Tips to Getting the Most Out of Energy Harvesting Sources
投稿人:DigiKey 北美编辑
2016-04-26
Spurred on by the need for less energy consumption, especially in remote, wireless sensing applications, system and circuit designers are looking to harvest ambient energy sources. Yet getting the most out of these harvested sources is challenging, since matching their outputs to the inputs of other storage, control, processing, sensing and other tasks are not simple tasks and vary for different applications.
The output of modern energy harvesting sources, such as a solar cell and a thermoelectric generator (TEG), is relatively small, in the range of a few hundred µJs of energy. As a result, it must be first gathered and accumulated over time in order to make practical use of it in a typical 3 V circuit.
The amount of energy that needs to be stored depends on the application’s usage profile and duty cycle, while the time taken to store the energy depends on the energy source and how efficiently the energy is transferred to the local storage device. This storage device can be a battery-storage and backup, as well as supporting electronic circuitry. A typical energy harvesting source, such as a capacitor or coin-cell battery (variations include solid state storage thin-film devices, ultra and supercapacitors and buffers), generally consume only a few µW.
In solar cell applications, "cold" starts can be a problem. Defined as turning on a solar cell after all circuitry is turned off for a long period of time, cold starts can run aground. Power-management controllers can drain the photovoltaic cell’s stored output. In situations where this is likely, a dedicated backup battery would be advisable.
Alternatively, a designer can use the photovoltaic cell’s output to power the controller. Low-power-consumption controllers for solar-energy harvesting are now available. Together with a backup battery, this solution would be advisable.
Of the currently available sources of energy for harvesting, solar energy is the most prolific and promising, with the higher output power densities. Other sources include thermal gradients (differences) which TEGs use to generate electricity using the Seebeck effect, as well as vibration/motion and RF energy (see Table 1).
A Comparison of Energy Desities for Ambient Energy Sources
Energy Source |
Condition | Power Density |
---|---|---|
Solar | Outdoor | 7.5 mW/cm2 |
Solar | Indoor | 100 µW/cm2 |
Thermal | ∆T = 5°C | 100 µW/cm2 |
Vibration | 1 m/s2 | 60 µW/cm3 |
RF | Unless near a transmitter | <1 µW/cm2 |
Source: Virginia Polytechnic Institute and State University (Virginia Tech) |
Table 1: Solar energy is the most prolific and promising energy source, with the highest output power densities. Other sources include thermal gradients, as well as vibration and RF energy.
Regardless of the energy harvesting technology chosen, it’s important to know how to maximally transfer power from that source to the storage device. This requires matching the ambient source impedance to the load impedance using an efficient maximum power point tracking (MPPT) algorithm. The load comprises the power management controller and DC-to-DC converter. For solar energy and TEG sources, a good example of MPPT management is provided by the STEVAL-ISV021V1 energy harvesting evaluation kit from STMicroelectronics (Figure 1).
Figure 1: A good example of MPPT management is provided by the STEVAL-ISV021V1 energy harvesting evaluation kit from STMicroelectronics for solar cell and TEG applications. (Source: STMicroelectronics)
The kit is based on the company’s SPV1050 ultra-low-power energy harvester and battery charger. It illustrates a modern solution that’s supported by a software graphical user interface (GUI) to show MPPT and conversion efficiency under any temperature or irradiance condition (Figure 2).
Figure 2: The STEVAL-021V1’s energy harvesting kit’s MPPT accuracy and power efficiency curve is one of four parameters selectable GUI tabs, shown on a connected PC or a laptop display. (Source: STMicroelectronics)
In the SPV1050 itself, a pass transistor is controlled between the STORE and BATT pins and implements both the undervoltage protection (UVP) and the end of charge (EOC) protection thresholds (Figure 3). These functions are implemented by the two control voltages, VUVP and VEOC, which can be regulated by a resistor partitioning of R4, R5, and R6 between the STORE and EOC pins.
