Addressing the Challenges of Power Management in Wireless Sensor Networks (WSNs)
投稿人:DigiKey 欧洲编辑
2013-07-16
Incremental improvements in the energy efficiency of electronics over the last decade have brought the electronics industry close to the point of practical, cost-effective Wireless Sensor Networks (WSNs). No doubt, many potential applications for these networks exist and they are highly attractive, offering quick and easy installation, no need for pre-existing infrastructure to support them, flexibility, scalability, and more. However, until recently these obvious advantages have been hard to deliver, primarily due to the challenges of providing the necessary remote, and ideally autonomous power. Batteries have been the workhorse solution, but inherently impact node reliability, operating lifetime, size, and the desire of many that WSNs operate independently of the power grid. Alternative strategies have been sought as battery capacity improvement moves at a snail’s pace compared to the rate at which semiconductor developments occur (c.f. Moore´s law).
Therefore, it is no surprise that considerable interest now surrounds energy harvesting - the exploitation of ambient physical energy sources to provide a perpetual power source for wireless networks reducing or possibly eliminating the reliance on primary batteries. IDTechEx, a research company in this market, indicates that $700M was spent on harvesting in 2012 and revenue from harvesting is set to grow to $5bn over the next decade1 (i.e. > 20% annual growth rate).
Wireless sensor networks have been enabled today by the availability of both ultra-low power radios and optimized low power microcontroller products. However, perhaps the biggest challenge remaining is that of power management for these systems. This article will look at some of the challenges of supplying long operating life for autonomously powered WSNs and considers some of the current power management products available including: Advanced Linear Devices' EH42x5/EH300 parts, the LTC3105 and new LTC3129 from Linear Technology; a new low power boost from Intersil (ISL9111A); the BQ25504 from Texas Instruments and finally STMicroelectronics’ SPV1040.
The article concludes by answering the question of whether energy harvesting now a viable source of power for autonomous micro-power systems.
Energy harvesting practicalities
The ambient power available from physical resources in the environment varies quite considerably, especially in terms of power densities achieved. Perhaps the most obvious and widely exploited sources of energy are photo-voltaics (PVs) using solar radiation.
However, other practical methods of energy harvesting include thermoelectric generators (TEGs) exploiting the Seebeck effect, as well as electro-mechanical systems able to exploit the piezo-electric effect. Figure 1 below shows power available from some examples of harvested sources.
Energy Source | Harvested Power |
Vibration/Motion | |
Human | 4 μW/cm² |
Industry | 100 μW/cm² |
Temperature Difference | |
Human | 25 μW/cm² |
Industry | 1-10 mW/cm² |
Light | |
Indoor | 10 μW/cm² |
Outdoor | 10 mW/cm² |
RF | |
GSM | 0.1 μW/cm² |
WiFi | 0.001 μW/cm² |
Figure 1: Available average powers from sample energy harvesting sources (courtesy of Texas Instruments).
Considerable research and recent development work has looked at these and other potential harvesting techniques including RF power. It is worth keeping in mind the level of power available across harvesting techniques, as it soon becomes clear that power management is crucial if autonomous power is to be a workable solution. Be aware that depending on the harvested source, the nature of these supplies can be highly sporadic (ambient light and vibration being good examples here). Rarely is there enough power on hand for the harvester alone to sustain the operation of the WSN system. Almost always designers have to deploy some clever energy storage system as well. The role of the power or energy management system is to ensure that harvesting always exceeds a break-even energy point (i.e. the power harvested exceeds power used in daily operation by some margin). Achieve that goal and you have a perpetual power solution – or at least one that will likely exceed any normal operating lifetime goal.
The importance of power management in harvesting applications
Having now established the critical role of power management, let’s look at the basic high-level architecture of a WSN as shown in Figure 2. The system comprises a low-power radio system, some form of sensor signal(s), and a processing system to generate useful information within the sensor node. Much has been made of the algorithmic approaches to handle the communication challenges of a mesh of WSNs. Most people have a sense that the only way to achieve a functional WSN within a constrained energy budget is to deploy basic power management techniques such as duty cycling to keep average power demands within manageable limits. This is especially the case where a power budgeting exercise will clearly show that the radio requires quite significant peak powers over the life of the system.
