Sensors Make Sense of Robots' Worlds
投稿人:DigiKey 欧洲编辑
2012-01-12
The global robot population is growing rapidly, and with it the demand for the sensors and systems that enable these machines to work in increasingly complex environments. According to a September 2011 report¹ from the International Federation of Robotics (IFR), industrial robot sales rose 18 percent year on year in 2011, to 140,000 units, and are expected to continue to grow by 6 percent a year through 2014. By then, IFR expects there will be 1.3 million robots at work in factories worldwide.
Who is buying these robots? Viewed by sector, a lot of the growth is coming from the automotive industry, and from efforts to automate the production of electrical and electronic goods such as flat-panel displays and solar cells. Viewed by country, however, China has been making “huge” investments in robots over the past few years, according to IFR, almost tripling the ratio of robots to human workers over four years. By 2014, IFR expects China will be the biggest single buyer of robots in the world.
Industrial robots are also being used in more unexpected and challenging ways, for example to pack champagne bottles, in the assembly of complex and rapidly changing consumer goods, in stone masonry, and even in industrial processes in which a human operator interacts safely with an unguarded robot welder.
Alongside the industrial robots, IFR is also tracking an emerging category of ‘service robots’, which it defines as ‘a robot which operates semi- or fully autonomously to perform services useful to the wellbeing of humans and equipment, excluding manufacturing operations’. Sales grew 4 percent , compared to 2006, to 13,741 units.
Figure 1: Global usage of robots is rising rapidly, especially in China.
The largest category of ‘professional service robots’ serves defense applications, for example with aerial drones, but the second-largest category is ‘field robots’, which are usually milking machines. Professional service robots are also used in the medical sector, for robot-assisted surgery, in factories for automated guided vehicles, in construction, cleaning, inspection and maintenance systems, and even underwater.
IFR also tracks personal and domestic service robot sales. These are largely robot vacuum cleaners, lawnmowers, toys, hobbyist systems and robots for education and research. IFR estimates that 1.445 million domestic robots, and about 753,000 entertainment robots, were sold in 2010.
Lots of robots, lots of sensors
IFR’s analysis suggests that the global population of robots is growing fast, and that these robots are becoming increasingly sophisticated, especially in the service robot sector where the robots have to work safely in a much more complex and less constrained environment than most industrial robots. Think of a domestic robot vacuum cleaner, for example, which has to navigate through an undefined space over undefined surfaces in undefined conditions to do its work. It takes multiple sensors, interacting with each other in complex ways, to make the robot vacuum cleaner work safely and effectively - and all this has to be achieved at a consumer price point.
What do the sensors do? One broad way to categorize them is to divide them into those sensors that are used by the robot to sense its state, and those which are used to sense its environment.
A robot’s state will be defined in part by its mechanical architecture, the combination of linkages, joints, and the sliding and rotating elements that make up its form. Each joint or slide will be driven by an actuator and will need to be monitored so the robot knows the positions of its joints and linkages, their velocities and accelerations. Robots will also need sensors that will enable the control software to derive dynamic parameters such as force, torque and inertia as the robot moves.
Robots will sense their environments at three scales: through contact; in proximity; and in the far field. Each type of sensing has different challenges: a simple micro switch can be used as a bump sensor on a robot vacuum cleaner, whereas the ‘fingertip’ of a remote manipulator may rely on a complex array of pressure sensors to provide the sensing necessary to apply the right amount of force to grip an object without crushing it. Proximity sensing may rely on inductive, capacitive, Hall effect, ultrasonic or optical techniques. In the far field, robots may need range sensors to know how far they are from objects in their environment, or full vision systems that produce images of the environment for interpretation by vision processing systems. In complex environments, robots often use combinations of sensors to get the best sense of where they are - for example, the automobiles that competed in DARPA’s Grand Challenge to develop vehicles that could navigate through an off-road course autonomously used various combinations of video cameras, radar, and laser rangefinders to sense their environments.
State sensors
Even the humblest of components can play a role in helping a robot understand its own state. A simple micro switch, such as the Omron D3M, can be used to sense when a moving component is reaching the end of its range of travel. The D3M has a snap action, so that it takes a defined force to operate it, and is available in normally open and normally closed electrical configurations. The part is also available with a variety of actuators, such as pin plungers, hinge levers and roller levers, and can be configured with various actuator positions and forces so that its action best matches the application.
For designs that need to sense a linear displacement, rather than simply registering when a component has reached the limits of its range of travel, gage heads provide one solution. The Measurement Specialties GCD-SE series gage heads include a spring-loaded linear variable differential transformer (LVDT), a precision linear bearing, and conditioning electronics. The gage heads can measure linear displacements over a variety of ranges, such as 0 to 2.54 mm, or 0 to 50.8 mm, and are engineered to work in mechanically and electrically harsh environments.
A joint approach
Along with sensing end stops and measuring linear positions, many robotic systems need to know how far various rotary joints have turned so they can derive the absolute position in space of manipulators or other arm-mounted devices. Angular encoders, such as Electroswitch’s 500 series use a Hall-effect magnetic sensor and digital signal processing to produce contact-free, high-resolution rotary position sensing. Because the sensor’s signal is captured and conditioned by an onboard integrated circuit, various types of outputs are available. For example, the encoders can produce a quadrature output of up to 256 pulses per revolution (PPR), or can be used as a tachometer with a resolution of up to 512 PPR and a direction indication. The encoder also offers an absolute position reading, measured at a resolution of 1024 PPR, as a 10-bit, pulse-width-modulated output.
