Building a Vibration Sensor for Industrial Systems
投稿人:DigiKey 欧洲编辑
2014-03-13
Monitoring the vibration in industrial systems can provide invaluable data on the health of the equipment and allow for cost-saving pre-emptive maintenance, but there are many different ways to build such a system. Simple piezoelectric vibration sensors can be used but need data acquisition and signal processing to capture and analyze the data. The increasing popularity of micromachined (MEMS) sensors used as accelerometers in applications such as airbags in cars and drop sensors for smartphones and tablets has led to the cost propping substantially and opens up the use of these sensors in industrial applications.
These MEMS accelerometers are built in standard CMOS process technology, allowing them to be manufactured in high volume, but also allowing integration alongside the sensor. This has led to single-package devices that can provide measurement of vibration along all three axes, along with complex signal processing in both the time and frequency domains. This allows designers to easily develop sensor systems that collect a wide range of data and identify many different types of failure mechanisms, alerting the operator to potential problems in all kinds of industrial equipment to allow for cost-saving pre-emptive maintenance.
Most vibrations of industrial machinery contain frequencies below 1 kHz, but the relevant signal components often exist at higher frequencies, and this is a key consideration for the choice of the vibration sensor. If the running speed of a rotating shaft is known, the highest frequency of interest may be a harmonic of the product of the running speed and the number of bearings supporting the shaft, and problems will show up around these harmonics. However, for other systems the frequencies of a failure mode may well be unknown, so more complex signal analysis can be required.
The type of equipment determines the high-frequency requirement of the application, and so determines the choice of sensor to provide an adequate frequency range while also meeting sensitivity and amplitude range requirements. Sensors with lower frequency ranges tend to have lower electronic noise floors, increasing the sensor's dynamic range. This factor may be more important to the application than the high-frequency measurements.
One example of a highly-integrated MEMS accelerometer sensor is the ADIS16228 iSensor from Analog Devices. This is a complete vibration sensing system that combines tri-axial acceleration sensing with advanced time and frequency domain signal processing. The time domain signal processing includes a programmable decimation filter and selectable windowing function, while the frequency domain processing includes a 512-point, real-valued FFT for each axis, along with FFT averaging, which reduces the noise floor variation for finer resolution. The 14-record FFT storage system offers users the ability to track changes over time and capture FFTs with multiple decimation filter settings.
The 20.48 kSPS sample rate and 5 kHz flat frequency band provide a frequency response that is suitable for many machine health applications. An internal clock drives the data sampling and signal processing system during all operations, which eliminates the need for an external clock source. The data capture function has three modes that offer several options to meet the needs of many different applications and a real-time mode provides direct access to streaming data on one axis. The SPI and data-buffer structure provide convenient access to data output. The ADIS16228 also offers a digital temperature sensor and digital power supply measurements to provide diagnostics on the sensor node itself.
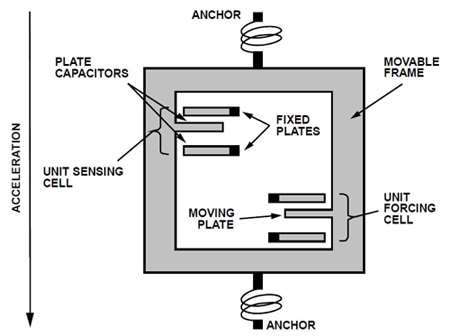
Figure 1: The mechanical element of the ADI tri-axis MEMS vibration sensor.
Digital vibration sensing in the ADIS16228 starts with a MEMS accelerometer core on each axis. This translates linear changes in velocity into a representative electrical signal, using a micromechanical system like the one shown in Figure 1. The mechanical part of this system includes two different frames (one fixed, one moving) that have a series of plates to form a variable, differential capacitive network. When experiencing the force associated with gravity or acceleration, the moving frame changes its physical position with respect to the fixed frame, which results in a change in capacitance. Tiny springs tether the moving frame to the fixed frame and govern the relationship between acceleration and physical displacement. A modulation signal on the moving plate feeds through each capacitive path into the fixed frame plates and into a demodulation circuit, which produces the electrical signal that is proportional to the acceleration acting on the device.
Figure 2 shows a simplified block diagram for the ADIS16228 with the signal-processing stage integrating the time domain data capture, digital decimation/filtering, windowing, FFT analysis, FFT averaging, and record storage.
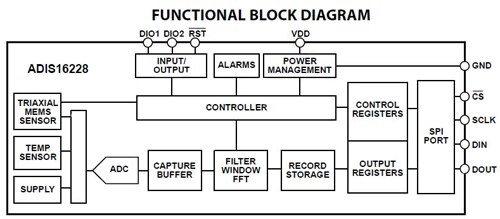
Figure 2: Simplified sensor signal processing block diagram for the ADI16228.
