Data Acquisition in Apollo's March to the Moon
投稿人:Convergence Promotions LLC
2013-01-31
America's Apollo space program to reach the Moon by the close of the 1960s was an ambitious, as well as audacious, effort that relied heavily on data acquisition (DAQ) for monitoring and automating the flight process from before final countdown through return landing.
This article examines some of the hardware and techniques used for flight data acquisition during Apollo. These technologies of the past are then compared with examples of their modern equivalents for state-of-the-art sensing and conversion for DAQ.
One giant leap
The technology of the late 1950s and early 1960s was pushed hard to get Neil Armstrong’s boot print on the lunar surface in July of 1969, but it was not just hardware/software systems that advanced.
The Apollo Project’s scope and diversity of suppliers, along with the unprecedented range of tasks at hand, meant much cooperation and interoperation paralleled the pure technology development. Program Management in Apollo evolved to coordinate massive system design and fabrication, including integration and checkout from suppliers that spanned facilities coast-to-coast.
Three major systems evolved during the manned missions of Apollo: Multistage Booster Rocket (Saturn V), Command/Service Module (CSM), and Lunar Module (LM). Each of these elements – hugely complex in their own right – required meticulous fabrication and integration. Assembling, testing, and ultimately flying the entire rocket stack was more complex still, but smart minds and copious taxpayer funds ultimately found a way to get it done.
Well-defined and efficient interfaces between spacecraft elements allowed three different rocket-stage suppliers (Boeing, North American Rockwell, and McDonnell Douglas) to synchronize with a capsule supplier (North American Rockwell) and a Lunar Lander supplier (Grumman) over large distances, offering integration at several NASA facilities. Of course these contractors – and there were many others - had their own suppliers/sub-contractors, so the supply chain ran deep, as did the technical elements of the Apollo’s systems.
New space vehicles emerged with the ability to redundantly automate, monitor, and cross-correlate hardware performance, function, and health. In some cases, this newfound complexity also meant that manual “stick-and-rudder” piloting could no longer be used as the primary means of flight control. Not all of the astronauts – mostly military test pilots – embraced the technology initially, so trust in automated assistance took time.
However, these were intercontinental ballistic missiles (ICBMs) with men strapped on top, not fighter jets. Eventually, the astronaut corps came to see that success meant being as much a Systems Manager as a pilot, with new computing and control technologies taking over tasks no longer possible or practical by humans in-flight. The ICBM guidance technology, borne of the era between WWII and the Cold War, would necessarily become the order of the day.
The astronauts also relied heavily on remote-controlled activities managed by the Manned Spaceflight Center in Houston (Mission Control). By using telemetry and sensing that let the “guys on the ground” follow every minutia of the many spacecraft elements, much deeper technical and logistical resources could be brought to bear in the process of launching, directing, landing, and returning safely. Guidance and tracking from the ground became the norm as the primary approach for mission success.
The same sensors and navigation systems which allowed Mission Control to follow and control the action also gave the astronauts awareness on the state of their spacecrafts and the ability to take over control when needed. This duality was key since the pilots were on their own in the case of failures, or even just being on the far side of the moon and out of communication reach. While astronauts were System Managers when things went right, they needed intimate knowledge and control of the spacecraft hardware when radio signals were lost or something just went wrong.
“It’s complicated…”
In an era which predates high levels of silicon integration, much of the Apollo program’s astrionics and avionics were based around very low integration levels, discrete transistor technology, or even non-silicon solutions. Single-gate RTL/DTL logic for CPUs and non-volatile core memory were state of the art for space, yet they provided just kilobytes of usable data storage and the compute horsepower of a modern calculator. Ground support and checkout relied on digital and analog processing capabilities from systems that filled a room at the time, but today would fit in your hand. Key guidance system components were based on sophisticated electro-mechanical instruments, weighing tens of kilograms then but mere grams now.
