How to Design Low-Power Always-On Wearables: Part 2 – Protect and Recharge Batteries for Long Life
投稿人:DigiKey 北美编辑
2019-09-24
Editor’s note: This is Part 2 of a three-part series on designing battery powered always-on wearable electronics, focusing on three areas in which to optimize for power. Part 1 described how to configure the microcontroller to extend battery life and reduce recharges. Here, Part 2 looks at how to safely maintain the battery to extend time between recharges. Part 3 examines wireless networking for wearables and how to maintain wireless connectivity while minimizing drain on the battery.
As wearables are becoming more popular, wearable manufacturers are adding more features to stay competitive, which usually increases the power drain on the battery. Fitness watches in particular have a more difficult time maintaining a long battery life as the batteries are very small, limiting their capacity. In addition, unlike many consumer devices, wearables such as fitness watches are always on, placing additional strain on the battery. Battery life of a wearable is crucial to customer satisfaction, so the engineer’s selection of the battery and the battery management system can mean the difference between a satisfactory user experience and the disaster of premature battery failure.
This article discusses the unique needs of battery management systems for always-on wearables. It examines a battery management chip from Maxim Integrated that simplifies wearable battery charging and maintenance, and then looks at two batteries from Adafruit Industries.
Using rechargeable batteries in consumer devices
Wearables are consumer products and are therefore subject to the consumer’s definition of customer satisfaction. Consumers expect a long time between recharges (“a long time” being subjective to the consumer) and expect the battery to last many years before needing replacement. This latter point is especially important as wearables are generally not consumer serviceable—there is no cover to pry off to get to the battery, and consumers are discouraged from removing those tiny little screws on the back.
While operational, the battery and wearable should be able to withstand the various temperatures and conditions a person would normally experience during the day. In addition, the selected battery chemistry must have a very high energy density so it can pack a lot of power in a small package.
While there are many battery chemistries to choose from, the lithium-ion battery has become the standard for most consumer rechargeable devices. Lithium-ion batteries have a very high energy density, allowing twice the watt-hour (Wh) capacity in the same package compared to their nearest rival—nickel-cadmium (NiCad) batteries. The industry standard cell voltage for a lithium-ion battery is 3.6 volts ±1 volt, which means a wearable can be powered by a single cell.
An engineer should not design a wearable with a battery chemistry that requires active customer maintenance. This excludes NiCad batteries which have a chemical memory that requires periodic charge cycling (i.e. completely discharged and then fully charged) by the customer. Lithium-ion batteries do not have a chemical memory, eliminating the need to be charge cycled to maintain capacity.
Unlike NiCad batteries, however, Lithium-ion batteries do require electronic maintenance while in-system. Lithium-ion batteries are not simply charged by applying a voltage. Instead, they must be carefully charged using either a constant current source, a constant voltage source, or a combination of both. During charging, a battery protection circuit must be used to guard against voltage or current spikes that can damage the battery or even make it unusable. Lithium-ion batteries can also be damaged by extreme hot or cold temperatures, and so require temperature monitoring. Extreme cold can disable a lithium-ion battery and make it unusable. Extreme heat can be dangerous to a lithium-ion battery and can lead to thermal runaway: as the battery gets hotter, the more energy it releases, making it even hotter, causing it to put out more energy. If left unchecked, thermal runaway can lead to the battery catching fire.
Lithium-ion batteries are subject to aging, even if the battery is not in use. Over time a lithium-ion battery will lose capacity and will require more frequent charging. Exactly how much capacity is lost over time is usually not specified by battery manufacturers. While aging might not be obvious for a battery pack of five 3.6 volt cells, for a single 3.6 volt cell aging can be a significant design concern. The battery gauge (sometimes called a fuel gauge) should show this loss of capacity over time so it can compensate for the difference.
Unique needs of batteries in always-on wearables
For battery-powered consumer devices, users expect a reliable and consistent battery gauge. Consumers understand that if a multipurpose mobile device plays a video; the battery gauge will drop faster than if the device is idle. However, for an always-on wearable, the user expects the battery gauge reading—shown as a percentage, bars, or both—to decline at a consistent and predictable rate. A user with a wearable on their wrist looks at it every day and will notice inconsistencies. For example, if over time a device’s battery consistently loses 10 percent of its charge every day and one day it suddenly shows a 25 percent loss, the user will notice and might even complain to the manufacturer. For this reason, the device’s battery management circuitry must accurately monitor and maintain the battery health to provide an accurate gauge reading.
