Dedicated ICs Ease Wireless Power Control Challenge
投稿人:DigiKey 北美编辑
2016-06-16
Wireless charging (also referred to as inductive charging or wireless power) has demonstrated promise ever since Nikola Tesla claimed he had discovered the basic principles and that it just needed an enterprising individual to commercialize the technology. That was back in 1921. Since then systems have come and gone without the sector really catching fire.
Technical hurdles, competing standards and consumer disinterest have been to blame for slow progress, but things are starting to change to the extent that analysts are getting excited. Consultants IHS, for example, forecasts that the wireless charging market will expand to $8.5 billion by 2018, up from $216 million in 2013. One reason for this optimism is the recent announcement that two formerly competing standards bodies are joining forces to jointly promote the technology. The second is that both inductive and resonant wireless charging have largely overcome the technical challenges to wireless charging and both have the support of a wide base of semiconductor vendors.
Widely-deployed wireless charging has the potential to increase consumer convenience for battery replenishment in the same way Wi-Fi has done for connectivity. This article takes a look at how the chip makers have made it much easier for designers to enter this lucrative sector by introducing integrated transmitter and receiver devices upon which engineers can base their circuit designs.
Basic principles of wireless charging
Fundamentally, wireless charging is the transfer of energy from a transmitter coil to a receiver coil using induction. The transmitter coil generates an oscillating magnetic field which induces an AC voltage in the receiver coil which is then rectified and regulated to charge a battery.
The efficiency of the power transfer depends on the coupling (k) between the inductors and their quality (Q). The coupling is determined by the distance between the inductors (z) and the ratio of the coil diameters. Coupling is further determined by the shape of the coils and the angle between them.
Tightly coupled systems – whereby the two similarly sized coils are held close, are well aligned and parallel – are more efficient and restrict troublesome electromagnetic interference (EMI) (Figure 1.) The higher efficiency limits unwanted heat. Loosely coupled systems can be used in situations where it's difficult to limit the gap between the coils and/or match the coil sizes, but at a trade-off of lower efficiency and greater EMI emissions. The degree of coupling is determined by the "coupling factor" and is a measure of how much of the magnetic flux generated by the transmitter coil is captured by the receiver coil. Perfect coupling, whereby all the flux is captured, has a coupling factor of 1. Practical systems typically have a coupling factor of 0.3 to 0.6.
Figure 1: Tightly coupled wireless chargers employ well aligned, similarly sized coils in close proximity and are more efficient while producing fewer EMI problems. (Image courtesy of the Wireless Power Consortium)
Resonant coupling, whereby transmitter and receiver coils are operated at a resonant frequency, generally improves system efficiency. Intuitively then, tightly-coupled coils both operating at their resonant frequencies should produce the most efficient system. However, this is not the case because there is a minimum distance at which each coil can maintain resonant operation. This minimum distance depends on the size of the coils and operating frequency, but is greater than the typical coil separation of a tightly coupled system. The physics is complicated but in essence, if two resonating coils are moved too close, their magnetic fields "collapse" and power transfer ceases. It turns out that the most efficient wireless power transfer occurs when using tightly-coupled coils operating close to – rather than exactly at – their resonant frequencies.
However, where resonant coupling has its advantage is in improving the efficiency of systems where tight coupling is not possible or increasing consumer convenience by lowering the precision with which the device to be charged has to be placed on the charging pad. Unlike the "focused" magnetic field of inductive systems, resonant systems produce a much wider field, allowing multiple objects placed within range to receive reasonable amounts of power.
Another option is a charging station with multiple coils, which offers the wider charging area of resonant charging (allowing more mobile products to be charged simultaneously) while still retaining the advantages of tight coupling (Figure 2).
Figure 2: Multiple overlapping coils provide a wider charging area while still retaining the efficiency advantages of tight coupling. (Image courtesy of the Wireless Power Consortium)
Apart from the technical challenges, competition between the standards bodies has been another major reason for the slow introduction of wireless charging. The Wireless Power Consortium (WPC) developed the Qi (pronounced "Chee") specification, which includes both inductive and resonant wireless charging, while the Alliance for Wireless Power (A4WP) and the Power Matters Alliance (PMA) both advocated resonant charging. In June 2015, there was consolidation, when A4WP and the PMA merged to form the AirFuel Alliance which now promotes both inductive and wireless charging technologies.
The specifications include provisions for higher-power versions. For example, Qi's low-power specification delivers up to 5 W (for smartphone charging) with the medium-power specification delivering up to 120 W (for tablets and laptops). A high-power specification delivering up to 1 kW is under development.
Closing the loop
While the design of a wireless charging system is simple in concept (Figure 3), practical circuits are more difficult to implement. Apart from selecting coil topologies such that energy is transferred as efficiently as possible, the major design challenge comes from control and compensation of voltage, frequency and duty cycle.
Figure 3: Wireless charging systems are simple in concept (as this schematic indicates) but detailed design is more challenging. This design uses backscatter modulation for the unidirectional communication that closes the feedback loop. (Image generated using DigiKey Scheme-it based on original image courtesy of Texas Instruments)
Control and compensation demands a feedback loop between the receiver and transmitter. Because this is a wireless technology, there is no physical link between the transmitter and receiver coils. Consequently, wireless techniques such as backscatter modulation or a low-power RF link are used to complete the feedback loop.
