems. Additionally, high-vibration environments can also be troublesome by causing mechanical failure of device leads, attachment between leads and electrodes, or by exacerbating moisture ingress problems. The dominant factors in film capacitor reliability and longevity are applied voltage, followed by temperature. Suppliers’ service life models vary, but generally are based on taking the ratio of rated and applied voltage to a large exponent (usually between 5 and 10), while the influence of temperature follows the Arrhenius relationship of a factor of 2 change with each 10°C temperature increment. Between the two effects, de-rating voltage by 30% and temperature by 20°C adds nearly two decimal places to service life estimates.
Dielectric types, features, and targeted applications:
Acrylic:
Acrylate materials are relatively new as a dielectric material for film capacitors. Currently available devices are often marketed as reflow-compatible film alternatives to ceramic dielectrics that avoid piezoelectric effects and loss of capacitance with DC bias, or as lower ESR tantalum alternatives.
Paper:
Kraft paper was one of the earliest dielectric materials used for film capacitors due to its low cost and availability prior to the development of modern polymers. Commonly impregnated with wax, various oils, or epoxy to fill voids and inhibit moisture absorption, its low dielectric strength and high moisture absorbency has caused paper to largely fall out of favor as a dielectric material, though it still finds limited use in applications that are extremely cost sensitive or where alterations to legacy Specifications are extremely difficult to realize. Due to the relative ease with which metal films can be applied to paper versus polymer materials, paper is occasionally used not as a dielectric material per se, but as a mechanical carrier of metallized electrode material, with a non-metallized polymer such as polypropylene serving as the actual dielectric.
Polyester/polyethylene terephthalate (PET):
Polyester, also known as Polyethylene Terephthalate or PET, is one of the most commonly used dielectric materials in film capacitors, alongside polypropylene. Relative to polypropylene, polyester generally has a higher dielectric constant, lower dielectric strength, higher temperature tolerance, and higher dielectric losses. In a nutshell, polyester dielectrics are good for film cap applications that value quantity of capacitance over quality, and which do not call for a surface mountable form factor. Certain formulations of polyester designed for high-temperature tolerance exist that facilitate the use of polyester film capacitors in surface mount packaging, though these devices are relatively few in number.
Polyethylene naphthalate (PEN):
Polyethylene naphthalate (PEN) is a polymer dielectric material designed to tolerate higher temperatures, permitting the use of film capacitor technology in surface mountable, reflow-compatible packaging. In application concept, it can be thought of as a reflow-compatible version of polyethylene (PET), delivering quantity of capacitance over quality. In exchange for gaining reflow soldering compatibility, PEN gives up a bit of specific capacitance (capacitance per volume), has higher dielectric absorption, and is more prone to moisture absorption issues, although dissipation factor at low frequency may be slightly improved relative to polyethylene.
Polypropylene (PP):
Polypropylene exhibits the lowest dielectric losses, lowest dielectric constant, and lowest maximum working temperatures of the commonly used film capacitor dielectrics. It also exhibits one of the highest dielectric strengths among these polymers, as well as good parameter stability over temperature. Overall, polypropylene is a dielectric of choice for film cap applications calling for quality of capacitance over quantity thereof. Due to its low temperature tolerance, polypropylene dielectrics aren’t compatible with reflow soldering processes, and are therefore found almost exclusively in through-hole or chassis-mount packaging of some form. Due to its superior loss characteristics, polypropylene film capacitors are a device of choice in high-current, high-frequency applications such as induction heating and thyristor commutation, as well as applications where a stable, linear capacitance is desired and other capacitor types are unavailable or unfeasible for some reason.
Polyphenylene sulfide (PPS):
Polyphenylene Sulfide (PPS) dielectrics can be regarded as a reflow compatible alternative to polypropylene for applications where quality of capacitance is more important than quantity. Relative to polypropylene, PPS capacitors exhibit a higher specific capacitance and dissipation factor over the range of applicable frequencies by a factor of roughly 2 to 3, though stability of capacitance over the temperature range is slightly improved.
