Use Edge AI to Extend Battery Life in Wireless Motor Monitoring
投稿人:DigiKey 北美编辑
2025-03-27
Artificial intelligence (AI) has been the subject of considerable attention. Among its many applications is at the edge, where it can enhance condition-based monitoring (CbM) of robotics, rotating machines, and their motors. Supported by wireless reporting, it can analyze critical data related to the health and performance of a machine for predictive maintenance and send out alerts as needed. Performing this monitoring function at the edge reduces power consumption and latency while allowing optimal use of available wireless bandwidth.
An effective system performing this edge AI CbM function requires a carefully chosen and integrated set of components supporting multiple sensor inputs, including accelerometers, AI processors, and power management.
This article examines the motor-monitoring challenge. It then presents a practical example of edge AI performing this function using analog, digital, and mixed-signal ICs from Analog Devices. It shows the design, functionality, and construction of a complete battery-powered system using a wirelessly connected vibration evaluation kit.
The motor-monitoring challenge
Targeted predictive maintenance done early in a machine’s life cycle reduces the risk of production downtime. It yields improved reliability, significant cost savings, and increased productivity on the factory floor.
Vibration is the most common and valuable among the many rotating machine parameters that can be monitored. While vibration is not hard to measure, using and reporting this data meaningfully are challenges requiring data analysis, advanced algorithms, and an effective connectivity scheme. All this must be accomplished with minimal power to maximize battery life.
For this purpose, Analog Devices developed the EV-CBM-VOYAGER4-1Z Voyager4 Wireless Vibration Evaluation Kit (Figure 1). This kit is a complete, low-power vibration monitoring platform that allows designers to rapidly deploy a wireless solution to a machine or test setup. It uses an edge AI algorithm to detect anomalous motor behavior and trigger a call for machine diagnostics and maintenance.
Figure 1: The EV-CBM-VOYAGER4-1Z Voyager4 Wireless Vibration Evaluation Kit allows designers to quickly deploy a wireless edge AI monitoring solution to a machine or test setup. (Image source: Analog Devices)
The Voyager4 has a diameter of 46 millimeters (mm) and a height of 77 mm and comes with an M6 threaded hole in the base for a screw stud or an adhesive mount to a motor casing. It is constructed using an aluminum base and wall housing. A lid of ABS plastic is used to avoid shielding the antenna of its Bluetooth Low Energy (BLE) link.
The BLE and edge AI microcontroller unit (MCU) printed circuit board (pc board) is vertically mounted with a battery attached to a standoff. The microelectromechanical systems (MEMS) sensor and power pc boards are placed on the base, close to the monitored vibration source.
Sensors operate with very low duty cycles in a typical wireless motor-monitoring system. They wake up at a scheduled interval, measure the parameters of interest such as temperature and vibration, and then transmit the data back to the user where it is analyzed for possible action.
In contrast, the Voyager4 system takes advantage of edge AI detection to limit the use of the power-hungry radio. When the sensor wakes up and measures data, the data is only sent back to the user if the MCU detects an anomaly. The result is an increase in battery life of at least 50%.
The Voyager4 system begins with the ADXL382-2BCCZ-RL7, a 16-bit, 8 kilohertz (kHz) triaxial digital MEMS accelerometer IC (Figure 2, left) that is used to capture vibration data.
Figure 2: Shown is the decision-making path at the core of the Voyager4 system. (Image source: Analog Devices)
The raw vibration data follows path (a) to the MAX32666GXMBL+, a BLE radio plus Arm® Cortex®-M4F DARWIN MCU. This data is used to train an edge AI algorithm. The data is then sent to the user over a BLE radio link (or can be sent via a USB port).
After an initial Voyager4 training phase, the vibration data can follow path (b), where the MAX78000EXG+ MCU’s edge AI algorithm will use the data to predict faulty or healthy machine operation. If the data is healthy, there is no need to use the MAX32666 radio, saving significant battery power, and the Voyager4 sensor operation can follow path (d). At the same time, the accelerometer returns to sleep mode, also saving power. However, if the algorithm predicts faulty or suspect vibration data, the system follows path (c) with a vibration anomaly alert sent to the user over BLE.
Additional ICs complete the design
The complete Voyager4 system has accelerometers, AI, power management, transient protection, data integrity, and wireless connectivity ICs (Figure 3). In addition to the ADXL-832 MEMS accelerometer, the ultra-low-power, 14-bit, 100 Hz ADXL367BCCZ-RL7 triaxial MEMS accelerometer is used to wake up the BLE radio from deep sleep mode when a significant vibration or shock event occurs. This wake-up device consumes only 180 nanoamperes (nA), contributing to substantial power savings.
Figure 3: The complete Voyager4 system uses a combination of accelerometers, AI, and other processor, power management, transient protection, data integrity, and wireless connectivity ICs. (Image source: Analog Devices)
Using two accelerometers may seem redundant, but each has its role. The lower-performance, ultra-low-power ADXL367 provides ongoing monitoring and initiates a wake-up, while the more precise ADXL832 provides high-accuracy, high-speed data.
For signal-path management, the ADG1634BCPZ-REEL7 analog switch, a 4.5 ohm (Ω), four-circuit, 2:1 single-pole double-throw (SPDT) CMOS device, is used to route the MEMS’ raw vibration data to either the MAX32666 BLE radio or the MAX78000 AI MCU, with the BLE MCU used to control the switch.
Several other peripherals are also connected to the MAX32666 BLE MCU, including the MAX17262REWL+T LiFePO4/Li-ion fuel gauge IC used to monitor battery current. The MAX32666 can stream the ADXL382 MEMS raw data to the host using either BLE or USB with the Future Technology Devices International (FTDI) FT234XD-R USB-to-basic serial UART interface IC.
