多传感器资产监控如何提高工业 4.0 工厂、物流和数据中心的性能
投稿人:DigiKey 北美编辑
2024-08-30
监测机器的振动和温度等参数可获取机器性能及其健康状况的实时数据,并为制造商提供所需的数据,以便安排主动维护、减少停机时间并提高生产率。
对物流设施或运输过程中的湿度和温度进行监控,可以提高运转效率,并能实现对疫苗或新鲜农产品等货物的保存。因此市场推出了提供有线和无线连接的环境监测系统,可适应各种应用需要,包括企业和云数据中心。
监测振动有助于在机器出现潜在问题之前就加以识别。国际标准化组织 (ISO) 10816 标准为此提供了重要参考。它为评估用于泵、风扇、压缩机、齿轮箱、鼓风机、干燥机、压力机和类似机器(工作频率范围为 10 到 1000 赫兹)的电机的振动严重程度提供了指导。
本文介绍了在选择有线还是无线连接监控系统时的一些主要考虑因素,并说明使用有线和无线网络并非是非此即彼的选择。然后,介绍了 ISO 10816 中定义的四个振动严重程度等级。最后讨论了实现有线和无线状态监测系统的各种方案,包括使用多个传感器监测振动、温度、湿度和代表性应用。
Banner Engineering 提供多种设备健康监测 (EHM) 网关选择,可轻松获取 EHM 网络数据。工业 EHM 设计人员可以选择该公司的 SNAP ID 有线网关解决方案和 CLOUD ID 无线网关,前者带传感器读数本地显示屏或可选的云仪表板,后者旨在直接连接云仪表板(图 1)。这两种选择的共同特性包括:
- 众多传感器可供选择,以优化 EHM 的运行
- 自动识别已连接的传感器,支持快速部署,无需额外编程
- 可随时获取传感器数据,用于调整设备或安排所需的维护工作,从而最大限度地减少停机时间,最大限度地提高生产率
- 两个系统都支持云连接
- 可提供预配置仪表板,并可进行定制,以实现最佳数据可视化
图 1:Banner 的 SNAP ID 有线网关(左)和 CLOUD ID 无线网关(右)EHM 网关有几个共同特性。(图片来源:DigiKey)
有线还是无线 EHM 网关?
虽然它们有一些共同的特性,但有线和无线 EHM 网关之间还是有本质区别的。AMG-SNAP-ID 资产监控网关 (AMG) 支持最多 20 个传感器和转换器的调试、监控和报警。它支持 Modbus 和 Banner 的 SNAP SIGNAL 连接,可扫描单个传感器或转换器,自动检测型号信息。用户可以更改和分配 Modbus 服务器 ID 编号,以构建和调试定制 EHM 解决方案。可对连接的设备进行分组,并可单独分配警报阈值。警报状态可通过触摸屏和外壳顶部指示灯的颜色显示出来。
当需要直接连接到云端时,EHM 系统设计人员可以使用 DXM1200-X2 IIoT 网关连接多达 200 台来自 Banner 和第三方的设备,以提供性能和机器健康数据。它可以自动检测和连接传感器节点,并将数据传输到 Banner 云软件。开发人员可以选择简单或复杂的编程工具。IIoT 网关可以在边缘处理信息,然后通过以太网和蜂窝网络发送信息,以便在世界任何地方通过直观的云仪表板进行监控(图 2)。
图 2:无线(左)和有线(右)IIoT 传感器网关有几个共同特性。(图片来源:Banner Engineering)
有线和无线 EHM 架构
有线和无线 EHM 架构并不相互排斥。有线系统可以包含无线元素,无线架构通常也包括有线连接。
例如,一个基本的有线 EHM 架构可以包括几个连接到多个传感器的接线盒,如 4 端口 R50-4M125-M125Q-P 和 8 端口 R95-8M125-M125Q-P。Banner 的 Sure Cross R70SR 串行数据无线电(如 900-MHz R70SR9MQ 和 2.4-GHz R70SR2MQ)无需额外布线即可扩展网络范围。这些无线电的特性包括(图 3):
- RS-485 串行接口
- 支持星形和树形网络拓扑结构
- 支持多跳自愈、自动路由射频网络,进一步扩展了网络范围
- 跳频扩频 (FHSS) 技术实现了可靠的数据传输
图 3:基本有线资产监控拓扑(左)和无线连接远程传感器集群示例(右)。(图片来源:DigiKey)
在大型设施中,众多系统可能分布在很大范围内,包括:
- 空气压缩机
- 泵送系统
- 传送带系统
- 众多电机和机器
- 变速箱
- 空气过滤系统
- 储罐液位测量和监视
在这种情况下,通过将有线和无线技术相结合,可以提高 EHM 系统的性能。上面提到的 DXM1200-X2 无线 IIoT 网关包括 Modbus 有线连接。如果需要以太网,设计人员可以使用 DXMR90-X1。DXMR90-4K 可实现 IO-Link 主机/控制器功能。除了 Modbus、以太网和 IO-Link 选择之外,设计人员还可以使用 R709 串行数据无线电为物理分散的资产提供无线连接(图 4)。
图 4:IIoT 无线网关(左下)提供 Modbus、以太网和 IO-Link 连接。(图片来源:Banner Engineering)
ISO 10816 振动严重程度标准
ISO 10816 是针对 EHM 的一项重要标准。它可以量化电机、泵和发电机等机器的振动严重程度。该标准使用加速度、位移或振动速度的均方根值。ISO 10816 还包括对峰峰值的考虑。在测量两个或多个参数时,振动严重程度的均方根值最高。该标准将振动严重程度分为四个等级:
- 良好通常表示新投入使用的机器。
- 振动合适表示工作区域不受限制。
- 振动不理想表示需要限制运行并安排预防性维护。
- 振动不可接受表示机器可能会损坏。
图 5:IEC 10816 包括四个振动严重程度类别。(图片来源:Banner Engineering)
振动与机器学习
即使是“完全相同”的机器也不是完全相同的复制品。这就是机器学习 (ML) 的用武之地。Banner Engineering 提供的 VIBE-IQ 是一款振动监测软件包,它利用机器学习 (ML) 为每台机器的振动建立独特的基准运行值。然后,ML 软件会自动设置警告和警报阈值。它可以自动进行复杂的 EHM 计算和分析。VIBE-IQ 的部分特性包括:
- 持续监测 10 至 1,000 Hz 的均方根速度、1,000 至 4,000 Hz 的均方根高频加速度和温度
- 只监控运行中的电机
- 利用数据进行趋势分析和实时监控,以识别以下状况:
- 系统失调或失衡
- 零部件磨损或松动
- 轴承过度磨损
- 电机安装或驱动不当
- 超温条件
- 主动向主机控制器或云发送警报
振动和温度
振动并不是机器需要预防性维护的唯一线索。温度上升的趋势也会提醒超高温机电系统注意潜在的问题,尤其是当温度上升与振动增加相关联时。
结合这两个参数,可以更全面地了解设备的状况。它们可以提醒操作员注意不同的情况,并带来了多种好处:
- 振动可以识别机械问题,如失调、失衡、轴承磨损等。
- 温度升高可以发现电气问题,如绕组过热或润滑问题。
- 在检测异常运行时,将带外振动和温度联系起来有助于确定可能的原因。例如,振动模式有助于找出根本原因。
- 通过监测温度和振动可以帮助制定预防性维护计划。温度逐渐升高并不一定会像振动加剧那样造成问题,因为振动加剧需要更及时的纠正。
- 了解如何利用传感器数据改进长期资产选择和利用,以在问题出现之前识别潜在的运行限制。
当需要监测温度和振动时,EHM 系统设计人员可以使用铝制外壳的 QM30VT2 传感器或不锈钢外壳的 QM30VT2-SS-QP。这两款产品均来自 Banner Engineering,都可以作为从机设备通过 RS-485 连接到 Modbus 无线电设备或任何 Modbus 网络。它们外形小巧,可以安装在狭小的位置(图 6)。其他特性包括:
- 高精度温度和振动测量
- 温度测量范围为 -40°C 至 +105°C,分辨率为 1°C,精度为 ±3°C
- 检测双轴振动,带宽高达 4 kHz,25°C 时精度为 ±10%,默认采样频率为 20 kHz
- 输出均方根速度、均方根高频加速度、峰值速度以及根据振动波形预处理的其他参数
图 6:双轴振动加温度传感器可直接安装在电机外壳上(右图)。(图片来源:Banner Engineering)
振动频谱分带是一项先进的功能。除了 10 至 1,000 Hz 和 1,000 至 4,000 Hz 标量数据外,它还允许用户拆分宽带快速傅立叶变换 (FFT),以获得较窄频带的均方根速度或加速度数据。根据用户需要,可手动输入频段频率,或根据动态或静态速度输入自动生成频段频率。频带分析可以更具体地帮助诊断旋转机器的问题。
温度和湿度
监控温度和湿度对数据中心、仓库、无尘室、冰箱或冷却器都很重要。像 DX80N9Q45THA 这样的温湿度传感器可以帮助您:
- 保存新鲜农产品或疫苗等物品,控制温度和湿度对这些产品的长期存活和防止变质至关重要
- 保护数据中心内服务器和存储设备之类设备,因为过高的温度或湿度会影响正常运行或导致故障
- 加强仓库和其他设施中人员的健康和安全,因为高湿度会使工人在高温下难以保持凉爽,从而可能导致中暑
温度测量范围为 -40°C 至 +85°C,分辨率为 0.1°C,精度为 ±0.6°C( -40°C 至 0°C )、±0.4°C(0°C 至 +60°C)、±1.2°C(+60°C 至 +85°C)。湿度传感器可测量 0% 至 100% 相对湿度,+25°C 时精度为 ±2%,0°C 至 +70°C、10% 至 90% 相对湿度时精度为 ±3%,0°C 至 +70°C、0% 至 10% 或 90% 至 100% 相对湿度时精度为 ±7%。
该装置开启后,以快速采样模式运行,每两秒发送一次数据。五分钟后,节点进入默认模式,每隔五分钟发送一次数据。用户可选择 15 分钟或 64 秒的采样率。
配备 900 MHz 无线电的型号发射功率为 1 W (30 dBm) 或 250 mW(24 dB 用户可选)。250 mW 模式虽然缩短了传输距离,但在短距离应用中却能延长电池寿命。对于 2.4 GHz 型号,发射功率固定在 65 mW(18 dBm)左右。工作在存储模式时,无线电会关闭,以节省电池寿命。
结语
工业 4.0 工厂中有效的 EHM 系统可监测振动和温度,帮助保持高水平的正常运行时间。温湿度传感器还能提高数据中心的运行性能,并帮助在仓库和物流操作中保存疫苗或新鲜农产品等货物。这些系统可使用有线或无线连接来监控多个参数。
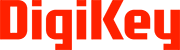
免责声明:各个作者和/或论坛参与者在本网站发表的观点、看法和意见不代表 DigiKey 的观点、看法和意见,也不代表 DigiKey 官方政策。