Other dielectrics
A number of film capacitor dielectric materials have either come and gone with time, or lingered in obscurity. While not readily available or advisable for use in new applications, mention is made here for reference and comparison.
Polycarbonate
Polycarbonate is a rigid, transparent thermoplastic often used to make lenses for safety glasses, helmet visors, or other impact-resistant optics. Its manufacture for use as a dielectric film was discontinued around the year 2000, and remaining material stocks for capacitor applications have largely been consumed. As a dielectric material it was quite good, with electrical properties similar though slightly inferior to polypropylene in most cases, although with superior temperature characteristics that permitted use over the military (-55°C to +125°C) temperature range with relatively stable parameters and frequently without de-rating at elevated temperatures. Polyphenylene sulfide (PPS) is commonly cited as an available alternative that is likely to be suitable for applications previously using polycarbonate-based devices.
Polyimide
Polyimide is a high-temperature polymer often sold under the trade name Kapton, and which finds use in many electronics applications as a substrate for flexible circuits. As a dielectric for capacitor applications it offers moderate performance comparable with polyester/PET, though its high temperature stability enables operation at elevated temperatures in excess of 200°C. While its high dielectric strength suggests potential for devices with good volumetric density, difficulties in producing the stuff as a very thin film have tended to limit appeal/availability of capacitors based on this dielectric material.
Polystyrene
Polystyrene film capacitors are largely an extinct species at this point, having fallen out of favor primarily because of the assembly and manufacturing difficulties associated with a very low temperature tolerance of only 85°C. At modest operating temperatures the electrical performance of polystyrene capacitors is quite good, and for a time such devices were a go-to choice when stability and electrical performance characteristics were the driving selection criteria. For the most part, these devices have been supplanted by polypropylene film capacitors.
Polysulfone
Polysulfone is a rigid, transparent thermoplastic similar to polycarbonates both electrically and in terms of being high-cost and relatively unavailable.
Teflon/PTFE
“Teflon” is a DuPont Trade name which encompasses a number of fluoropolymers, principally polytetrafluoroethylene (PTFE), though fluorinated ethylene propylene (FEP) and others can be found with the “Teflon” moniker. These polymers tend to be very stable and possess many admirable qualities as precision dielectrics, including high temperature tolerance and excellent stability over time, temperature, voltage, and frequency, etc. The mechanical properties of PTFE films and difficulties in metallization thereof make production of PTFE-based film capacitors a difficult and costly affair, so few such devices are available in the market.
What are Mica/PTFE capacitors?
Figure 15: Mica capacitors in a variety of package formats. (Not to scale)
Device construction
Mica is a naturally occurring group of minerals characterized by an ability to split readily into flat, thin films, with the specific type known as “muscovite” mica being preferred for capacitor applications. As a dielectric, mica offers excellent stability over time and applied voltage, a low temperature coefficient, high temperature tolerance, very good dielectric strength, and low loss characteristics over a wide frequency range. Aside from being excellent dielectric materials, mica (a naturally occurring mineral) has almost nothing in common with PTFE (a synthetic fluoropolymer), but because there’s at least one capacitor product series on the market that uses PTFE instead of mica for some capacitance values, both materials get mention in the heading… Construction of mica capacitors varies depending on application, though similarities can be found with ceramic and film types. Whether the mica is used as monolithic sheets cleaved from a chunk of raw material, or as a “paper” made from many small flakes, an electrode/terminal attachment layer (usually silver) is deposited on two sides, and then either used singly (like a single-layer ceramic device) layered together like an MLCC, or wound like a film capacitor. Early devices produced prior to the development of metallization processes mechanically clamped sheets of mica together with electrode foils. Like other clamped capacitors, the stability and reliability of these devices was inferior to more modern types, and clamped mica capacitors have thus been obsolete at least since world war two.
Common usages and applications:
Mica capacitors are a technological contemporary of the vacuum tube, and have historically been a device of choice where a stable, high-quality capacitance was needed. Like the vacuum tube, newer technologies offering better price/performance ratios have gained dominance and relegated mica technology to niche markets where uncommon stress factors such as nuclear radiation, extreme temperatures, or high voltage stresses justify the cost of a mica device.
