Creating Efficient Motor Control Solutions
投稿人:DigiKey
2012-02-21
Electric motors in a broad span of applications consume more than half of all electric energy produced, and stringent regulations are renewing the attention that goes into designing them. Incorporating a controller into many motor applications would provide a degree of energy savings and contribute to significantly reducing industrial operating costs. Power handling, power dissipation, and temperature specifications are important considerations when selecting the components for more efficient motor system design.
In addition, advancements in performance and miniaturization are contributing to enhanced integrated solutions, thus increasing the motor power output and a more efficient use of system design layout space. To help speed the development process, many OEMs would prefer a one-stop solution for motor drives, controls, smart motors, bearings, and gears. The selection of components Bourns® offers to meet the needs of low power dissipation, space savings, and cost effectiveness in the motor system design meets this need.
This article presents information about current sense resistors for motor drive design, and introduces a full motor system with additional components for power, circuit protection, and control panel adjustment.
Introduction to motor technology
The basic purpose of a motor is to convert electrical energy into mechanical energy, and there are numerous types of motors to accomplish this. One main difference among motor types is the use of alternating current (AC) or direct current (DC). AC motors are further differentiated by the number of phases in the drive. Shaded-pole, AC induction, and universal motors typically use single-phase AC drives. These are good for appliances, pumps, fans, and stationary power tools. Poly-phase AC drives are more suitable for AC poly-phase induction squirrel-cage motors that require low cost, long life, and high efficiency in pumps, fans, blowers, conveyors, and compressors. Poly-phase AC is also used in more expensive AC synchronous motors that have no slip for use in clocks, audio applications, and industrial equipment. DC motors typically offer simple speed control or precision positioning though often at higher cost than AC motors.
By far, the most popular types are AC induction motors, which are more cost-effective, compared to other motor types. Unfortunately, induction motors are also the most inefficient. Adding a variable frequency drive to an induction motor design allows for the speed of the electric motor to be adjusted by modulating the power that is delivered. The variable frequency drive can have an active front end, which is gaining relevance in the AC drive market with the new emphasis on reducing reactive power and due to the rising cost of energy. Active front ends convert the three-phase AC supply to DC power, using IGBT technology to control the level of DC current. Advantages in addition to power savings include increased performance, reduced torque ripple, power regeneration, power factor correction, and elimination of harmonics.
Sections of the motor system
The motor, motor drive, and motor controller units often are separate, although customers are starting to demand integrated solutions. Each of these units has a unique function within the system, which is shown in Figure 1. The drive produces power conversion, amplification, and sequencing of waveform signals. It provides the interface between the motor and its controller. The drive must match the voltage level and power level of the controller and the signal type of the motor in order to drive it. One step further from the motor, the motor controller receives supply voltages and provides signals to the motor drive.
Figure 1: Motor system diagram.
Since the fundamental function of the motor drive is to serve as the interface between motor and controller, it is essential that the drive accurately translate the input of the controller. Current sensing is the common method used for this task. A voltage signal is then developed that corresponds to the current flowing at a particular point in the circuit. Current sensing is used to provide current information from the drive to the controller and to detect any overcurrent or short circuit conditions that may arise. For circuits under 5.5 kW, a current sense resistor typically is sufficient for providing the current measurement. However, higher power systems will use mainly current transducers or IGBT modules because of the power loss and efficiency they provide over 5.5 kW.
