Touch Sensing Technology for Human Interface Designs
投稿人:DigiKey 欧洲编辑
2012-02-16
With more computing power available in the industrial environment, there are many more options for the human interface to machines. Multiple sensor technologies for touch sensors and touchscreens are becoming more popular, while other technologies such as capacitive touch wheels and proximity sensors are seeing increased adoption.
Increasingly, industrial equipment requires a more sophisticated interface, with buttons and switches being replaced by slider bars, control wheels, and touchscreens. Providing a rugged interface that can be easily integrated into more sophisticated control systems and still be quickly used on the shop floor is vital for a wide range of equipment.
There is a extensive selection of different touchscreen controllers, and for industrial applications, the power consumption is not necessarily as vital as for portable consumer equipment. However, keeping power consumption low keeps the temperature down, increasing the reliability, and potentially reducing running costs. There is also a wide range of portable equipment used on the factory floor, particularly for test, where the power consumption is critical. Similarly, the electromagnetic performance of a device may not be an issue for a consumer device but is vital in a noisy industrial environment. Techniques to reduce the susceptibility to EMI and to minimize the emissions from the interface are both key design factors.
Capacitive controllers have become much more popular with the advent of the Apple iPod control wheel, some of which is based around technology from Cypress Semiconductor. The capacitive technology helps in the industrial environment as the sensor can be covered. This technology functions by detecting changes in the electric field caused by the presence of another field such as a finger. However, these sensors can struggle with gloved fingers, so resistive contacts can be helpful in these situations. This distinction is continued with touchscreens. Capacitive screens are common up to 10 inches, but resistive screens can handle larger screen sizes and even gloves.
Proximity capacitive touch sensors in simple linear or rotational sliders offer significant advantages for industrial interfaces. With no moving parts to wear out and easily sealed to offer protection from harsh environments, they are more reliable, more energy efficient, and are more easily integrated to create an intelligent system.
Freescale’s MPR031 proximity capacitive touch sensor controller is a CMOS-based state machine that simplifies designing numerous touch applications. It can be used to replace up to three touch pads and switch replacements, and communicates via the I2C bus. It is optimized to manage two electrodes with interrupt functionality, or three electrodes with the interrupt disabled, and can accommodate a wide range of implementations due to increased sensitivity and a specialized feature set.
STMicroelectronics’ STMPE16M31QTR touch sensors are capacitive touch key controllers that offer highly versatile and flexible capacitive sensing capabilities in a single chip (Fig. 1). The devices integrate up to 24 capacitive sensing channels, which are highly sensitive and noise tolerant. Two units of hardwired ratiometric engines enable the implementation of a slider/wheel without external computations. Eight independent PWM controllers allow control of up to 16 LEDs with brightness control, ramping, and blinking capabilities. The I2C interface supports up to 400 kHz communication with the system host. A very wide dynamic range allows most applications to work without hardware tuning.
Figure 1: ST’s capacitive touch key controller.
IDT’s PureTouch technology is used in the LDS6000 family of devices and supports a range of sensor inputs to control buttons and sliders. This is a programmable capacitance-to-digital converter (CDC) designed for use with capacitive sensor arrays implementing touch-based input controls including sliders, scroll wheels, and buttons. Featuring 15 sensor inputs, the LDS6000 provides the flexibility to implement multiple touch inputs using a single controller.
The capacitive sensor inputs are directed through an integrated switch matrix to a 500 kHz sigma-delta CDC which senses changes in the external sensor array. When a sufficiently large change in capacitance occurs, sensor activation is registered and the host processor is notified.
On-chip calibration logic continuously monitors the environment and automatically adjusts on-and-off threshold levels to prevent false sensor activation. The LDS6000 is offered with both SPI-compatible and I2C-compatible interfaces (active interface selected by I/F select pin) and features a general-purpose input/ output (GPIO) and an interrupt output for additional communication with the host processor (Fig. 2).
Figure 2: IDT’s PureTouch LDS6000.
The Qtouch technology from Atmel is a digital burst mode charge transfer (hence QT) capacitive sensor drive for any touch key application. The keys can be constructed in different shapes and sizes to meet the requirements of the interface design, and the device contains all the signal processing required for stable sensing under a wide range of changing conditions with fully de-bounced outputs.
Noise immunity – a vital element in industrial environments where electromagnetic interference is a key issue – comes from the signals being modulated with a spread spectrum protocol. This provides immunity from external interference and also minimizes any emissions.