Figure 16: Plot of capacitance values vs. voltage ratings for Mica/PTFE capacitors available through DigiKey at the time of writing.
Common failure mechanisms/critical design considerations:
Modern mica capacitors tend to be quite reliable by virtue of the stability of materials used in their manufacture, and for most application purposes can be treated similarly to a C0G ceramic device. Mechanically-induced failures stemming from vibration, impact, thermal cycling, etc., are all possible as with other capacitor types, and electrode corrosion due to moisture ingress is also a potential problem.
What are tantalum capacitors?
Figure 17: Tantalum capacitors in a variety of package configurations. (Not to scale)
Device construction and distinguishing traits
Tantalum capacitors are electrolytic devices primarily used where a compact, durable device with relatively stable parameters is needed, and modest capacitance and voltage ratings are sufficient. Traditionally, tantalums’ advantages over aluminum electrolytics have been found in terms of capacitance per volume, parameter stability over temperature, and longevity; tantalums in general do not suffer from dry-out problems or issues of dielectric degradation when stored discharged for long periods of time. However, tantalums are generally more costly, have a more limited range of available capacitance and voltage values, are made of rarer materials more subject to supply disruption, and may require special care in design, owing to some sub-types’ tendency to fail with great enthusiasm.
Figure 18: Plot of capacitance values vs. voltage ratings for tantalum capacitors available through DigiKey at the time of writing.
Figure 18 illustrates the combinations of voltage and current ratings for various flavors of tantalum capacitors available from DigiKey at the time of writing. Regardless of the sub-type, the anode construction of tantalum capacitors is quite similar; finely powdered tantalum metal of high purity is molded into the desired shape, and sintered at high temperature to fuse the individual metal powder grains into a highly porous mass known as a “slug” with extremely high internal surface area for its volume. The capacitor’s dielectric is then formed electrochemically in a liquid bath, creating a tantalum pentoxide (Ta2O5) layer over the whole internal surface area of the slug, much in the same way that the dielectric of aluminum electrolytic capacitors is formed. From this point the construction of the different tantalum sub-types diverges, with the different cathode systems employed giving rise to the different types’ characteristics.
Ta/MnO2 caps
There are three basic cathode systems in use that give rise to the different sub-types of tantalum capacitor; manganese dioxide (MnO2), conductive polymer, and “wet”. With the manganese dioxide system, after dielectric formation the tantalum slugs are dipped in a series of manganese nitrate (Mn(NO3)2) solutions and baked after each dip, converting the liquid solution into solid (semi) conductive manganese dioxide that thoroughly permeates the microstructure of the tantalum slug and serves as the device’s cathode. A layer of interface material such as graphite is then applied to keep the MnO2 from reacting with the metal layer (commonly silver) needed in order to have something to attach a lead to, before the whole assembly is packaged in epoxy and tested prior to shipment. The end product is a solid-state electrolytic capacitor with high specific capacitance, no dry out problems, good reliability, relatively good stability over temperature, and a rather nasty failure mode… Because the composition and construction of a tantalum-MnO2 capacitor is similar to that of a firecracker (a finely divided metal in intimate mixture with a substance that releases oxygen when heated) these capacitors are well-known for failing in pyrotechnic fashion, characterized by explosions and/or violent spewings of flame. Particular care in their selection and application is recommended for this reason.
Military/high reliability/fail safe
Some practical improvements on the basic Ta/MnO2 capacitor technology have been made, and mechanisms for mitigating, or at least quantifying the risk of failure, are available. Products designated as military and procured under a MIL-spec part number are produced and tested according to the prescriptions of the referenced MIL-spec, which typically include lot testing and screening procedures to establish a statistical assurance of reliability. MIL-specs often also call for a (non RoHS compliant) lead bearing terminal finish, which benefits system reliability overall due to reduced risk of tin whisker formation and lower peak temperatures during assembly. High reliability parts are often built as MIL-spec materials with different labeling and terminal finish, but may also incorporate technological improvements not yet adopted by MIL-spec governing bodies. In any event, Hi-Rel product worthy of the name will have been screened, tested, and/or burnt-in to offer a statistical assurance of reliability. Fail-safe devices incorporate some type of fusing mechanism in order to convert short-circuit failures into open-circuit failures before they can progress into open-flame failures. These mechanisms are not perfect, but they do reduce the risk of incendiary failures by a few decimal places.
