Using AMP DC/DC Converters to Achieve True Digital Power Interoperability
投稿人:DigiKey 北美编辑
2017-01-11
The adoption of digital power techniques is almost universal, yet achieving true interoperability between devices from different manufacturers to enable multi-sourcing of products has remained elusive. This ability to have multiple sources for digitally-controlled DC/DC converter modules is critical for designers of systems for telecom, datacom, and datacenter applications, where both efficiency and design longevity are important requirements.
Digital power based on PMBus and its SMBus communications structure has allowed designers to leverage software-based power control to achieve high levels of overall system efficiency. But PMBus didn’t go deep enough. It has taken efforts like the Architects of Modern Power (AMP) Group to realize a level of device interoperability that will allow a converter from one company to be considered a second source from another company. This ensures supply-chain continuity, rapid replacement of products in the field, and provides the necessary assurance of design longevity.
This article will quickly look at PMBus before introducing a digitally-controlled DC/DC converter and how to use it. It will conclude with a look at interoperable devices and the next steps for multi-sourced DC/DC converters.
What are PMBus and SMBus?
Defined by the Digital power Open Standards Alliance (DOSA), PMBus is exactly what it was intended to be: A flexible, powerful tool for digital power system management that provides a standard way to communicate with power converters over a digital communications bus. It supports both embedded and discrete converters, as well as complete and purchased converters. It comes with high-level features needed by nearly all users, while also including application-oriented feature sets to control costs.
PMBus is a variant of the System Management Bus (SMBus), a simple, singled-ended, two-wire bus derived from I2C, but with more defined voltage levels and timing, as well as clock, data and instructions.
The specification has two parts: Part 1 is Transport, which deals with addressing and hardwired signals, such as CONTROL signal (On/Off). Part II is Command Language, including configuration, control, status monitoring, fault management and information storage.
While DOSA liked SMBus and its I2C roots, it added features to address I2C’s shortcomings. For example, to prevent a slave device from hanging the bus, PMBus Timeouts force a device reset. To retrieve device information by polling, the PMBus SMBALERT# line acts as an interrupt, while Automatic Bitwise provides arbitration of simultaneous requests. PMBus also defines fault tolerance, maximum bus capacitance (400 pF), and the maximum number of devices on one bus. Over 100 device addresses are available.
That said, not all PMBus devices will support all commands: support is based on application and price point. There are 32 Command Codes for PMBus device makers to support user inventory and configuration data, such as digital control-loop coefficients. Then there are 45 Command Codes reserved for PMBus device makers to implement manufacturer-specific commands. This opens the door to variations between manufacturers and a lack of uncertainty and ambiguity regarding command-level interoperability between devices.
Typically, parameters monitored include input and output voltage and current, hold-up capacitor voltage, temperature (up to 3 sensors), fan speed, duty cycle, and switching frequency.
There are protections built in, such as packet error checking to protect against corrupted transmissions, and a Write Protect pin and WRITE_PROTECT command to prevent unwanted or unintentional data changes (Figure 1).
Figure 1: The PMBus connections specify Write_Protect, Control_Signal, and SMBALERT# signals as being optional, while the hardwired Physical_Address pins are mandatory. (Image source: System Management Interface Forum)
The latest revision, PMBus 1.3, brought about many general improvements. Primary among those are adaptive voltage scaling (AVS). This lets you control processor voltages, both statically and dynamically. The group also added high-speed communications to reduce latencies.
PMBus is widely adopted by IC and power supply manufacturers and has done much to shorten time to market, improve interoperability and reduce complexity. However, three companies: Murata, Ericsson Power Modules, and CUI, Inc. concluded it did not go deep enough into the various physical and hardware aspects to enable multi-sourcing and standard programming interfaces for digital power supply components such as DC/DC converters.
Architects of Modern Power (AMP) enables multi-sourcing
With increasing IP traffic comes the increasing application of digitally-controlled DC/DC converters and point-of-load (PoL) regulators for high-end processors in telecom, datacom, and datacenters. This means you need to be assured of multiple sources for critical, high-efficiency power components to ensure design continuity through supply-chain stability. Essentially, you must be able to swap high-efficiency parts from one company with similar or better parts from another if one part fails or a company stops supporting that line.
This was the impetus behind the formation of the Architects of Modern Power (AMP) Group by Murata, Ericsson, and CUI. Their goals include establishing common mechanical and electrical specifications for their products, standardization of monitoring, control and communications functions, and to create common configuration files for plug-and-play interoperability between products from each company.