Figure 3: In STMicroelectronics’ SPV1050 ultra-low-power energy harvester and battery charger, a pass transistor is controlled between the STORE and BATT pins and implements both the under voltage protection (UVP) and the end of charge (EOC) protection thresholds. (Source: STMicroelectronics)
A complete system for energy harvesting power management is the MAX17710 energy harvesting charger and protector from Maxim Integrated (Figure 4).
This tiny ultra-thin (3 x 3 x 0.5 mm) IC in a UTDFN package charges and protects micro-power storage cells with energy harvested outputs over a wide range of 1 µW to 100 mW. It features lithium cell undervoltage protection and overvoltage short protection and uses only 1 nA of standby current.
Figure 4: The tiny MAX17710 charger and protector IC from Maxim Integrated is a complete system for energy storage cells and offers under-voltage and over-voltage protection. (Source: Maxim Integrated)
When hooking up to its FB pin, a divider circuit can be used to boost charge efficiency for charge systems between 1.0 and 2.0 V (Figure 5). The IC’s boost input LX pin controls current drive through the inductor of the external circuit. The divider, formed by resistors R1 and R2, allows the voltage on the FB pin to transition properly between FBON and FBOFF. This occurs during the boosting procedure.
Figure 5: To boost charge efficiency for charge systems between 1.0 and 2.0 V using the Maxim Integrated MAX17710 charger and protector IC, a divider network formed by resistors R1 and R2 allows the voltage on the FB pin to transition properly between FBON and FBOFF. This occurs during the boosting procedure. (Source: Maxim Integrated)
More complex control
If there is a need to control multiple energy harvesting outputs and storage devices, then the Cypress Semiconductor SAE101A energy harvesting power management IC fits the bill (Figure 6). It operates by switch control, providing input power selection via a solar cell or a primary battery.
Figure 6: Cypress Semiconductor’s SAE101A energy harvesting power management IC operates by switch control, providing input power selection via a solar cell or a primary battery. (Source: Cypress Semiconductor)
The IC stores the harvested energy on an output capacitor and turns on the power from the switching circuit while the capacitor voltage is within a preset maximum and minimum range for supplying energy to the load.
A series of seven switches on the SAE101A allows it to operate using two input power supplies, namely the solar cell voltage VDD and the primary voltage VBAT.
Figure 7: A series of seven switches on the Cypress Semiconductor SAE101A energy harvesting power management IC allows it to operate using two input power supplies, namely the solar cell voltage VDD and the primary voltage VBAT. (Source: Cypress Semiconductor)
Voltage at the VDD and VBAT pins are monitored, and selection control of the input power supply is performed based on the voltage state. Input power (solar cell or primary battery) is temporarily stored in a capacitor connected to the device’s VSTORE1 pin. When the voltage of the VSTORE1 reaches a certain threshold value or higher, power switch SWI connects VSTORE1 and VOUT1.
This device can be used in a wireless sensor node that works with Cypress Semiconductor’s EZ-BLE PRoC-module (Figure 8).
Figure 8: Cypress Semiconductor’s SAE101A power management IC and EZ-BLE PRoC module provide a wireless sensor node application. (Source: Cypress Semiconductor)
Consider the application
An important factor to consider is the end application whose energy demands vary. These include solar heating of homes and buildings, plant maintenance and control, automotive, and medical applications to name a few. The issues of maintenance time and frequency, not to mention the costs, of replacing batteries and other storage devices, must be measured against powering electronic circuitry that employs batteries and/or 115 VAC line power, without the use of an energy harvesting source.
The aforementioned wireless sensing capability is particularly important in industrial environments where electric motors proliferate and provide both vibration and thermal-gradient energy sources. This trend is being spurred on by the BLE (Bluetooth low energy) protocol.
Estimates are that total cost of electric-motor ownership can be substantial, even with the use of batteries, when you consider the energy that can be harvested from those motors. In fact, low-voltage booster modules for harvested energy are readily available on the market and can be set up for wireless sensor networking.
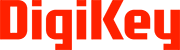
免责声明:各个作者和/或论坛参与者在本网站发表的观点、看法和意见不代表 DigiKey 的观点、看法和意见,也不代表 DigiKey 官方政策。