Build a Redundant Power Bus for Reliable UAV Operation
投稿人:DigiKey 欧洲编辑
2016-11-15
A key criterion for the success of the future market for unmanned aerial vehicles (UAVs), otherwise known as drones, is reliability. We expect them to carry parcels or perform surveillance over populated areas. Sudden, unexpected power loss is unacceptable for airborne drones because of the risk of injury to bystanders when they fall to the ground. Redundancy is therefore an important part of the design architecture, not least for the power delivery subsystem given its role not just in enabling the guidance systems but the rotor blades themselves.
Possible architecture that improves reliability through redundancy is to use two or more separate battery packs, each feeding a separate DC/DC converter. If one battery or converter fails, the others can take over, albeit with a greatly reduced flying time. However, this should be sufficient to bring the UAV to a controlled landing.
The N+1 architecture has been shown to be a cost-effective approach in larger systems as a way of providing fault tolerance. The probability of more than one power supply failing at once under normal operating conditions is extremely low, so the addition of one additional power supply to an array of two or three running in current-sharing mode does not significantly increase cost. In practice, dual-redundancy a 1+1 architecture – is likely to be favored in UAV designs because of size and weight concerns.
In a dual-redundant architecture, it is important to select appropriate DC/DC converters because of the change in current load if one side fails. Often converters demonstrate improvements in efficiency at higher loads, peaking at close to full load. Under normal conditions, each DC/DC converter will operate at less than 50 per cent of load capacity, which may mean a drop in efficiency. Multiphase converter architectures can help deal with the problem.
Such a design uses multiple switching circuits to perform conversion at full load. As the load demand drops, phases that are no longer in use can be turned off while those remaining active operate at close to peak efficiency.
In a power circuit that uses multiple converters, it is not enough to simply wire the outputs feeding the load together. One problem is that the two converters will not split the current demand equally and it presents problems for load regulation. If a power supply goes offline, short-circuit faults may develop, causing the entire system to fail. An ORing device is used to protect the system against power-sharing problems.
In its simplest form, the ORing device is a diode. By allowing current to flow in one direction only, the ORing diode isolates the fault from the redundant bus, allowing the system to keep running using the remaining power supplies. By its nature, a diode will disconnect an input power source short-circuit instantaneously. However, because of efficiency consideration, a conventional diode may not be the most suitable choice, particularly in terms of energy efficiency. In an ORing application, a diode will spend most of its operational life in forward-conduction mode, dissipating power and heat due to the diode’s inherent voltage drop.
Replacing the ORing diode with an N-channel MOSFET calls for a small increase in the level of complexity, but the greater conductivity and low voltage drop of the MOSFET improves efficiency and the possible need for cooling – so saving on the additional weight, albeit small, of a heatsink. In fact, active ORing solutions can show a 10x reduction in power loss versus diodes.
There is a tradeoff with active ORing. When turned on, unlike a diode, it allows current to flow in either direction between source and drain. If an input power source fails due to a short circuit, a large reverse current can be induced and the MOSFET will pass the current as long as it switched on. The redundant bus cannot be exposed to an input short circuit for a prolonged period of time or the bus voltage will drop and cause the system to fail. Therefore, an ORing system based on a MOSFET must be capable of fast detection of reverse current fault conditions.
A controller circuit senses the voltage across the source and drain to determine the magnitude and polarity of current flow through the MOSFET. A gate-control pin switches the MOSFET between conducting and non-conducting states based on the controller’s algorithm. The resulting behavior is that of a rectifier – the source and drain pins of the MOSFET act as the anode and cathode pins of a diode, respectively.
The most critical parameter is the reverse current threshold: when exceeded it provides an indication of an input power source failure. This threshold needs to be at a level that allows for consistent and fast detection of a fault. The response time to the fault needs to be fast to limit the amount of reverse current and potential voltage droop on the redundant bus.
Figure 1: Use of an ORing controller on the power bus with a TPS241x series device.
Although discrete circuitry can control the N-channel MOSFET, off-the-shelf solutions such as the Texas Instruments TPS2412 and TPS2413 are available that provide rapid response to reverse current flow. The TPS2412 and TPS2413 differ primarily in the control loop that sets the state of the MOSFET. The TPS2412 provides a gentler turn-on and turn-off strategy for slower changes in input voltage that also reduces the tendency to perform on-off cycling at light loads that can happen with simpler comparator-only circuits. This can make the MOSFET appear to have a high resistance at light load when the regulation is active. A momentary output voltage droop occurs when a large step load is applied from a light-load condition. The TPS2412 tends to be more suited to situations where it can be used on a mid-rail bus that feeds a tree of downstream point-of-load regulators. The TPS2413 turns the MOSFET on if the voltage across it is greater than 10 mV and performs a rapid turnoff if the threshold turns negative. For turnoff to be implemented, the threshold must be negative, which may not always be the case at very light loads. However, in flight, the UAV is unlikely to be in that situation. Step loads from a light-load condition are handled without a significant voltage droop, which helps to maintain regulation on the output bus.
Figure 2: Typical use of the Cool-ORing device.
An alternative is to opt for a packaged device that packages the MOSFET and controller together, such as the Cool-ORing series of devices from Vicor. These combine a high-speed ORing MOSFET controller and a very low on-state resistance MOSFET in a 5 x 7 mm land-grid-array (LGA) package. These packages achieve as low as 1.5 μΩ typical on-state resistance while enabling up to 24 A of continuous load current over a wide range of operating temperatures. The design can be used in low voltage, high side applications and, by packaging the support circuitry together, can save board space compared with discrete solutions. The components offer responses as fast as 80 ns to fault conditions.
By providing high-efficiency support for redundant behavior, MOSFET controllers in ORing architecture represent part of the solution for building reliable UAVs. Combined with high-efficiency DC/DC converters will help keep them airborne for longer.
Figure 3: Comparison of power efficiency between traditional diode and MOSFET controller, using the Cool-ORing family as an example.
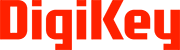
免责声明:各个作者和/或论坛参与者在本网站发表的观点、看法和意见不代表 DigiKey 的观点、看法和意见,也不代表 DigiKey 官方政策。