选择工业自动化设备时需要考虑哪些关键因素?
投稿人:DigiKey 北美编辑
2024-08-28
选择最优的电机、驱动器和通信模块等工业自动化设备需要格外注重细节。例如,北美的美国电气制造商协会 (NEMA) 和欧洲的国际电工委员会 (IEC) 在电机和驱动器额定值方面就存在许多差异。
选择电机、驱动器和控制器时,需要考虑的因素包括输入和输出电压及公差、所需的速度范围和调节需求、扭矩要求、加速度、制动占空比、快速或扭矩响应等特殊需求,以及包括热管理在内的环境因素。
通信需求因设备在工业控制层级中的位置而异。在最靠近工厂车间边缘的层级,IO-Link 等协议可用于智能传感器和执行器,EtherCAT、PROFINET、Modbus 和其他协议可连接运动、安全、I/O 和视觉系统。
工厂自动化网络的最高层级通常使用以太网/IP 与各种自动化控制器、编程接口和云端连接,并使用 DisplayPort 等协议与人机接口 (HMI) 连接。在这两者之间,以太网/IP、EtherCAT 和其他协议的组合可将工厂车间的现场层级与运营和控制层级连接。
其中的细节不胜枚举,无法一一详述。不过,本文将介绍在指定电机、驱动器和通信模块时应考虑的几个指导原则,以及 Siemens、Phoenix Contact、Omron Automation、Panasonic Industrial 和 Schneider Electric 的应用、硬件和协议示例。
关注点转移
电机和驱动器是许多工业自动化系统中的共同关注点。作为讨论的起点,了解电机能效在更广泛的工业自动化系统性能考量中的位置,以及关注点是如何转移的,将对讨论有所帮助。
使用能效更高的电机可节约多达 6% 的能源。这非常好。然而,增加一个高效驱动器和支持组件可使节能效果提高至高达 30%。
当关注点转移至整体系统优化时,游戏规则开始颠覆。考虑所有机械部件,并增加通信功能以连接包括运营和工厂层级的工业物联网 (IIoT),最终连接至企业层级和云端后,可节省多达 60% 的能源并提高生产率(图 1)。
图 1:提高集成度和通信水平可节约更多能源并提高生产率。(图片来源:Siemens)
电机系统的生态设计
IEC 61800-9 第 2 部分“电机系统的生态设计 - 能效确定和分类”是一项重要资源。该标准没有只关注电机能效,而是详细介绍了“电机驱动系统”的一系列更高层级的性能因素。VFD 可视为完整驱动模块 (CDM) 的一部分,后者包括交流输入“馈电部分”、类似 VFD 的“基本驱动模块”(BDM) 以及包括输入和输出滤波器、线路扼流圈和其他支持组件的“辅助设备”。
该标准还将电力驱动系统 (PDS) 定义为 CDM 加电机。接下来是层级,该标准将电机系统描述为 PDS 加接触器等电机控制设备。
最高层级是扩展产品或图 1 中的整体系统,其增加了变速器和装载机等机械驱动设备。有关 IEC 61800-9-2 PDS 能效标准的更多详情,请参阅文章“可调速工业电机驱动器有哪些不同类型?”
指定“电机驱动系统”的出发点是电机。
电机很重要
如果指定和使用得当,电机可以是非常高效的机器。因此,指定电机是机器设计人员的一项重要任务。
IEC 以 kW 为单位量化电机功率,而 NEMA 则使用 hp,这两者可以轻松进行换算。不过,IEC 和 NEMA 采用不同的能效计算方法,对于相同的电机设计,IEC 铭牌能效可能略高于 NEMA 额定值。
电机的实际能效与具体用例密切相关。因此,电机能效标准通常是从减少能量损耗而非绝对能效的角度来讨论。
IEC 60034-30-1 确定了五个电机能效等级,从 IE1 到 IE5。各等级之间的能量损耗下降 20%。这意味着 IE5“超超高效”电机的损耗比 IE4“超高效”电机低 20%。还有更多需要考虑的因素。在某些情况下,能效更高的电机的功率因数 (PF) 会下降。
在北美,NEMA 的能效等级更少,但同样重要。NEMA 认可 IEC 标准中未包含的电机服务系数 (SF)。SF 为 1.15 的 NEMA 电机能够以 115% 的额定功率连续运行,但电机运行温度较高,会导致轴承和绝缘材料寿命缩短。
IEC 不使用 SF,而是根据连续运行与间歇运行、速度变化及制动使用等因素,确定了十种工作制或服务系数(S1 至 S10)。
NEMA 和 IEC 的工作电压和频率范围不同,但都以“每单位”(p.u.) 量表示。在 p.u. 系统中,量值以基准值的分数表示。NEMA 认可一种电机电压和频率范围。IEC 认可两个“区”(图 2)。
图 2:NEMA 和 IEC 工业交流电压和频率范围的对比。(图片来源:NEMA)
提高 PDS 能效
根据 IEC 61800-9-2 的定义,电机驱动器是提高 PDS 能效的关键因素。这些驱动器可以从几个方面进行分类,例如电机电压、功率水平、运动类型、支持的应用等。运动类型可分为连续运动和非连续运动。根据所需的最大输出功率,它们可进一步分为低、中和高性能。
不同类型的驱动器支持不同的系统需求。伺服驱动器和电机非常适合机器人等需要快速加速、减速和精确定位的应用场合。软起动器适用于输送机等连续作业场合,这些场合可受益于平稳起动和减速。VFD 广泛应用于各种工业机器。
一些 VFD 产品系列针对泵送、通风、压缩、移动或加工等作业进行了优化。Siemens SINAMICS G120 的通用驱动器系列的额定功率范围为 0.55 至 250 kW(0.75 至 400 hp),适用于汽车、纺织和包装作业等一般工业应用。
