使用全面的 PLC 参考设计加快工业物联网应用的开发
投稿人:DigiKey 北美编辑
2019-02-07
工业物联网 (IIoT) 应用有望提高复杂工业系统的效率。由于能够实现这些 IIoT 应用的是下一代基于微控制器的可编程逻辑控制器 (PLC),因此对开发人员提出了挑战,既要支持这些系统中所需的各种工业接口,还要使器件足够紧凑以便能适合工厂设备。
这些挑战已经成为创建更高级 IIoT 应用这一终极目标的重大障碍。不过,采用模块化方法来定制 PLC IO 可能是开发人员需要的解决方案。
本文首先会讨论 IIoT 高级 IO 设计所面临的挑战,然后介绍 Maxim Integrated 的模块化系统解决方案,最后说明该解决方案作为现成方案或作为现代定制 IIoT 应用的参考设计时如何使用。
PLC 在 IIoT 中的角色演变
作为工厂自动化系统中的中间设备,PLC 多年来一直提供将传感器、致动器和其他设备连至主机系统所需的多个接口。在服务于 IIoT 应用时,PLC 系统不但需要支持更多数量的终端器件和本地处理能力,同时还要足够小巧,以便可以安装在单个机件上,或者位于工作单元或子装配线中不显眼的位置。这样会造成开发人员深陷于设计细节的泥沼中,为工业环境中所需的许多接口考虑解决方案。
在许多情况下,这不能有效利用开发人员的时间,如果将这些时间用在为智能工厂、自适应制造、预测性维护以及其他基于人工智能方法的新兴功能方面提供高水平解决方案的话,则会取得更佳效果。对传感器和致动器采用灵活的模块化接口方法,可以缩短开发时间,不过,这种接口解决方案必须足够坚固耐用,以便可以承受恶劣的工业环境。
工业接口
典型的工业环境需要各种接口,以满足外设和主机系统之间数字及模拟信号的通讯需求,其中,IO-Link 行业标准已经成为连接兼容的终端器件,以及传统传感器和致动器的有效方法。
在标准点对点 IO-Link 连接中,开发人员可以使用 PLC 中的 IO-Link 主站,通过端接有标准 M12 连接器的低成本 3 线或 4 线非屏蔽式电缆连接到 IO-Link 收发器。凭借其电气接口和功能协议,IO-Link 即使在恶劣的存在电噪的工业环境中也能确保可靠通信。IO-Link 主器件(如 Maxim Integrated MAX14819)解决了 IO-Link 电气接口及协议的实施复杂性。对于电气接口,MAX14819 集成了生成 L+ 和 L- 稳压电源,以及 IO-Link 标准要求的 C/Q 数据信号所需的电路。对于通信协议,该器件集成了 IO-Link 通信方法的基础构件,如 IO-Link 成帧器、UART 和 FIFO(请参阅“使用 IO-Link 收发器来降低功耗、提升性能和简化开发”)。
要将传感器或致动器连至 PLC 中的 IO-Link 主站,开发人员可以轻而易举地找到兼容的 IO-Link 器件,也可以使用 Maxim MAX14827A 收发器轻松构建自己的器件(图 1)。
3
图 1:通过将外围传感器中的 Maxim Integrated MAX14827A IO-Link 收发器与 PLC 或其他主机系统中的 Maxim MAX14819 IO-Link 主站配对,开发人员可以快速实现 IO-Link 点对点通信链接。(图片来源:Maxim Integrated)
尽管 IO-Link 已在较新的工业环境中得到广泛采用,但传统及较新环境中的应用仍然可以发现其他标准接口的身影。其中,RS-485 仍然是最广泛使用的串行接口标准之一,该接口是一种标准电气接口,是 RS-232 或 RS-422 等早期串行接口的替代品,具有更加坚固耐用的特点,设计用于通过一根 24 AWG 双绞线进行双向通信,RS-485 具有共模性能特点,这使其在满足延长电缆仍能可靠运行要求方面发挥了核心作用,即使在嘈杂的环境中也是如此。因此,这种接口为许多工厂网络奠定了基础,例如在 Profibus 和现场总线中充当物理层 (PHY)。
与 IO-Link 一样,工程师可以轻松找到旨在简化实现 RS-485 通信的集成器件。Maxim Integrated MAXM22511 RS-485 收发器专为工业应用而打造,不仅简化了该接口的实现,而且能在恶劣环境中保护其完整性。使用该器件,开发人员只需将 MAXM22511 的电缆侧连至双绞线,将 UART 侧连至微控制器或其他数字设备,即可实现电位隔离的 RS-485 接口,且无需额外元件(图 2)。集成在该器件内的高压电容器可以隔离数据通道,内置在器件 DC-DC 稳压器中的变压器可通过片上低压差 (LDO) 稳压器为电缆侧提供隔离电源。
3