The first two groups of standards: Digital Point of Load and Advanced Bus Converter, were announced in November of 2014, and have a growing list of standards defined under each (Figure 2). Devices within each group have matching feature sets and compatible configuration files.
Digital Point of Load Modules | ||||
---|---|---|---|---|
Standards | CUI | Ericsson | Murata | |
picoAMP | picoAMP-6 | - | BMR461 | OKDL-T/6 |
picoAMP-12 | - | BMR461 | OKDL-T/12 | |
picoAMP-18 | - | BMR461 | OKDL-T/18 | |
microAMP | microAMP-20 | - | BMR463 | OKDX-T-20 |
OKDY-T-20 | ||||
OKDH-T-20 | ||||
microAMP-25 | NDM2Z-25 | BMR463 | OKDX-T-25 | |
OKDY-T-25 | ||||
OKDH-T-25 | ||||
megaAMP | megaAMP-40 | - | BMR464 | OKDX-T-40 |
OKDY-T-40 | ||||
OKDH-T-40 | ||||
megaAMP-50 | NDM2Z-50 | BMR464 | OKDX-T-50 | |
OKDY-T-50 | ||||
OKDH-T-50 | ||||
teraAMP | teraAMP-90 | NDM3Z-90 | BMR465 | - |
Advanced Bus Converters | |||
---|---|---|---|
Standards | CUI | Ericsson | Murata |
ABC-ebAMP | NEB-D | BMR457 | DBE |
NEB-N | |||
ABC-qbAMP | NQB-D | BMR456 | DBQ |
NQB-N |
Figure 2: As of December 2016, the AMP Group has defined two main standards groups under which are a total of 34 products sorted under 10 standards. (Source: AMP Group)
For Digital Point of Load, the standards are: PicoAMP (6 to 18 A), microAMP (20 to 25 A), megaAMP (40 to 50 A), gigaAMP (60 A) and teraAMP (90 to 120 A) with gigaAMP being the most recently announced standard (September 2016). All have defined horizontal and vertical configurations.
The Advanced Bus Converter Standards are ABC-ebAMP (264 to 300 W), ABC-qbAMP (420 to 468 W), and the most recently announced standard (October 2016) HPABC-qbAMP (1000 W). All come with defined digital and analog configurations.
Applying AMP products
A high-end processor core for a telecom switching center or a video server may have an instantaneous PoL current requirement of up to 150 A or higher, while at the same time operating at 1 V or lower. These are extreme cases, but are becoming more common as processing and data requirements increase. It’s very likely that if you’re a good power designer you will be able to design a solid discrete power supply delivering 6 A across five or ten layers of a pc board. However, good experienced power designers that can meet the layout, noise-immunity and thermal management requirements are becoming rare, while at the same time, currents are increasing and 20-layer pc boards are becoming more common.
In many cases, the design of the power supply is best left to dedicated experts within companies like CUI which has a digital DC/DC module, the NDM3Z-90, which is compatible with the AMP Group’s PoL teraAMP line-up (Figure 3). The non-isolated module gives you 90 A at between 0.6 to 1.8 VDC, from an input of 7.5 to 14 VDC. Your package options are SMT, DIP, or SIP, measuring 50.8 x 19.05 x 10 mm (SMT, DIP) or 50.8 x 9.51 x 19.05 mm (SIP).
Figure 3: CUI’s NDM3Z-90 PoL converter can be used in parallel mode for current sharing by connecting the DDC and SYNC pins. Up to four devices can be paralleled. (Image source: CUI, Inc.)
To help compensate quickly for transient load variations, the NDM3Z-90 comes with adaptive algorithms and cycle-by-cycle charge management. We’ll discuss these in more detail later.
Digital power modules use a configuration file to set functionality and performance parameters, and the NDM3Z-90 is no different. The standard wide range configuration is designed to fit most application needs, so off the shelf, you can take it in its default configuration and most likely it will meet your input voltage, output voltage and load requirements. However, if you’d like to implement features such as current sharing, you need to use the PMBus interface to tweak the configuration file, which is stored in non-volatile memory (NVM).
This configurability speaks to the advantage of digital power in that it works closely with the OS to give flexibility from development through production and out in the field.
The NVM itself is actually split into two parts: The Default NVM and the User NVM. The Default is pre-loaded with CUI factory default values and is write protected. If you need to reset or are new to digital power configuration files, this provides some headroom for learning. Defaults can be restored using the command: RESTORE_DEFAULT_ALL
.
