Embedded World 2012 Highlights the Current Trends in Microcontroller Development
投稿人:DigiKey 欧洲编辑
2012-03-28
Embedded World normally forms the backdrop for a number of significant product announcements and this year, the 10th anniversary of the Embedded World Conference & Exhibition, was no exception. Held over three days in the Nuremberg Exhibition Center in Germany, it attracted over 900 exhibitors and in excess of 20,000 trade visitors. In this article, we will look at the most significant announcements made in the area of microcontrollers.
While every year brings new innovations in microcontroller (MCU) design and support, those innovations are typically driven by far-reaching trends. A little while ago those trends would have been summed up by ‘smaller, faster, cheaper’, but today they are best described (albeit less succinctly) as the demand for low power, the rising complexity of software development, and the greater integration of intelligent peripherals. Each of the new and innovative MCUs, and many of the evolutionary developments announced at Embedded World this year, had some foundation in these trends.
Specifically, battery powered applications are now a significant driver for MCU manufacturers, which means ultra-low power in both standby and active modes is essential. This trend has shaped the developments of new companies, such as Energy Micro, and those more established, including Texas Instruments and STMicroelectronics. The demand from their customers for better software development support is also showing up in the support for both new MCUs and existing product lines, such as Cypress Semiconductors’ PSoC family. Finally, the market’s thirst for greater integration has enabled some companies — Silicon Labs and Infineon to name just two — to make ‘late’ entrances in to the already crowded ARM Cortex-M arena. Here we present a round-up of all these trends and developments, as announced at this year’s Embedded World Conference & Exhibition.
ARM proponents
Although it may seem omnipotent, ARM’s penetration of the microcontroller market is still only around 15 percent of the total available market; a figure that reflects the many millions of devices shipped each year which favor either a 16- or, more likely, an 8-bit architecture. That being said, ARM’s own figures show that there are now over 100 million ARM cores shipped in general purpose MCUs every month. If that figure were to include standard parts which are not classed as MCUs, it would be nearer 200 million.
With a target market share of 40 percent within the next few years, ARM’s route to market remains its licensees, so it is not surprising that many of the significant announcements made at Embedded World this year were enabled by the Cortex-M family.
Perhaps most significant (although arguably least surprising) was Silicon Labs’ entry into the 32-bit market with its Precision32 family of mixed-signal MCUs. This MCU embeds the ARM Cortex-M3 core and is heralded as the most flexible 32-bit MCU available. The reason for this is partly due to a patented ‘crossbar’ technology that allows almost any peripheral to be routed to any pin. Adding to this flexibility is a development environment which adopts a GUI front end supporting automatic code generation, allowing engineers to ‘drag & drop’ peripherals into a design and configure them visually, and then generate source code automatically.
What really sets the Precision32 family apart from other Cortex-M3 based MCUs, however, is its mixed signal capability. Silicon Labs has used its expertise in mixed signal to integrate some useful features that should also significantly reduce the total BoM cost for any application. These include a voltage regulator, allowing the MCU to be powered directly from a USB port; pull-up resistors and USB termination circuit; a crystal-less oscillator that can be used for the USB port as well as clocking the processor core; and capacitive-touch circuitry. In Figure 1, we see how the crossbar technology implemented in the Precision32 family allows almost any pin-out to be achieved without affecting the performance, all of which can be achieved using a GUI.
Figure 1: The patented Crossbar technology in Silicon Labs’ new Precision32 family allows almost any peripheral to use any pin.
In addition to high performance analog, the Precision32 family also boasts more low-power modes than competitive Cortex-M3 based products, stating that it can achieve between five and one-hundred times lower sleep current than in-class competitive devices. These levels measure just 0.35 μA with the real-time clock (RTC) running, while consuming just 275 μA/MHz active current at up to 80 MHz clock frequency. Figure 2 shows graphically how the low power modes can help extend the lifetime in a battery-powered application.
Figure 2: The low power modes of the Precision32 family target battery-powered applications.
There will initially be two variants within the Precision32 range: the SiM3U for USB applications, and the SiM3C for non-USB applications. The Eclipse-based development environment includes a compiler, debugger, and ‘dashboard’ for accessing the latest documentation such as data sheets. It also supports the standard ARM library, CMSIS, as well as a range of third party compilers and debuggers.
