用于 SWaP-C 的高可靠性连接器选型和应用指南
投稿人:DigiKey 北美编辑
2025-01-02
国防和航空航天应用系统的设计人员正面临着越来越严格的尺寸、重量、功率和成本 (SWaP-C) 优化要求。随着设计越来越复杂和紧凑,设计人员必须在高性能和高可靠性之间取找到平衡。传统连接器往往难以满足这些相互冲突的需求,这给设计人员寻找替代品以满足系统设计和性能要求带来了不小的挑战。
本文将探讨针对 SWaP-C 设计的先进连接器技术如何满足国防和航空航天应用的独特需求。然后介绍 Harwin 的高可靠性解决方案 ,并展示如何将其应用于各种国防和航空航天场合,以实现可靠的 SWaP-C 性能。
推动连接器小型化的因素
从升级为多光谱成像的潜艇潜望镜系统,到搭载不断扩大的传感器阵列的无人机 (UAV),密闭空间对精密电子设备的要求正逐年复杂化。尽量减小元器件尺寸可以增加传感器和其他功能,从而增强系统能力,改善空气动力性能。
连接器历来是体积较大的器件,因此对于成功实现小型化具有至关重要的作用。要减小连接器尺寸,就必须缩小触点间距,减轻重量,同时保持耐用性,确保在极端条件下保持稳定的电气性能。
面对这些挑战,Harwin 推出了专为 SWaP-C 优化而设计的综合连接器系列。他们的方法以三大设计原则为核心:
- 将间距缩小至 1.25 毫米 (mm),同时保持较高的载流能力
- 使用多指铍铜触点,确保极端条件下的信号完整性
- 采用耐高温热塑性塑料外壳,并有选择地使用轻质金属以确保耐用性
从高密度信号连接器到混合技术和大功率解决方案,这一设计理念贯穿于其高可靠性产品系列。
减轻连接器重量对移动性和效率的影响
在 SWaP-C 优化过程中,尤其是在机载和移动应用中,减轻重量至关重要。更轻的器件可以延长飞行时间,提高机动性,同时可以携带更多的设备。
与传统工业连接器相比,现代微型连接器可通过战略性材料选择大大减轻重量。例如,玻璃填充耐高温热塑性塑料可用于主外壳。同时,设计人员可以有选择性地使用轻质铝合金,而且仅在由于电磁干扰 (EMI) 和射频干扰 (RFI) 以及机械耐用性而需要金属的地方使用。
即使是在传统设计严重依赖金属元件的大电流应用中,这些材料组合也能保持稳健的电气和机械性能,同时最大限度地减小连接器的质量。
在不牺牲可靠性的前提下管理连接器成本
在 SWaP-C 设计中,任务关键型系统的设计人员一直面临的挑战是,如何在更低成本和高可靠性之间取得平衡。对于连接器来说,意味着选择能确保长期耐用且成本最低的设计和材料。
管理成本的关键战略之一是关注总拥有成本,而不仅是前期的器件价格。虽然高可靠性连接器的初始成本可能较高,但由于其延长了使用寿命并降低了维护要求,因此可实现显著的长期节约。在连接器必须承受包括高振动、温度波动和重复配接在内的极端条件应用中,这一点尤为重要。
此外,标准化和模块化的连接器设计可以通过更简单的集成和更换来降低生产和维护成本。符合行业通用标准的连接器可实现互换并简化库存管理,从而减少产品生命周期内的开支。
在功率输出与尺寸之间实现平衡
连接器在电源管理中同样至关重要。目前的挑战在于开发既能承受大功率负载,又能保持紧凑外形并确保将功耗降至最低的连接器。 高可靠性连接器必须能够支持高效的功率传输,尽可能减少发热,防止产生电弧,同时符合现代系统设计对空间和重量的限制规定。
要实现效率和可靠性,就必须采用具有低电阻的材料和触点设计。连接器具有坚固的触点电镀层、先进的绝缘和经过优化的触点几何形状,即使在极端工作条件下也能提供稳定的功率。
关键的考虑因素是,将信号和电源连接整合到一个外形紧凑的连接器中。虽然集成信号线和电源线可减少连接器的总占用面积并节省宝贵的空间,但这也给管理电源和信号通路之间的潜在干扰带来了挑战。
应用案例:喷气式战斗机驾驶舱
研究典型的使用案例有助于说明这些设计原则在实践中是如何发挥作用的。例如,喷气式战斗机的照明控制装置 (LCU) 需要可靠的连接器来管理不同飞行条件和任务下的照明。 这些系统用来控制驾驶舱内、外部、夜视和应急照明,因此需要能够在拥挤狭小的环境中实现可变照明强度的器件。LCU 的空间有限,需要在不影响性能的前提下能够有效集成的小型组件。