Tantalum polymer
Tantalum polymer capacitors dispense with the manganese dioxide altogether and use a conductive polymer as the cathode material instead, which pretty much eliminates the risk of pyrotechnic failures. Due to the lower resistance of the polymer materials used relative to MnO2, tantalum polymer caps generally have better ESR and ripple current specifications, as well as better performance at high frequency relative to their MnO2-based counterparts. The disadvantages of polymer cathode systems include a more limited temperature range, greater sensitivity to moisture, and a reduced efficacy of self-healing that contributes to higher leakage currents.
Wet tantalum
Wet tantalum capacitors, as the name suggests, use a liquid electrolyte in their cathode systems. Since it’s hard to solder to a liquid, a cathode counter-electrode is needed to complete the circuit through the sintered tantalum anode slug, and the design of this counter-electrode is one of the differentiators among different lines of wet tantalum devices. Modern devices use hermetically sealed/welded tantalum cases, which are less prone to electrolyte leakage and more tolerant of incidental voltage reversals than earlier devices incorporating a silver case material and elastomer seal. The chief advantages of wet tantalum devices are their reliability and relatively high specific capacitance; the liquid electrolyte provides a continuous self-healing action for the dielectric, leading to low leakage currents and a higher range of applicable operating voltages. Due to the resistance of the liquid electrolyte however, the ESR of most wet tantalums is not particularly good, resulting in loss of capacitance at relatively low frequencies. Wet tantalums are also quite costly, roughly 100x that of an aluminum electrolytic device of comparable ratings. Taken together, these factors render wet tantalums something of a niche technology, found mostly in the sort of applications where failure is not an option and money is not an object; space/satellite applications, life critical avionics systems, etc.
Failure mechanisms and design considerations
For tantalums in general
The dominant cause of dielectric faults in tantalum capacitors is impurities in the tantalum powders from which the anode slugs are formed. Like the gaps that occur when highway crews don’t bother to move roadkill out of the way when painting lines on roads, impurities in the tantalum result in flaws in the dielectric layer. Since the dielectric in a tantalum capacitor is only a few nanometers thick to start with, even very small impurities can cause problems. Other dielectric faults in tantalum capacitors are mechanically induced. Being a somewhat brittle, glass-like substance, the tantalum pentoxide dielectric is prone to fracturing when mechanical stress is applied. Particularly significant are thermal expansion stresses during soldering operations when parts are assembled onto a board. Because these stresses can cause faults that did not exist (and are therefore undetectable) at the time of production, failure of tantalum capacitors on first application of power following assembly is a known phenomenon. Because of the softer, more pliable nature of polymer cathode materials (and obviously, liquid cathodes) relative to manganese dioxide, these types have an advantage over MnO2-based capacitors in terms of infant mortality.
For MnO2-based devices
The self-healing mechanism at work in Ta/MnO2 capacitors is based on thermal decomposition of the MnO2 material into the much less conductive Mn2O3 . When the leakage current near a fault site causes the local temperature to rise high enough, the region of MnO2 cathode material supplying current to the fault breaks down, thus insulating the fault from further current flow. Unfortunately, this process generates loose oxygen: 2(MnO2) + (energy) --> Mn2O3 + O. The difference between a successful self-healing event and a pyrotechnic failure is whether or not this oxygen finds tantalum metal at a high-enough temperature to auto-ignite. Ambient temperature and the amount of electrical fault current available to cause ohmic heating at a fault site are both factors that influence the outcome.
