Properly Configure Parallel Power Supplies to Share Load Current or Risk System Failure
投稿人:DigiKey 北美编辑
2016-09-28
Designers connect power supplies in parallel to obtain a total output current greater than that available from one individual supply as well as to provide redundancy, enhance reliability, avoid PCB thermal issues and boost system efficiency. However, if the engineer doesn’t properly configure these paralleled systems to share load current, a supply could shut down before the required current is delivered, leading to system failure.
This likelihood of system failure only increases in step with the progressively increasing current demands of memory cards, DSPs and ASICs, all of which usually operate with lower supply voltages and very high DC currents. These high-performance semiconductor devices also demand very fast changes in load current.
Figure 1: Three power supplies connected in parallel to produce additional current. The total output current is the sum of the output currents of the individual power supplies. (Source: Keysight Technologies)
There are several other good reasons to employ a parallel power architecture (Figure 1):
- Reliability and Redundancy. Using multiple small power supplies can be more reliable than using a single large power supply. Continuously operating a power supply at maximum load significantly reduces its reliability and shortens its life. Redundancy is important in mission-critical systems such as military or medical applications where failure of one module cannot be allowed to affect the entire system. In situations where a product or system cannot tolerate any downtime, “N + 1 redundant” systems use a number of small supplies where N units are needed to power the load, but a “+1” supply is added for redundancy.
- Efficiency. If the power system must support widely ranging loads, efficiency can be optimized by adjusting the number of operating supplies to the load. For example, a DC/DC converter formed by two supplies running at half capacity can have better overall conversion efficiency than a single supply running near full capacity.
- Thermal Management and Lifespan. Using two or more lower-power modules to produce higher output power also helps to distribute the thermal load, thereby avoiding hot spots on the board. If two supplies source half of the load current, each will get only half as hot as they would not be shouldering the complete load. Spreading the supply heat also puts less thermal stress on components, extending each supply’s lifetime.
Paralleled supplies will provide differing portions of the load by default, so simply connecting the outputs of multiple power supplies in parallel will not guarantee that the load current is shared properly. Even modules with the same part number will have slightly different output voltages and the one with the highest voltage will naturally source the most current. Unless forced current-sharing control is designed into the system, one supply or converter – typically the one with the highest output voltage – will deliver current up to its current limit setting. Unless measures are taken to balance the load, a supply could shut down due to reaching its maximum current limit before the required current is delivered to the load. What’s more, if the paralleled power supplies are not sharing their contribution equally, one supply will be subjected to more stress than the others, shortening its life expectancy.
This article will discuss typical current-sharing methods. In each case the trick is to implement load sharing without degrading the performance and efficiency of the individual units. We will examine the intricacies of a typical load-share controller and then discuss a bus converter array used in intermediate voltage bus architectures, presenting a design example where the modules offer the inherent ability to share load current when its inputs and outputs are connected in parallel.
Current-sharing methods
When done right, current sharing improves system performance, optimizes transient and dynamic response and minimizes thermal problems, which improves reliability and helps extend the lifetimes of all of the supplies in an array. Specifically, the mean time between failure (MTBF) roughly doubles with every 10°C decrease in operating temperature. Current sharing also enables better recovery on supply failure as the functioning supply has to go from half to full load instead of from zero to full load. Current sharing between power supplies can be achieved by several different methods. Let’s look at these one at a time, starting with the voltage-droop current-share mode.
Voltage droop is the intentional loss in output voltage from a device as it drives a load. It works by allowing the power output voltage to sag as a function of load current to ensure balanced current sharing among the modules connected in parallel. This “droop-share” method increases the output impedance of a module, lowering its output voltage, to force the currents to be equal.
Droop share (Figure 2) is accomplished by an error signal interjected into the control loop. If one supply is delivering more current than another, its output voltage will be forced down a bit so that it will be delivering equal current for an equal voltage. Droop share can work with any topology, but the method has some drawbacks: there is a trade-off between how well the currents balance and voltage regulation, and there is an inherent difficulty in current sharing between parallel modules with different power ratings.
Figure 2: The droop method programs the output impedance of the power supplies to achieve load sharing. As the individual supply-current increases, the feedback voltage will decrease. (Source: Texas Instruments)
Another approach is to select a master module to perform the voltage control and force the remaining modules (slaves) to act as current sources (Figure 3). The dedicated master–slave control scheme ensures that all of the slave modules follow the reference current of the master.
While this technique achieves load sharing, it does not achieve redundancy, because if the master fails, the entire system becomes disabled. Only supplies having the same model number should be connected for this type of operation, since the supplies must have the same voltage drop across the current monitoring resistor at the full current rating.
Figure 3: A dedicated master approach with current-mode supplies will facilitate current sharing but does not achieve redundancy. (Source: Texas instruments)
A popular solution is to use an external controller to perform the load sharing. The current-sharing controller adjusts the power-supply voltages based on the current contributions. A power supply with lower current would be adjusted up in voltage to increase its share until both inputs to the controller are equal. Access to the power supply is required and the supply needs feedback networks to allow on-the-fly adjustment of the output voltage.