The user registers (which include both the output registers and the control registers, as shown in Figure 2) manage user access to both sensor data and configuration inputs. Each 16-bit register has its own unique bit assignment and two addresses: one for its upper byte and one for its lower byte. The data collection and configuration command uses the SPI, which consists of four wires. The chip select (CS) signal activates the SPI interface, and the serial clock (SCLK) synchronizes the serial data lines. Input commands clock into the DIN pin, one bit at a time, on the SCLK rising edge. Output data clocks out of the DOUT pin on the SCLK falling edge. When the SPI is used as a slave device, the DOUT contents reflect the information requested using a DIN command.
Dual-memory structure
The user registers provide addressing for all input/output operations in the SPI interface to simplify the interface to the sensor node using a dual-memory structure. The controller uses SRAM registers for normal operation, including user-configuration commands while the Flash memory provides non-volatile storage for control registers that have Flash backup. Storing configuration data in the Flash memory requires a manual Flash update command so that when the device powers on or resets, the Flash memory contents load into the SRAM, and the device starts producing data according to the configuration in the control registers.
The ADIS16228 uses a SPI for communication, which enables a simple connection with a compatible, embedded processor platform. The factory default configuration for DIO1 provides a busy indicator signal that transitions low when an event completes and data is available for user access. The DIO_CTRL register is used to reconfigure DIO1 and DIO2, if necessary.
User control registers govern most of the internal operations. The DIN bit sequence provides the ability to write to these registers, one byte at a time. Some configuration changes and functions require only one write cycle. For example, setting GLOB_CMD[11] = 1 (DIN = 0xBF08) starts the manual capture sequence. The manual capture starts immediately after the last bit clocks into DIN (16th SCLK rising edge). Other configurations may require writing to both bytes.
The recording-mode selection establishes the data type (time or frequency domain), trigger type (manual or automatic), and data collection (captured or real time). The REC_CTRL1[1:0] bits provide four operating modes: manual FFT, automatic FFT, manual time capture, and real time. After setting REC_CTRL1, the manual FFT, automatic FFT, and manual time-capture modes require a start command to start acquiring a spectral or time domain record. There are two start command options in this mode: SPI and I/O. The SPI trigger involves setting GLOB_CMD[11] = 1 (DIN = 0xBF08). The I/O trigger involves using DIO_CTRL to configure DIO1 or DIO2 as an input trigger line.
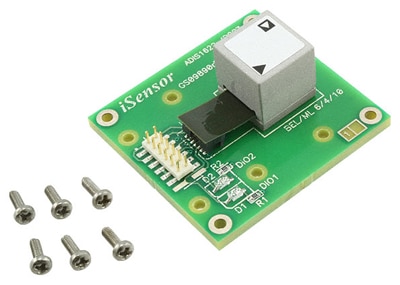
Figure 3: The ADIS16228 mounted on its evaluation board.
The MEMSIC MXR7250VW is a low-cost, dual-axis accelerometer built on a standard, submicron CMOS process that uses an alternative approach. It measures acceleration with a full-scale range of ±5 g and a sensitivity of 250 mV/g.
The MXR7250VW provides a g-proportional ratiometric analog output above/below the zero-g point at 50% of the supply voltage. The typical noise floor is 0.6 mg/Hz, allowing signals below 1 mg to be resolved at 1 Hz bandwidth. The 3 dB rolloff of the device occurs at 27 Hz.
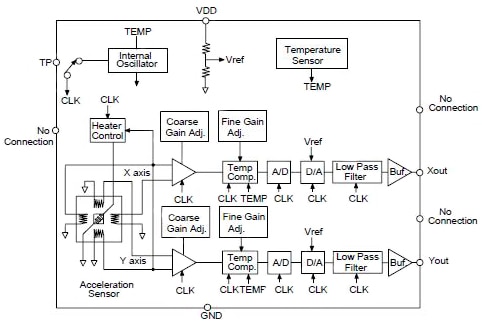
Figure 4: Block diagram of the MXR7250VW dual-axis accelerometer.
The MXR7250VW is packaged in a hermetically-sealed LCC surface-mount package (5.5 mm x 5.5 mm x 2.7 mm height), and the package can be used as both XY and XZ sensing with an operational temperature of -40°C to +95°C.
Memsic’s accelerometer technology allows for designs from ±1 g to ±70 g with custom versions available above ±70 g. It can measure both dynamic acceleration such as vibration and static acceleration such as a gravity drop. The design is based on heat convection and requires no solid proof mass and operates like other accelerometers having a proof mass, except it is a gas in the sensor.
