使用隔离技术保持数据采集的准确性并提高其性能
投稿人:DigiKey 北美编辑
2024-12-20
为了解决新出现的复杂问题,智能化在向边缘迁移,随之而来的确保数据采集 (DAQ) 的可靠性、准确性和性能就变得愈发重要。因此,要求设计人员在信号采集和系统处理器之间提供一个隔离式精密信号链。
在模拟信号精密测量链中,确保隔离能力是一项极具挑战性的任务。尽管存在信号破坏因素和不可避免的温度漂移,但要保持信号链的性能,还需要认真关注每一个细节。对于许多设计人员来说,在选择和使用适当的隔离技术之前更好地了解相关问题将大有裨益。
本文将讨论与开发、优化高端隔离式 DAQ 系统有关的各种问题,其中“高端”一词包含精度、准确性、信号完整性和一致性等属性。然后介绍 Analog Devices 的 DAQ 信号链解决方案,并说明如何使用这些解决方案来构建此类系统。
优化每个功能块
典型的 DAQ 系统由一系列功能模块组成。借助这些模块,信号可通过传感器从物理系统中传递。然后,信号进入模拟前端 (AFE) 进行调节,进入模数转换器 (ADC) 进行数字化处理,最后进入基于计算机的读出器或控制器(微控制器或者更大的系统)(图 1)。
图 1:DAQ 系统包括一条定义明确的线性信号链,其路径为从被测物理系统和传感器到主处理器。(图片来源:Bill Schweber)
要实现 DAQ 的精度和准确性,首先要选择前端的信号调节器件,特别是变送器前置放大器。低噪声性能是此项功能的众多关键因素之一,因为在设计后期很难降低内部噪声,而且会与所需信号一起被放大。信噪比 (SNR) 基准在此确定,并且当信号穿过更多级时,信噪比会不可避免地进一步降低。
因此,AFE 通常使用噪声优化型单功能运算放大器(运放)。Analog Devices 的 ADA4627-1BRZ-R7 是前端前置放大器的理想选择。这是一款 30 V(±15 V 双电源)、高速、低噪声、低偏置电流的 JFET 运放。在众多传感器优化规格中,该器件具有 200 µV(最大值)低失调电压、1 μV/°C(典型值)失调漂移、5 pA(最大值)输入偏置电流。临界电压噪声规格为 1 千赫兹 (kHz) 时 6.1 nV 每根号赫兹 (nV/√Hz)(图 2)。
图 2:ADA4627 JFET 运算放大器的电压噪声为 6.1 nV/√Hz(1 kHz)。(图片来源:Analog Devices)
隔离有许多好处
一旦信号经过放大和数字化,就会在信号与系统的数字部分和相关处理器之间建立电隔离。采取这一步骤主要有三个原因:
- 降低噪声和干扰:电隔离可消除共模电压变化、接地回路和电磁干扰 (EMI)。电隔离还能防止外部噪声源干扰已采集到的信号,确保测量结果更清晰、更准确。
- 消除接地回路:接地回路会引入电压差,使导致测量信号失真。电隔离可切断接地回路,从而消除地电位变化造成的干扰,提高测量精度。
- 安全和保护:隔离栅可防止危险的电压尖峰、瞬态电压或浪涌电压波及敏感的测量元件,以确保电气安全。这可以保护测量电路和连接设备,确保工作安全可靠。此外,如果低电平传感器即使是短暂地接触了高压线路或 AC 线路,这种屏障也能消除对用户的电气危险。
基于磁性、光学、电容甚至射频原理,有多种技术可用于隔离数字信号。Analog Devices 提供一系列高性能解决方案,包括基于其专有 iCoupler 技术的 ADUM152N1BRZ-RL7 五通道数字隔离器(图 3)。
图 3:ADuM152N 五通道数字隔离器使用专有的磁耦合技术实现高性能。(图片来源:Analog Devices)
这些隔离器结合了高速 CMOS 电路和单片空芯变压器技术。为确保性能符合高速数字链路的需求,在 5 V 电压下,最大传播延迟为 13 纳秒 (ns),脉宽失真小于 4.5 ns,通道与通道之间的传播延迟匹配严格控制在 4.0 ns(最大)。ADUM120N1BRZ-RL7 也有类似的双通道版本,因此隔离通道的总数可以与总线宽度相匹配。
这些隔离器针对高速性能进行了优化,保证数据传输速率为每秒 150 兆比特 (Mb/s)。这些隔离器具有 100 kV 每微秒 (kV/μs) 的高共模瞬态抗扰度 (CMTI) 和 3 kV 均方根 (rms) 的额定耐受电压,并符合所有相关的法规要求。
信号隔离只是整个隔离过程的一部分。DAQ 系统的所有 DC 电源轨也必须隔离。最常见的方法是将变压器作为隔离元件。
如果初级电源已经是 AC 电源,则需要通过变压器,然后进行整流和稳压;如果电源是 DC 电源,则必须首先进行斩波处理为类似 AC 的波形。使用诸如 LT3999 等器件可大大简化这一过程。这是一款低噪声、1 安培 (A)、50 kHz 至 1 兆赫 (MHz) 的 DC/DC 驱动器。