Figure 2: High level WSN block diagram.
Recent system proposals have shown that an average WSN node typically requires between 20 and 100 µW of average operating power. These figures will be affected both by the complexity of the sensed signal (and its data conversion and processing needs) as well as the interrogation interval of the WSN node. Compare that to the output from an indoor solar harvesting system that may only achieve 10 µW/cm2 (Table 1) from the low ambient light levels available.
There are several additional problems when harvesting energy including:
- Managing the mismatch in the voltages available from a harvester and the regulated system voltages needed to drive sensor, radio and processing circuits
- Ensuring maximum power is extracted from the harvested source requires impedance matching between the harvesting source and the following power circuitry
- Managing the all-important system start-up conditions – a bootstrapping process. This is particularly tricky as the harvester power alone is unlikely to be able to bias conventional circuitry
- Ensuring long term, reliable operation of the WSN under widely varying operating conditions and ensuring a long term, net positive energy storage is supplied
Solutions to the WSN power management challenges
Consider maximum power extraction from DC energy harvest sources (PVs and TEGs). Most important in extracting energy is establishing an operating point enabling maximum power output from the harvester. Maximum power point tracking (MPPT), as it is known, has been written about in many places as it effects the operation of a PV cell (and TEGs), but here’s a brief reminder. The graph of Figure 3 shows plots of the voltage and current characteristic of the PV cell together with output power available from a typical PV cell. The electrical equivalent circuit model of a PV cell is shown in Figure 4. It is clear from this power plot that the maximum power point for a given PV cell occurs around 75-80% of the open circuit voltage of the panel. To extract this maximum power, an interface circuit is needed that can adjust its input impedance to match the ideal operating point.
Figure 3: Single PV cell current, voltage and power plot highlighting the MPP point.
Figure 4: Equivalent electrical circuit of a PV cell.
Handling the mismatch between harvester output voltage and that needed by the system can be achieved via standard architectural design approaches. With a standard single PV cell offering an output level of perhaps 1 V, an inductive boost power convertor will usually be required. This approach has the benefit that MPPT can be provided through control of the duty cycle ratio of the switching conversion. Equally it may be possible to achieve a simpler switched capacitive boost, though in this case it is likely to be harder to implement a workable MPPT system given the integer nature of step-up ratios of such designs.
Also, given the low level output currents provided from the example solar cell above, it is clear that any power management circuit to be effective in its interface role between harvester and system needs to have firm control over leakage currents – given that nominally leakage currents can be close to the net output current available from the harvesting source if not well managed. Clearly then, what may be acceptable in traditional power design can have a make-or-break impact on harvester function.
Toughest of all to solve is the start-up operation. This is considered in the context of commercial solutions currently available to the energy-harvesting world. Because of the technical implementation challenges highlighted above, there is a rather scant availability of off-the-shelf solutions today. Thankfully, greater interest is emerging from semiconductor suppliers and the last few years has seen meaningful advances made both in products released and their ongoing research efforts.
Advanced Linear Devices (ALD) has been promoting a low power, PCB based module technology for harvesting applications over the last few years in the shape of the EH4205 (50 Ohm input impedance) and EH4295 (950 Ohm input impedance). The claimed benefit of this technology is the complete absence of the need to deploy a battery for harvester operation and its zero power drain in sleep mode. The modularized solution exploits ALD’s precision sub-threshold micro-power EPAD MOSFET technology in a power-miserly, self-oscillating system. Minimum harvester start-up power for these modules is claimed to be as low as 230 µW with operation from sources with output voltages as low as 75 mV. The output from the module is an AC signal which is often coupled into ALD’s own harvester power supply modules (EH300 family) though equally the output can be rectified and used to power a micro-power inductive boost convertor. Costs of this implementation appear to be relatively high and ALD seems to recognize this as the company looks to be readying a monolithic IC strategy in this field.
