通过路测的 GMSL 相机驶入新市场
投稿人:DigiKey 北美编辑
2024-10-24
由于汽车制造商对可靠性和性能要求严格,以及在恶劣电子环境条件下对快速数据传输速率的需要,为汽车应用开发的技术经常转移到其他市场。正因如此,千兆位多媒体串行链路 (GMSL™) 相机在自动化和机器人、智慧农业、数字医疗、航空电子、机器人轴以及零售和仓库库存管理等领域的视觉应用中找到了现成的市场。
Analog Devices GMSL 最初是为解决车载高速视频和数据传输应用而推出的,它是一种被广泛采用并经过验证的成熟技术,可将高速视频链路的性能提升到新的水平,并通过单根电缆实现多数据流传输。
视觉应用需要非常大的数据流,以确保高质量的视频。全高清图像由 1080 行 x 1920 列组成。这相当于 200 万像素,每个像素由一个红色、绿色和蓝色元素组成,因此共有 600 万个元素。每个元素代表 8 比特数据,因此每帧的数据量接近 50 Mbps。以每秒 60 帧的速度计算,一台相机所需的数据传输速率超过 3.5 Gbps。
第一代 GMSL 于 2008 年推出,利用低压差分信令 (LVDS) 标准提供最高 3.125 Gbps 的并行数据下行链路速率。特别适合用来传输来自多个相机系统、高级驾驶辅助应用系统 (ADAS) 以及用的越来越多的车载高清平板显示器的数据。
第二代 GMSL2 于 2018 年推出,将数据传输速率提高到 6 Gbps,并支持更多标准的高速视频接口,包括 HDMI 和 MIPI 接口标准,后者是用于消费类和车载相机的常用图像传感器接口。这些进步适应了全高清 (FHD) 显示屏和分辨率高达 8 MP 的相机的需要。
最新一代 GMSL3 可通过单根电缆传输高达 12 Gbps 的数据,支持多个 4K 分辨率的数据流、多个显示器的菊花链连接,以及多个相机(如位于车辆前部、后部和侧面的相机)的聚合,以提供 360° 的观察能力。如今,越来越多的汽车制造商在后视镜和侧视镜上加装相机,利用面向前方和后方的相机来避免碰撞,并利用车内相机来监控驾驶员和乘客的安全。GMSL3 可以汇总来自多个视频的馈送以及激光雷达和雷达的数据。
随着相机尺寸缩小到 CMOS 传感器的水平,它们可以以低成本、低功耗的方式产出曾经被认为是不可思议的质量。图像传感器有数百万个接收器元件,每个接收器元件将测量值转换成数字值,连同同步信息一起通过并行接口的串行数据通道流式传输出去。
GMSL2 和 GMSL3 均采用 MIPI 接口标准,能够让设计人员和供应商将各种图像传感器用于 GMSL 相机。
GMSL 对 GigE
刚开始研究视觉应用的工程师很快就会面临这样一个决定,是使用 GMSL 还是千兆位以太网 (GigE) 视觉技术。GigE 之所以在工业应用中得到广泛应用,主要是因为它依赖于以太网基础设施和标准。
如今,2.5 GigE、5 GigE 和 10 GigE 的 GigE Vision 相机已经普遍得到应用,而最先进的 100 GigE 相机可以使用高达 100 Gbps 的数据速率。GMSL 旨在通过同轴电缆或屏蔽双绞线传输数据,传输距离最远为 15 米,而 GigE 的传输距离则为 100 米,不过在某些条件下这两个极限都可能有所突破。
每种技术都能通过同一根电缆传输数据和电力:GMSL 使用同轴电缆供电 (PoC),因此视频、音频、控制、数据和电能均可在单个通道上传输。大多数 GigE Vision 应用都依赖以太网供电 (PoE) 来实现 4 对以太网,或较少地使用数据线供电 (PoDL) 来实现单对以太网 (SPE)。
系统要求和应用需求将决定哪种视觉技术最合适。例如,GigE Vision 可为单相机应用带来一些优势,特别是当它们直接连接到带有以太网端口的 PC 或嵌入式平台时。
当使用多个相机时,GigE Vision 应用需要使用专用以太网交换机、带有多个以太网端口的网络接口卡 (NIC) 或以太网交换机 IC。这种切换要求可能会降低最大总数据传输速率,并在相机和终端设备之间带来不可预测的延迟,而 GMSL 则提供了一种更简单、更直接的架构。
GigE Vision 设备可支持更高分辨率和更高帧率(或两者同时支持),并提供额外的缓冲和压缩。GMSL 设备不提供帧缓冲和处理功能,因此分辨率和帧率取决于图像传感器在链路带宽内所能提供的支持。工程师需要在分辨率、帧率和像素位深之间进行简单的权衡。
GMSL 简化了高速视频架构
GigE Vision 相机通常使用一个信号链,其中包括图像传感器、处理器和以太网物理层 (PHY)(图 1)。来自传感器的原始图像数据由处理器转换成以太网帧,通常依靠压缩或帧缓冲来适应所支持以太网带宽的数据速率。
图 1:GigE Vision 相机传感器侧关键信号链组件示意图。(图片来源:Analog Devices, Inc.)
