Rapid Development of a Compact Mobile Cold Chain Temperature Monitoring System
投稿人:DigiKey 北美编辑
2017-07-20
Accurate temperature measurement is an essential feature in mobile applications ranging from health wearables to industrial, medical, and pharmaceutical cold chain monitoring. For these applications, developers are challenged to design solutions that provide high accuracy and reliability with minimal power consumption, the smallest possible footprint and the lowest possible cost.
Designing with typical temperature transducers, developers are hard pressed to build signal chains capable of delivering on all these design requirements. However, a single-chip sensor from ams provides an integrated solution that is capable of delivering high accuracy at low power with a minimal footprint.
Critical temperature sensing applications: Cold chain monitoring
Accurate temperature measurement is vital to a wide range of applications where even small variations in temperature can impact performance. An unexpected deviation in operating temperature in mechanical systems frequently warns of mechanical problems. Chemical reaction rates increase with increasing temperature, dictating the need for close monitoring of temperature in sensitive chemical and biochemical process flows. Even with the use of specialized additives, bioreactive materials can degrade rapidly and irreversibly when exposed to temperatures outside of their recommended range. The safe delivery of sensitive pharmaceuticals depends on regular temperature measurement throughout the entire supply chain – a process called cold chain monitoring.
Among bioactive materials, vaccines are particularly sensitive to temperature. The World Health Organization notes that vaccines need to be stored between +2°C and +8°C, and any deviation outside of this range generally leads to loss of potency of the vaccine [ref 1]. Yet, according to the US Centers for Disease Control, occurrences of improper storage and handling continue to occur each year. Worse, a degraded vaccine cannot be detected through normal clinical methods. The result is not only financial loss due to wasted vaccine, but also the need to revaccinate affected individuals who received the compromised vaccine – a process that can damage public confidence in vaccine and health providers [ref 2].
In the past, cold chain monitoring has relied on manual temperature reading and measurement logging. For vaccines in particular, periodic manual temperature monitoring is insufficient according to the US Department of Commerce National Institute of Standards and Technology (NIST). NIST notes that cold chain monitoring without a continuous temperature measurement system results in a very high likelihood of undiscovered violations of viable temperature thresholds, which in turn leads to a very high likelihood that patients will receive ineffective doses [ref 3].
The CDC recommends that these continuous temperature measurement systems, called digital data loggers, provide specific features including an alarm for out-of-range temperatures as well as current, minimum, and maximum temperature measurement with an accuracy of +/-0.5°C [ref 2]. Taken alone, these requirements present little difficulty for the developer. Combined with the need for portability, communication, and extended battery life, however, development of a cost-effective solution for extended duration temperature monitoring of health or other mobile applications becomes problematic.
Meeting requirements
Among available design options, developers can select from a broad array of specialized analog-to-digital converters (ADCs) and analog front ends (AFEs) able to support highly accurate temperature measurement. Although other devices can meet individual requirements for performance and functionality, the ams AS6200 offers a unique combination of small size, low power, and high accuracy needed for mobile temperature monitoring. Delivered in a 1.6 x 1.0 millimeter wafer-level, chip-scale package (WLCSP), the device integrates a full sensor signal chain to provide an accurate digital temperature sensing system (Figure 1).
Figure 1: The ams AS6200 combines a bandgap temperature sensor with a full sensor signal processing chain and digital interface in a 1.6 x 1.0 mm package. (Image source: ams)
The device provides four continuous sampling rates including 8 Hertz (Hz), 4 Hz, 1 Hz, and 0.25 Hz. For different measurement rates, developers can use the device in a single-shot measurement mode. By setting the “Single Shot” (SS) bit in the device’s configuration, developers can force the device to perform a single temperature measurement. When conversion is complete (typically 32 ms), the device resets the SS bit to zero. Developers can initiate measurements and monitor the SS bit for completion to achieve arbitrary sampling rates.
In theory, this method can be used to boost the sample rate well above the built-in maximum rate. In practice, however, the increased power consumption associated with maximum rate sampling can lead to self-heating effects that will degrade the accuracy of temperature measurements.
In normal operation, the factory calibrated device features ±0.4°C accuracy at all built-in sample rates and draws power proportionally. For example, the device consumes 6 µA at 4 conversions per second, but at one conversion per second, the device uses only 1.5 µA.
Beyond its ability to reduce power at lower sample rates, the device includes an important power-saving feature as part of its normal operating mode. At startup, the device automatically initiates a conversion, providing a temperature measurement sample within the 32 ms typical conversion period. Between samples, however, the device conserves power by returning to standby mode, where it consumes only 0.1 µA (Figure 2).
Figure 2: The ams AS6200 helps reduce system power consumption by automatically returning to its 0.1 µA standby mode after each temperature sampling (TS) cycle. (Image source: ams)
The AS6200 uses this power-saving feature whether operating at any of the four supported conversion rates in continuous conversion modes, or in one-shot mode.
Simplified implementation
Because the device integrates all required sensor signal processing circuitry, only three pullup resistors (10 to 18 kilo ohms) and a decoupling capacitor (10 nanofarads min) are required to implement a digital temperature sensing design (Figure 3). Besides power and ground connections, developers only need to connect the device’s I2C clock (SCL) and data (SDA) pins as well as the alert pin to a host MCU.