One of the broadest solution portfolios available can be found from Linear Technology. Under energy harvesting, they claim more than a dozen devices. Their portfolio targets a range of harvesting sources with efficient low operating current switchers and battery chargers.
A noteworthy part is the small (12-pin MSOP) LTC3105 featuring a low 250 mV start-up capability and MPPT control targeting harvesting from a single PV cell. The part can provide a trickle charge for a battery such as a single Li-ion cell. It handles start-up using a proprietary approach where an internal low voltage circuit controls ramp-up of an auxiliary supply rail. Establishing this biasing rail (at 1.4 V) takes typically between 20 and 100 µs depending on the harvester source characteristics. Once normal continuous operation for the device is established, the internal low current LDO is enabled and will start conducting depending on its set voltage. The LDO requires only 105 mV of dropout to obtain regulation. The output defaults to 2.2 V but can also be resistor programmed to outputs in the range 1.4 to 5 V. Output from the LDO is usually used to power the WSN microcontroller and can support a guaranteed minimum of 6 mA. The boost convertor section of the LTC3105 is able to output a peak of around 0.5 A and its output voltage can be programmed from 1.5 to 5.25 V. A power good flag, MPP power adjust, and soft-start complete the functional roll call of this useful IC. The LTC3105 shows its harvesting credentials by achieving a 24 µA operating quiescent current.
A new member of LTC’s ultra-low power DC/DC convertors is the 200 mA synchronous buck-boost controller, the LTC3129. Whilst not achieving ultra-low voltage start-up, with its minimum start-up VIN limited to just 2.42 V, this switcher has a lot to commend it for use in powering WSNs. Foremost amongst the operating parameters is the 1.3 µA quiescent current in burst-mode operation, which in full shutdown falls to 10 nA. The current mode buck-boost design supports output voltages either above, below or equal to the input voltage level (ranging from 1.4 to 15.75 V). This switcher can achieve greater than 85% efficiency under most operating conditions. Using a 1.2 MHz PWM switching architecture minimizes the size of critical inductor and capacitor components. The design is enhanced by its built-in loop compensation and soft-start circuits. An unusual and accurate RUN pin comparator input is offered to allow user programmability and thus predictable regulator turn-on thresholds. The LTC3129 also has a MPP capability. The device is illustrated below.
Figure 5: Application circuit of LTC3129 (courtesy of Linear Technology).
Intersil, well versed in high efficiency power management products offers a sub 1 V boost IC. The ISL9111A features a minimum start-up at threshold of 0.6 V (for the A grade part). This synchronous boost, offered in a small, six lead SOT23 package, features a built-in switch capable of supporting a peak inductor current of 1 A giving continuous output currents of a few hundred milliamps, depending on the specific input and desired output voltage conditions. The part features PWM switching at 1.2 MHz, but in light load conditions operates in a pulse-skipping mode reducing quiescent operating current to just 20 µA. The device is offered in both adjustable and fixed output versions. It features a 1 µA logic shutdown pin which provides an output disconnect capability.
Texas Instruments has been one of the most aggressive developers of key power management technologies supporting WSN implementations. This is no surprise given that TI has been at the forefront of all major technologies associated with WSNs; low power embedded processing; low power radios; battery management and power conversion driving an obvious interest their holistic approach to WSNs.
One of TI’s initial forays into the energy harvesting space was marked by the launch of its BQ25504 IC at the end of 2011 illustrated in Figure 6. What sets this device apart from much of what has been talked about so far is the fact that it was one of the first to combine an ultra-low power, high performance boost switcher with a battery management system, effectively providing a fully managed, single chip, energy harvesting solution.
Figure 6: Application circuit of BQ25504 (courtesy of Texas Instruments).
The BQ25504 offers flexibility both in the harvesting sources it supports and in the supported energy storage options. Storage solutions can include standard primary batteries, thin-film batteries, capacitors, and even super-caps. Power management features that prevent potential damage to the customer selected storage system include the monitoring of both under- and over-voltage thresholds. In addition, a third threshold is specified indicating a ‘battery good’ condition.