MnO2 design considerations
While a careful study of manufacturers’ application literature is recommended, the following guidelines regarding the application of Ta/MnO2 capacitors are offered for the impatient:
- Use series resistance: limiting the external current available to a fault greatly reduces the chance of a fault site reaching the critical ignition temperature. Historically a series resistance of 1 to 3 ohms per applied volt has been recommended. Modern designs may not tolerate this much ESR, and larger devices may contain sufficient electrical energy when charged to self-ignite should a fault suddenly appear. In these cases, de-rating and device screening are particularly important.
- De-rate voltage: To (significantly) increase steady-state reliability, de-rate devices by half from rated voltage, and as much as 70% when series resistance is extremely low, on the order of 0.01 ohm per applied volt or less. If currents are externally limited, as little as 20% de-rating may suffice. A further (compounding) de-rating factor for temperature is recommended, increasing linearly from 0 @ 85°C to 33% @ 125°C, though high-temp product series may differ.
- Burn-in carefully: Many tantalum failures occur on first power up of an assembled device, as a result of assembly-induced dielectric faults. Facilitating successful self-healing through gradual application of voltage via a current-limited source may avert some of these failures. Subsequent exposure to maximum expected electrical and environmental stresses will serve as a proof test, since Ta/MnO2 capacitors that survive a given set of stresses once are likely to survive them almost indefinitely.
- Limit transient current: Current flows in excess of the manufacturer’s stated surge current limit are to be avoided, including those arising from non-routine events, such as hot-plugging of batteries or power supplies, short-circuit faults of system outputs, etc. In absence of a surge current specification, a value Imax<V/ratio/(1+ESR) has been suggested.
- Observe ripple current/temperature limits: Ripple current ratings are typically based on the amount of ripple required to produce a given rise in device temperature above ambient. Excepting cases where the resulting waveforms would violate voltage or surge current limits, ripple current limits are a thermal management issue. Evaluate the test conditions under which the datasheet ripple limit figures are specified, and adapt those limits according to actual application conditions.
For polymer and wet tantalums
When they do fail, tantalum polymer capacitors tend to become a warm resistor, rather a rapidly expanding cloud of hot gasses and shrapnel. Because of this and the reduced risk of assembly-induced defects, their application rules of thumb are a bit simpler: de-rate voltage by 20%, observe recommended ripple current limits, and follow the manufacturer’s recommended de-rating schedule at elevated temperatures. For wet tantalums, the sort of applications that can justify the cost of the parts are also likely to require a detailed reliability analysis of the system on a part-by-part basis, rendering rules of thumb less valuable than they might be in other applications. With that, a 20% standard de-rating factor is suggested, and users are advised to be mindful of the relatively low frequency response characteristics common among these devices.
What are niobium oxide capacitors?
Figure 19: A niobium oxide capacitor.
Device construction and distinguishing traits
Niobium oxide capacitors are similar in construction to tantalum and manganese dioxide (Ta/MnO2) devices, using sintered niobium oxide (NbO) in lieu of tantalum metal as the anode material. Produced chiefly by AVX as an alternative to Ta/MnO2 capacitors that doesn’t have the nasty inclination to deflagrate upon failure and also having the potential for improved raw material supply logistics, niobium oxide capacitors are in competition with tantalum polymer devices for a variety of applications. Construction of niobium oxide capacitors is similar to that of Ta/MnO2 devices; the anode material consists of a highly porous, sponge-like mass of niobium (mon)oxide (NbO) on which a dielectric layer of niobium (pent)oxide (Nb2O5) is established and around which a counter electrode of manganese dioxide is built up, in a fashion similar to the common Ta/MnO2 devices. Capacitors based on niobium metal (rather than the oxide NbO) and polymer electrolyte technologies have also been developed, but are not being produced in any significant quantity at the time of writing.
Figure 20: Plot of capacitance values vs. voltage ratings for niobium oxide capacitors available through DigiKey at the time of writing.
Why niobium?
A shortfall in tantalum supply amid high demand around the turn of the millennium resulted in tantalum capacitors being a rare and costly item for a season, causing production headaches that motivated the development of devices based on niobium. Relative to tantalum, which finds its primary use in the electronics industry, niobium is estimated to be some 20 times more abundant in nature, and is also used widely as an alloying element in steel production in quantities much larger than would conceivably be required for electronics purposes. Between there being more of the stuff to start with and the electronics industry not being the primary buyer for it, the long-term supply prospects for raw materials were thought to favor niobium over tantalum.