Three million parts formed the fully-configured Saturn/CSM/LM stack, but let us contrast some modern components with just a handful of their parallels used in Apollo’s DAQ, specifically temperature sensing, A/D conversion, and – stepping it up a notch – inertial measurement that formed the core of Apollo’s self-contained guidance.
Is it hot in here?
As one can imagine, measuring temperatures in and across the many elements of a Moon Rocket was a big deal. Environmental control systems, cryogenics of the rocket propulsion systems, heat shield interfaces, and electronics operating environments were just some of the areas needing temperature monitoring to assess and maintain the health of the spacecraft.
For the most part, temperatures were measured by way of thermopiles, thermocouples, and resistance temperature detectors (RTDs). Figure 1 shows a flight spare of such an RTD used for surface temperature DAQ in the Apollo CSM. The transducer is a roughly one inch square plate with the long attached lead wire rolled up and to the lower right in the image.
While such RTDs are still in wide use, they are heavy (particularly with the stout shielded wiring needed for each) and certainly cannot match the compactness or capabilities of the modern silicon temperature sensors available today.
As an example, consider Texas Instruments' TMP725, a small, 8-pin, addressable temperature sensor that goes far beyond the function of the purely analog RTD, reporting temperature outputs via digital messaging over a SMBus interface. For simpler thermopile replacements, modern-day passive sensing in shrunk form can also be seen in Texas Instrument’s TMP006 product training module.
While not suitable for cryogenics applications, the TMP275/TMP006 and other devices like it have changed the temperature-monitoring landscape, creating small, low-power sensors able to digitally report temperatures being monitored at a fraction of the cost and weight of the RTD and associated electronics to which it interfaced in the spacecraft.
Don’t give me that (analog) nonsense
Digitizing of analog data was widespread during the Apollo missions, but the tools to do such conversions have sharpened substantially in the 40+ years since our trips to the moon. Analog-to-digital conversion (ADC) in DAQ could be found on the Launchpad and in the spacecraft itself, so let us look at just one example of ADCs in each location.
Radio Corporation of America (RCA) supplied the RCA110 control computer to NASA during Apollo. The RCA110’s primary role was to monitor and automate the pre-flight checkout of the rocket system before ignition, dutifully performing checkout of the spacecraft while still on the launch pad. While a significant portion of the RCA110 system interfaced directly to the already-digital signals on the Saturn rocket, many of the monitored items (such as the temperature sensors discussed) were a strictly analog affair, and ADCs fronted much of the RCA110 interface.
The RCA110 was implemented almost entirely with discrete transistors, so ADC functions were correspondingly complex at the circuit card level. Figure 2 illustrates two PCB cards from the RCA110 – each about 25 x 12 cm. While it is unclear whether these boards were part of ADC functions, one can get a good idea of the transistor density of the day and the corresponding real-estate needed to implement an ADC which might require hundreds of transistors.
While the RCA110 had the luxury of bulk allowed by its ground-based role, such was not the case for flight equipment where ADCs could again be found. The ability to monitor myriad analog signals in the CSM/LM in-flight provided ground controllers and astronauts’ critical system status visibility, but digital radio transmission was required to get the information back to Houston.
A special data telemetry box supplied by Harris had at its core an 8-bit, successive approximation register (SAR) ADC to digitize multiplexed analog signals for transmission back to earth using a Pulse Code Modulation radio. Weighing in at 45 pounds, along with the 23 pounds for the CSM and LM telemetry boxes, respectively, the ADC coding portions of the design were likely a big part of the weight/size/power budget for boxes holding some ten to twenty thousand components each.
In comparison to the power-hungry, 50 sample per second, 8-bit ADC of the PCM Telemetry system, 16-bit ADC devices such as Analog Devices’ AD7988 bring orders of magnitude higher SAR ADC conversion rates at a fraction of the power, size, and weight of ADC solutions before silicon integration.