One of the main differentiators for SiLabs’ IDE is the ‘AppBuilder’, which allows engineers to graphically configure peripherals, set clocking modes, and customize the pin-out before automatically generating code. As a new entry to the 32-bit market, SiLabs has approached the issue of writing code for the relatively more complex architecture from the point of view of an engineer who is more accustomed to using an 8-bit MCU architecture; a theme that is developing into a trend for ARM licensees. Cypress, using the Cortex-M3 core in its PSoC family, used Embedded World to announce the latest extension to its IDE, PSoC Creator 2.0, which now includes component packs. The first pack includes SD Card interfaces and a royalty-free FAT file system, graphics LCD driver and royalty-free graphics library, a 4-wire resistive touch interface, and enhanced digital filter support. Cypress said it intends to release a new component pack every six to eight weeks.
Also focusing on the Cortex-M3 core and easing the engineer’s workload, Atmel announced two new variants to its SAM3 family, which for the first time added CAN capability to the family. In the two new families, the SAM3N and SAM3X, the X series integrates an Ethernet PHY, while both offer dual CAN interfaces and High Speed USB On The Go PHYs; features that Atmel claims differentiate the SAM3 from competitors. The new devices also offer Flash memory densities up to 512 Kbytes − at launch, Precision32 is limited to 256 Kbyte.
Perhaps more significantly, Studio 6, the latest edition of Atmel’s IDE, now supports both the company’s AVR and ARM Cortex based MCUs in a single unified IDE, intended to give engineers a ‘seamless’ migration from 8- to 32-bit architectures. Unified development environments that offer a graphical design interface and automatic code generation are definite trends among the ARM fraternity, demonstrating both the need for a higher level of software abstraction and the powerful benefits of a standard instruction set architecture. It is no wonder, however, that each of the IDEs are tightly integrated to the peripherals around the core, given that most of the design environments are offered free of charge.
While the Cortex-M3 has seen massive up-take from both licensees and the industry, the Cortex-M4 has arguably taken longer to reach significant penetration. This is predominantly due to a lack of products available, but ARM believes it has taken the last year or so for the industry to get the ecosystem in place and now expects to see significant developments with respect to the Cortex-M4. The first development, in what may prove to be many, came earlier this year when long-time ARM licensee Infineon announced its first standard products using an ARM Cortex core, and it was the M4 that it chose. Like SiLabs, Infineon believed it was not enough just to offer another Cortex-based MCU family; there needed to be differentiation. Thus, the first Cortex-based family of MCUs from Infineon — the XMC4x — uses the Cortex-M4F variant with floating-point support and is specifically targeting industrial control applications, where the extra compute power of the core can be put to good use.
However, while the XMC4x family targets motor control, where the power drawn by the MCU is potentially less important than the resulting power efficiency of the motors being controlled, Energy Micro has also opted to use the Cortex-M4F in its latest family of ultra-low power MCUs. The Wonder Gecko range (Figure 3) is the company’s first to use the M4 core, but still maintains the ultra-low power credentials of its other products, which, with the addition of sixty Wonder Gecko devices, now numbers in excess of 240 variants. It is documented as consuming just 180 μA/MHz in active mode, and 400 nA with just the RTC running, which positions it well not only against other Cortex-M4F devices but also Cortex-M3 alternatives.
Figure 3: Energy Micro’s latest Gecko family uses the Cortex-M4F core.
Even though the Cortex-M3, and to some extent the M4, received much of the limelight, there were also announcements at the ‘low end’ of the Cortex family, in the form of the Cortex-M0. This is the smallest and perhaps ‘least capable’ variant of ARM’s code-compatible Cortex family, but offering it is seen as an important part of delivering a complete ‘performance roadmap’ for many manufacturers. NXP has long been supplying MCUs based on the Cortex-M0 and is arguably the manufacturer of choice for ultra-low power and ultra-small packaging in the Cortex domain. Its latest offerings, the LPC1100XL and LPX11E00, represent the fourth generation of NXP’s Cortex-M0 range, and the XL (which stands for extra low power) pushes the active current consumption down from 130 μA/MHz to 110 μA/MHz while operating up to 50 MHz. It also reduces the Flash page size from 2 Kbyte to 256 byte and uses a new low power ‘embedded Flash’ technology that NXP plans to roll out across its MCU range (Figure 4). The LPC11E00 uses another proprietary memory technology to emulate EEPROM and up to 4 Kbyte is available. NXP said it will address the need for applications that require external EEPROM.
