Ultra-Low Power Management for IoT Devices
投稿人:DigiKey 欧洲编辑
2018-01-16
The IoT is already estimated to be generating 100s of zettabytes (trillion gigabytes) of data per year, and this figure is only increasing. The amount of data the average household contributes to this figure is expected to increase fivefold by 2020. Creating data doesn’t require much compute power as data can be captured, digitized, and stored using the simplest of sensor hubs. MEMS sensors that are able to detect movement in nine axes are available in packages that measure just 1 or 2 millimeters on each side. These tiny devices and an increasing variety of sensors form the heart of today’s IoT, enable endpoints to capture, process, and share data online in real time.
As more endpoints are expected to operate from limited power sources or energy harvested from their environment, the need for ultra-low-power operation is increasing. Endpoints could be part of a larger sensor network, but could just as likely be remote and isolated. Once put into service they may be expected to operate for many years without maintenance, including battery replacement.
Manufacturers are busy developing new solutions to tackle this design challenge allowing us to conceive devices that can gather and transmit information without the need for any external power source. In the case of wearables, this could soon include devices that are powered solely by the wearer’s body or their activity.
Energize!
To illustrate how this may be realized, consider the block diagram shown in Figure 1. In most applications the power section could be any one of a wide range of power management devices, but for ultra-low-power applications, the choice is restricted to solutions specifically developed to maximize limited available power such as harvested energy.
Figure 1: A growing number of integrated solutions are now aimed at applications running primarily from harvested energy.
The block diagram in Figure 2 shows a version of our typical energy harvesting example using the ADP5090 power management unit from Analog Devices.
Figure 2: A block diagram of an energy harvesting application based on the ADP5090 from Analog Devices.
This is an ultra-low-power boost regulator that integrates maximum power point tracking (MPPT) and charge management functionality. The MPPT can be configured for both photoelectric and thermoelectric energy sources, operating over a range of 16 W to 200 mW. The device can start from a supply voltage as low as 380 mV and run from just 80 mV. It also supports the use of an optional primary cell battery, which can be switched in and out automatically. At just 3 mm by 3 mm, the 16-lead device is small yet highly capable, making it ideal for many IoT applications. The device is supported by an evaluation and demonstration kit, the ADP5090-2-EVALZ (Figure 3), providing the perfect platform for developing an energy harvesting application.
Figure 3: The ADP5090-2-EVALZ provides the perfect platform for evaluating the ADP5090 ultra-low-power boost regulator with MPPT and charge management from Analog Devices.
An alternative solution comes in the form of the LTC3588-1 from Linear Technology. Like other PMICs targeting energy harvesting, it features an ultra-low quiescent current. As it is designed to work with an energy source with an alternating current such as a piezoelectric generator, the LTC3588 integrates a low-loss full-wave bridge rectifier and a buck regulator (see Figure 4).
Figure 4: Block diagram of the LTC3588-1 nanopower energy harvesting power supply from Linear Technology.
The external capacitor connected to the Vin pin serves as an energy reservoir, while the output capacitor forms part of the regulated output. The device generates the internal drive rails for the buck converter, which in turn enables the charge in the input capacitor to be transferred to the output capacitor. The device functions by cycling the buck converter on and off. When the input voltage is high enough, the buck converter starts up. When it falls below the dropout voltage the buck converter is disabled, and the output is held up by the output capacitor. This hysteretic cycle repeats during normal operation, defined by the external inductor. The output voltage can be set using the D0 and D1 inputs to 1.8 V, 2.5 V, 3.3 V or 3.6 V. All of the functionality of the LTC3588-1 can be evaluated using the demonstration circuit DC1459B-A-ND.
If the application is a wireless sensor operating from a solar cell, then the S6AE101A from Cypress Semiconductor could be the perfect solution. This energy harvesting PMIC works with linear sources such as solar cells, and is able to function in light conditions as low as 100 lux thanks to its low start up power requirement of just 1.2 μW. An optional primary cell can also be included to ensure operation in no light conditions. Figure 5 shows a block diagram of the S6AE101A, showing the main features, including power gating.
Figure 5: Block diagram of the S6AE101A energy harvesting PMIC for wireless sensor nodes, from Cypress Semiconductor.
The device operates by comparing the stored voltage with a threshold. The output voltage is enabled automatically whenever the stored voltage exceeds the threshold. Once the stored voltage drops below the threshold, the output voltage is disabled. The active time is determined by the total system power consumption, and therefore varies by application, voltage source and the size of the energy storage capacitor. This must also be weighed against the generator’s capacity to deliver energy, and therefore, the time needed to charge the storage capacitor. All of the features of the S6AE101A can be evaluated using the development kit S6SAE101A00SA1002.
Getting connected
In our example application one of the main functional elements is the RF transceiver. Due to the increase in demand for ultra-low-power wireless networks, the number of highly integrated solutions targeting this application area continues to expand. A recent addition is the MAX7037 from Maxim Integrated, which is a 4-band sub-GHz RF transceiver with an integrated 8051 microcontroller and a mixed-signal sensor interface (Figure 6).
Figure 6: The MAX7037 from Maxim Integrated is an ultra-low-power quad-band multichannel transceiver targeting ultra-low-power wireless sensor networks.