Avago Technologies has a different approach with the HEDS-9000 series two-channel optical incremental encoder modules. These put a lensed LED as a light source and a detector IC in a small, C-shaped plastic package. The module shines light through a translucent code wheel, which is patterned to produce up to 1000 codes per revolution. Four photo detectors are arranged in two pairs so that when one pair is receiving light shone through the code wheel, the pattern is blocking light to the other pair. Comparing the outputs of the two pairs produces two final digital outputs that are 90 degrees out of phase. Avago says the part is suitable for low-cost applications such as plotters and factory-automation equipment, but should not be used in safety-critical applications.
Figure 2: Two pairs of photodiodes produce a pair of phase-related outputs from an optical code wheel sensor.
Pitching in
Some robotic applications need to know the absolute angle to horizontal or vertical of elements of their construction. Inclinometers, such as VTI Technologies’ SCA61T, use micro-electromechanical-machining (MEMS) techniques to build extremely robust and sensitive angle measurement devices. The SCA61T family includes inclinometers that can measure ±30 degrees or ±90 degrees, with a resolution of 0.0025 degrees. This resolution is available on an analog output, although a digital output conforming to the serial peripheral interface (SPI) bus specification is also available. A digital temperature readout enables temperature compensation for greater measurement accuracy. The MEMS basis of the part means it can also self-test, by generating an electrostatic force that deflects the proof mass to its maximum positive deflection, which then pushes the output signal to its maximum value.
MEMS technology is also behind Analog Devices’ ADX193 family of single-axis accelerometers, which are useful in robotic applications, such as the pick and place head of an assembly machine, where you want to move the head over large distances as quickly as possible but ensure that it is moving slowly and precisely when it arrives in the work area. The ADX193 family derives from Analog Devices’ involvement in producing airbag sensors for cars. These fourth-generation single-axis accelerometers offer signal-conditioned voltage outputs measuring both dynamic acceleration (vibration) and static acceleration (gravity) with a full-scale range of ±120 g or ±250 g.
Bosch Sensortec produces a three-axis MEMS accelerometer, the BMA222, which can be programmed to sense ±2 g, ±4 g, ±8 g or ±16 g, and includes digital and analog outputs. Although this part is designed for use in consumer applications, such as drop sensors in hard disc drives and attitude sensors in handheld devices, Bosch Sensortec has included an intriguing facility that could be of use to robot makers: the part can be programmed to produce a digital interrupt signal when particular conditions are met, such as when it receives a high g shock, or on any motion. The part is also tiny - at 2 x 2 x 0.95 mm, which means that it could be used where space is tight, for example, on the tips of delicate remote manipulators.
External sensors
There are many other ways for a robot to sense its own state, but it is equally important for the robot to be able to sense its environment.
One of the simplest ways this is done is optically, for example in line-following applications where a part such as Fairchild Optoelectronics Group’s QSE 15x Optologic photosensors can be used to build low-cost light sensing systems. The part is available in totem-pole or open-collector configurations, buffered or unbuffered, and includes a photodiode, linear amplifier, voltage regulator, and Schmitt trigger, which provides some hysteresis that helps shape the output pulse and improve noise immunity. The output can drive up to ten TTL loads over supply currents from 4.5 to 16.0 V.
More subtle optical measurements are also available in predefined modules, such as Sharp Microelectronics’ GP2Y0D810Z0F distance-measuring sensor unit. This part includes photodiodes and infrared diodes, as well as signal-processing circuitry, which improves its ability to work accurately in varying optical conditions. The part works over a distance of up to 100 mm, and will provide an output signal even when it senses something static within 100 mm, rather than needing a moving target to produce an indicator output. Typical applications are in touch-less switches, but the part could also be used as a proximity sensor in consumer robotics applications.
Other environmental sensing systems use passive or active infrared, sonar, ultrasonics, and even radar. Specialist robots may be equipped with radiation sensors, infrared cameras, and even GPS for global positioning, so that they can better understand the environment in which they are working.
Constraints on sensor systems
All sensors have limitations, and it is worth understanding what they are before trying to build robot control systems around them. If a rotary encoder only offers 256 PPR, you’ll be unable to position a joint with 1-degree accuracy. If a thermal sensor is accurate to ±1 degree C, it won’t be much use in an environment that needs to be controlled to ±0.1 degree C. These may be simplistic examples, but the point is that any control system will have to be designed to take account of the limitations of the sensor system, and the compounding errors induced by multiple sensors working together.
Sensors are also often relatively delicate, when compared to the large, fast-moving masses used in many robots. Some sensors are built for industrial applications and so protect the delicate sensing elements, such as the gage tip in the gage head described above, in a tough steel casing. Others need the system integrators in the robot design team to engineer systems that will put protection around them.
Sensors are often delicate in terms of the signals they produce. An analog measurement system such as a strain gauge needs its output signal to be protected from electrical interference if its readings are to be trusted. That is why many modern sensors handle all the temperature compensation and signal-conditioning onboard, and convert their signals into a digital output that can be transmitted through an electrically noisy environment with fewer errors. The trade-off for this approach, of course, is a reduction in the theoretical resolution available from the sensor, although the practical usefulness of analog and digital versions of the same output may be equivalent.
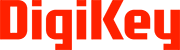
免责声明:各个作者和/或论坛参与者在本网站发表的观点、看法和意见不代表 DigiKey 的观点、看法和意见,也不代表 DigiKey 官方政策。