使用温度控制器和微型 PLC 加快小型自动化项目的速度
投稿人:DigiKey 北美编辑
2024-10-02
加热。在包装封口机、塑料成型作业、焊料回流炉、半导体加工等许多工业流程中,加热都很重要。每种工艺对温度水平和控制精度都有特定的要求。
自动化有助于在工业 4.0 设施中实现最高生产率和可持续性。小型机器和热加工也不例外。但并不是所有情况都需要大型、全面的解决方案。借助相对简单的专用温度控制器和小型可编程逻辑控制器 (PLC),也可以提高许多应用的性能。
机器设计人员可为简单的自动化项目选择一系列选项,包括适用于单相和三相电源环境的加热器控制器、采用一系列复杂控制算法的加热器控制器,以及针对中小型自动化环境进行优化的 PLC。一些小型机器在相对孤立的环境中工作,而另一些机器与大型设备连接则更有益。
本文介绍了功率控制器和加热器控制器的各种选择,包括硬件和软件方面的考量。最后简单介绍了与用于测量温度的传感器技术和已针对中小型机器进行优化的 PLC 有关的系统集成问题,以及 Omron 的典型产品。
从热固树脂和粘合剂等材料的固化到食品饮料产品的生产,工业流程通常都需要进行温度控制才能维持效率和确保质量。工业加热器不可或缺,但温度控制器才是关键。
控制工业加热器温度的方法不止一种。系统的运行优先级决定了所选择的方法。当运行成本是首要考虑因素且较低的温度控制精度可以接受时,便可采用简单的电压控制系统。
通过调节加热元件的供电电压,可以控制加热器的功耗,并改变热量输出。电压的变化可以快速实现,并产生相应的温度变化,但其滞后性随系统设计的不同而变化。减小电压可降低能源成本和温度。不过,对于许多工艺而言,温度降低的响应时间可能太长,而且很难精确控制温度。
基础电压控制之外
对于许多应用而言,基础电压控制是不够的。在这些情况下,设计人员可使用开/关控制、周期控制、最优周期控制或相位控制(图 1)。每种技术都具有不同的性能特点:
- 相位控制可提供极佳的可控性响应,并具有优异的解决方案尺寸和成本,而且噪声性能在大部分应用中都可以接受。
- 周期控制可提供优异的可控性响应,并具有优异的解决方案尺寸和成本,而且噪声性能也同样优异。在“最佳”周期控制中,每半个周期都会确定开关状态。
- 使用固态继电器 (SSR) 进行开/关控制具有优异的可控性响应、最小的解决方案尺寸、合理的成本以及出色的噪声性能。
图 1:用于工业加热器控制的电源开关选项。(图片来源:Omron)
实现相位控制和最优周期控制
Omron 为设计人员提供多种选项来实现开/关控制、相位控制或最优周期控制,其中包括型号 G3PW-A245EU-S,其额定工作电压为 100 VAC 至 240 VAC;另提供工作电压为 400 VAC 至 480 VAC 的其他型号。
这些控制器加入了加热器烧毁检测功能,可延长系统正常运行时间。一个 RS-485 通信端口用于设置变量和监测负载电流。
G3PW 控制器支持总运行时间监测,适用于恒阻负载和变阻负载。
多通道功率控制器
G3ZA 多通道功率控制器系列增加了三相最优周期控制功能,以支持三相加热器。与过零型 SSR 结合使用时,可支持低噪声功率运行。一个控制器最多可控制 8 个 SSR。此外,灯加热器还具有软启动功能(图 2)。
图 2:G3ZA 多通道功率控制器支持三相最优周期控制。(图片来源:Omron)
三相加热器已增加了三相最优周期控制功能。型号 G3ZA-4H203-FLK-UTU 的额定工作电压为 100 VAC 至 240 VAC,包括 RS-484 连接。另有工作电压为 400 VAC 至 480 VAC 的其他型号可供选择。
用于系统集成的温度控制器
EJ1N-TC4A-QQ 等温度控制器可连接至 G3ZA 系列多通道控制器等功率控制器。这些控制器具有用于温度传感器的输入端和用于系统 PLC 的连接端。输入单元可处理热电偶、铂电阻温度检测器 (RTD) 和模拟输入。
功能包括自动调谐 (AT),可帮助实现比例-积分-数字 (PID) 控制。自动调谐可用于通过手动使用阶跃响应法确定 PID 常量。一个 DeviceNet 通信集线器最多可连接 16 个温度控制器。
热管理软件
EJ1N 温度控制器可受益于 EST2-2C-MV4 热支持软件包。该软件可从个人电脑编辑和批量下载参数,加快配置和调试速度。
还支持对多达 31 个控制器进行趋势监测。可监测的参数包括过程值 (PV)、系统值 (SV)、操纵值 (MV)、PID 参数和警报开/关状态。
支持的逻辑运算包括从外部输入(事件输入)或温度状态设置输入,向外部控制或辅助输出装置发送值,以及通过开/关延迟改变工作状态。
改进的 PID
PID 控制在温度控制应用中非常有用。具有快速 SSR 的 G3ZA 系列多通道控制器等功率控制器与采用 PID 算法的温度控制器结合使用时,可提供维持要求的温度公差所需的细粒度控制。
基础 PID 控制需要在快速达到工作 SV 但存在可测量的过冲量,或尽量减少过冲但以较慢的速度上升到 SV 之间进行权衡。此外,在达到 SV 与响应传感器测得的实际 PV 干扰之间也要进行权衡。对 PV 变化的响应更好往往意味着 SV 上升性能不佳。