Figure 4: NXP’s latest LPC1100XL family uses the Cortex-M0 to achieve ‘extreme low power’ operation.
Rounding off its Cortex roadmap, STMicroelectronics made the significant introduction of the STM32 F0 family, its first to implement the Cortex-M0, which was pre-announced at the end of 2010. It takes the number of MCUs within the STM32 family to over 300.
As with other manufacturers, ST is using the Cortex-M0 to bridge the gap between the 8- and 16-bit users and existing 32-bit users. When ARM first targeted the MCU market several years ago, it was often cited that typical applications could not make use of the extra processing power. Subsequently, the first application spaces where Cortex-M based devices have prevailed have been those that need significant processing performance, hence the wider uptake of the M3. Now that the industry has become more used to the 32-bit paradigm — and applications have become more demanding — the M0 arguably becomes more viable for manufacturers. ST has also chosen to take the ‘mixed signal’ route with its STM32 F0 family, integrating a 12-bit ADC, 12-bit DAC, and two programmable analog comparators which are tightly coupled to the DAC. ST claims this delivers higher analog capabilities than competitors’ devices.
Beyond ARM
While it would be easy to assume that all new developments are ARM-based, the truth is that other cores — both licensable and proprietary — continue to have a place in the MCU domain. Specifically, Microchip continues to develop its proprietary 8- and 16-bit families — the PIC12 and PIC24. A new family in the PIC12 range features an innovative peripheral that provides non-overlapping complementary waveforms for comparators and PWMs (pulse width modulators), through what the company calls the ‘Complementary Output Generator’ (COG). This, Microchip said, is particularly useful in motor control applications.
Also, an expansion of the PIC24 Lite portfolio employs the company’s Extreme Low Power (XLP) technology to drive down both active and sleep currents to 150 μA/MHz at 1.8 V and 30 nA at 25ºC (typical) respectively. Microchip also used Embedded World to unveil the latest addition to its PIC32 range, which uses the licensed MIPS 32-bit core; the MX1 and MX2 are low pin-count versions but feature dedicated audio and capacitive touch sensing peripherals, as well USB OTG (Figure 5).
Figure 5: Microchip’s latest PIC32 offering features dedicated audio and capacitive-touch peripherals.
However, the prize for the most aggressive product introduction at Embedded World this year must surely go to Texas Instruments with the launch of its ‘Wolverine’ range of MSP430 MCUs. The MSP430 family is based on a proprietary 16-bit core and has for some time targeted low power applications including smart sensors that use energy harvesting techniques — possibly the most demanding application from a low power point of view. The Wolverine family claims to ‘slash’ the power requirements by 50 percent versus both its competition and existing MSP430 families.
These claims may be justifiable (at least for now), as it purports an active current of less than 100 μA/MHz and 360 nA in RTC mode. Of course, these claims will be made under a ‘comparable’ caveat and as it uses a proprietary core that may be difficult to challenge, particularly by a device based on the Cortex-M0 core. However, the figures stand and what may be more significant is that the process is qualified over a wide temperature range, which means that the power requirements are stable beyond 25ºC. This, claims TI, is not the case with its competitors’ processes, where the power requirements increase significantly with temperature. TI said it has successfully pushed out the ‘knee’ of the power/temperature curve, so the current consumed stays lower for longer.
The process is described as a mixed-signal ultra-low leakage and ultra-low power process that has been optimized for any temperature. It follows therefore that at higher temperatures TI expects to see even more than a 50 percent improvement in power consumption, although at launch this had not been qualified.
Another significant aspect of Wolverine is that is utilizes FRAM memory, which does put an upper limit on how fast the parts can run, but TI said it is targeting a clock frequency range of between 25 and 50 MHz with Wolverine, with a focus on industrial applications thanks to its stability over temperature.
The trends for smaller, faster, and cheaper have, for some time now, been giving way to new trends: lower power, smarter hardware, and easier software. This year’s announcements at Embedded World have highlighted this and they look set to continue for some time to come. Of course, manufacturers are well aware that they still have to meet these new demands while observing the need for smaller, faster, and cheaper devices.
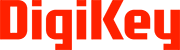
免责声明:各个作者和/或论坛参与者在本网站发表的观点、看法和意见不代表 DigiKey 的观点、看法和意见,也不代表 DigiKey 官方政策。