The USER NVM is also loaded with factory defaults, but is writable and customizable over the PMBus interface. The STORE_USER_ALL command will store the changed parameters to the User NVM.
The module is compatible with PMBus Ver. 1.2, and per the SMBus specification, you need to use passive pull-up resistors for the SCL, SDA, and SLRT pins. SLRT is used for monitoring faults. For a guaranteed rise time, select the pull-ups using the formula:
Where T is the rise time, Rp is the pull-up resistor value and Cp is the bus loading. The maximum allowed bus load is 400 pF. You should tie the pull-up to a 2.5 to 5.2 V external power supply, but note that this supply needs to be present prior to or during power-up. If that’s not possible, you can use a voltage divider instead of an external supply, but note that the resistance in the equation corresponds to a parallel connection of the resistors forming the voltage divider.
To set the PMBus address, you need to connect a 1% tolerance resistor between the SA and PREF pins (Figure 4).
|
|
Figure 4: A PMBus module’s address is set in hardware using a 1% tolerance resistor placed between the SA and PREF pins. (Image source: CUI Inc.)
Fault monitoring
An important enabling feature of digital power and power control is fault monitoring, which you can accomplish using the SLRT pin on the NDM3Z-90. The pin will be asserted low when pre-configured fault or warning conditions occur (Figure 5).
|
Figure 5: In response to the SLRT signal, you can read a number of status commands to find out what fault or warning condition occurred. (Image source: CUI, Inc.)
SLRT will stay low until faults and/or warnings are cleared by the CLEAR_FAULTS command, or until the output voltage has been re-enabled. You can mask which fault conditions should not assert the SLRT pin using the command MFR_SMBALERT_MASK.
Control loops and protection
Closed-loop feedback in a converter compensates for sudden changes in output current or input voltage and the loop should be matched to your output filter. While the advantage of digital control is that the loop parameters can be altered without changing components, optimization to your output filter can still be difficult due to parasitic impedances in the pc board, as well as artifacts introduced by the filter components themselves.
To help you account for this, the NDM3Z-90 uses dynamic loop compensation (DLC). This uses algorithms to identify the characteristics of any output filter by injecting a known excitation signal, measuring the output, and compensating accordingly.
The NDM3Z-90 comes with the classic protection mechanisms, such as over and undervoltage protection, over and undercurrent protection, and remote sensing. Along with parallel operation for current sharing, it also has pre-bias startup capability, voltage tracking, output voltage sequencing, and a Digital DC Bus (DDC).
The DDC is particularly interesting as it allows communication between products. For example, if you set up Broadcast Control, the DDC can be used to broadcast an output voltage enable or a setting of an output-voltage level to other devices in the group. When a configured device receives a PMBus OPERATION command or VOUT_COMMAND, it will broadcast it. Incidentally, you can configure Broadcast Control using the PMBus command: DDC_GROUP.
Thermal management and layout
The NDM3Z-90 is cooled by conduction from the pins to the board, as well as by convection. However, over-temperature protection (OTP) lets you set thresholds and set how the converter responds. For example, it can respond by completely shutting down until the fault is cleared by the PMBus command CLEAR_FAULTS.
Alternately, you can set it so it shuts down while the temperature is above a warning threshold and turn on automatically when the temperature falls again. This is the default setup, and can be readily changed using PMBus commands.
AMP Group compatibility
It should be noted from Figure 2 that not every converter has a corresponding device from the AMP Group members. In the case of the NDM3Z-90, its match is the Ericsson BMR465. However, Murata’s OKDY-T/25 is interoperable with Ericsson’s BMR463 and CUI’s NDM2Z-25.
Conclusion
Digital power control with PMBus has helped designers develop flexible and adaptable systems that are power efficient and cost effective. With more in-depth compatibility and device interoperability efforts like AMP, one can also be confident of design and supply-chain continuity from at least two other companies. This is critical as designs move rapidly and become key elements of the telecom, datacom, datacenter and IoT infrastructure.
Looking forward, the AMP Group continues to work on a single GUI that designers can use to program any AMP-compatible device, setting up the next stage of design continuity and simplification. It is also looking at what’s required to meet the developing need for 54 to 1 VDC conversion for datacenter applications.
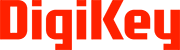
免责声明:各个作者和/或论坛参与者在本网站发表的观点、看法和意见不代表 DigiKey 的观点、看法和意见,也不代表 DigiKey 官方政策。