图 2:Maxim Integrated MAXM22511 收发器简化了工业 RS-485 接口的实现,同时配备内置隔离保护,可防止电缆侧发生电气事件。(图片来源:Maxim Integrated)
实际上,典型的工业自动化系统可能需要支持 IO-Link 和 RS-485 接口以外的接口。在输入侧,这些系统通常需要支持符合 IEC 61131-2 标准及其所有三种输入类型的数字输入设备:第一类是较早的带机械开关触头的 3 线式传感器,第二类是更早的带半导体接口的 2 线式传感器,第三类是最近的 2 线或 3 线式低功耗传感器。
对于本电路而言,开发人员可以使用 Maxim MAX22192,该器件配有 8 个符合 IEC 61131-2 标准的输入通道,只需添加电流设定电阻器即可将各通道配置为 1 类、2 类或 3 类输入。
在输出侧,许多此类系统都依赖于数控驱动器,这些驱动器能够支持精确控制致动器或其他设备所需的高速切换。本图中,工程师可以使用诸如 Maxim Integrated MAX14912 等器件,此器件具有 8 个通道,可将这些通道配置为高压侧开关或驱动器。
对于直接控制直流电机等更专业的输出要求,开发人员可以选择 Maxim MAX14870,这款器件可提供完全集成的电机控制解决方案,旨在减少零件数量,降低设计复杂性。为响应脉冲宽度调制 (PWM) 信号和方向 (DIR) 控制信号,该器件的集成驱动器可在最高 36 伏电压条件下,直接驱动有刷直流电机和继电器,并且添加的元件最少(图 3)。设计人员可将 MAX14870 的输出功能与 Maxim MAX14890E 编码器接收器相结合,以实现精密运动控制子系统。
3
图 3:Maxim Integrated MAX14870 集成了驱动器和开关,可使开发人员能够在几乎不添加元件的情况下,即可实现 PWM 控制的电机子系统。(图片来源:Maxim Integrated)
下一代 PLC 设计
由于市场上拥有种类繁多的专用 IC,因此许多与实现工业系统所需的各种接口相关的低级设计挑战得到了缓解。即便如此,因需要接口的设备数量众多,并且每一种设备的设计要求各不相同,因此仍然需要工程师来应对挑战,即:在尽可能最小的设计空间内将多个接口设备与一个微控制器相结合。对于希望为高级 IIoT 应用奠定基础的开发人员,Maxim Integrated MAXREFDES212 Go-IO PLC 系统可以帮助他们消除这一障碍。
Maxim Integrated MAXREFDES212 Go-IO PLC 系统是一个模块化系统,由多块小电路板组成,每块电路板的设计均可满足下一代 PLC 的一系列要求。设计人员可将应用处理器板 (MAXREFDES211)、IO-Link 工厂自动化板 (MAXREFDES200) 和运动控制板 (MAXREFDES201) 插入基板 (MAXREFDES215),该基板配有 IO 端子块以及与 IO-Link 相兼容的独立 M12 连接器(图 4)。(请注意,Maxim 为四种板提供了指示性 MAXREFDESxxx 名称,不过,这些板仅作为 MAXREFDES212 Go-IO PLC 系统的部件提供。)插到一起后,Go-IO 系统内所含的这些板即可形成一个尺寸小于 3 平方英寸的基于微控制器的紧凑型 PLC,同时提供 20 多个 IO,可支持各种接口,其中包括 IO-Link、RS-485、符合 IEC 61131-2 标准的数字输入、数字输出和电机控制。开发人员随即可使用 Go-IO PLC 来补充现有工业系统,或将其用作自定义 PLC 的参考设计。
3
图 4:借助 Maxim Integrated GO-IO PLC 模块化设计,开发人员能够通过将单块板(包括基于 Arm 微控制器的应用处理器板 MAXREFDES211、工厂自动化板 MAXREFDES200 和运动控制板 MAXREFDES201)插入基板 MAXREFDES215 来配置 PLC。(图片来源:Maxim Integrated)
除了充当 PLC 的物理框架外,载板还可为扩展板提供稳定电压,该电压可源自标准 24 伏壁式适配器,也可来自与载板上螺纹端子相连的独立高电流电源。此电路板设计结合了 Maxim MAX17681 DC-DC 转换器、电感器以及 MAX17608 电流保护 IC,可为其他电路板提供隔离电源(图 5)。其他 MAX17608 器件可为各电路板上可用的其他 24 伏电源提供保护。
3
图 5:Maxim Go-IO 载板可为这种模块化 PLC 设计方法中的其他电路板提供连接器和电源。(图片来源:Maxim Integrated)