The latter technique is less common but is starting to make inroads. The AirFuel Alliance, for example, encourages the use of technologies such as Bluetooth low-energy or Wi-Fi to communicate between receiver and transmitter or vice versa (remembering that the devices most commonly in need of a top-up, such as smartphones, tablets and laptops, typically have built-in Wi-Fi and Bluetooth). The advantage of a bidirectional RF link is more precise control over the charging process than can be achieved with backscatter modulation. The downside is additional cost and added complexity.
Despite the cost and complexity, feedback is vital, particularly when charging the lithium ion (Li-ion) batteries used in the majority of today’s portable devices. These cells are very sensitive to damage from rapid charging when approaching full capacity and overcharging. (See the TechZone article "A Designer's Guide to Lithium (Li-ion) Battery Charging".)
To communicate this feedback, the majority of contemporary wireless charging systems use backscatter modulation to form a unidirectional communication link between the receiver and transmitter (it's a similar system to that used by passive RFID tags). In essence, the technique takes advantage of the fact that a load on the receiver coil will generate an electromagnetic wave that can induce a current on the transmitter coil (the reverse process to the main wireless charging operation). With appropriate (relatively inexpensive and simple) circuitry, the induced current can be modulated and interpreted to determine how the load on the receiver varies as the battery charges. Such information can then be used to regulate the energy provided by the transmitter coil to power the charging process.
Wireless charging solutions
Designing the wireless charging products using discrete components is tricky and requires considerable experimentation so it's not for designers with limited experience and tight time constraints. However, that doesn't exclude the novice from developing wireless charging products. The key to success is to base the design around one of several chipsets which integrate much of the control and compensation functionality demanded by a wireless charging system into a single chip.
One example of such a device is Semtech's TS80000 wireless charging transmitter IC and its sister component, the TS81001 receiver IC. The TS80000 looks after the control, communication and compensation of the wireless charging circuit and can provide power outputs up to 40 W while supporting Qi- and AirFuel-compliant, as well as proprietary, applications. The TS80000 can be configured to drive single- or multi-coil applications, in half- and full-bridge systems.
The TS80000 looks after the backscatter modulation decoding and adjusts the energy levels accordingly. An integrated PID filter provides the necessary compensation for the feedback loop for high-precision control of duty cycle, frequency and bridge voltage. The TS80000 transmitter IC is recommended for use with Semtech's TS61001 full-bridge FET driver while the TS81001 receiver IC is recommended for use with Semtech's TS51111 synchronous rectifier.
Texas Instruments (TI) supplies several wireless charging solutions, among them the bq500511. This wireless power transmitter can be combined with the company's bq50002 analog front end device to integrate all functions required to create a Qi-compliant or proprietary 5 V transmitter. The chip "pings" the surrounding environment for the receiver devices to be powered, safely engages the device to be charged, receives communication from the device and manages the power transfer according to the WPC v1.2 specification.
A nice bonus with this chip is a function called Foreign Object Detection (FOD) which protects against power loss due to energy sinking into metal objects misplaced in the magnetic field.
The wireless power transmitter works in partnership with devices such as the bq51051, a Qi-compliant wireless power receiver. TI claims the bq51051 provides efficient AC-to-DC power conversion and integrates the digital controller required to comply with Qi v1.1 communication protocol. This device is notable because it integrates a Li-ion battery charge controller, which allows for "direct charging". TI explains that this improves overall efficiency by up to 10 percent compared with a wireless power receiver paired with a separate downstream charger chip (Figure 4.) Other advantages are cost and space savings.
Figure 4: Direct wireless charging systems––whereby receiver and battery charge controller are combined into a single chip––are up to 10 percent more efficient than discrete systems. (Image courtesy of Texas Instruments)
NXP also supplies a wireless charging solution based on its MWCT1111 wireless charging transmitter. The device supports any industry-compliant 15 W single-coil topology and uses the company’s proprietary core, which is optimized for power-conversion applications. The MWCT1111 perform tasks such as digital demodulation of backscatter modulation, FOD and power-supply regulation.
The MWCT1111 can work in conjunction with sister devices such as the NXP MWPR1516, a receiver that adheres to the WPC specification and which has the potential to support other future standards. Two notable aspects of the device are its ARM® Cortex®-M0+ core and frequency shift keying (FSK) feature which allows for development of wireless bidirectional communication architecture between transmitter and receiver.
Quick entry to a lucrative market
The convenience of wireless charging coupled with improvements in efficiency (some manufacturers now claim up to 75 percent efficient energy transfer from input to battery) and adoption of industry standards has raised the technology's profile.
Design engineers tackling wireless charging are advised to consider adhering to one of the published specifications as it will likely improve the commercial opportunities for an end product. For example, several mobile product vendors have adopted one or both of the specifications for their smartphones and tablets.
Designing a system from the ground up is feasible and might result in a lower bill of materials (BOM), but requires expertise and familiarity with the wireless charging standards. Less experienced engineers would be advised to base their systems on a wireless charging chipset, available from a range of reputable semiconductor vendors, which has been optimized for efficiency, includes useful capabilities such as FOD, and is certified for compliancy with one or more of the major standards. The savings in design time that the novice engineer is likely to make by employing a chipset will more than cancel out the increased component cost compared with a discrete solution.
References:
- "Magnetic Resonance and Magnetic Induction," Wireless Power Consortium.
- "Why Not a Wire? The case for wireless power," Kaylan Siddabattula, Texas Instruments.
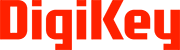
免责声明:各个作者和/或论坛参与者在本网站发表的观点、看法和意见不代表 DigiKey 的观点、看法和意见,也不代表 DigiKey 官方政策。