With this approach a single heat source, centered in the silicon chip, is suspended across a cavity. Equally spaced aluminum/polysilicon thermopiles (groups of thermocouples) are located equidistantly on all four sides of the heat source (dual axis). Under zero acceleration, the temperature gradient is symmetrical about the heat source, so that the temperature is the same at all four thermopiles, causing them to output the same voltage. Acceleration in any direction will disturb the temperature profile, due to free convection heat transfer, causing it to be asymmetrical. The temperature, and hence voltage output of the four thermopiles will then be different.
The differential voltage at the thermopile outputs is directly proportional to the acceleration. There are two identical acceleration signal paths on the MXR7250VW, one to measure acceleration in the X-axis and one to measure acceleration in the Y-axis. Using the convection approach eliminates particle problems associated with other MEMS designs and provides shock survival greater than 50,000 g, leading to significantly-lower failure rates and lower loss due to handling during assembly and at the customer field application.
Due to the standard CMOS structure of the MXR7250VW, additional circuitry can easily be incorporated into custom versions for high-volume applications.
The API Technologies XL203A is a rugged, small and accurate tri-axial analog accelerometer for measurements in harsh environments. The device has a built-in power regulation, and the voltage output is directly proportional to the acceleration along the axes. Each DC-coupled sensor output is fully scaled, referenced, and calibrated. The XL203A has a machined aluminum case with a black anodized finish per MIL-A-8625, and the shielded cable has a high-temperature PVC jacket and Teflon-insulated conductors. Each XL203A comes with a calibration certificate listing sensitivity and offset, as well as the on-axis and transverse alignment parameters needed to ensure rapid and efficient system implementation. There are other, simpler ways of measuring the vibration with a piezoelectric crystal such as the ACH-01 accelerometer from Measurement Specialties.
The ACH-01 (Figure 5) is a robust, general-purpose, linear, single-axis accelerometer featuring buffered electronic output to simplify the interface of a data capture subsystem. It has a sensitivity of 10 mV/g and a lower frequency limit (-3 dB) of 2 Hz. The upper frequency limit (+3 dB) is 20 kHz, giving enough room for harmonics to be detected, and this gives a dynamic range of ±150 g with a linearity of 0.1%.
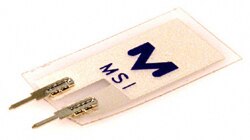
Figure 5: The ACH-01 single-axis accelerometer.
This can be interfaced to a low-cost 12-bit analog-to-digital converter and output via the I²C or SPI interface to a microcontroller or digital signal processor. This can then perform the signal analysis to monitor the equipment.
The vibrations themselves can even be used to generate power to drive the accelerometer. Piezoelectric devices such as the Mide V25W do not monitor the vibrations but convert the energy of the vibrations to power other sensors. By matching the resonant frequency of the healthy equipment to the sensor, the peak power can be generated for other sensors and a wireless link. This can be done by an FFT analysis, or by adjusting the positioning of the sensor until it generates the peak power. This then allows the sensors to be placed in inaccessible areas of the machinery as changing batteries is not necessary. This provides even more visibility of the performance of the equipment.
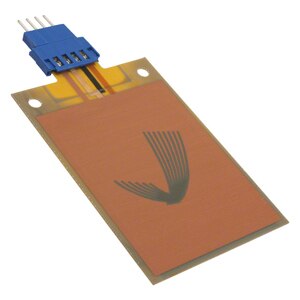
Figure 6: The Mide V25W piezoelectric sensor can be used to harvest vibrational energy to power other vibration sensors.
Conclusion
The advent of low-cost CMOS manufacturing for MEMS has created a range of accelerometers that can be used to monitor the vibration of equipment to give early warning of problems. Many accelerometers are used for detecting static movements such as a drop, but there are devices available with a range beyond the 1 kHz vibrations of the equipment being monitored. Being able to analyze these harmonics can give clues as to the likely failure mechanism of the equipment and allow pre-emptive maintenance to be carried out.
The use of CMOS is also allowing the data conversion and the signal processing to be integrated into a single package, saving space and design complexity. Coupled with the use of a piezoelectric energy-harvesting device, the monitoring of vibration can be increasingly effective in preventing the break-down of vital equipment and ensuring the maximum possible availability.
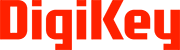
免责声明:各个作者和/或论坛参与者在本网站发表的观点、看法和意见不代表 DigiKey 的观点、看法和意见,也不代表 DigiKey 官方政策。