By far the most obvious constraint for a battery in a wearable is size. Most wearables today use a single 3.6 volt lithium-ion cell for power. One factor to be aware of is that even a well-maintained and healthy lithium-ion battery will still become hot and expand under load. So, while a wearable is already space constrained, the designer must still leave room in the enclosure for battery expansion to avoid potential safety issues.
Damaging current spikes are unlikely to occur to wearable batteries when dealing with small voltages near 3.6 volts. However, an errant combination of multiple simultaneous sensor activations and events may produce an unusually large current spike that may damage the battery. Fortunately, because of the typical small voltages and currents involved, protection is a relatively simple matter.
Battery management for wearables
As mentioned previously, lithium-ion batteries require constant monitoring of their output voltage, current draw, and temperature. Additionally, the monitoring function must be stable and reliable over time, taking time and resources away from the main product differentiators.
Fortunately, the monitoring function can be greatly simplified by using an IC specifically designed for the task. One such device is the Maxim Integrated MAX17301X+ one-cell fuel gauge with battery protection. This is a complete battery management system for a single-cell 3.6 volt lithium-ion battery (Figure 1).
Figure 1: The Maxim Integrated MAX17301X+ is a complete lithium-ion battery management system that monitors, protects, and safely charges a single 3.6 volt cell. It interfaces to most microcontrollers using a standard I2C interface. (Image source: Maxim Integrated)
The MAX17301X+ is in a 15-pin WFBGA package that measures 1.68 x 2.45 millimeters (mm), making it particularly suited to a wearable application. Also making it suitable for wearables is its current draw, only 24 microamps (µA) when active.
The MAX17301X+ integrates the many complex tasks of managing a 3.6 volt lithium-ion battery cell. A charge FET and a discharge FET are used to provide power to and from the battery to the wearable system. When a cell is connected to the IC, the MAX17301X+ is constantly monitoring the voltage across the terminals, current flow through an external sense resistor, and the temperatures of both the IC and the battery.
To avoid temperature-related issues like those mentioned earlier, two temperature sensors are available: an internal sensor and an external battery sensor. The external sensor is connected to the TH pin. The external temperature sensor can be internal to the battery, or it can be placed against it. If the external temperature sensor is omitted, it is recommended that the MAX17301X+ be placed against the side of the battery so that the internal sensor reflects the battery temperature. The charge and discharge FETs should also be placed near the MAX17301X+ so their heat can be factored into the analysis.
The MAX17301X+ communicates with a host microcontroller using a standard I2C interface. The IC has programmable registers that set the alert limits and conditions according to the battery manufacturer’s specifications. These initial values can be programmed by the host microcontroller or set during factory test of the wearable. Most values are stored in non-volatile memory (NVM) registers, so even if the battery is removed the MAX17301X+ will still retain these values. To ensure data integrity, a checksum register is used to validate the NVM registers.
Discharge protection
During battery discharge, the MAX17301X+ provides three forms of discharge protection: overcurrent, overtemperature, and undervoltage.
Excess current draw can reduce a battery’s available capacity, damage the battery to where it is unusable, or even cause it to catch fire. Overcurrent discharge protection can disable power to the wearable as quickly as 70 microseconds (µs). This is especially important if there’s a short circuit. Its response can also be as slow as 23 seconds for small current spikes.
High temperatures can have the same effect as excess current. Overtemperature discharge protection can turn the wearable off if the on-chip temperature sensor or external sensor reaches the programmed level. When this occurs, the MAX17301X+ will not allow the wearable to be turned on until temperatures have dropped to a safe level. The MAX17301X+ also has a Permanent-Fail-Hot protection setting. If a severe overtemperature is detected, the event is stored in the MAX17301X+ and the charge and discharge FETs, shown in Figure 1, are permanently disabled, which disables the wearable. This is the last line of defense against thermal runaway.
Battery voltages lower than those specified by the battery manufacturer can also damage the battery. Undervoltage discharge protection provides three levels of protection:
- Undervoltage protect can be used to turn off the discharge FET to disable power to the wearable
- Undervoltage shutdown is a lower voltage setting that turns off the discharge FET and also turns off the MAX17301X+ to conserve every nanowatt of power
- SmartEmpty turns off the discharge FET to conserve power if the MAX17301X+ determines there is an open circuit to the wearable’s electronics
Charging protection
During battery charging, protections similar to those for discharge are provided. The MAX17301X+ has a wide range of programmable battery protection register settings that allow tight control over almost every aspect of battery maintenance (Figure 2). The charging voltage and current is programmed in the MAX17301X+ based on the battery manufacturer’s specifications.