Selecting a current sense resistor
The selection criteria for current sense resistors include the following:
- a low resistance value to minimize power losses
- low inductance because of high changes in current over time
- tight tolerances on the initial resistance value
- a low temperature coefficient of resistance (TCR) for accuracy
Bourns motor drive solutions
For the various types of motors and the units each contains, Bourns offers resistors that will fit in each section. For example, in an AC induction motor drive control, a three-phase inverter is required to control the motor. As a closed loop system, rotor feedback is required by using a sensor, such as a hall-effect sensor for each phase, or a current sense resistor to provide current feedback without a sensor. For medium power motor applications, power losses of discrete shunt resistors limit their efficiency. As an alternative to discrete resistors, insulated-gate bipolar transistor (IGBT) modules are used. For current sensing, IGBT modules have integrated shunt resistors, which provide an accurate measurement and are cost effective. Metal strip Bourns SMD products are available with power ratings up to 3 W for this purpose. Bourns’ CRA series, open air shunts such as Bourns’ PWR4412, or Bourns’ PWR4413 are used in IGBT inverters that use current sense resistors. Separately, snubber circuits consisting of diodes, capacitors, and external resistors are used to limit the IGBT switching overshoot. Thick-film, non-inductive resistors are available up to 35 W including Bourns’ PWR163 and PWR263 in DPAK packages and Bourns’ PWR220T and PWR221T in TO-220 packages.
Motors used in automotive, consumer, medical, and industrial applications may have space-constrained requirements. Bourns has a portfolio of power and current sense resistors to meet the size and power needs of designers. Current sense resistors such as Bourns’ CRA series have higher power capabilities and minimal surface temperature. In some instances, it is necessary to place multiple chip resistors in parallel in order to distribute the power to more resistors that have lower power capability instead of using a single large resistor. This keeps the surface temperature lower than using a single resistor. The layout of the board can affect the temperature distribution and performance as well, and Bourns Field Application Engineers (FAEs) are available for guidance in the design process.
Implementing a motor drive solution
An example of the challenges customers face in the design of a motor drive is finding surface mount components to replace through-hole resistors. These surface mount current sense resistors must also be capable of handling high power levels. In this particular case, a Bourns’ CRA2512 resistor is available to provide efficient transfer of heat from the resistor to the board, and thus, capable of handling the power required for the application. The CRA2512 has higher power handling capabilities than other competitive resistors because of the nickel-tin plating on its terminations. This provides for efficient transfer of heat from the resistor to the board. The customer is able to implement the surface mount design without increasing the number of components on the board, thus achieving both cost and real estate objectives while maintaining reliability. Figure 2 shows how the resistor can be incorporated in the motor drive design.
Figure 2: Motor drive schematic.
Current sense resistors are just one example of Bourns technology for motor systems. Throughout the motor system, Bourns technology is available to provide a solution that meets the needs of the customer, as shown in Figure 3. Power resistors with excellent power handling capability, such as Bourns’ PWR2010, are available in small package sizes. Bourns performs testing in-house and has facilities available for testing to the specific power needs of its customers. Potentiometers are used in the user interface at the control unit, such as for the manual adjustment of speed or torque. Bourns is able to customize its potentiometers for use with specific system specifications such as shaft length, bushings, and many other features. Bourns also offers a large portfolio of magnetic components with inductors that have high power ratings and are cost effective. These parts typically are used at the power supply and occasionally in the motor control and DC/DC conversion portions of the system. Potentiometers, encoders, or a combination of the two are used as position feedback sensors from the load to the control unit, and trimmers may also be found in motor control.
In addition to individual components, the system typically will include interfaces with additional systems using a standard communications protocol such as Ethernet, RS-485, and CAN. These interfaces require protection in order to maintain reliable operation. Bourns eases the design of surge and power cross protection with its technology and support. To minimize the number of parts and ease of coordination within the circuit protection solution, Bourns offers an electronic current limiter (ECL) that can be used in a variety of solutions. In addition to the detailed support provided by FAEs, Bourns offers single-page PortNote® Solutions that provide examples of circuit protection designs for a variety of communication protocols. Additional components for effective circuit protection solutions include TVS diodes, Bourns’ Multifuse® polymer positive temperature coefficient (PTC) devices, and Bourns’ SinglFuse™ thin film chip fuses.
Figure 3: Components in motor systems.
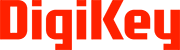
免责声明:各个作者和/或论坛参与者在本网站发表的观点、看法和意见不代表 DigiKey 的观点、看法和意见,也不代表 DigiKey 官方政策。