Pulse Electronics EP13 Plus Optimized Transformer Platform
投稿人:DigiKey
2014-06-17
There are wide varieties of electronics applications, including Power-over-Ethernet, datacom, telecom, and industrial that operate from a 12 V, 24 V or 48 V input and require an isolated switch-mode power supply solution to convert this available input voltage to a regulated output voltage and current. For power levels below 60 W, the most common power supply switching topologies used are the continuous mode flyback topology and the active reset forward topology. The leading transformer platform for these applications, at present in terms of power efficiency, board area, and cost, is the de facto industry standard EP13. This article has been created to detail the development of the EP13 Plus platform, which has the same physical size and footprint as the EP13 but is capable of handling higher through-power. Figure 1 below shows the design for an optimized transformer.
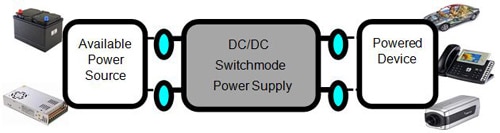
Figure 1: Optimized transformer design.
As system efficiency becomes increasingly more important and output power requirements continue to increase, two limiting factors emerge when using the industry standard EP13. The first is pin size and coplanarity. Surface-mount transformers must have excellent coplanarity to ensure that the leads are properly soldered to the printed circuit board and to avoid excess heating in the solder interconnection. However, the standard EP13 platform was initially developed for low current telecom filter magnetics so the pin is small and there is little room to terminate higher current windings. As a result, the standard EP13 platform limits the size and number of wires that can be terminated on a pin, and therefore increases the transformers resistance, which limits the through-power. Pulse Electronics took on the goal of creating a more efficient transformer while maintaining the same package size and footprint as the standard EP13. To solve the limitations caused by the pin size, as Figure 2 shows, Pulse’s EP13 Plus platform has employed a larger pin with twice the winding termination area resulting in a 20% reduction in winding resistance and therefore higher through-power.
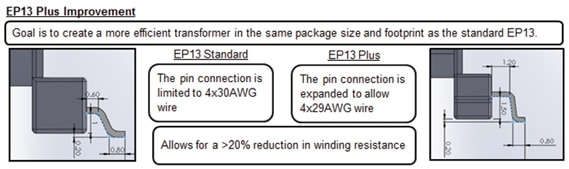
Figure 2: Terminal optimization.
The second limitation of the existing EP13 platform is the magnetic core area cross-section. For a given application, and in simplified terms, the core cross-section dictates the number of primary-side turns required to limit the magnetic flux density, which is necessary to avoid saturation or excessive core loss. The smaller the cross-section, the greater the number of primary turns required. The higher number of primary turns results in higher winding resistance (DCR) leading to higher I²R losses.
Pulse Electronics used finite element analysis to analyze the standard EP13 platform and found that the non-uniform core cross-section is not optimized. Using the same finite element analysis tools, Pulse created the optimized EP13 Plus core, which allows the cross-sectional area to be increased without increasing the overall platform size. This development has allowed for a 45% increase in core area, which leads to lower primary winding turns, resulting in lower winding resistance and higher through-power.
The graphs below show the core area optimization in further detail. In Figure 3, the top picture shows the finite element analysis of the flux density of the standard EP13 platform. The red areas indicate high magnetic flux density. It can be seen in the picture that the entire center leg of the standard platform has very-high flux density, or inversely, that the remaining core area is under-utilized. The second picture shows the flux density of the EP13 Plus platform core and the dramatic reduction in flux density. The uniform coloring indicates that the flux levels are constant throughout the core resulting in an efficient, three-dimensional core utilization.
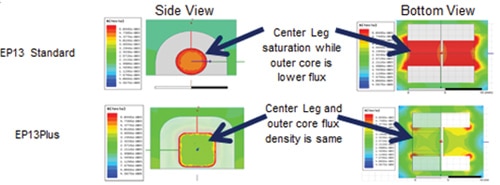
Figure 3: EP13Plus – core area optimization.
A simple way to test if core utilization has been improved is to do a comparison test between the EP13 Standard and the EP13 Plus platforms to determine which structure has a higher saturation current. This test can be done by winding the same number of turns on each platform, setting the air gap on each core to yield the same primary inductance and using the same core material. By keeping these three factors the same, the only variable affecting the saturation current will be the core cross-sectional area. The graph in Figure 4 shows that with the standard EP13, in red, the saturation current is around 1.6 A. The blue line shows the dramatic improvement of the EP13 Plus, which pushes the saturation current out to 2.7 A, resulting in a 68% improvement.
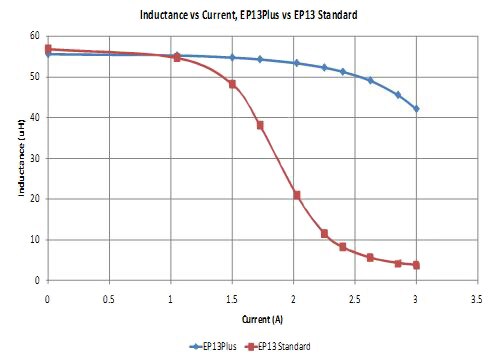
Figure 4: EP13 Standard and EP13Plus.
Pulse Electronics has created twelve catalog transformers based on the EP13 Plus platform. Each of these options is provided in Figure 5. The PA3855.XXXNL series offers six designs for flyback topologies with either 33-57 V or 9-57 V inputs and outputs ranging from 3.3 V to 24 V and power levels up to 36 W. The PA3856.XXXNL series offers six designs for active clamp forward topologies with either 33-57 V or 9-57 V inputs and outputs ranging from 3.3 V to 24 V and power levels up to 72 W. Custom designs are possible and interested groups should contact Pulse Electronics.
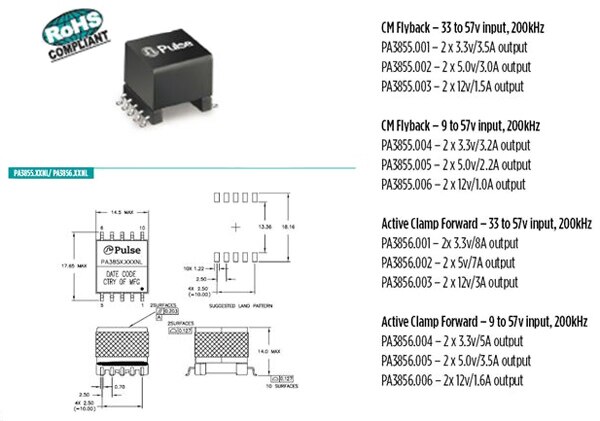
Figure 5: Pulse Electronics EP13Plus – PA3855 and PA3856.
In summary, Pulse Electronics has used finite element analysis to create the EP13 Plus transformer platform and have released twelve new catalog transformer designs all based on the industry standard EP13 platform. The new EP13 plus platform allows for a 45% increase in core cross-sectional area, a 68% increase in the useable magnetic flux saturation limit and a 25-35% increase in through-power capability making it the ideal solution for 20-70 W power transformer applications.
References:
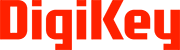
免责声明:各个作者和/或论坛参与者在本网站发表的观点、看法和意见不代表 DigiKey 的观点、看法和意见,也不代表 DigiKey 官方政策。