GMSL 相机信号链采用串行器/解串器 (SerDes) 架构,避免使用处理器(图 2)。相反,图像传感器并行数据由串行器转换为高速串行数据流。在后端,解串器将串行数据转换回并行形式,供电子控制单元(ECU)片上系统 (SoC) 处理。
图 2:与 GigE Vision 相比,GMSL 相机在传感器侧采用了更简单的信号链架构。(图片来源:Analog Devices, Inc.)
GMSL 相机架构使设计低功耗的小型相机变得更加简单。串行器可通过标准 MIPI CSI-2 接口直接连接相机,并通过 GMSL 链路传输分组数据。
典型的主机设备是一个定制的嵌入式平台,带有一个或多个解串器,通过 MIPI 发射器以与图像传感器 MIPI 输出相同的格式传输图像数据。定制设计需要新的 GMSL 相机驱动程序,但如果已有图像传感器驱动程序,则只需使用几个配置文件寄存器或进行寄存器写入,就能实现从相机到控制单元的视频流。
GMSL 组件
ADI 提供全系串行器和解串器产品组合,支持各种接口。这些产品组合具有强大的 PHY 设计、低误码率 (BER) 和向后兼容性。任何视频协议都可以桥接在一起。例如,将 HDMI 连接到开放式 LVDS 显示接口 (oLDI)。
工程师需要根据设备接口、数据传输速率、带宽、功耗、环境条件和电缆长度等应用需求选择最佳组件。其他因素包括电磁干扰、错误处理和信号完整性。以下为 ADI 的几个 GMSL 组件实例:
- MAX96717,是 CSI-2 转 GMSL2 串行器(图 3),工作速率固定为正向 3 Gbps 或 6 Gbps,反向 187.5 Mbps。
图 3:使用 MAX96717 串行器说明数据流的示意图。(图片来源:Analog Devices, Inc.)
- MAX96716A,可将双 GMSL2 串行输入转换为 MIPI CSI-2。GMSL2 输入可独立运行,来自两个输入端的视频数据可在单个 CSI-2 端口汇聚以进行输出,或在第二个端口进行冗余复制。
- MAX96724,是一款四通道隧道式解串器,可将四个 GMSL 2/1 输入转换为两个 MIPI D-PHY 或 C-PHY 输出。数据链路速率:GMSL2 为 6/3 Gbps,GMSL1 为 3.12 Gbps;反向链路速率:GMSL2 为 187.5 Mbps,GMSL1 为 1 Mbps。
- MAX96714 解串器将单个 GMSL 2/1 输入转换为 MIPI CSI-2 输出,具有 3 Gbps 或 6 Gbps 正向固定速率和 187.5 Mbps 的反向固定速率。
- MAX96751 是一款带有 HDMI 2.0 输入的 GMSL2 串行器,可将 HDMI 转换为单通道或双通道 GMSL2 串行协议。它还能实现视频和双向数据的全双工单线传输。
- MAX9295D 可将单端口或双端口 4 通道 MIPI CSI-2 数据流转换为 GMSL2 或 GMSL1。
ADI 还提供多种开发工具,如用于 MAX96724 器件的 MAX96724-BAK-EVK# 评估套件。
结语
与 GigE Vision 相比,GMSL 相机的复杂性更低,结构更紧凑,通常能够提供更具成本效益的解决方案。GMSL 为越来越多基于相机和显示屏的应用(从机器学习和自主操作到信息娱乐和安全)提供可靠的微秒级延迟的高分辨率数字视频传输。如今,数以百万计的 GMSL 链路正在改善着驾驶员的道路体验,证明了其可靠性和性能。
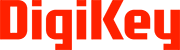
免责声明:各个作者和/或论坛参与者在本网站发表的观点、看法和意见不代表 DigiKey 的观点、看法和意见,也不代表 DigiKey 官方政策。