应用处理器板设计用于插入载板底座,包括一个 Maxim MAX32630 微控制器,并且支持开发和执行组装 PLC 的代码(图 6)。基于带有 FPU CPU 的 Arm® Cortex®-M4,MAX32630 微控制器具有新兴 IIoT PLC 所需的低功耗、安全性以及处理器性能。该应用处理器板从载板取电,并且使用 MAX17502 DC-DC 转换器将 24 伏电源降至 3.3 伏,以便为两个 MAX1806 线性稳压器供电,从而为 MAX32630 提供所需的 1.8 伏和 1.2 伏电源。
3
图 6:Maxim Go-IO 应用处理器板可承载能够协调扩展板功能的 Maxim MAX32630 微控制器,并且通过共享的 SPI 总线和 80 路连接器进行通信,这种连接器用于连接此模块化系统中使用的各种电路板。(图片来源:Maxim Integrated)
除了用于连接开发系统的 USB 连接器外,该板还支持单线、I2C、UART 和 SPI 连接。实际上,这款应用处理器板配有多条 SPI 总线,可用于整个模块化 Go-IO 系统。其中两条 SPI 总线(APP_SP1 和 APP_SP2)与 80 路连接器相连,供其他插件板使用。如下所述,APP_SP2 在系统保护方面起着至关重要的作用。
截至撰写本文时,还有两条 SPI 总线尚未使用:SD_SPI 总线保留用于连接 SD 卡,WIFI_SPI 总线保留用于 Wi-Fi 模块。尽管目前尚不支持,但设计硬件规范仍包括一个 Microchip Technology ATWINC1510-MR210PB1952 Wi-Fi 模块,此模块配有完整的 Wi-Fi 子系统,包括功率放大器 (PA)、低噪声放大器 (LNA)、开关和印制线天线。
虽然该应用处理器板仅在受控的数字域内工作,但工业接口始终容易受到电缆短路或静电放电带来的突然高压的影响。无论哪种原因引起的高压,都会降低或破坏设计用于在窄电压轨内运行的数字电子器件。如前所述,诸如 Maxim Integrated MAXM22511 RS-485 收发器 IC 等接口器件内置隔离功能,可以保护其数字电路免受电缆副作用的影响。然而在电路板级别,工程师需要在总体设计中构建隔离功能。Go-IO PLC 系统参考设计展示了一种系统级隔离方法。
MAXREFDES212 套件和参考设计旨在保护与 APP_SPI2 总线的连接,对剩余的两块扩展板(工厂自动化板和运动控制板)采用的是常见的隔离方法。在这种方法中,多个数字隔离器件可以保护 APP_SPI2 SPI 总线,以及 80 路连接器承载的其他信号线。此连接器用于将扩展板上的器件连接到应用处理器板上的 MAX32630 微控制器。
本电路的 Go-IO 设计利用的是 MAX22192 内置的隔离 SPI 接口,可为其他扩展板器件(包括各扩展板中内置的 Maxim MAX3108 UART)提供受保护的板侧 SPI 总线。Go-IO 设计还采用了 Maxim MAX14483 IC,可提供 6 个针对 SPI 事务优化的隔离通道。最后,此设计还使用了多个 Maxim MAX14130 四通道数字隔离器,可为其他 SPI 连接和特定信号线提供保护。
尽管两块扩展板上的 MAX14483 和 MAX14130 数字隔离器的配置略有不同,但两块板共享上述通用架构,这种架构也被工厂自动化板设计所采用(图 7)。除采用类似隔离方法外,两块电路板均可连接 Maxim MAX22192 提供的符合 IEC 61131-2 标准的输入,以及 MAX3108 和 MAXM22511 提供的受保护 RS-485 接口。
图 7:Maxim Go-IO 工厂自动化板可在微控制器和专用接口器件之间提供隔离连接,从而为开发人员提供多种工业接口(包括数字输入、数字输出、RS-485 和 IO-Link)支持。(图片来源:Maxim Integrated)
两块扩展板的主要区别在于器件的配置,其中一块扩展板的器件用于支持工厂自动化接口,另一块的器件则用于支持运动控制功能。在工厂自动化板 (MAXREFDES200) 内,受保护的 SPI 总线和信号线与高速输出驱动器连接,进而连至 IO-Link 子系统。此电路板设计使用上文提到的 Maxim MAX14912 高速开关/驱动器进行数字输出控制。对于 IO-Link 子系统,该电路板设计将一对 Maxim MAX14819 IO-Link 主收发器与 STMicroelectronics STM32F412 微控制器结合在一起,可执行其预装的 IO-Link 协议栈。