On the electrical side, the MAX3207EAUT+T transient voltage suppression (TVS) diode array, with a negligible capacitance of just 2 picofarads (pf), provides ±15 kilovolt (kV) protection per human-body (HBM) and air-gap models. For data integrity, the DS28C40ATB/VY+T Secure Authenticator delivers a core set of cryptographic tools derived from integrated asymmetric (ECC-P256) and symmetric (SHA-256) security functions.
Advanced power management leads to minimum consumption
The details of power management illustrate how battery life is affected in the context of the many power phases of the Voyager4 operation. This management is centered on the multifaceted MAX20355EWO+ power management integrated circuit (PMIC), a power-line communication and buck-boost converter with a proprietary ModelGauge fuel gauge.
This IC incorporates two ultra-low quiescent current buck regulators and three ultra-low quiescent current low-dropout (LDO) linear regulators. The output voltage of each LDO and buck regulator can be individually enabled and disabled, and each output voltage value can be programmed through the device’s I2C interface. The BLE processor enables or disables individual PMIC power outputs for different Voyager4 operating modes. Additional power regulation is provided by the MAX38642AELT+T, an adjustable, single-output, positive-voltage buck regulator that sources up to 350 milliamperes (mA).
In operation, the features of the Voyager4 depend on the BLE and AI operating modes to determine the MAX32666 and MAX78000 active or inactive modes that are critical to minimizing overall power (Figure 4).
|
Figure 4: To minimize overall power consumption, the Voyager4 shifts its power-mode features between active and inactive states depending on the BLE and AI operational phase. (Image source: Analog Devices)
For example, in training mode, the BLE MCU must first advertise its presence in the BLE network and then connect with the network manager. The Voyager4 then streams the ADXL382 MEMS raw data over the BLE network to train an AI algorithm on the user’s PC.
Approximately 0.65 milliwatts (mW) of power is consumed when the evaluation kit operates in training mode, and BLE is active, advertising, connecting, and transmitting data once per hour. If the Voyager4 sensor operates in AI mode, the power consumption drops to 0.3 mW, even when the sensor is active once per hour. Test data shows that a sensor that does not have to transmit raw BLE data can consume up to 50% less power (Figure 5).
Figure 5: A sensor that does not have to transmit raw BLE data can consume up to 50% less power. (Image source: Analog Devices)
As a result of the 0.3 mW power consumption, a battery life of up to two years is possible with a single 1500 milliampere-hour (mAh) battery, and over seven years is achievable with two AA-size 2.6 ampere-hour (Ah) batteries. For maximum lifespan, these AA cells should be the type that is intended for low baseline operating current with only periodic pulses. These can operate for five years minimum under these conditions, while some higher-end versions can provide power for over 20 years.
Mechanical modal analysis is also needed
Designing a suitable mechanical enclosure requires modal analysis, which is used to understand the vibration characteristics of the structure being monitored. This analysis provides insight into a design's natural frequencies and normal modes (relative deformation).
The primary concern in modal analysis is to avoid resonance, where the natural frequencies of a structural design closely match that of the applied vibration load. For vibration sensors, the natural frequencies of the enclosure must be greater than that of the applied vibration load measured by the MEMS sensor. For Voyager4, the 3-decibel (dB) bandwidth across the x, y, and z axes is 8 kHz, so the sensor enclosures should not have any significant resonances at less than 8 kHz.
The analysis was performed using ANSYS and other simulation tools supplemented by appropriate plug-ins. These tools enable the exploration of the effects of geometry, material selection, and mechanical assembly on the frequency response of the sensor enclosure. The analysis factors in that the sensor enclosure mass, stiffness, and natural frequencies are interrelated.
The Voyager4 sensor assembly was simulated using 3003 aluminum alloy for the enclosure bottom and mid-section, with ABS-PC plastic for the lid. The modal analysis simulation showed fourteen mode results occurring in the frequency range of interest.
Several modes were of initial concern but were judged as non-problems upon further study (Figure 6). Mode 1 (Figure 6, left) was located far from the sensor pc board at the base; this slight resonance should not affect the ADXL382 MEMS’ performance. Mode 7 (Figure 6, center) occurred at approximately 7.25 kHz on the z (vertical) axis. While it shows some appreciable effects on the vertical wall of the enclosure, the base itself was not strongly affected by this mode.
This modal simulation shows that no modes would have an appreciable effect on the ADXL382 sensor pc board located on the enclosure base, and the 8 kHz (3 dB) bandwidth of interest should not have significant mechanical resonances.
Figure 6: Mechanical modal analysis shows that two mechanical resonances identified as a possible concern would not be a problem (mode 1 (left), mode 7 (center)); these results were confirmed by a Voyager4 used in a shaker-table test (right). (Image source: Analog Devices)
The simulation results were validated using a Voyager4 sensor placed on a modal shaker, with a constant 0.25 peak (g) input vibration and frequency sweep from 0 to 8 kHz. The observed frequency response of the Voyager4 sensors was within ±1.5 dB up to 8 kHz (Figure 6, right).
Conclusion
AI can provide tangible benefits such as longer battery life when used for CbM of robotics, rotating machines, and their motors. An effective system performing this edge AI CbM function requires a carefully chosen and integrated set of components. Analog Devices MCUs with embedded AI hardware accelerators, supported by the EV-CBM-VOYAGER4-1Z evaluation kit with wireless connectivity, allow for the quick development of a CbM edge AI solution.
Related Content
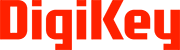
免责声明:各个作者和/或论坛参与者在本网站发表的观点、看法和意见不代表 DigiKey 的观点、看法和意见,也不代表 DigiKey 官方政策。