型号 6SL32203YE340UF0 使用三相电,工作电压范围为 380 至 480 Vac +10 % / -20%。在欧洲,该型号指定用于电压为 400 V、电机额定功率为 22 至 30 kW 的作业;在北美,则指定用于电压为 480 V、电机额定功率为 30 至 40 hp 的作业(图 3)。
图 3:该 VFD 可与额定功率为 22 至 30 kW 的电机结合使用,具体取决于工作电压。(图片来源:DigiKey)
VFD 并非高效 PDS 设计的唯一关键因素。文章“需要哪些辅助产品才能最大限度地发挥 VFD 和 VSD 的作用?- 第 1 部分”介绍了一些必需的支持组件。
通信和系统优化
虽然电机和驱动器所处的工厂车间属于第 1 层级或现场层级,但它们并非处于工业 4.0 通信层级的最底层。最底层属于第 0 层级中的传感器和执行器等功能。此外,在现场层级之上还有多个层级。要最大限度提高工业 4.0 工厂的整体效率、生产率和可持续性,就必须在直至云端的通信层级中实现及时、高效的上下级通信。云端连接可通过以下协议实现(图 4):
- uOPC PubSub Bridge,该协议可整合多个运营技术 (OT) 数据流。
- MOTT BRoker,该协议可接收消息并根据消息主题将其转发给用户。
图 4:工业 4.0 通信层级的所有级别都可以直接连接到云端。(图片来源:OPC 基金会)
第 1 层级不只有驱动器和电机。现场总线主站单元 (FMU) 能促进通信,并简化驱动器与其他器件的集成。FMU 可用于各种协议,包括 PROFINET、PROFIBUS、DeviceNet、CANopen 等。使用 FMU 可实现独立于制造商的连接。
Panasonic 的型号 AFP7NPFNM 是一款 PROFINET FMU。该型号提供用于编程软件的集成功能库,能够大幅缩短开发应用特定解决方案所需的时间。
传感器、执行器和安全装置为第 0 层级
要提高 VFD 的 PDS 节能收益,就必须将连接性降低到第 0 层级。在第 0 层级集成传感器、执行器和安全装置(如光幕)可大幅提高效率,并将节能率提高到 30% 以上。
用于连接第 0 层级功能的常用协议包括 DeviceNet、HART、Modbus 和 IO-Link。IO-Link 是一种点对点协议,可将传感器和执行器连接到上一级控制装置。该协议提供有线和无线两种标准,其作为一种具有成本效益的替代方案,越来越多地部署在工业 4.0 中。
Omron 的 NX-ILM400 IO-Link 主站单元可混合使用标准 I/O 和高速同步 I/O。标准数字 I/O 每个单元有 16 个连接,可选择(图 5):
- 四个带电源的 3 线传感器连接
- 八个 2 线触点输入或执行器输出
- 十六个单线连接,用于连接到共用电源的传感器和执行器
图 5:该 IO-Link 主站单元支持标准和高速同步 I/O。(图片来源:Omron Automation)
PDS 及其他为第 2 层级
更高层级的通信不仅有助于改善现场层级的作业,更是最大限度提高组织效率和生产率的必要条件。从第 2 层级到第 3、4 层级和云端,需要使用以太网/IP、EtherCAT 和 Modbus TCP/IP 等协议。
用于实现此类连接的设备包括可编程逻辑控制器 (PLC) 或工业个人计算机 (IPC)。PLC 是专为工业自动化和控制而优化的计算机。在典型应用中,PLC 可监测来自机器和相关传感器的输入,根据其编程做出决策,然后发送控制输出。
虽然 IPC 可执行类似 PLC 的功能,但它们是更通用的设备。IPC 运行 Linux 或 Windows 等操作系统,因此可使用一系列软件工具,并且通常连接至 HMI(许多 PLC 也可连接至 HMI)。PLC 往往以机器为中心,而 IPC 则有更多操作功能。
PLC 与 IPC 之间的区别越来越模糊。例如,Phoenix Contact 的 1069208 PLC 运行 Linux 操作系统。与传统 PLC 类似,该 PCL 可使用符号化流程图 (SFC)、梯形图 (LD)、功能区块图 (FBD) 和结构化文本 (ST) 进行编程。其包括三个独立的以太网接口,可连接至 PROFICLOUD。
Schneider Electric 提供的 HMIBMIEA5DD1E01 IIoT Edge Box 适用于可受益于 IPC 的应用。其采用无风扇设计,包括一个运行频率为 1.8 GHz 的 Intel Atom Apollo Lake E3930 双核处理器。该产品有一个 mini PCIe 扩展插槽和九个通信端口(图 6)。
图 6:带 mini PCIe 扩展插槽和多种通信选项的无风扇 IPC。(图片来源:Schneider Electric)
结语
本文简要概述了设计人员在为工业 4.0 设施指定电机、驱动器和通信模块时应考虑的一些指导原则。其内容并非详尽无遗。旨在引人思考和提供一些用于进一步调查的资源。
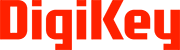
免责声明:各个作者和/或论坛参与者在本网站发表的观点、看法和意见不代表 DigiKey 的观点、看法和意见,也不代表 DigiKey 官方政策。