There are two basic configurations of the QT1110 to handle 11 keys or 7 keys, each with an individual output. One of the key issues is tuning the controller to the touch sensor, which can be time consuming. Cypress Semiconductor's patent-pending SmartSense auto-tuning algorithm (Fig. 3) eliminates the requirement for system tuning through automatic tuning of over ten parameters to achieve optimal touch sensing performance and the best user response. This is advantageous if there is a change in the PCB technology or supplier, as no re-tuning is required, nor when the overlay material or thickness changes.
Figure 3: The Cypress SmartSense technology.
The PSoC 5 family, such as the CY8C5247 from Cypress, has integrated the CapSense and SmartSense technology with a microcontroller and a range of configurable peripherals to support the sensor design. The CY8C52 family offers a modern method of signal acquisition, signal processing, and control with high accuracy, high bandwidth, and high flexibility. Analog capability spans the range from thermocouples (near DC voltages) to ultrasonic signals and can handle dozens of data acquisition channels and analog inputs on every GPIO pin.
The family also includes parts with interfaces such as USB and multimaster I2C. This allows designers to easily create system level designs through a library of prebuilt components and Boolean primitives using PSoC Creator, a hierarchical schematic design entry tool (Fig. 4).
Figure 4: The Cypress CapSense controller evaluation kit.
The 32-bit ARM Cortex-M3 CPU core runs at up to 40 MHz with flash program memory of up to 256 KB with 100,000 write cycles and 20-year retention, ideal for industrial designs with long lifetimes. The I/O system has between 46 to 70 pins (60 GPIOs, 8 SIOs, and 2 USBIOs) and there is routing from any GPIO to any digital or analog peripheral. An LCD display can be driven directly from any GPIO, up to 46 × 16 segments, and there is CapSense support from any GPIO. With 1.2 V to 5.5 V I/O interface voltages on up to four domains, the device supports maskable, independent IRQ interrupts on any pin or port as well as Schmitt trigger transistor-transistor logic (TTL) inputs.
Touchscreen
While touch wheels and touch panels are useful for machine control, sometimes a larger display is needed. Touchscreens have developed significantly in the last few years, coming down in cost by taking advantage of new resistive and capacitive designs.
3M’s MicroTouch System SCT3250EX is designed to meet the performance requirements of display applications ranging from 5.7 to 32 inches. As an all-glass design, the SCT3250EX touch system offers light transmission up to 11.5 percent better than typical resistive sensors and 3.5 percent better than typical surface capacitive sensors. It uses a proprietary hard coat and a scratch-resistant topcoat, called ClearTek, to support heavy-use applications (Fig. 5).
Figure 5: 3M’s MicroTouch screen.
3M has its own dedicated custom ASIC controller with proprietary firmware and patented algorithms that dynamically adapt to changes in the application’s environment to help maintain the initial video alignment of the display for the life of the product. It is this dedicated ASIC that gives the touch system ‘minimum touch duration’ that is 50 percent faster than typical surface acoustic wave and surface capacitive solutions.
For ease of integration, the E-84-C resistive touchscreen from IRTouch, shown in Figure 6, can be powered from a USB or PS/2 interface with a maximum power ripple of 200 mV rms. The standard range supports screen from 6.4 inches to 24 inches with custom versions from 5.7 inches and resolution of 4096 by 4096 pixels. The response speed is less than 16 ms, and it can be used with a finger, gloved hand, or opaque object. As the screen is resistive there is no minimum touch activation force required and the surface durability is that of glass with a Mohs' hardness rating of 7 to meet industrial requirements.
Figure 6: Touchscreens from IR Touch can be powered from the USB port.
Conclusion
There is a wide range of technologies available for touch interfaces in industrial applications. From capacitive to resistive sensing, the different formats can be used in many different ways to provide the appropriate level of control. Balancing the speed of response with the ease of tuning the sensors brings a range of design choices, and the increasing levels of integration allow more flexibility to control the sensors in software. New algorithms are making the process of sensor tuning easier, reducing the cost of developing the equipment. Additionally, more design options are available to assist in the development of rugged interfaces for industrial environments.
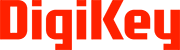
免责声明:各个作者和/或论坛参与者在本网站发表的观点、看法和意见不代表 DigiKey 的观点、看法和意见,也不代表 DigiKey 官方政策。