Current monitoring, an ever-present need in electronics, was applied to fuel cell power-generation/inverter plants in the Apollo CSM and LM, along with the many circuits that drew from these power sources. Today, parts such as ams’ AS8510 DAQ chip can be used to leverage ADC integration for modern digital current metering in electric vehicles and the like, vastly reducing component overhead versus earlier approaches. DigiKey carries a short Product Training Module for the AS8510 that suggests how it might be used in automotive applications.
That is my ticket home…
Propulsion, environment-control, and navigation are three pillars of successful manned space flight. For the latter, Apollo relied on advanced versions of the era’s electromechanical guidance and navigation (G&N) marvels found elsewhere in aviation and autonomous missile systems.
Gyro-accelerometer inertial measurement units (IMUs) for Apollo were basketball-sized whirling dervishes, almost literally providing a stable platform to determine relative motion from a specific location and the orientation in space of the platform relative to a reference coordinate system. By knowing direction and magnitude of accelerations and angular displacements in three axes, along with orientation, the basis for guidance and navigation is put in place. You are able to determine where you are and which way to go to get somewhere else.
Ground tracking and navigation had to have spacecraft-based G&N as backup for times when radio signals were lost. The Apollo CM’s IMU was paired to a stargazing sextant for verifying alignment or correcting for platform drift and, with the addition of Apollo Guidance Computer, the entire assembly became the Apollo Primary Guidance, Navigation, and Control System (PGNCS).
Figure 4 shows the Apollo CM’s PGNCS and the IMU contained within, along with an Analog Devices ADIS16488 inertial sensor module for comparison. The ADIS16488 represents an industrial-grade IMU assembly offering ten degrees of situational awareness, 3-axis each for acceleration and angular rate, along with a 3-axis magnetometers and pressure sensing. Size, weight, cost, power, and feature-set are all dramatically improved over traditional IMU approaches.
In data acquisition for location/position sensing, a revolution has come via silicon MEMS technology. For consumer products, gyros and accelerometers are available in thumbnail-sized packages and at bargain-basement prices. Sub-$100 GPS systems can now perform dead reckoning by interpolating location when GPS signals are lost. Cameras can automatically compensate for shake, producing much clearer images. Everyday smartphones are now orientation-aware and motion-sensitive, opening up whole new functions and use modes. Positional DAQ is now an “everyman’s technology”, available to almost any product design where it makes sense to include it.
From past to future
How could we possibly put men on the moon with such limited electronics resources? In a nutshell, it took courage, ingenuity, conservative design in spots, reliance on the mechanical at times, and a willingness to push technology boundaries in critical areas.
Despite the limitations and some serious setbacks along the way, the Apollo program was a success, and data acquisition was a critical dimension in the systems management efforts therein.
The sensor and mixed-signal electronics technologies that form the backbone of DAQ have advanced dramatically along with - and inside of - the digital silicon revolution over the 40 years since our visits to the lunar surface. Apollo-era data acquisition technologies got us to the moon – and back – nine times, but imagine how the space ships of tomorrow will benefit from flight-hardened versions of today’s silicon-based sensors.
Power consumption and weight are among the biggest enemies in space travel, and both are improved dramatically by application of the silicon innovation engine to spacecraft electronics.
Today’s unmanned missions to Mars are already leveraging the many advances in silicon-based sensors and instrumentation. As the commercial industry begins to take up the mantle for space exploration, surely we will see even more powerful application of these DAQ components in the areas of spacecraft design and space flight automation.
To those who succeed in space ‘faster, better, lighter, cheaper’ will not be a mantra for just the consumer electronics world.
References:
- NASA History Program Office, “The Apollo Program”
- “Moonport: A History of Apollo Launch Facilities and Operations”, Charles D. Benson and William Barnaby Faherty, NASA SP-4204, 1978
- Digital Apollo; David Mindell, 2008, MIT Press, ISBN 9780262134972
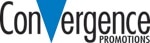
免责声明:各个作者和/或论坛参与者在本网站发表的观点、看法和意见不代表 DigiKey 的观点、看法和意见,也不代表 DigiKey 官方政策。