Under the control of a host processor, the MAX7037 consumes as little as 16 mA in transmit mode and 22 mA in receive, falling to just 100 nA in deep-sleep mode. Designed for use in the ISM sub-GHz bands worldwide, it can be configured for operation at 315, 433, 868 or 915 - 930 MHz using FFSK, FMSK or ASM modulation.
The mixed-signal sensor interface supports analog sensors through an integrated 9-bit sigma delta ADC. The host CPU controls the MAX7037 over UART, but by default it operates as a SPI slave. In this mode, its 64 Kbyte of on-chip Flash can hold firmware programmed by the host CPU. The TEST0 pin controls whether the device starts up in programming or runtime mode. To evaluate the features of the MAX7030, take a look at the MAX7037EVKIT.
An alternative and slightly more integrated solution which doesn’t require a host CPU, could be the CC1310 from Texas Instruments, part of its SimpleLink family. As illustrated in Figure 7, this ultra-low-power sub-GHz wireless MCU integrates an ARM® Cortex®-M3 core with an ultra-low-power sensor controller that can run autonomously to save system power, and a fully integrated RF transceiver capable of operating at 315, 433, 470, 500, 779, 868 and 915 - 920 MHz.
Figure 7: The CC1310 from Texas Instruments is a highly integrated wireless MCU from its SimpleLink family
Adding sensors
At the core of this kind of IoT device sit the sensors used to capture the data. While many forms of transducer exist, MEMS technology has revolutionized the sensor sector.
Popular use-cases in wearable technology for sports or medical purposes include heart rate monitoring and pulse oximetry. These functions are often realized using LEDs and photodiodes. The SFH7050 BioMon sensor from Osram Opto Semiconductors is a prime example. It integrates three emitters (green, red and infrared) and one detector in a single package measuring just 4.7 mm by 2.5 mm by 0.9 mm.
Other forms of sensing often used in wearable devices include motion sensing, and here, MEMS sensors excel in terms of functionality, size and power. Many manufacturers are now integrating several types of sensors into a single device, making it even easier to add functions to smaller products that can be worn or carried unobtrusively.
For example, the ICM-20789 from TDK InvenSense is a 6-axis MEMS motion sensor with an integrated pressure sensor. It features a 3-axis gyroscope and a 3-axis accelerometer, complemented by the pressure sensor that can be used to track changes in elevation. The motion and pressure sensors are supported by their own temperature sensors for calibration purposes. However, the temperature measurements can also be used by the host application.
The MEMS sensors are joined by a digital motion processor (DMP), realized in CMOS and wafer-level bonded to the sensors in a package measuring just 4 mm by 4 mm by 1.365 mm. While the primary interface to the host system is I2C, the device’s features are accessed and controlled using APIs for drivers running on the DMP. This allows the sensor parameters and output data rate to be configured, as well as the mode (low power or low noise) and the I2C/SPI interface.
All of the features can be evaluated using the DK-20789 SmartMotion platform which is supplied with a GUI-based development environment to control and configure the device, as well as capture and visualize the data it produces.
Putting it all together
Combinations of the components outlined above could be used in our hypothetical application. Table 1 shows the relevant electrical characteristics for each of the devices.
It should be noted that the power requirements of each of the devices featured in this article vary significantly during operation depending on the mode, surge at start-up, and ambient conditions. The figures provided in Table 1 are purely for illustration and are not definitive.
|
Notes:
- Estimated from manufacturers’ datasheet figures – these figures are load dependent and are provided for illustration only
- Calculated using Equation 1, based on a periodic on-time of 10 ms
Equation 1:
Equation 2:
Table 1: An illustration of the energy requirements for the devices featured in this article.
The energy figures shown in Table 1 have been calculated using equations detailed in the application note AN210772: ‘Energy Calculation for Energy Harvesting with S6AE101A, S6AE102A and S6AE103A’. It was produced by Cypress Semiconductor to support its S6AE101A/2A/3A family of energy harvesting PMICs to better estimate the energy demands of a given application.
Although they are very rough estimates, by using these figures as a starting point we can begin to build an energy budget for our application. By assuming a periodic on-time of 10 ms, selecting the components highlighted in Table 1 suggests our hypothetical IoT device would consume around 3.4 mJ. If we put this figure into Equation 2, we can estimate that our application would need a charge capacitor of at least 1000 μF.
This can, of course, be optimized based on the application, but it does at least indicate that developing a highly featured wearable device powered by harvested energy is theoretically possible using solutions available today.
Conclusion
A cursory investigation into the solutions available for developing ultra-low-power wireless sensor networks operating from harvested energy shows that developing these applications is entirely feasible. As the IoT continues to expand, it is a surety that semiconductor manufacturers will seize the opportunity to service the demand for devices that consume even less power.
Using today’s technology, it is possible to create a functional, self-powered IoT device from a limited energy budget that uses long-range, low-power wireless connectivity, provided it is only required to transmit data infrequently and has access to sufficient ‘free’ energy.
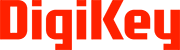
免责声明:各个作者和/或论坛参与者在本网站发表的观点、看法和意见不代表 DigiKey 的观点、看法和意见,也不代表 DigiKey 官方政策。