对于稳压电源,每块电路板都包含一对 Maxim MAXM15462 DC-DC 转换器,可将来自载板的 24 伏电源降至每块板所需的供电电平,即 3V3_DIO、3V3_MCU 和 5V0_DIO。此外,MAX22192 集成的 LDO 可将 24 伏电源转换为 3.3 V VDD_IO 电源,从而使 MAX14130 数字隔离器 IC 可在其受保护域中使用。
对于运动控制板 (MAXREFDES201) 而言,设计可将数字隔离器件与一组 MAX14870 电机驱动器和 MA14890 编码器结合在一起(图 8)。如前所述,MAX14870 和 MA14890 的组合使用可为开发人员提供所需关键功能,从而实现精密控制系统(由电机、继电器和其他装置构成)。
图 8:Go-IO 运动控制板集成了类似于工厂自动化板所使用的保护方案,可为开发人员提供驱动器输出和编码器输入,以实现电机、继电器和其他工业子系统的高级控制功能。(图片来源:Maxim Integrated)
为帮助工程师加快 Go-IO PLC 系统的软件开发,Maxim 提供了一款基本软件包,其中包含驱动程序和基本测试程序。虽然基础框架可作为固件预装在 Maxim MAX32630 微控制器中,但开发人员仍可以研究示例软件,该软件演示了通过系统的应用程序编程接口与单个器件交互的基本设计模式(清单 1)。GO-IO PLC 系统硬件参考设计及配套软件专注于工业 IO 接口,可为实现先进工业自动化系统提供所需的关键基础。
副本
* ************************************************************************* */
int TEST_MAX22192_run_tests(void){
int error;
di_channel_t di_ch;
TEST_print_line(0, 0, 0);
TEST_print_header("MAX22192 Tests", 0);
TEST_print_header("HW", 0);
//Read input for channel 1
di_ch = DI1;
error = MAX22192_read_input(di_ch);
printf("Test- MAX22192_read_input(%d): %d", di_ch, error);
TEST_print_pass(error == 1, 1);
. . .
/* ************************************************************************* */
int TEST_MAX14912_run_tests(void){
int error;
int counter;
do_channel_t do_ch;
do_mode_t do_mode;
uint8_t do_value;
TEST_print_line(0, 0, 0);
TEST_print_header("MAX14912 Tests", 0);
TEST_print_header("HW", 0);
//Write mode for channel 1
do_ch = DO1;
do_mode = DO_MODE_HS;
error = MAX14912_write_mode(do_ch, do_mode);
printf("Test- MAX14912_write_mode(%d, %d): %d", do_ch, do_mode, error);
TEST_print_pass(error == 0, 0);
. . .
清单 1:Maxim Integrated 的示例软件平台包括测试代码,可展示外设操作的基本设计模式,包括从 Maxim Integrated MAX22192 数字输入 IC 中的单个通道读取 (MAX22192_read_input()),以及将 (MAX14912_write_mode()) 写入 Maxim Integrated MAX14912 数字输入 IC 中的单个通道。(代码来源:Maxim Integrated)
结语
动态制造、预测性维护以及其他先进人工智能方法等高级应用取决于传感器、致动器及其他工业设备是否可靠连接。Maxim Integrated Go-IO PLC 模块化系统和参考设计可为现有环境提供现成的平台,并且可为满足新兴需求提供可扩展的基础。通过在 Go-IO PLC 平台上构建,开发人员可以快速部署紧凑型 PLC 解决方案,从而实现先进的制造系统。
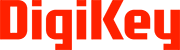
免责声明:各个作者和/或论坛参与者在本网站发表的观点、看法和意见不代表 DigiKey 的观点、看法和意见,也不代表 DigiKey 官方政策。