Figure 2: The Maxim Integrated MAX17301X+ has a wide range of programmable functions that allow the designer to fine-tune battery protection to maintain battery life and safety. (Image source: Maxim Integrated)
The MAX17301X+ can be used to specify a charging voltage and current for six different temperature ranges to safely charge the battery. Overcharge protections are also set by the designer. Because these charging parameters are specific to the battery, wearable manufacturers discourage replacing the battery as the replacement may have different specifications than the one installed at the factory. This can lead to poor battery life or an unsafe wearable.
Both Overcharge-Current protection and Overcharge-Voltage protection can be set for different temperature ranges. If the set limits are exceeded, the MAX17301X+ can attempt to throttle back the voltage and current, disable the charge FET to discontinue charging, or in extreme fault cases, permanently disable the charging FET. Charge Temperature Protection is the same with the added protection that charging is temporarily disabled at extremely cold temperatures to avoid permanent damage to the battery.
Battery state and health
The MAX17301X+ also maintains the battery gauge reading for the wearable. The most common method of estimating the battery state is by coulomb counting. This maintains a historical record of the current flow during charging and discharging operations. In other words, coulomb counting keeps a running count of the total coulombs flowing into and out of the battery over time. The MAX17301X+ constantly measures the current in both directions using the sense resistor seen in Figure 1. The coulomb counting method uses an algorithm to calculate the battery’s state of charge (SOC) expressed as a percentage. On the wearable, the battery gauge represents this SOC as a percentage of available capacity.
The MAX17301X+ uses a Maxim Integrated proprietary method similar to coulomb counting called the ModelGauge m5® algorithm to accurately calculate the SOC. The host microcontroller can read this value over the I2C interface to display on the wearable.
Another useful value for determining the state of the battery is arrived at by calculating the battery’s state of health (SOH). This is the percentage of the battery’s available full capacity against the battery’s specified full capacity when new. Referring to the aging mentioned earlier, as the battery ages, the SOH decreases.
Batteries for wearables
The selection of batteries for wearables is immediately limited based on size. A wearable battery will be a single lithium-ion cell that may or may not include protection. Although battery datasheets come with recommended specifications, an engineer should experiment with charging and discharging the battery under different conditions to evaluate exactly how the battery will perform in the final product.
The Adafruit 4237 lithium-ion polymer battery is rated at 3.7 volts and 350 milliamp-hours (mAh). With the cable, the battery pack measures 55 x 25 mm. Without the cable, it measures 31 x 25 mm, slightly larger than an American quarter (Figure 3).
Figure 3: The Adafruit 4237 Lithium-ion battery is rated at 3.7 volts and is slightly larger than an American quarter. (Image source: Adafruit)
The 4237 battery is specified to charge at a constant current and voltage, with a recommended charging current in the range of 100 to 350 mA at a charging voltage of 3.7 volts. Although specified at 3.7 volts, depending on temperature and current load, it can show a voltage as high as 4.2 volts when completely charged. This is important when setting a battery management IC to the battery’s specifications.
The 4237 battery comes with a simple internal voltage protection circuit that will temporarily disable the battery output if it drops below 3.0 volts. The protection circuit also prevents the battery from overcharging.
Like many small lithium-ion batteries, the 4237 does not have an internal temperature sensor or a temperature protection circuit. Using a battery management chip like the MAX17301X+ is strongly recommended to protect it from temperature or current faults.
For additional capacity, Adafruit has the 4236 3.7 volt lithium-ion battery rated at 420 mAh. At 35 x 47 mm (without the cable) it is a little larger than the 4237 but comes with 20 percent more capacity. Charging specifications are the same as the 4237 except that the charging current can go as high as 420 mA. It has the same basic protection circuit as the 4237 and so can also benefit from a battery management chip.
Conclusion
Managing a lithium-ion rechargeable battery for an always-on wearable can be a complex task as many batteries come with limited or no protection. Designing in appropriate protection and battery charge and discharge management adds cost and design time. However, designers don’t have to design protection from scratch due to available programmable battery management chips that can greatly simplify the task, while maintaining the safety of the battery, the system, and the user.
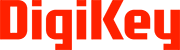
免责声明:各个作者和/或论坛参与者在本网站发表的观点、看法和意见不代表 DigiKey 的观点、看法和意见,也不代表 DigiKey 官方政策。