Figure 3: The ams AS6200 integrates a complete temperature sensing system, requiring only four passive components and three connections to a host MCU for hardware implementation. (Image source: ams)
As described below, the alert pin can be used as an interrupt signal for the MCU in threshold-based monitoring. Finally, developers tie the address select pin (ADD0) to VDD or ground to set the device’s I2C bus address to one of two supported values. As noted below, this capability enables developers to use a pair of AS6200 devices to implement sophisticated guard band features in a temperature monitor.
Software implementation requirements are similarly straightforward. Developers access the device’s four registers across the I2C interface through a simple index register, which uses its last two bits to access the device’s four registers (Figure 4).
Figure 4: Developers access ams AS6200 registers across the I2C bus through a simple index register that points to the current temperature value (TVAL), device configuration settings (CONFIG), and upper (THIGH) and lower (TLOW) threshold values for generating alerts. (Image source: ams)
Developers set the index register to read the temperature value (TVAL), read/write the configuration register (CONFIG), or read/write a pair of registers that specify the upper (THIGH) and lower (TLOW) temperature threshold. Using the THIGH and TLOW thresholds along with other device features, engineers can quickly design a system that generates an alert warning when the measured temperature falls outside of a specified temperature range.
Threshold crossing alert system
The AS6200 alert pin provides a simple mechanism for signaling an MCU when temperature readings cross above or below the threshold values set in THIGH and TLOW, respectively. Besides this hardware-based alert mechanism, the device provides an alert bit that reflects the value of the alert pin. Consequently, developers can choose between hardware-based interrupts or software-based polling to detect temperature excursions with the AS6200.
In practice, however, transient excursions of temperature outside of the target window might not rise to the level of a true temperature fault for a particular application.
For example, the act of opening the door of a cold storage unit can cause a short spike in temperature that for a particular application might have no practical effect on the refrigerated items. The AS6200 provides a simple mechanism for avoiding false positive alerts. Here, developers set bits in the configuration register to specify the number of consecutive threshold violations before the device issues an alert through its hardware signal and software bit. For applications with particularly stringent temperature requirements, developers can set the consecutive fault value to one, causing the device to generate an alert on every threshold violation.
Besides single threshold violation alerts, demanding applications might require the monitoring system to build in sufficient margin to account for the finite accuracy of its sensor and sensor signal chain. In fact, NIST suggests the use of guard bands at the upper and lower limits of the allowed temperature range (Figure 5).
Figure 5: Developers can use a pair of AS6200 devices to create guard bands that eliminate uncertainty of temperature measurement by tightening the window of allowable temperatures – here from the recommended +2°C and +8°C to a stricter range of 2.6°C to 7.4°C. (Image source: NIST)
Using highly accurate sensors such as the AS6200, developers can shrink the margin, providing an effective operating window that is wider than possible with less accurate devices. To implement this type of monitoring system, developers can connect an MCU to two AS6200 devices, setting each device’s ADD0 address select pin to configure each device at a separate address on the shared I2C bus. By setting appropriate values for THIGH and TLOW in each device, developers can specify separate upper and lower guard bands for a temperature monitoring system.
Wireless monitoring system
The AS6200’s low power, high accuracy, and simple integration requirements make it an attractive solution for mobile applications. For evaluation of the device itself, ams offers its AS6200-WL_EK_AB adaptor board. The board implements the basic design mentioned earlier, adding onboard pull-up resistors, decoupling capacitor, and ADD0 address select toggle. The board also provides a five-pin connector that brings out the device’s I2C, alert, power, and ground pins.
For prototyping of a complete wireless temperature monitoring system, developers can take advantage of the RF Digital RFD77810 starter kit. By connecting a few Arduino shields provided in the kit and downloading a pre-built mobile app, developers can quickly prototype temperature monitoring features such as consecutive fault alerts or guard banding.
The RFD77810 kit includes the RF Digital RFD77313 sensor shield, which implements the simple AS6200 design. It includes a pushbutton and an LED as a simple user interface. RF Digital also includes its RFD77201 Simblee™ shield, which provides a complete Bluetooth low energy system based on an ARM® Cortex®-M0 processor. Developers simply stack the sensor and Simblee shields on the included RF Digital RFD22126 battery shield to create a functioning wireless temperature monitoring prototype. RF Digital also provides a Simblee app that enables developers to get up and running with a fully connected application. After evaluating their application design, engineers can leverage the shield designs for their custom systems.
Conclusion
Despite a broad array of available sensor signal processing solutions, developers of mobile temperature monitoring systems have had few choices that offer a combination of small size, low power, and high accuracy. Along with meeting these requirements, the ams AS6200 provides essential features required to build monitoring systems capable of generating alerts when measured temperatures fall outside target windows.
Using an available AS6200 based starter kit, developers can rapidly prototype wireless temperature monitors able to meet the needs of a wide range of temperature sensing applications.
References
- World Health Organization, Immunization in Practice - A practical guide for health staff, Module 2: The vaccine cold chain
- Centers for Disease Control and Prevention, U.S. Department of Health and Human Services, Vaccine Storage & Handling Toolkit
- National Institute of Standards and Technology , Cold Chain Management: Temperature Monitoring Solutions
- World Health Organization, Immunization in Practice - A practical guide for health staff, Module 2: The vaccine cold chain
- Centers for Disease Control and Prevention, U.S. Department of Health and Human Services, Vaccine Storage & Handling Toolkit
- National Institute of Standards and Technology, Cold Chain Management: Temperature Monitoring Solutions
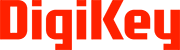
免责声明:各个作者和/或论坛参与者在本网站发表的观点、看法和意见不代表 DigiKey 的观点、看法和意见,也不代表 DigiKey 官方政策。