为了解决这些性能权衡问题,Omron 开发了一种增强型 PID 算法,称为 2-PID,或双自由度 PID。出厂时的 PID 预设值适合大部分加热应用,并支持过冲最小的响应。然而,借助 2-PID,设计人员还可设置对 SV 变化的响应速度,控制器会自动调整 PID 算法,以提供对 PV 干扰的优化响应(图 3)。
图 3:Omron 的 2-PID 温度控制(下图)结合了优异的干扰响应(右侧)和优异的阶跃响应(左侧)。(图片来源:Omron)
Omron 的 E5CC 温度控制器(如 E5CC-QX3A5M-003)加入了 2-PID 控制。这些控制器还可以为要求不高的应用实现基础开/关控制。
大号白色 PV 显示屏显示的是 PV 值,小号绿色 SV 显示屏显示的是期望值(图 4)。选配 CX-Thermo 管理软件支持快速编程。对于简单的应用,这些控制器可在 PLC 的介入下实现定时器功能和基本逻辑运算。
图 4:E5CC 温度控制器可清楚显示 PV 值 和 SV 值。(图片来源:DigiKey)
RS-485 接口支持 Modbus 通信或 Omron 专有的 CompoWay/F。这些控制器可接受各种输入,包括:
- 12 种热电偶
- PT100 或 JPt100 RTD
- 4 至 20 mA 或 0 至 20 mA 电流输入
- 1 至 5 V、0 至 5 V 或 0 至 10 V 电压输入
用于干扰抑制的自适应 PID
NX-TC 自适应温度控制器将 PID 控制提升到了一个新的水平,并且能够适应实时工作条件。自适应控制可根据工艺变化对控制设置进行自我优化。此外,这些控制器还包括用于包装密封应用和水冷塑料挤出机的内置功能。对于简单的应用,可以实现基础开/关控制。
干扰抑制功能 (DSF) 与 PID 控制结合后,可抑制常规和预期干扰造成的温度下降,例如在以下应用中:
- 当通过打开的门注入气体或添加或移除材料时,腔室温度会下降的沉积设备
- 电流流过晶圆时会导致温度升高的晶圆探针
- 注入树脂时模具温度会下降的成型系统
DSF 可自动抑制由可预见事件引起的正负温度波动。DSF 在发生干扰前由触发信号启动,然后对 MV 进行增减。这种自动调整可调整前馈 (FF) MV、FF 工作时间和 FF 等待时间,并且最多可将实现温度稳定的时间缩短 80%(图 5)。
图 5:DSF 增强型 PID 控制最多可将温度稳定的等待时间缩短 80%。(图片来源:Omron)
专为驱动 SSR 设计的 NX-TC 单元(如双通道 NX-TC2405)针对可扩展性进行了优化。在实现多级加热/冷却过程时,设计人员可使用 Omron 的 Sysmac studio 对多个加热电路或位置进行编程控制。
除 DSF PID 外,这些控制器还支持开/关控制,并且具有加热器烧毁错误检测功能。不仅包括用于网络连接的 EtherNet/IP 和 EtherCAT,而且还可接受各种热电偶或 RTD 传感器输入。
不测量就无法优化
电源开关设计、温度控制器和热管理软件无法在信息真空时提供最佳性能。温度传感器提供运行数据,使控制器和软件能够完成它们的工作。有多种温度传感器技术可供设计人员选择,其中包括:
- 用作温度敏感型电阻器的热敏电阻。这些热敏电阻的可重复性和稳定性通常约为 ±0.1°C。型号 E52-THE5A-0/100C 的工作温度范围为 -50°C 至 300°C。
- K 型温度传感器是一种含有铬和铝导体的热电偶。这些传感器可以配置为浸入式传感器、表面传感器或其他样式。型号 E52-CA1GTY 2M 的工作温度范围为 0°C 至 300°C。
- RTD 传感器精度高,抗电噪声能力强,因此适用于恶劣的工业环境。E52-P6DY 1M 铂 pt100 RTD 传感器的额定工作温度范围为 -50°C 至 250°C。
- ES1-LW100-N 等非接触式红外 (IR) 传感器可在 1,000 mm 的距离内测量直径为 35 mm 的目标区域的温度。其指定使用温度高达 1,000°C。
集成到一个系统中
设计最多具有 320 个 I/O 的中小型机器时,可选用 Omron 的 CPE2 系列 PLC。这些小型 PLC 的通信功能支持机器对机器 (M2M) 数据传输,并且可集成到工业物联网 (IIoT) 中。
CPE2 PLC 的工作温度范围为 -20°C 至 +60°C,适用于各种工业应用,例如包装封口机、灌装压盖机、金属或塑料加工工具、塑料成型机以及小零件装配。型号 CP2E-N30DR-D 有 18 个输入和 12 个输出,可在 100 至 240 VAC 或 24 VDC 电源下工作。可与 NB7W-TW01B 7" 彩色触摸屏 HMI 搭配使用,以形成完整的系统解决方案(图 6)。
图 6:Omron 的 CP2E-N30DR-D 控制器和 NB7W-TW01B 7" 彩色触摸屏 HMI。(图片来源:Omron)
结语
热管理是许多工业流程的一个重要方面。这就需要选择并集成具有优化算法的功率控制器和加热器控制器。温度传感器是热管理难题的另一个重要组成部分。最后,设计人员可选用小型 PLC 来支持 M2M 通信并集成到 IIoT 中。
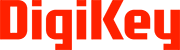
免责声明:各个作者和/或论坛参与者在本网站发表的观点、看法和意见不代表 DigiKey 的观点、看法和意见,也不代表 DigiKey 官方政策。