Application strengths and weaknesses
Niobium oxide/manganese dioxide capacitors have a significant advantage over their tantalum kin in that they generally don’t ignite when they fail catastrophically. This is attributed to a much larger amount of energy required to ignite niobium oxide compared to tantalum, as well as a secondary self-healing effect wherein the niobium oxide anode material exposed at a fault site is further oxidized to a less conductive state. Between the two effects, the behavior of niobium oxide capacitors experiencing catastrophic failures is said to be a high-impedance short circuit in the Kohm range; a value high enough to prevent the resulting fault currents from delivering enough energy to ignite the device at rated voltages. Relative to Ta/MnO2 devices, NbO/MnO2 capacitors currently are a bit behind in terms of performance, being limited to voltage ratings of 10 V or less, having leakage currents roughly double those of tantalum devices, slightly lower capacitance per volume, and higher temperature de-rating over 85°C. On the other hand, “doesn’t burst into flame” is a very nice feature to have, and the issue of better raw materials availability offers promise of lower costs. Though the tantalum polymer approach to the pyrotechnic capacitor problem seems to be gaining greater popularity, the niobium oxide technology is said to retain advantages in terms of long-term service life and environmental tolerance, particularly in high humidity applications. If for no other reason, it’s an interesting technology simply because bringing up the subject with the sales & marketing folks representing the different factions seems to elicit decidedly different perspectives and opinions...
Application considerations
The ignition-resistant character of niobium oxide capacitors permits a more aggressive application of NbO-based devices relative to their tantalum-based counterparts. Whereas the rule of thumb for designing with Ta/MnO2 capacitors is to de-rate voltage by 50% (or more if series resistance is very low), the leading manufacturer of NbO-based devices (AVX) has suggested that de-rating voltage by only 20% is sufficient for safe operation. Additional de-rating beyond these levels can improve long-term reliability of both device types significantly. Also, since the device’s internal structure and thermo-mechanical properties of the solid MnO2 electrolyte remain, users of niobium oxide capacitors are advised to be mindful of the potential for failures induced by the assembly process.
What are silicon & thin film capacitors?
Figure 21: Silicon & thin film capacitors in various package formats. (Not to scale)
Device construction and distinguishing traits
Silicon and thin film capacitors are a relatively new crop of devices produced using tools, methods, and materials borrowed from the semiconductor industry. The precise control over structure and materials that these techniques provide allows production of near-ideal capacitors with excellent parameter stability, minimal ESR & ESL, wide service temperature capabilities, and comparable to better capacitance per volume compared to the Class 1 ceramic type devices with which they most directly compete. Their main disadvantages include high cost, and, as a related matter, a relatively limited range of available capacitance values. Typically based on a silicon oxide/nitride dielectric, the distinction between “thin film” and “silicon” capacitors is something of a marketing concession, though significant differences exist within & among the two depending on the intended application. Devices targeting RF tuning & matching applications tend to be low-capacitance, single-layer devices optimized for parameter stability and consistency, and are commonly found in standard JEDEC package sizes. In contrast, devices intended for power supply decoupling, broadband DC blocking, and similar applications allow larger tolerances in favor of achieving higher specific capacitance, and are more likely to be found in packaging adapted to advanced assembly methods such as wire bonding or embedding within a PCB. Regardless of intended application however, devices in the thin film and silicon capacitor families are premium-performance products and are priced accordingly, at the time of writing fetching something on the order of 5 to 5000 times the price of ceramic devices with similar capacitance and voltage ratings. Parts designed as high-precision devices mostly compete with ceramic capacitors based on C0G (NPO) dielectrics, as a higher-performance alternative for RF and microwave applications. While these class I ceramic devices are quite good and approach idealness themselves after some decades of refinement, characteristic manufacturing differences allow thin film/silicon devices to be a little better in terms of consistency across devices and manufacturing lots. Higher-capacitance thin film/silicon capacitors compete more directly with the class II ceramics based on X7R and X8R dielectrics for de-coupling and broadband DC blocking applications. For these purposes, thin film/silicon devices can offer notable advantages, such as a significantly lower dissipation factor and much better stability of capacitance over temperature and voltage.