完整的高性能 DAQ 系统需要额外的核心和外围器件。其设计和布局必须确保测量准确性和数据完整性。除放大器和隔离栅外,精密信号链通常还包括滤波元件、高分辨率 ADC 和开关。这些器件的组合可消除噪声,减少干扰并实现准确的信号表示。
全部整合在一起
在使用这些关键元器件的隔离信号链中,ADSKPMB10-EV-FMCZ 便是其中之一,这是一个可实现单通道、全隔离、低延迟 DAQ 系统的精密平台(图 4)。该解决方案结合了用于信号调节的可编程增益仪表放大器 (PGIA),以适应各种传感器接口的灵敏度,并在一块紧凑的电路板内实现了数字和电源的隔离。
图 4:ADKSPMB10-EV-FMCZ 是一个可实现单通道、全隔离、低延迟 DAQ 系统的精密平台。PMOD - FMC 转接板(中心块)提供隔离和其他功能。(图片来源:Analog Devices)
用于评估时,该板被配置为一个多板解决方案,包括具有 PMOD 外形的 ADSKPMB10-EV-FMCZ (图 5)和 EVAL-SDP-CH1Z 系统演示平台 (SDP) 接口板。这两块电路板之间是一块完全隔离的 PMOD 转 FMC 转接板。
图 5:ADSKPMB10-EV-FMCZ(左)通过 PMOD 转 FMC 转接板(右)连接 SDP 接口板(未显示)。转接板上的垂直分割区显示了隔离栅的实施位置。(图片来源:Analog Devices)
ADSKPMB10-EV-FMCZ 采用 ADA4627-1 运算放大器构建的分立式 PGIA。PGIA 具有高输入阻抗,这是支持与各种传感器直接连接所必须的。该模块还具有一个用于增益设置的精密型四重匹配排阻、一个四通道多路复用器和一个用于 ADAQ4003 的全差分放大器 ADC 驱动器。ADAQ4003 是一款以 μModule 形式实现的 18 位、2 兆样本每秒 (MSPS) 的 ADC 和 DAQ 子系统。
该模块不仅仅是一个高分辨率 ADC。ADAQ4003 采用多种降噪技术,以实现高保真信号捕捉。例如,在 ADC 驱动器输出和 μModule 内部的 ADC 输入之间放置了一个单极低通电阻电容 (RC) 滤波器,以消除高频噪声并减少来自内部 ADC 输入的电荷“反冲”。
此外,μModule 的布局确保了模拟和数字路径的分离,从而避免了交叉并最大限度地减少了辐射噪声。
完全隔离的 PMOD 至 FMC 转接板包括 LT3999 DC/DC 驱动器、五通道和双通道数字隔离器、低噪声低压差稳压器 (LDO) 和超低噪声 LDO。转接板起桥接作用,与 SDP 接口板相连。
SDP 接口板执行采集后处理、管理和连接功能。该电路板有一个 160 针 FMC 连接器、一个 12 VDC 电源(可进一步调节并为其他电路板分区)、一个 Blackfin 处理器(具有用于代码和内容保护的硬件安全功能)、一个 USB 端口和一个 Spartan-6 FPGA。
性能即证明
评估精密数据采集系统的性能并非易事,因为仪表、测试布局和标准都非常关键。虽然许多动态参数与 DAQ 系统的性能有关,但最能说明问题的是动态范围、信噪比 (SNR) 和总谐波失真 (THD)。
动态范围是指设备的本底噪声与其指定的最大输出电平之间的范围。
该设计的典型动态范围令人印象深刻,在最高增益设置下为 93 分贝 (dB),最低增益设置下为 100 dB(图 6)。将超采样率提高 1024 倍后,测量结果得到进一步改善,最高分别达到 123 dB 和 130 dB。
图 6:根据增益和其他设置,整个电路和信号链的动态范围约为 100 dB,表明这是一个高性能 DAQ 系统。(图片来源:Analog Devices)
SNR 是均方根信号幅值与所有其他频谱成分(不包括谐波和 DC)的均方根 (RSS) 平均值之比。总谐波失真 (THD) 是基波信号均方根值与其谐波 RSS 平均值之比。
这种设计的信噪比和总谐波失真 (THD) 显然具有很高的性能,因为信号链的最大信噪比达到 98 dB(图 7(左)),总谐波失真达到 -118 dB(图 7(右)),具体取决于增益设置。
图 7:除了动态范围之外,高 SNR(左)和低 THD(右)也是以模拟为重点的 DAQ 性能卓越的具体证明。
结束语
设计和实施隔离式精密信号链,以保持精度,最大限度地减少噪声和干扰,并确保数据完整性,是一项重要的设计和实施工作。幸运的是,通过合理地使用精密放大、隔离技术、高分辨率模数转换器和模块以及低噪声电源管理,即使在具有电气挑战性的环境中也能实现精确测量。通过使用 Analog Devices 的先进器件(从基本运算放大器到高级隔离器件),并辅以必要的外设功能以及详尽的数据表和应用指南,这一切都成为可能。
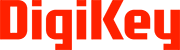
免责声明:各个作者和/或论坛参与者在本网站发表的观点、看法和意见不代表 DigiKey 的观点、看法和意见,也不代表 DigiKey 官方政策。