The special input structure of this part has been designed to achieve start-up at around 330 mV as well as to sustain energy harvesting capability all the way down to 130 mV. To manage the sporadic nature of harvested energy the first priority of the BQ25504 is to charge up a storage capacitor (CSTOR). This will first be attempted from the local energy storage system attached. If that is not possible because there is not enough energy on hand, then the cold-start system will switch in. Cold-start is facilitated when a harvested source is applied to the VIN pin with enough energy (the minimum power to drive the cold-start system is specified as 50 µW) and input voltage should exceed the part’s 330 mV threshold. The cold-start system consists of an unregulated low power booster circuit. After a charging delay, the voltage on CSTOR should rise to around 1.8 V at which point the IC achieves functional biasing and normal operation. From here, regulation passes over to the primary boost regulator of this IC, which, similar to other solutions already discussed, operates at a switching frequency of 1 MHz whilst using pulse frequency modulation to boost efficiencies.
Ensuring minimal loss of energy through controlling leakage current is where the BQ25504 excels. TI claims that the leakage current on the VBat pin (the energy store) is kept to a maximum of just 80 nA. A further TI claim for the BQ25504 is its typical operating quiescent current of just 330 nA.
The BQ25504 is packaged in a small, 3x3 mm, sixteen-lead QFN package. Additional features includes a sampling MPP control loop which may be driven externally to implement more complex MPP algorithms run on the WSN’s own microcontroller. The battery good indication is toggled by the part to indicate to the external controller when the energy store is reaching a critical low state-of-charge. It uses this feature to implement load-shedding strategies, thus providing a graceful system power down.
A targeted solar charger, the SPV1040 from STMicroelectronics is another new, low power boost/charger option. The simple 8-pin device claims to operate from as little as 0.3 V and is capable of delivering a maximum output power of 3 W. It has been designed to maintain charge on a battery cell with a charging voltage that can be set between 2 and 5.2 V. The device includes an interesting MPP control loop that uses a so-called ‘perturb and observe’ algorithm to establish the MPP point. The device can operate in either constant current or constant voltage regulation modes. To protect the input structures a reverse polarity protection has been included in this device. To protect the energy storage device over-voltage, over current and thermal protection is provided. The company claims high efficiencies for the switcher but does not offer any guidance on minimum start-up power needed.
Conclusions
Without a doubt, many more practical harvesting options are emerging today. However, there remains a relatively limited range of workable power IC choices for designers to use right now. A survey of recent research topics presented in forums such as the ISSCC suggests we can expect to see a range of new and exciting parts emerge in the next few months and innovation remains as healthy as ever. Both Texas Instruments and Linear Technology are preparing full market release of new solutions.
Footnote
Several suppliers offer energy harvesting demonstrators through DigiKey. Four that may be of interest to the reader using the parts mentioned are detailed in Figure 7 below.
DigiKey Part Number | Main Power Device | Main Energy Source | Chip Supplier | What’s Included? |
296-29834-ND | BQ25504 | N/A | Texas Instruments | IC – this is an electrical EVB with no harvesting source |
1014-1201-ND | EH4295 & EH300 | N/A | Advanced Linear Devices | Parts and connectors |
497-11286-ND | SPV1040 | Solar | STMicroelectronics | IC – this is an electrical EVB with no harvesting source |
296-23113-ND | TPS61200 | N/A | Texas Instruments | IC – this is an electrical EVB with no harvesting source |
Figure 7: Summary of some energy harvesting demos available from DigiKey.
References:
- IDTechEx: Energy Harvesting and storage for Electronic Devices 2012-2022: Forecasts, Technologies, Players. Oct. 2012
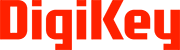
免责声明:各个作者和/或论坛参与者在本网站发表的观点、看法和意见不代表 DigiKey 的观点、看法和意见,也不代表 DigiKey 官方政策。