Harwin 的 Gecko SL连接器间距为 1.25 mm,是一种紧凑轻便的解决方案,比 Micro-D 连接器轻 75%、小 45%。因此,这种连接器特别适合像 LCU 这样的密集环境。 Gecko SL 系列的主要特点包括:
- 单独导通时每个触头均可承受 2.8 A 的电流;同时导通时,所有触头均可承受 2.0 A
- 四触指铍铜合金触头设计确保了高可靠性
- 模铸材料采用玻纤填充热塑性 UL94V-0(无卤素和无红磷)材料
G125-MC10605M1-0150L变体采用六针位插头,通过单独的导线引线进行端接(图 1)。此外,该连接器还提供多种其他装配样式以及轻质铝制罩,以增强电气连续性,提供电缆保护和有效的 EMI/RFI 屏蔽。
图 1:Gecko SL 连接器适用于喷气式飞机驾驶舱等空间有限的环境。G125-MC10605M1-0150L 变体采用六针位插头,通过单根导线端接。(图片来源:Harwin)
除了外形小巧外,Gecko SL 连接器还异常坚固耐用。这种连接器能承受高达 100g 的冲击 6 毫秒 (ms) 和 20g 的振动 6 小时,因此非常适合航空航天环境。这类连接器的耐久性等级达到了 1000 次配接,可确保在反复连接和断开时的可靠性,而这正是密集维护型应用的常见要求。
应用案例:混合信号无人机连接器
另一个案例是,在防御环境中作业的无人机需要坚固耐用、结构紧凑的连接器,并且可在恶劣条件下正常工作。无人机会遭受剧烈的振动和冲击,因此信号完整性对其机载系统至关重要。
Harwin 的 Datamate Mix-Tek 连接器将电源线和信号线集成在一个紧凑的封装中,解决了上述难题。这种节省空间的设计采用 2 mm 间距,可在印刷电路板(PC 板)上留出足够空间安装其他器件,最终提高无人机的能力和性能。这些连接器具有信号触点 6 毫欧 (mΩ) 和电源触点 25 毫欧 (mΩ) 的低接触电阻,极大地减少了功耗和信号丢失情况。这些连接器的额定配接次数为 500 次,可确保其在需要频繁维护和重复连接的应用中经久耐用。
例如,M80-5T10805M1-02-331-00-000 组合了两个功率触点,每个触点的载流能力为 20 A;此外,还配备了八个信号触点,每个触点的额定电流为 3 A(图 2)。在大多数无人机应用中,这种配置可满足关键系统的电源需求、控制和通信的数据需求。
图 2:M80-5T10805M1-02-331-00-000 连接器将两个电源触点和八个信号触点以 2 mm 的间距集成在一个封装外壳中,适用于无人机等空间受限的应用。(图片来源:Harwin)
应用案例:大功率无人机电池
以防御为重点的无人机通常需要大量电力,由可提供数十到数百千瓦电力的电池系统提供动力。将这些电池与电机等关键部件连接起来的连接器必须能够可靠地处理大电流,同时尽量减少功率损耗。
Harwin 的 Kona 高可靠性连接器可满足这些要求,其每个触点可承受 60 A 电流和 3000 伏电压。这种触点的间距为 8.50 mm,支持大功率负载,同时具有防御级的坚固耐用性。2 mΩ 的接触电阻可确保将功率损耗降至最低。
KA1-MV10205M1 就是一个很好的例子(图 3)。这种连接器有两个公插针,最大电流能力共计 120 A。这种连接器非常适用于连接无人机电池,既能满足 SWaP-C 要求,又能提供强大的电力。
图 3:KA1-MV10205M1 连接器每个触点的额定电流为 60 A,电压为 3000 V,采用六指触点设计,可在强冲击条件下保持稳定。(图片来源:Harwin)
Kona 连接器采用镀金铍铜触点以及六指触点设计,可在强冲击条件下保持稳定连接,间距为 8.5 mm。铝合金底壳和不锈钢螺纹锁设计轻巧耐用。
结论
选择合适的连接器对于平衡 SWaP-C 优化的各种要求至关重要。Harwin 先进的连接器解决方案证明,将紧凑性、轻量化设计、电源效率和耐用性相结合是可能的,从而使设计人员能够满足航空航天和国防应用的复杂要求。
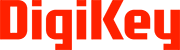
免责声明:各个作者和/或论坛参与者在本网站发表的观点、看法和意见不代表 DigiKey 的观点、看法和意见,也不代表 DigiKey 官方政策。