Figure 22: Plot of capacitance values vs. voltage ratings for silicon & thin film capacitors available through DigiKey at the time of writing.
What are trimmer and variable capacitors?
Figure 23: Trim & variable capacitors in a variety of styles and package types. (Not to scale)
Device construction and distinguishing traits
Trimmer and variable capacitors are devices that provide a capacitance which is variable within some range, the difference between the two terms being mostly one of design intent; a “trimmer” capacitor is usually intended to be adjusted only a handful of times over its service life, while a “variable” capacitor anticipates routine adjustment. Numerous different construction types are used, but with few to zero exceptions, they are of the electrostatic variety and achieve their adjustability by changing the effective surface area between the electrodes, the distance between them, or perhaps both.
Figure 24: Plot of capacitance values vs. voltage ratings for trimmer and variable capacitors available through DigiKey at the time of writing.
One common design approach resembles two small wheels on a common axle, with a semicircle (or similar shape) of electrode material plated on each. By changing the angle of rotation of the two “wheels” relative to each other, the effective capacitance between them can be varied. Beyond this, changing the shape of the electrodes on each “wheel” can produce varying relationships between rotational adjustment angle and device capacitance as needed for a given application. A variation on the approach may involve using a worm gear or similar mechanical arrangement to vary the relative rotation of the two “wheels” in order to provide a higher adjustment resolution within the device’s range of variation. Other designs include variable piston capacitors, which operate by varying the degree of overlap between concentric cylinders, and vacuum capacitors that use a screw or other mechanism to vary the mechanical relation between electrode plates in a vacuum which is maintained through the use of a flexible membrane.
Common usages and applications
Trimmer and variable capacitors are generally used for tuning & matching applications in RF circuits. Radio receivers that indicate the selected tuning frequency by sweeping a mechanical indicator past a scale (or vice-versa) typically have a mechanical linkage between the indicator and the variable capacitor(s) used in the tuning circuit. Most such receivers are of older vintage or lower cost/quality design, though modern applications may still include trimmer capacitors for finetuning or calibration purposes. Variable capacitors (the sort designed for frequent adjustment) on the other hand are something of an endangered species; the use of alternative design techniques enabled by better manufacturing tolerances and newer technologies renders the characteristically bulky, drifty, mechanically cumbersome, and expensive variable capacitor a less desirable design element than the alternatives.
Common failure mechanisms/critical design considerations
The wide variations in device construction that can be found within trimmer and variable capacitors preclude extended discussion on their specific merits and drawbacks herein. If one considers the basic principle behind an electrostatic capacitor however, a given device’s merits can often be discerned though observation; anything that affects the dielectric, electrode geometry, or electrode positioning will affect device capacitance. For example, an air-dielectric device will exhibit changes in capacitance at a given setting with changes in barometric pressure, temperature, and humidity because all of these factors affect the dielectric constant of air to a small degree. Similarly, a vacuum dielectric capacitor will be affected by leakage or loss of vacuum. From a mechanical perspective, the rigidity of the final assembly will affect capacitance stability with respect to mechanical shock or vibration, and the design of the adjustment mechanism will also influence the tendency for drift over time. Capacitor Quick Reference Guide The table on the next page provides a brief summary of different capacitor types and their relative merits, arranged approximately in terms of decreasing quantity (or increasing quality) of capacitance offered by each type.
Figure 25: Capacitor quick reference guide.
For further reading on capacitors, or if you have any questions please visit the DigiKey TechForum’s capacitor section.
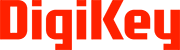
免责声明:各个作者和/或论坛参与者在本网站发表的观点、看法和意见不代表 DigiKey 的观点、看法和意见,也不代表 DigiKey 官方政策。