Linear Technology’s LTC 4370 current-balancing controller, for example, is a two-supply current-sharing, controller with reverse blocking that prevents a fault in one supply from bringing down the power system (Figure 4). It employs external N-channel MOSFETS that act as adjustable diodes whose turn-on voltage can be modulated to achieve balanced sharing. This produces better sharing accuracy than droop sharing and the power spent in the adjustable diodes is far less than that lost in a traditional diode.
Figure 4: The LTC4370 current-balance controller from Linear Technology is shown balancing a 10 A load current between two diode-ORed 12 V supplies. Sharing is achieved by modulating the MOSFET voltage drops to offset the mismatch in the supply voltages. (Source: Linear Technology)
The minimum diode drop is 25 mV. The upper limit of the drop is set by the RANGE pin, which determines the supply difference for which the controller can compensate. The maximum voltage difference allowed is determined by a <60 KΩ resistor placed between the RANGE and GND pins. When the input supply voltage difference rises beyond the programmed range, the LTC4370 disables the current sharing function. There are two alarm outputs, each monitoring the control voltage at the gate of each MOSFET. By cascading the shared output of one LTC4370 with another LTC4370, three or more supplies can be controlled to provide equal current to the load.
To help you get started, Linear Technology offers a Product Training Module, “Current Sharing Basics with LTC4370” that discusses the basics of connecting two power supplies in parallel, and methods to make them share the load current. It addresses the pros and cons of each method and provides a brief discussion of the LTC4370 current-balancing controller.
Current sharing in paralleled bus converters
Parallel arrays of bus converters for intermediate bus architectures (IBAs) are often used in applications where the output power of a single bus converter is not sufficient for the maximum load conditions. Typically, active current sharing is employed in these configurations. Vicor’s ChiP bus converter modules (BCM), for example, may be paralleled to provide multi-kW arrays. When multiple BCM modules of a given part number are connected in an array, they will inherently share the load current according to the equivalent impedance divider that the system implements from the power source to the point of load.
Sharing accuracy is a function of input- and output-interconnect impedance matching, the output impedances (ROUT) of the BCM modules, and uniform cooling. The lower the ROUT of the module, the more closely input voltages must match to avoid excessive current imbalance. As such, the input voltages must be equal to ensure evenly distributed sharing.
Designed for high-voltage DC distribution infrastructure in datacenter, telecom and industrial applications Vicor’s VI ChiP High Voltage BCM Bus Converter 6123 offers up to 1.75 kW at 50 V with 98% peak efficiency and a power density of 2750 W/in3. You might want to take advantage of the evaluation board for the 6123, the BCM6123E60E15A3T00.
The paralleling and sharing performance of multiple BCMs can be easily demonstrated. Stack multiple evaluation boards and then interconnect the inputs and outputs with metal standoffs of sufficient current rating to create a parallel array. With equal impedance, the load is effectively shared across multiple BCMs.
Module # | 48 A Load (6.86 A / BCM) |
95 A Load (13.6 A / BCM) |
143 A Load (10.4 A / BCM) |
192 A Load (27.5 A / BCM) |
||||
IBCM | % Deviation | IBCM | % Deviation | IBCM | % Deviation | IBCM | % Deviation | |
U1 | 5.9 | 14.0 | 12.6 | 7.4 | 19.2 | 5.9 | 27.6 | 0.4 |
U2 | 7.1 | 3.4 | 13.2 | 2.9 | 19.9 | 2.5 | 27.3 | 0.7 |
U3 | 6.7 | 2.4 | 13.6 | 0.0 | 20.6 | 1.0 | 27.7 | 0.7 |
U4 | 7.4 | 7.9 | 14.4 | 5.9 | 21.3 | 4.4 | 27.4 | 0.4 |
U5 | 7.1 | 3.4 | 14.0 | 2.9 | 20.8 | 2.0 | 27.5 | 0.0 |
U6 | 7.2 | 5.0 | 14.0 | 2.9 | 20.9 | 2.5 | 27.7 | 0.7 |
U7 | 6.8 | 0.9 | 13.5 | 0.7 | 20.4 | 0.0 | 27.2 | 1.1 |
Worst Case deviation from nominal (%) |
14.0 | 7.4 | 5.9 | 1.1 |
Table 1: Vicor tested the current-sharing performance of a seven-BCM bus converter array and despite less-than-ideal layout conditions, the overall sharing of the array was within 5%. (Source: Vicor Corp.)
As a design example Vicor tested an array of seven high-voltage-input 300 W BCM bus converters (modules U1 through U7 in Table 1 above), providing a total power of 2.1 kW. The table illustrates the measured currents for the layout. Even with less than ideal layout conditions (long wires, separate boards, use of standoffs to carry current), the overall sharing of the array is within 5%.
Conclusion
Using multiple power supplies connected in parallel, designers can get greater output current while also achieving redundancy, improving efficiency and enhancing overall system reliability. While there is of course a cost factor associated with adding more power electronics, if done right, using the techniques and example devices outlined in this article, the benefits can quickly start to outweigh the costs, especially in applications where system failure is unacceptable.
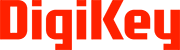
免责声明:各个作者和/或论坛参与者在本网站发表的观点、看法和意见不代表 DigiKey 的观点、看法和意见,也不代表 DigiKey 官方政策。